Are Aluminum Rivet Nuts Strong?
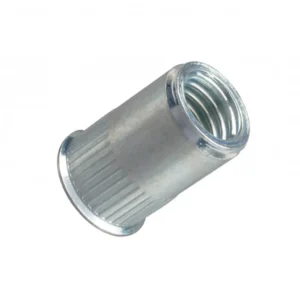
Leading Rivet Nut Manufacturer and Supplier in China
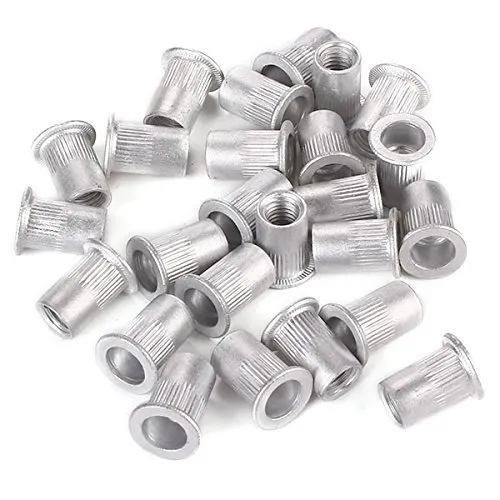
When it comes to lightweight and corrosion-resistant fastening solutions, aluminum rivet nuts are often a top choice across industries like aerospace, electronics, and automotive. But many engineers and buyers still ask the critical question: “Are aluminum rivet nuts strong?” This blog explores the mechanical strength, performance characteristics, and suitable applications of aluminum rivet nuts to help you determine whether they meet your structural and load-bearing requirements.
Table of Contents
Why Worry About the Strength of Aluminum Rivet Nuts?
Among various rivet nut materials, aluminum rivet nuts are widely used due to their lightweight and corrosion resistance, especially in industries that demand lightweight structures and strong environmental adaptability, such as:
- Aerospace: cabin interiors, control panel mounting structures;
Automotive manufacturing: fastening for non-load-bearing components;
Electronics: internal connections in laptops, monitors, and consumer electronics enclosures;
Display equipment and lighting structures: lightweight aluminum profiles for exhibition stands and lighting supports.
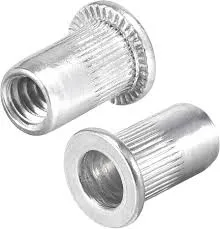
However, despite the many advantages of aluminum, its strength and rigidity lag behind those of steel or stainless steel. This raises common concerns among users:
“Are aluminum rivet nuts prone to being pulled out or sheared?”
“Will they loosen or fail under vibration, impact, or other harsh conditions?”
“What types of structures are suitable for aluminum rivet nuts? Can they be used where strong fastening is required?”
Therefore, when selecting and designing with aluminum rivet nuts, it is essential to thoroughly understand their mechanical properties, load-bearing capacity, and applicable scenarios to ensure the fasteners meet both lightweight demands and sufficient strength and durability.
What Are the Material Properties of Aluminum Rivet Nuts?
Aluminum rivet nuts are typically manufactured from high-strength aluminum alloys such as 5052, 6061, and 7075 series, offering an excellent combination of light weight, formability, and mechanical strength. They are particularly suitable for applications that demand structural weight reduction and corrosion resistance. The following sections outline the key alloy types and their performance characteristics:
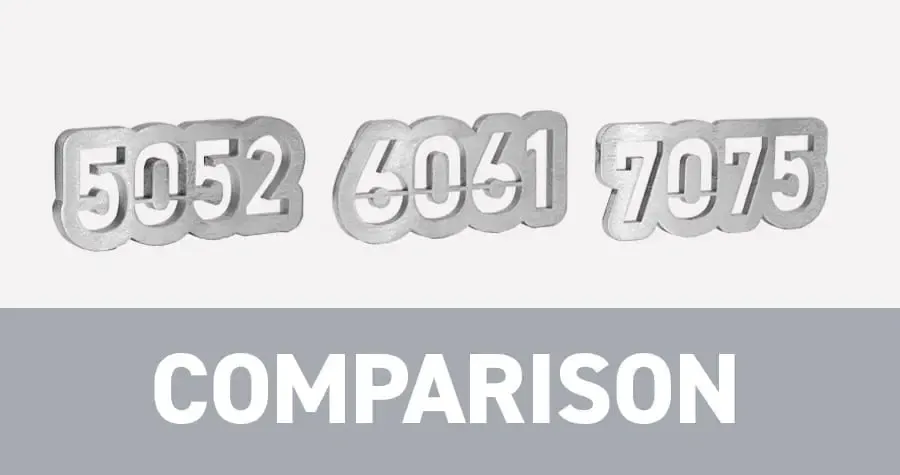
a. Common Aluminum Alloys and Their Applications
1. 5052 Aluminum Alloy
Key Characteristics:
- Moderate strength: 5052 is a medium-strength aluminum-magnesium alloy, with a yield strength of approximately 193 MPa and tensile strength around 228 MPa. While not suitable for high-load scenarios, it is more than sufficient for general industrial structures and electronic devices.
