Top 10 Self Clinch Nut Manufacturers in the World (2025)
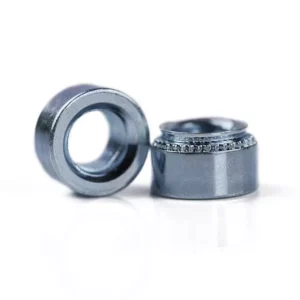
Leading Self-Clinching Fasteners Manufacturer and Supplier in China
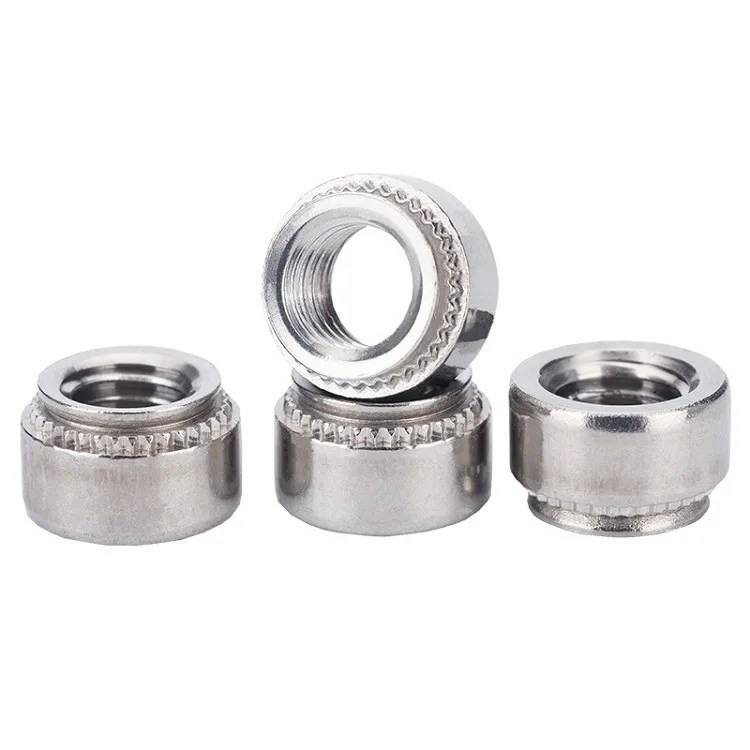
This blog will help you understand the TOP 10 self clinch nut manufacturers in the world and help you find the most suitable manufacturer.
Table of Contents
What Are Self Clinch Nuts?
Self-clinching nuts are fasteners designed to create secure, permanent threads in thin sheet metal or panels. These nuts are inserted into pre-drilled holes in a workpiece, and then they are installed by applying pressure, which causes the nut to “clinching” or embed into the material. The clinching process creates a strong, durable thread that provides excellent resistance to torque and pull-out forces.
These nuts are widely used in applications where threading a hole after assembly is impractical or where traditional nuts and bolts might be difficult to use. They eliminate the need for external hardware like bolts or nuts, providing a clean, secure fastening solution. Self-clinching nuts are available in various materials like stainless steel, carbon steel, and aluminum, and can accommodate different thread types and sizes, making them highly versatile.
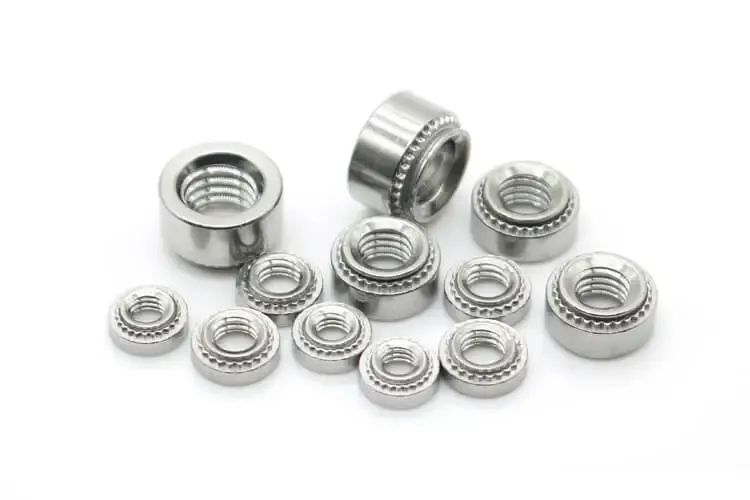
Advantages of Using Self Clinch Nuts
There are many advantages to using self-clinching nuts. They are often used in applications where space, efficiency and strength are critical.
