Installing Rivet Nuts into Curved Surfaces
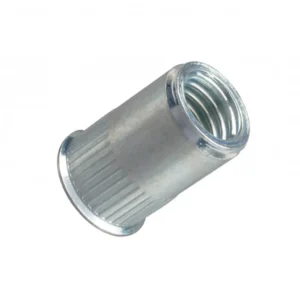
Leading Rivet Nut Manufacturer and Supplier in China
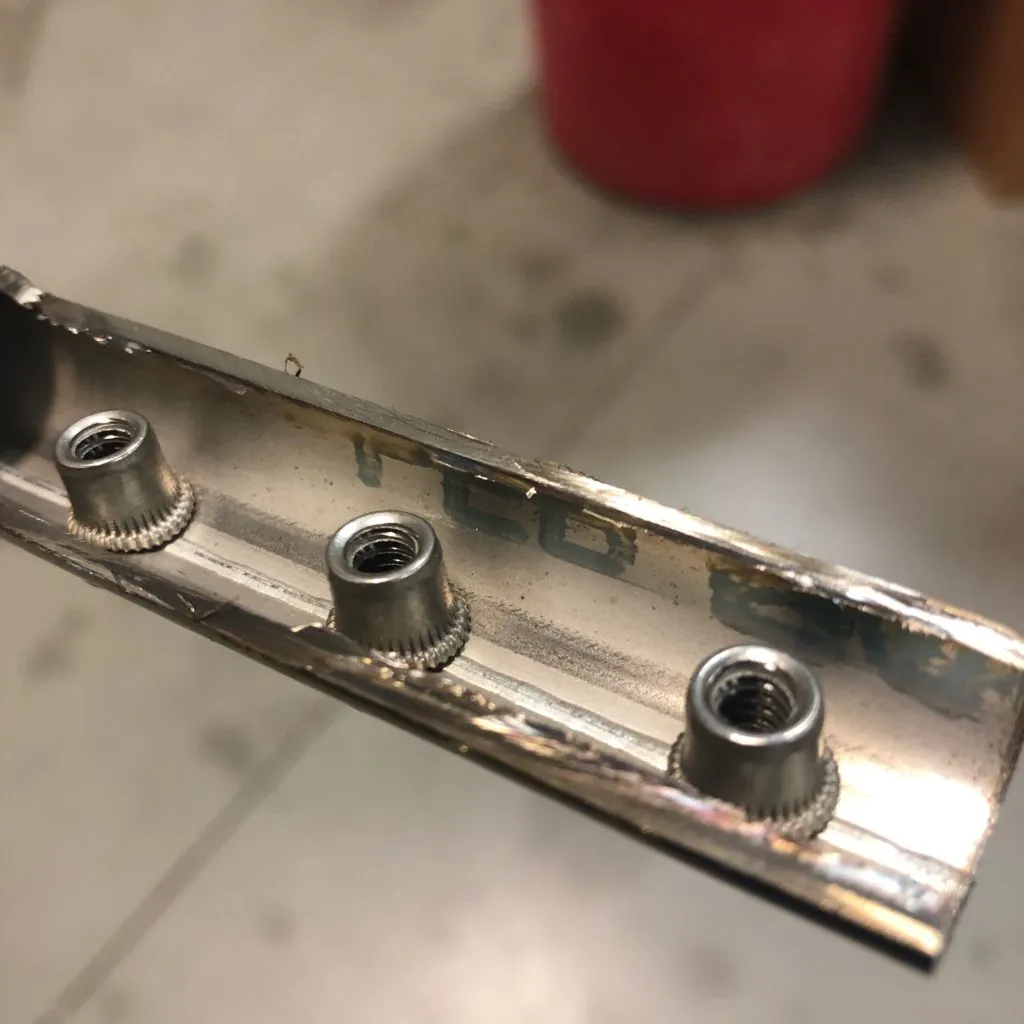
In real-world manufacturing and repair scenarios, many components are far from flat—think of metal tubing, curved sheet metal, vehicle body panels, or control box enclosures. Unlike flat surfaces, these curved profiles often pose challenges such as poor fit, unstable clamping, and uneven deformation during fastening. That’s why installing rivet nuts into curved surfaces requires more than just standard techniques—it demands specialized fasteners, tailored tools, and a clear understanding of the geometry involved. Mastering this process is essential for achieving secure, durable connections in a wide range of applications.