- Excellent corrosion resistance: Performs well in marine and chemically corrosive environments, ideal for salt spray and acidic/alkaline conditions.
- Good weldability: Compatible with MIG and TIG welding processes, making it suitable for secondary processing.
- Improved fatigue resistance: Offers better fatigue strength than pure aluminum, making it suitable for lightweight structures subjected to cyclic loads.
Typical Applications:
- Enclosures for light- to medium-duty equipment (e.g., telecom cabinets, power supply housings);
- Outdoor electronic panels and aluminum profile connectors;
- Traffic signs and display stands;
- Industrial sheet metal parts with moderate load requirements.
2. 6061 Aluminum Alloy
Key Characteristics:
- Balanced mechanical performance: One of the most commonly used structural aluminum alloys. In T6 temper, its yield strength can exceed 250 MPa, with tensile strength up to 310 MPa.
- Good machinability: Suitable for turning, milling, drilling, and other machining processes, with good dimensional stability after forming.
- Excellent weldability and surface treatment adaptability: Retains good mechanical properties after welding, and can undergo anodizing or powder coating for better appearance and corrosion protection.
- High cost-performance ratio: Offers a good balance between strength, corrosion resistance, and cost, making it the most widely used base material for aluminum rivet nuts.
Typical Applications:
- Moderate-load connection points such as automation frames and electronics supports;
- General sheet metal structures and aluminum profile assemblies;
- Aircraft interior structures and portable device frames;
- Fastening needs requiring a balance of strength and lightweight properties.
3. 7075 Aluminum Alloy
Key Characteristics:
- Ultra-high strength alloy: 7075 is an aerospace-grade aluminum-zinc alloy. In T6 temper, it offers a yield strength of up to 500 MPa and tensile strength up to 570 MPa, comparable to some alloy steels.
- High hardness with lower ductility: While extremely strong, it is less ductile and more difficult to machine than 5052 or 6061, requiring precise forming and heat treatment control.
- Moderate corrosion resistance: Not as corrosion-resistant as 5052, but its performance can be improved with anodizing or coating.
- Higher cost: Due to the high raw material cost and machining difficulty, it’s mainly used in applications that demand extremely high strength and low weight.
Typical Applications:
- High-strength fasteners in military and aerospace components;
- High-end outdoor equipment (e.g., climbing carabiners, ski gear);
- Load-bearing joints in industrial robots and high-performance robotic arms;
- Heavy-duty aluminum rivet nuts in demanding structural areas under high tension or shear loads.
Summary Table:
Material | Yield Strength (MPa) | Features | Typical Applications |
5052 | ~193 | Corrosion-resistant, easy to form, moderate strength | General light-load structures, outdoor assemblies |
6061 | ~250 | Balanced performance, cost-effective | Universal structural use, industrial parts |
7075 | ~500 | Ultra-high strength, high cost | Aerospace-grade, high-load connections |
b. Physical and Mechanical Properties of Aluminum Rivet Nuts
Low density and lightweight
- Aluminum has a density of approximately 2.7 g/cm³, about one-third that of steel;
- Ideal for reducing overall weight in aerospace, automotive, and electronic products.
Moderate strength
- Yield strength typically ranges from 150 to 300 MPa, depending on alloy type and heat treatment;
- Sufficient for moderate- to light-load applications, though not as strong as steel rivet nuts.
Excellent corrosion resistance
- Forms a natural, dense oxide layer that protects against moisture, oxygen, and salt spray;
- Especially well-suited for humid or outdoor environments.