1. Secure, Permanent Fastening
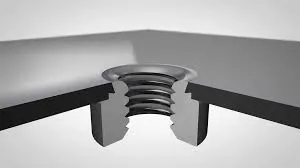
Self-clinching nuts provide a strong, permanent attachment by embedding themselves into the thin sheet metal or panels during installation. The process ensures the nut “clinches” into place, forming a secure mechanical bond without the need for additional fasteners. Once installed, the nut becomes an integral part of the material, offering exceptional resistance to torque, pull-out, and shear forces. They are ideal in industries where long-term stability and durability are critical, such as in aerospace or automotive applications.
2. Space-Saving Design
Self-clinching nuts are perfect for applications where space is constrained. Once installed, these nuts sit flush with the surface of the material, which helps conserve valuable space within assemblies. This flush design allowing components to be stacked or placed closer together without sacrificing strength or performance. As such, self-clinching nuts are widely used in industries such as electronics, automotive, and medical devices, where compact designs are essential for achieving performance while maintaining small form factors.
3. No Need for Threading After Installation
They create a threaded insert in the base material without the need for post-installation threading. This feature greatly streamlines the assembly process because there’s no need to tap or drill threads into the material after installation. This eliminates time-consuming steps in the manufacturing process and reduces the risk of damaging the material. Particularly in high-volume production environments, this feature leads to faster throughput, lower labor costs, and more consistent results.
4. Reduced Assembly Time and Costs
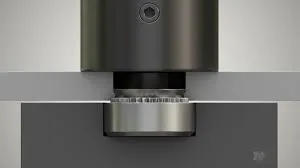
Installation of self-clinching nuts is typically faster and simpler than traditional fastening methods. The nuts are pressed into the material with minimal effort, usually using a hydraulic or manual press, reducing the need for skilled labor or complex equipment. This process drastically cuts down on installation time and labor costs. The fact that no additional hardware is required (e.g., bolts, washers) further reduces the material cost and simplifies inventory management.
5. Strong and Reliable Performance
Self-clinching nuts are engineered to offer exceptional strength and long-lasting performance. The clinching process creates a permanent, durable bond with the parent material, providing high resistance to vibrations, torque, and environmental factors. These fasteners perform well even under challenging conditions. For industries like aerospace, defense, and heavy machinery, where reliability and durability are non-negotiable, self-clinching nuts are an ideal choice, offering dependable fastening that endures over time without failure.
6. Clean, Aesthetic Appearance
A major appeal of self-clinching nuts is their clean, unobtrusive appearance once installed. These fasteners are flush with the surface of the material, which eliminates visible fasteners or protrusions. This not only enhances the aesthetic appeal of the final product but also improves the ergonomics and functionality.
In consumer-facing industries like electronics, medical devices, and high-end consumer goods, this aesthetic benefit is particularly important. A smooth, flush finish ensures the product has a polished, professional appearance and can also reduce the risk of snagging or damage from external forces.
7. Versatility in Material and Size
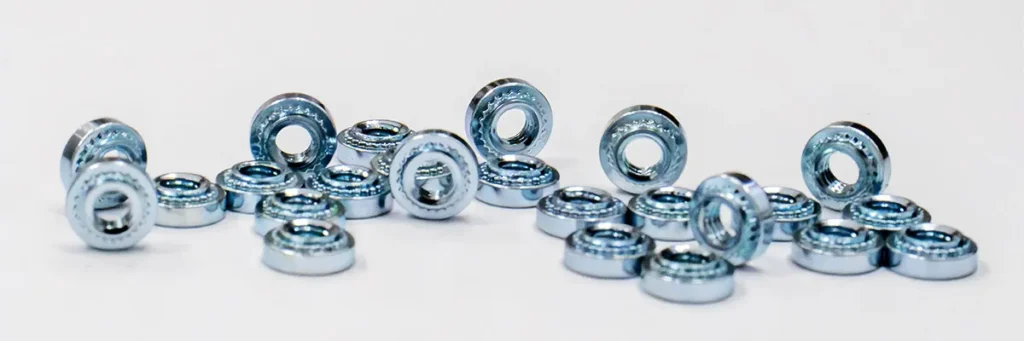
Self-clinching nuts come in a wide range of materials and sizes, offering great flexibility for various applications. Materials such as stainless steel, aluminum, brass, and carbon steel ensure that self-clinching nuts can be used in diverse environments, from highly corrosive conditions to lightweight applications where weight savings are critical.