Table of Contents
What Challenges Do Curved Surfaces Pose for Rivet Nut Installation?
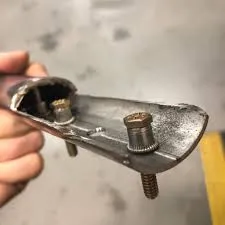
When installing rivet nuts on curved surfaces (such as round tubes, arched structures, or bent sheet metals), there are several practical issues that arise due to the mismatch between the surface geometry and the rivet nut’s design, leading to the following challenges:
1. Loose Installation, Easily Rotates or Detaches
- The flange of the rivet nut needs to be tightly adhered to the base material’s surface to ensure proper clamping force and anti-rotation function.
- On curved surfaces, the flange cannot fully adhere to the surface, resulting in “gaps” or “warping.”
- After installation, the rivet nut may rotate during screw tightening or detach from the base material due to insufficient stress.
2. Uneven Deformation During Riveting, Affecting Clamping Force
- The tail of the rivet nut relies on axial force to “shrink and expand” and fix itself in the sheet material.
- Curved surfaces lead to uneven force distribution, causing the tail to deform diagonally, eccentrically, or incompletely, which reduces the clamping force and affects connection strength.
- In severe cases, it may even cause the sheet material to crack, leading to structural damage.
3. Stress Concentration, Material Susceptibility to Fatigue or Cracking
- The force direction on curved surfaces is inconsistent, leading to localized stress concentration points.
- Over long-term use or in vibrating environments, the connection area may crack due to fatigue, especially in brittle or rigid materials like aluminum alloys or plastics.
- For thin sheets or coated materials, peeling or cracking may occur, affecting the overall structural strength.
4. Poor Appearance, Affecting Product Aesthetics
- After installation on curved surfaces, the flange of the rivet nut often cannot “lie flat,” leading to warped edges or protrusions.
- For applications that require good appearance (such as appliance housings or decorative panels), this may appear rough and irregular, even affecting subsequent assembly or sealing performance.
- If post-treatment processes such as painting, anodizing, or electroplating are needed, the raised flange can compromise the overall surface quality.
Summary
The main issue with curved surface installations is the inability to achieve stable clamping, which can lead to structural damage, fastening failure, and aesthetic problems. Therefore, during the design and selection phase, it is crucial to choose more adaptable rivet nut types (such as Jack Nuts or Slotted Rivet Nuts) or pre-treat the installation surface (e.g., with washers or reinforcement).
How Can You Successfully Install Rivet Nuts on Curved Surfaces?
1. Choose the Right Type of Rivet Nut
- Structural Features: The rivet nut has multiple longitudinal slots on its body. During installation, the metal slots first compress and then deform, providing good clamping force.
- Suitable Materials: Metal sheets (such as aluminum, stainless steel), slightly curved thin sheets.
- Advantages:
- Better adaptability to curved surfaces compared to standard round-shank rivet nuts.
- Stable formation, suitable for blind hole installations.
- Limitations: Requires good surface contact, not suitable for surfaces with large curvature.
- Structural Features: The tail of the rivet nut splits into four parts during installation, forming an umbrella-like structure that tightens through expansion.
- Suitable Materials: Plastics, fiberglass, thin metal sheets, hollow tubes, and other flexible or irregular base materials.
- Advantages:
- Suitable for soft materials and non-flat surfaces.
- Simple installation tools, suitable for light-duty connections.
- Limitations:
- Lower structural strength, not suitable for high-strength connections.
- Cannot be used for thick plates or high-load structures.
- Structural Features: A metal sleeve that deforms at the bottom through riveting tools to secure the nut in place.
- Suitable Materials: Metal sheets (steel, aluminum), flat structures.
- Advantages:
- High strength, versatile, and suitable for standard structural fastening.
- A wide range of specifications and head styles available.
- Limitations:
- Not suitable for curved surfaces, as it requires a flat installation surface.
- May not provide effective clamping or could shift when installed on curved surfaces.