Good thermal and electrical conductivity
- Aluminum conducts heat better than most structural materials, ideal for electronics, enclosures, and thermal transfer applications.
c. Ductility and Formability of Aluminum
High plasticity and lower hardness
Aluminum and its alloys exhibit good ductility and relatively low hardness, meaning they can undergo significant plastic deformation under force without fracturing. This property allows aluminum materials to adapt during rivet nut installation, forming a strong mechanical interlock.
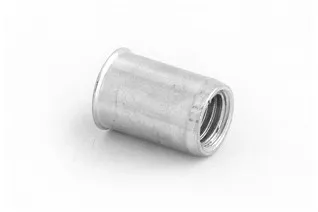
Plastic deformation aids secure fastening
During installation, the rivet nut’s tail expands under axial force. Thanks to aluminum’s ductility, the surrounding material flows and conforms around the expanded tail, creating a tight mechanical lock. This plastic expansion ensures a strong, stable bond with the base material.
Reduced risk of substrate damage
Compared to harder and more brittle materials (like certain steels or cast iron), aluminum’s flexibility helps prevent cracking or breakage during the installation process. This is particularly important in thin sheet metal or lightweight aluminum profiles, where substrate integrity must be preserved.
Ideal for lightweight, thin-walled structures
Aluminum rivet nuts are especially suitable for applications involving thin panels or extrusions. If a nut is too rigid, it may cause the material to fracture or distort, but aluminum’s flexibility allows for safer and more reliable installation.
More forgiving during installation
Due to aluminum’s softness and ductility, it tolerates variations in installation force better than harder materials. This improves production efficiency and increases the success rate of proper installations.
Are Aluminum Rivet Nuts Strong?
1. Pull-Out Strength
Definition and Influencing Factors
Pull-out strength refers to the maximum load required to extract a rivet nut from the base material. It depends on several factors including the rivet nut material, installation quality, and the thickness and hardness of the base material.Performance of Aluminum Rivet Nuts
Due to the relatively soft nature of aluminum, aluminum rivet nuts generally have lower pull-out strength compared to their steel counterparts.Example Data
For instance, an M6 aluminum rivet nut installed in an aluminum sheet typically exhibits a pull-out strength between 3.5 kN and 5.5 kN, depending on the thickness of the aluminum sheet (e.g., 1.5 mm, 2.0 mm, 3.0 mm).