Additionally, these nuts are available in different thread types (e.g., UNC, UNF, M, or metric threads) and thread sizes, making them suitable for many industries, including electronics, automotive, industrial equipment, and even food processing. Their ability to be customized for specific material properties and design requirements makes them highly versatile.
8. No Need for Additional Hardware
Unlike traditional fasteners, which require nuts, bolts, and washers to complete the assembly, self-clinching nuts eliminate the need for these additional components. The nut itself serves as both the fastener and the threaded insert, reducing the number of parts needed and simplifying the overall design. This reduction in the number of components not only cuts down on material costs but also decreases assembly time, reducing the complexity of the entire assembly process. It also simplifies inventory and logistics, as fewer components need to be managed and stored.
Do You Have Any Questions?
Let Us Solve Your Problem
Top 10 Self Clinch Nut Manufacturers in the World(2025)
Rank | Manufacturer | Country | Main Products |
1 | Rivetfix | China | Rivet nuts, threaded inserts, self clinching fasteners |
2 | PennEngineering | United States | Self-Clinching Nuts (CL series), Self-Clinching Studs & Pins (FH series), Fasteners for Use in PC Boards (K series), MicroPEM® Fasteners (MPF series) |
3 | Bossard Group | Switzerland | Self-Clinching Nuts (CLS-632-2, CLS-440-2), Self-Locating Projection Weld Nuts |
4 | LISI Group | France | HI-LOK™ and HI-LITE™ Fasteners, STARLITE™ Nuts, OPTIBLIND™ Blind Fasteners |
5 | Sundram Fasteners | India | High Tensile Fasteners, Powertrain Components, Pumps & Assemblies |
6 | Nifco | Japan | 2pcs Clip, 1pcs Clip, Trim Clip |
7 | Arnold Umformtechnik | Germany | Thread-Tapping Fasteners, Aluminum Screws, Direct Screw Fastening |
8 | Stanley Engineered Fastening | United States | Nuts & Nut Assemblies, Rivet Nuts, Screws & Bolts |
9 | TONG Stainless Steel (Dong Ming) | Taiwan | Rivet Nuts, Pop Rivets, Expansion Bolts |
10 | Rivmate | China | Rivet nuts, threaded inserts, custom fastening solutions |
The manufacturers listed in our 2025 review represent the pinnacle of superior performance by self clinching nuts manufacturers.
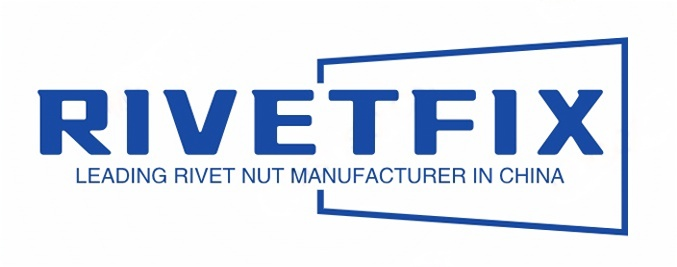
Country:China
Suzhou Rivfix Import & Export Co., Ltd. is a rivet nut manufacturer and supplier integrating R&D, design, production and sales. Since 2012, Rivetfix has supplied a large number of high quality rivet nuts to 2000+ customers worldwide. Currently, we have 200+ production staff and 40+ sales team.
Rivetfix has introduced 64 sets imported multi-station machines and 6 sets selecting machines. Our factory manufactures 400 million pieces of structural rivets and automobile blind rivets, 1 billion standard blind rivets annually now.
Main Products:
- Steel Rivet Nuts
- Self Clinching Nuts
- Self Clinching Studs
- Through-Hole Threaded Standoffs
Core Advantages:
- Over 15 years experience in manufacturing fasteners
- Understand the uniqueness of each project, provide a wealth of customized products
- Provide professional pre-sales and after-sales service to assist customers with selection, technical support and problem solving
- Efficient logistics management system and inventory control
Do You Have Any Questions?