Summary: Which Rivet Nut Is Best for Curved Surfaces?
If you are dealing with medium to large radius curved metal surfaces, the Slotted Rivet Nut is a more reliable and professional choice.
For very thin, flexible, or curved material surfaces, such as plastics and non-metallic materials, Jack Nuts are generally more suitable than Slotted Rivet Nuts.
Comparison Table for Three Types of Rivet Nuts: Curved Surface Suitability
Rivet Nut Type | Curved Surface Adaptability | Installation Method | Load Capacity | Suitable Materials | Typical Applications |
Jack Nut | ★★★★☆ | Manual or screw gun | Light-duty | Plastic, fiberglass, curved tubes, hollow sheets, etc. | Curved panels, instrument mounts, electrical enclosures |
Slotted Rivet Nut | ★★★☆☆ | Riveting tool | Medium-duty | Thin metal sheets, lightly curved plates | Electronic enclosures, control panels |
Standard Rivet Nut | ★☆☆☆☆ | Riveting tool | Medium to high | Metal sheets, structural parts (flat surfaces required) | Structural connectors, industrial assembly |
2. Optimize the Hole Preparation
When installing rivet nuts on curved surfaces, the design and processing of the hole are critical. The following measures can greatly improve installation stability:
- Local Flattening: If the material thickness and structure allow, prior to drilling, locally flatten the area where the nut will be installed using stamping, jigs, or localized flattening. This creates a small flat surface to improve flange adhesion and reduce the risk of rotation.
- Optimize Hole Diameter: Pre-drill the hole slightly smaller (e.g., by 0.1mm) than the standard hole size to increase interference between the nut’s shank and the hole wall. This effectively prevents rotation or slipping, especially for round-shank or knurled rivet nuts.
3. Use Curved Surface Adapters or Tools
Professional installation tools are crucial for curved surface applications, significantly improving stability and efficiency:
- Curved Surface Jigs or Molds: Use adjustable-angle or elastic support mounting jigs to ensure the rivet nut tightly adheres to the base material before riveting. This eliminates gaps or rotation issues caused by poor surface contact.
- Specialized Installation Heads: Some brands (such as Gesipa, POP, etc.) offer special installation gun heads designed specifically for curved or tubular surfaces. These tools automatically adjust the riveting angle, ensuring even force distribution and more accurate deformation of the nut’s tail.
4. Use Adhesives or Sealing Aids
When the curved surface cannot be fully compressed, adhesives or auxiliary sealing materials can be used to enhance grip and improve protective performance:
- Structural Adhesives/Sealants: Before installation, apply epoxy structural adhesives, anaerobic adhesives, or waterproof sealants under the rivet nut’s flange. This secondary bonding force helps reduce rotation and prevents moisture penetration after riveting.
- Blind Rivet Nuts: Consider using waterproof rivet nuts with rubber washers (e.g., closed-end sealed rivet nuts), especially suitable for outdoor equipment, hollow tubes, or structures prone to water ingress.
Do You Have Any Questions?
Let Us Solve Your Problem
Where Are Curved Surface Installations Commonly Used?
1. Automotive Industry
In the modern automotive lightweight and modular assembly process, many structural components are curved or bent.
- Wheel arch liners, underbody protection plates: These areas have limited space, making traditional welding difficult, while rivet nuts support blind installation.
- Car door and tailgate edges: Used for installing motors, module brackets, etc.
- Roof beams and sunshade system connectors: These structures often consist of high-strength curved steel plates and require reliable fastening methods.
2. Piping Equipment Assembly
In industries such as machinery, food processing, medical, and power, stainless steel or aluminum alloy pipes are widely used for equipment enclosures and supports.
- Installing junction boxes, button panels, sensor brackets on round pipes.
- Adding auxiliary devices on mechanical equipment’s internal circular framework.
- Connecting hollow profiles, such as joining slides, pivots, etc.
3. Sports Equipment and Outdoor Gear
Many outdoor products and fitness equipment use lightweight metal structures, most of which are curved or tubular.
- Tent frames, camping bed frames, folding chair support rods.
- Fitness equipment such as elliptical machines, rowing machines with link structures.