2. Spin-Out Strength (Torque Resistance)
Definition and Influencing Factors
Spin-out strength refers to a rivet nut’s ability to resist rotational torque without spinning or coming loose.Characteristics of Aluminum Rivet Nuts
Due to their softer material, aluminum rivet nuts tend to have weaker anti-rotation capability, especially under high torque conditions.
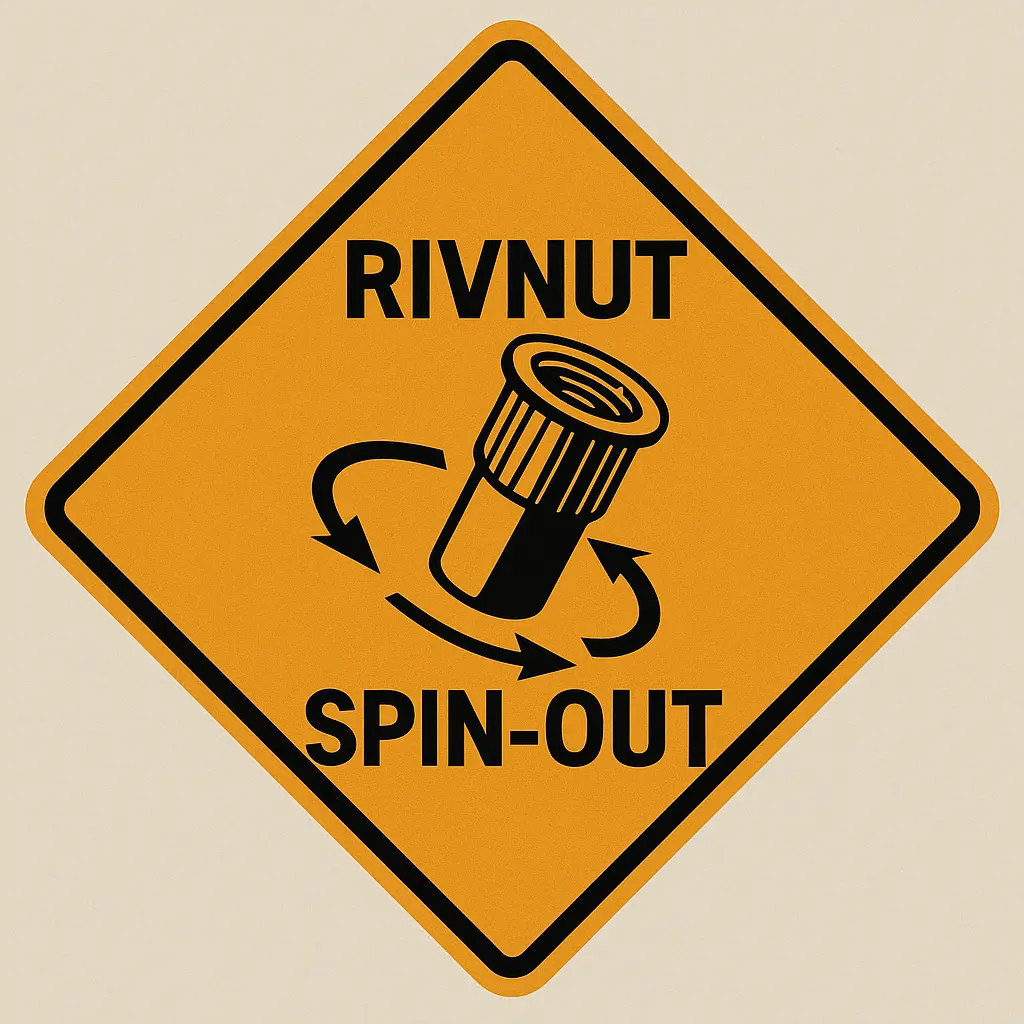
- Design Recommendations
To enhance torque resistance, it is recommended to use knurled body or hexagonal body aluminum rivet nuts. These designs improve mechanical interlock with the base material and significantly increase rotational stability.
3. Shear Strength
Definition and Performance
Shear strength measures the rivet nut’s ability to resist forces parallel to the material surface. Aluminum rivet nuts typically have slightly higher shear strength than pull-out strength.
Typical Range
Commonly falls within the 4 kN to 6 kN range, making them suitable for light- to medium-load applications such as electronics enclosures and lightweight structural supports.
Summary Table: Common Aluminum Rivet Nut Specifications and Strengths
Nut Size | Pull-Out Strength (kN) | Torque Resistance | Shear Strength (kN) | Grip Range (mm) | Notes |
M4 | 2.0 – 3.0 | Moderate | 3.0 – 4.5 | 1.0 – 3.0 | For light loads |
M5 | 2.5 – 4.0 | Moderate to High | 3.5 – 5.0 | 1.2 – 3.5 | Light to medium load |
M6 | 3.5 – 5.5 | Moderate to High | 4.0 – 6.0 | 1.5 – 4.0 | Most commonly used |
M8 | 4.5 – 6.5 | Strong | 5.0 – 7.0 | 2.0 – 5.0 | For medium loads |
Where Are Aluminum Rivet Nuts Suitable (or Not)?
Aluminum rivet nuts are highly suitable for lightweight and medium-load applications where lightweight construction and corrosion resistance are critical. However, in high-strength or heavy-duty scenarios, caution should be taken—steel or stainless steel rivet nuts are often preferred to ensure safe and reliable connections. Choosing the right material and proper design is key to maximizing the performance of aluminum rivet nuts.
✅ Suitable Applications – Detailed Explanation:
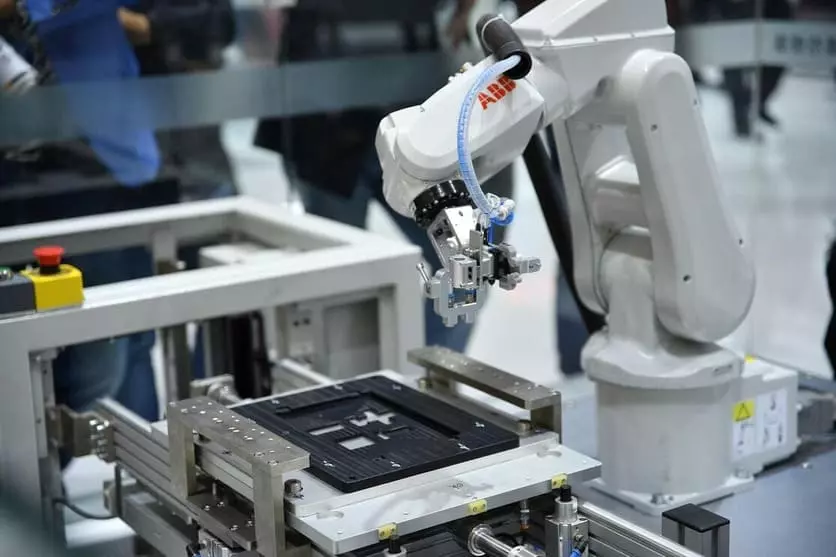
1. Lightweight Structural Applications
Due to their low weight, excellent formability, and corrosion resistance, aluminum rivet nuts are ideal for securing lightweight structures. Typical examples include sheet metal components, electronic housings, and light-duty metal brackets. These applications prioritize reduced weight and appearance over extreme mechanical loads.