Let Us Solve Your Problem
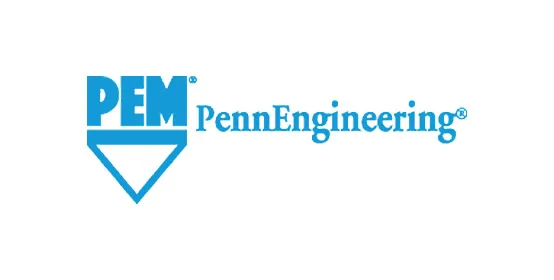
Country: United States
Founded in 1942 by Heinz Bachmann in Pennsylvania, USA, the company initially produced precision components for military applications during World War II. In the 1970s, it invented the world’s first self-clinching nut (PEM® series), marking a significant technological milestone in the industry.
Today, the company operates three major R&D centers in the United States, Germany, and China, with annual R&D investments accounting for 12% of its revenue. Its micron-level self-clinching nuts are used in the lens module fixation of Apple iPhones, with tolerance precision reaching ±0.005mm. In 2024, the company led the revision of the ASME B18.13.5M international standard for self-clinching nuts.
Main Products:
- CL – Self-Clinching Nuts
- FH – Self-Clinching Studs & Pins
- K – Fasteners for Use in or with PC Boards
- MPF – microPEM® Fasteners
Core Advantages:
- Patented “No-Pre-Punch” installation technology, which reduces processing steps.
- Long-term partnerships with leading companies such as Tesla and Apple.
- Offers an online calculation tool (PEM® App) for rapid matching of customer materials and load requirements.
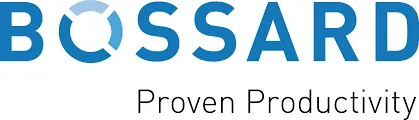
Country: Switzerland
Established in 1831 in Zug, Switzerland, the company initially provided miniature screws for the watchmaking industry. In the 1990s, it transitioned to smart assembly solutions, and in 2018, it introduced ARIMS® (Advanced RFID-based Intelligent Assembly Management System). This system tracks nut installation status using RFID chips and is already implemented by leading companies such as BMW and Siemens.
As of 2023, the company operates a global warehouse space of 420,000 square meters, enabling 12-hour delivery within Europe. In 2024, the company collaborated with ETH Zurich to develop AI-based predictive algorithms to forecast spare parts demand up to six months in advance. Its estimated annual revenue for 2025 is approximately CHF 2.3 billion, with over 2,900 employees.
Main Products:
- CLS-632-2 Self-Clinching Nut
- Self-Locating Projection Weld Nuts
- CLS-440-2 – Self-Clinching Nut
Core Advantages:
- ARIMS® system enables digital management of inventory and assembly processes.
- Customized surface treatments, such as Geomet® coatings, enhance corrosion resistance.
- Quick response to small and medium-sized orders, with support for 3D-printed prototype manufacturing.
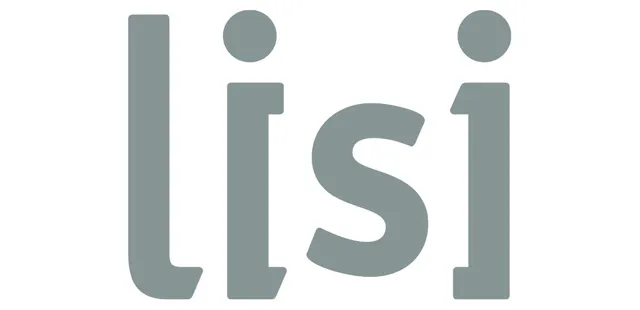
Country: France
Originally established in 1780 as a steel workshop in eastern France, the company shifted focus to aerospace fasteners in 1960, contributing to the development of the Concorde supersonic aircraft.
In 2023, it supplied titanium-aluminum alloy self-clinching nuts to the Airbus A320neo, achieving a 15% weight reduction, which saves approximately $20,000 in fuel costs per aircraft. Its testing laboratory holds the highest NADCAP (National Aerospace and Defense Contractors Accreditation Program) certification and is capable of simulating extreme environments from -55°C to 300°C.
In 2024, the company launched an automated factory in Monterrey, Mexico, focusing on the North American electric vehicle market. By 2030, the company plans to reduce its aerospace business share from 65% to 50%, while expanding its presence in the automotive sector.