- Electrical component mounting points on outdoor billboards, light poles.
4. New Energy Support Systems
In solar photovoltaic systems, wind energy facilities, and similar applications, hollow structural profiles are often used for mounting supports, many of which involve curved or arched connections.
- Curved pipe solar panel support connections.
- Connection points between support structures and control boxes, cable trays.
- Wind energy equipment with curved covers and reinforcements.
FAQs - Installing Rivet Nuts into Curved Surfaces
1. Can’t I Use Standard Rivet Nuts on Curved Surfaces?
Not necessarily. If the curvature of the surface is small and the material is relatively thin (such as aluminum or stainless steel sheets), some standard round body rivet nuts or knurled rivet nuts can be installed stably with the proper fixture. However, for larger curvatures or areas with uneven wall thickness, it is recommended to use nut types specifically designed for curved surfaces, such as Slotted Rivet Nuts or Jack Nuts, to ensure anti-rotation and secure fastening.
2. Why Are Slotted Rivet Nuts Suitable for Curved Surfaces?
Slotted Rivet Nuts have longitudinal cuts in their tail, making them more flexible during the riveting process. This allows them to conform to the curvature of the substrate and provide even clamping force. This structure is especially suited for irregular curves or round pipe structures, effectively preventing traditional nuts from rotating or falling off due to poor surface contact.
3. Are the Installation Tools for Jack Nuts the Same as Rivet Nuts?
Not exactly. Jack Nuts are typically installed using a screwdriver and wrench or a specialized tensioning tool, without the need for a standard rivet gun. In contrast, standard rivet nuts require the use of a manual, pneumatic, or electric rivet gun for installation. Jack Nuts have a simpler installation process, making them ideal for situations with limited space or where specialized tools are not easily available.
4. How Can I Improve the Firmness and Waterproofing of Curved Surface Installations?
The following measures are recommended:
- Choose waterproof nuts with rubber washers.
- Apply sealant or structural adhesive on the contact surfaces before installation.
- Use specialized molds or fixtures to improve surface contact and avoid nut rotation due to gaps.
- Opt for nuts with flanges to increase contact area and enhance the even distribution of clamping force.
5. Can I Install Rivet Nuts on Curved Surfaces of Plastics or Composite Materials?
Yes, but special attention is needed for the following points:
- For materials with low strength, it is recommended to use rivet nuts with backplates to prevent the nut from pulling through or rotating.
- Choose tooth nuts or Jack Nuts specifically designed for plastics, which anchor in the material after deformation.
- Avoid excessive pulling force during installation to prevent damage to the substrate.
- Some plastic parts can be pre-heated in the forming area to improve nut contact and riveting performance.
Do You Have Any Questions?
Let Us Solve Your Problem
Buy Rivet Nuts from Rivetfix
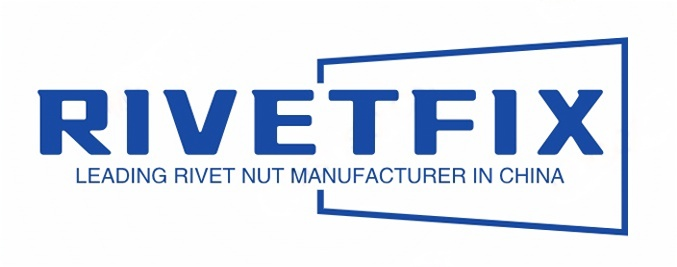
As a leading fastener manufacturer in China with more than 15 years in the industry, Rivetfix are committed to providing first-class quality fasteners and responsive services to the world. We offers a wide range of rivet nuts and clinch nuts designed to meet the unique demands of your projects. Rivetfix ensures you have the right solution for every application. Choose Rivetfix for versatile, cost-effective, and durable fastening solutions tailored to your specific needs. In addition, we can also provide customized rivet nuts service and clinch nuts according to your requirements.
Contact us now for more information and customization options on Rivet Nuts!
Get High Quality Rivet Nuts Quote!
Send Your Rivet Nut Request
For more than 20 years, Rivetfix has helped customers solve many rivet nuts sourcing needs and technical challenges.
Have a question? Contact us and we’ll provide you with the perfect solution.