2. Weight-Sensitive Devices
Aluminum rivet nuts are especially suitable for devices where weight is critical, such as drones, laptops, and portable instruments. Their use helps reduce overall weight, enhancing portability and system efficiency. Additionally, aluminum’s good thermal conductivity and corrosion resistance contribute to improved heat dissipation and long-term stability.
3. Corrosive Environments
The natural oxide layer on aluminum provides inherent corrosion resistance, making aluminum rivet nuts well-suited for humid or outdoor environments. In such conditions, aluminum rivet nuts help prevent galvanic corrosion that may occur between dissimilar metals like steel and aluminum, ensuring long-lasting, aesthetically clean connections.
❌ Unsuitable Applications – Detailed Explanation:
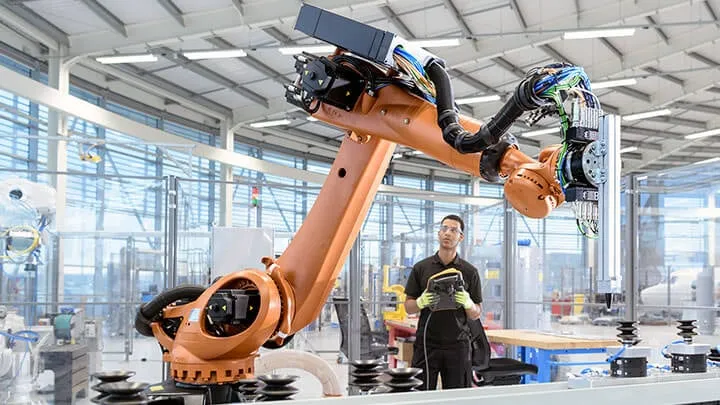
1. Heavy-Duty or High-Strength Connections
For industrial machinery, heavy equipment, high-vibration environments, or frequently disassembled assemblies, aluminum rivet nuts may lack the required strength and durability. These use cases demand higher tensile and shear strength, where steel or stainless steel rivet nuts provide better fastening performance and longer service life.
2. Critical High-Load Connections
In load-bearing structures or areas requiring high mechanical reliability, aluminum rivet nuts may fall short of engineering standards. Under high temperature, high pressure, or harsh working conditions, their mechanical properties may degrade, increasing the risk of loosening or failure, which could compromise the overall safety of the structure.
How Can You Improve the Performance of Aluminum Rivet Nuts?
① Ensure Precision of Mounting Holes and Surface Preparation
To achieve optimal fastening results with aluminum rivet nuts, it’s crucial to control the accuracy of the hole dimensions. The hole size tolerance is generally recommended within ±0.1 mm. Oversized holes may lead to loosening or spinning of the rivet nut after installation, while undersized holes can increase installation resistance or damage the rivet nut or base material. Therefore, an exact hole size can keep a rivnut from spinning.
Additionally, surface preparation—such as deburring, chamfering, and cleaning—helps reduce stress concentration during installation, preventing edge cracking and improving joint quality.
② Select the Proper Size and Grip Range
Aluminum rivet nuts are available in various rivet nut sizes and grip ranges. It’s essential to select a specification that matches the actual thickness and structural requirements of the aluminum material. An insufficient grip range may result in a loose connection, while an excessively large grip range can generate excessive clamping force, potentially deforming or damaging the aluminum. Proper sizing ensures effective load distribution, prolongs service life, and enables the rivet nut to perform at its best.