Main Products:
- HI-LOK™ and HI-LITE™ Fasteners
- STARLITE™ Nuts
- OPTIBLIND™ Blind Fastener
Core Advantages:
- Proprietary laser etching technology, meeting NASA-level non-destructive testing requirements.
- Collaboration with Safran to develop high-pressure-resistant nuts for aircraft engines.
- Strategic manufacturing in Mexico and Malaysia to reduce supply chain risks in North America and Europe.
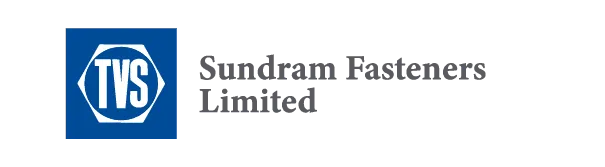
Country: India
Introduction: A subsidiary of the TVS Group, the company was founded in 1966 with a single plant in Chennai. Today, it is the only fastener manufacturer in India with a fully integrated supply chain, covering steel production, forming, and electroplating.
In 2023, the company partnered with the Indian Institute of Technology (IIT) to develop low-friction coating technology, reducing nut installation torque by 22%. Its “FastWheel” initiative aims to establish 100 satellite warehouses across Africa to support mining and infrastructure customers.
According to its 2024 financial report, overseas revenue surpassed 40% for the first time, with key markets in South Africa, Indonesia, and Turkey. The company employs around 8,500 people, with labor costs locally approximately one-fifth of those in Germany.
Main Products:
- High Tensile Fasteners
- Powertrain Components
- Pumps & Assemblies
Core Advantages:
- Localized production in Asia and Africa, offering prices 30% lower than Western competitors.
- Strong partnerships with Tata Motors and Maruti Suzuki.
- ISO/TS 16949 automotive quality management certification.
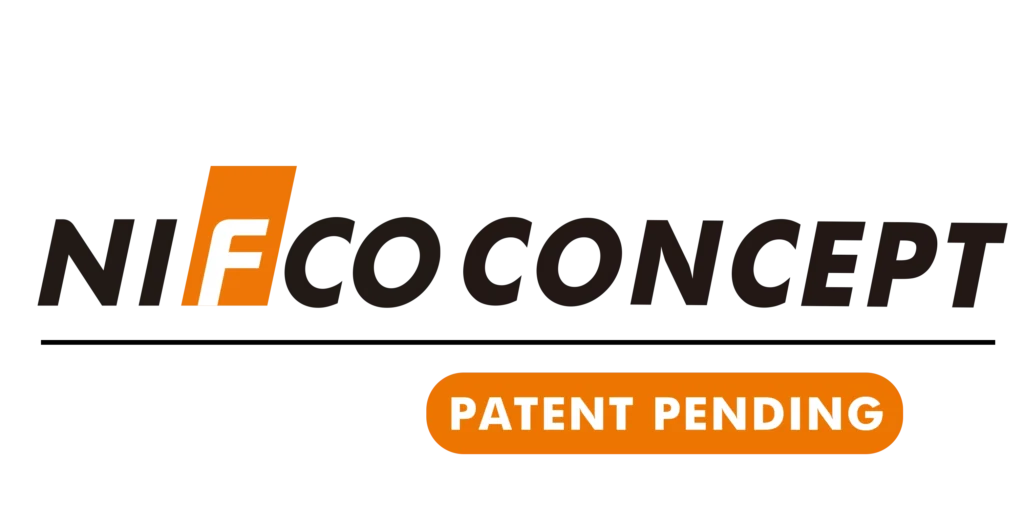
Country: Japan
Established in 1956, initially specializing in plastic buttons, the company was inspired by the 1973 oil crisis to develop resin-metal composite nuts. Its “METAPLAS” series embeds metal threads into plastic substrates, achieving a 30% weight reduction in the battery pack of the Toyota Prius.
In 2024, the company partnered with Toray to develop carbon fiber-reinforced nylon nuts, with a tensile strength of 120 MPa. Domestically, it holds a 70% market share, and globally, it operates 19 technical service centers with a response time reduced to just 4 hours. Its annual production capacity reaches 20 billion units, with 30% dedicated to consumer electronics, including structural components for Sony’s PS6.
Core Advantages:
- Exclusive resin molding technology, reducing metal usage by 30%.
- Provides miniature fasteners for electronic devices to Panasonic and Sony.
- JIS-certified standardized product database that shortens delivery cycles.
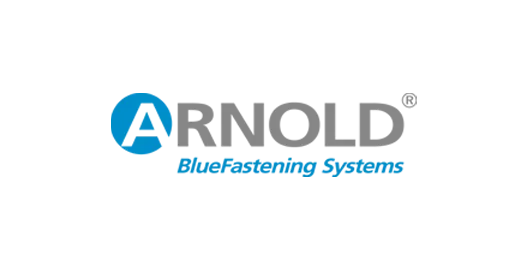
Country: Germany
Founded in 1943 in Hesse, Germany, the company originally served as a military contractor for East Germany during the Cold War. Its patented “MicroGrip” cold-forming technology enables the mass production of M1.2 ultra-micro nuts, used in medical endoscope assemblies.
In 2023, the company invested €120 million to establish a “carbon-neutral factory” that uses geothermal energy and produces 5 billion nuts annually. In the electric vehicle sector, its “CellLock” battery module clinching solution has been adopted by Volkswagen’s MEB platform, improving vibration resistance by 40%. The company expects revenue of €1.4 billion by 2025, with 17% of its R&D team holding Ph.D. degrees.
Main Products:
- Thread-tapping fasteners
- Aluminum screws
- Direct screw fastening
Core Advantages:
- Multi-station continuous cold-heading machines for micron-level tolerance control.
- LEED-certified green factory reducing carbon emissions.
- Offers modular clinching and harness integration solutions, reducing cable junctions.
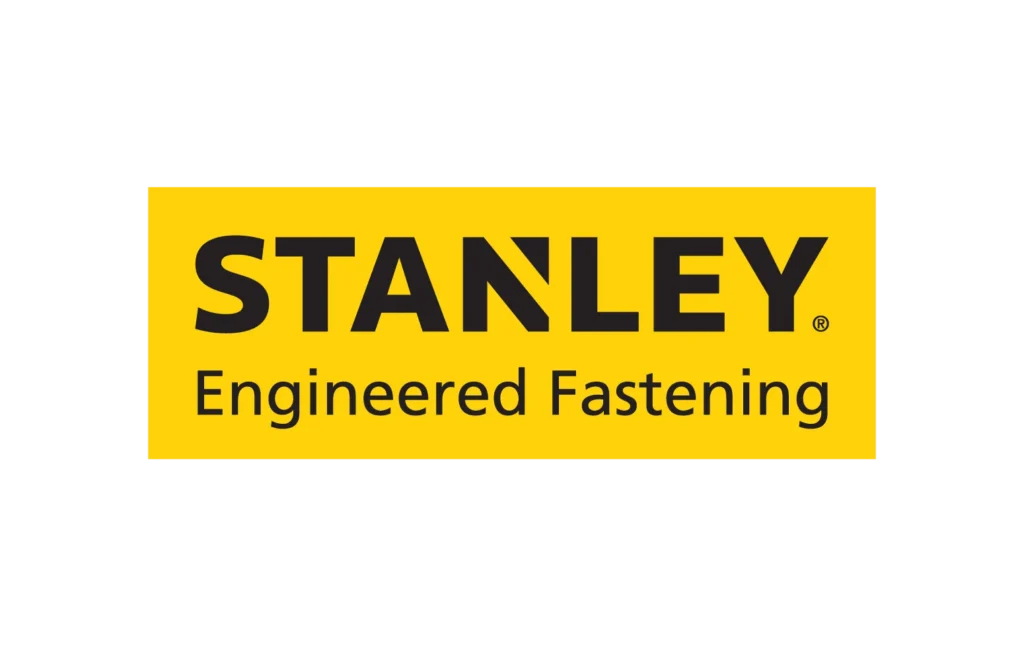
Country: United States
A subsidiary of Stanley Black & Decker, the company traces its roots to the American Screw Company, founded in 1935. Its “SmartTorq” series nuts are equipped with micro-sensors that provide real-time feedback on installation stress data. These have been implemented in Tesla’s Berlin factory for the Model Y chassis assembly line.
In 2024, the company established the largest fastener testing facility in North America in Houston, capable of simulating seismic tremors of up to magnitude 10 and salt-spray corrosion environments. In the nuclear power sector, it is the exclusive supplier of radiation-resistant zirconium alloy nuts for the AP1000 reactor, capable of withstanding temperatures above 800°C. With over 2,200 patents globally, the company serves over 50,000 customers annually.