③ Add Washers or Apply Anodizing to Enhance Durability
For applications requiring higher durability and corrosion resistance, consider adding soft washers (such as nylon or rubber) between the rivet nut and aluminum surface. These help distribute pressure more evenly and reduce localized stress, preventing indentation or cracking in the aluminum. Additionally, anodizing the aluminum base material forms a dense oxide layer on the surface, significantly increasing hardness and corrosion resistance. This improves the overall durability and stability of the riveted connection structure.
How Do Aluminum, Steel, and Stainless Steel Rivet Nuts Compare?
Lightweight, ideal for weight-sensitive applications such as aerospace and electronics
Excellent corrosion resistance, especially after anodizing
Lower mechanical strength, suitable for light to medium load connections
Minimal damage to base material during installation, suitable for soft or thin materials
Weaker spin-out resistance, requires knurled or hex-shaped designs for improved stability
High strength, capable of withstanding large tensile and shear forces, suitable for heavy-duty structures
Lower cost, but prone to corrosion; typically requires zinc plating or other surface treatments
High rigidity, may cause dents or damage to soft base materials like aluminum
Good spin-out resistance, commonly available in knurled and hex body designs
Not suitable for prolonged exposure to moisture or salt spray due to risk of galvanic corrosion
- Excellent corrosion resistance, ideal for harsh or outdoor environments
- Relatively high strength, typically between that of aluminum and carbon steel rivet nuts
- Higher cost, but better long-term durability and performance
- Strong spin-out resistance, suitable for critical fastening points
- Good compatibility with various base materials, especially where corrosion resistance is critical
Comparison Table:Aluminum, Steel, and Stainless Steel Rivet Nuts
Feature | Aluminum Rivet Nuts | Steel Rivet Nuts | Stainless Steel Rivet Nuts |
Material Density | Light (~2.7 g/cm³) | Heavy (~7.8 g/cm³) | Heavy (~7.9 g/cm³) |
Tensile Strength | Low to Medium | High | Medium to High |
Corrosion Resistance | Good (Better after anodizing) | Poor (Requires coating) | Excellent |
Spin-Out Resistance | Average (Design dependent) | Good | Good |
Suitable Environment | Indoor, light-duty, humid environments | Dry or protected heavy-duty use | Harsh, wet, or corrosive conditions |
Cost | Low to Medium | Low | High |
Base Material Impact | Low | High (Possible indentations) | Medium |
Recommended Applications | Lightweight structures, electronics, aerospace | Heavy machinery, automotive, industrial equipment | Marine, chemical, outdoor, and high-corrosion environments |
Conclusion:Are Aluminum Rivet Nuts Strong?
Aluminum rivet nuts perform excellently in applications requiring lightweight design, corrosion resistance, and low to medium load capacity.
While their strength is lower than that of steel or stainless steel rivet nuts, they can fully meet the fastening needs of most lightweight structures when properly selected and installed.
For higher strength requirements, consider using high-strength aluminum alloys or switching to rivet nuts made of stronger materials.
Do You Have Any Questions?
Let Us Solve Your Problem
Why Choose Rivetfix
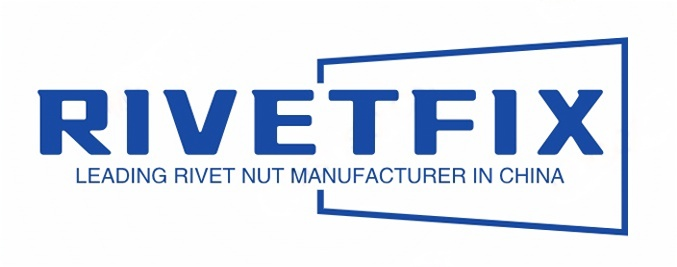
As a leading fastener manufacturer in China with more than 15 years in the industry, Rivetfix are committed to providing first-class quality fasteners and responsive services to the world. We offers a wide range of rivet nuts and clinch nuts designed to meet the unique demands of your projects. Rivetfix ensures you have the right solution for every application. Choose Rivetfix for versatile, cost-effective, and durable fastening solutions tailored to your specific needs. In addition, we can also provide customized rivet nuts service and clinch nuts according to your requirements.
Contact us now for more information and customization options on Rivet Nuts!
Get High Quality Rivet Nuts Quote!
Send Your Rivet Nut Request
For more than 20 years, Rivetfix has helped customers solve many rivet nuts sourcing needs and technical challenges.
Have a question? Contact us and we’ll provide you with the perfect solution.