Main Products:
- Nuts & Nut Assemblies
- Rivet Nuts
- Screws & Bolts
Core Advantages:
- NexGen™ smart assembly platform providing real-time torque feedback.
- Collaboration with General Electric to develop radiation-resistant nuts for nuclear power equipment.
- Over 50 global service centers ensuring 48-hour spare parts supply.
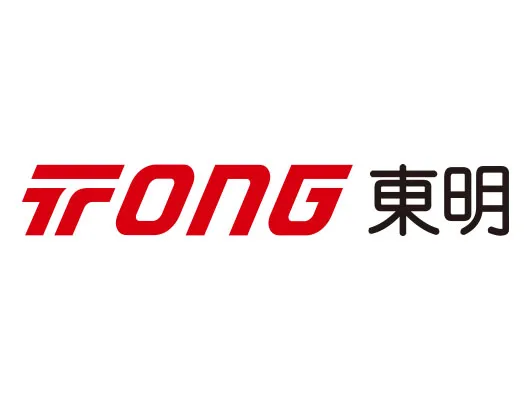
Country: Taiwan, China
Founded in 1976 in Kaohsiung, Taiwan, the company initially provided hardware for yachts.
In 2021, it expanded into the photovoltaic sector by acquiring the Japanese company SST, launching its “SolarGrip” series of self-clinching fasteners, which are UV aging resistant for up to 25 years and adopted by Longi and Jinko Solar.
In 2023, the company’s revenue surpassed $600 million, and its stainless steel procurement accounted for 3% of China’s nickel-iron imports. It established Asia’s first AI visual inspection production line at the Tainan Science Park, achieving a defect detection rate of 99.99%. The company also developed “TitaniumPlus” coated nuts for the Southeast Asian market, designed to withstand high-temperature and high-humidity environments, priced at only 60% of similar products from Europe and the U.S.
Main Products:
- Rivet Nuts
- pop rivets
- expansion bolt
Core Advantages:
- Utilizes vacuum solid solution treatment technology to enhance stainless steel’s resistance to intergranular corrosion.
- Develops specialized anti-salt fog products for desert and coastal regions.
- Operates a low-cost B2B e-commerce platform (TITAN) covering Southeast Asian retailers.
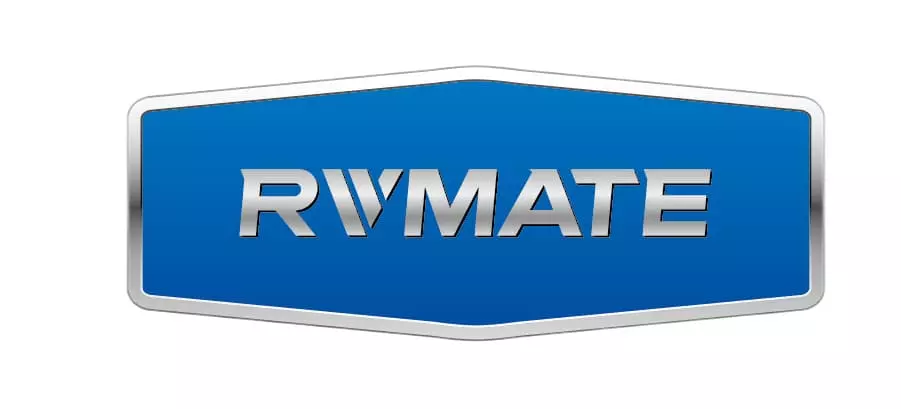
Country:China
Rivemate is dedicating to supply the qualified structural rivets to Europe and the United States and we have established partnership with the world’s top 500 companies such as Stanley and Würth.
Rivmate’s laboratory is equipped with Projector, Tensile & Shear Machines, Hardness Testing Machine, Vision Measuring System, laser selecting machine, Thickness Testing Machine and Salt Spray Testing Machine.
Main Products
- Reduce Head Knurled Body Rivet Nut
Speed Rivets
Core Advantages
- Employ advanced manufacturing technologies and strict quality control processes
- Offer a diverse selection of rivets and fasteners, customize products based on specific requirements, such as size, material, and application.
- Stay ahead of market trends and invest in R&D to develop new technologies that improve product performance and efficiency
- Provide personalized support, fast response times, and flexible solutions
Why Does Rivetfix Stand Out Among Self Clinch Nut Manufacturers
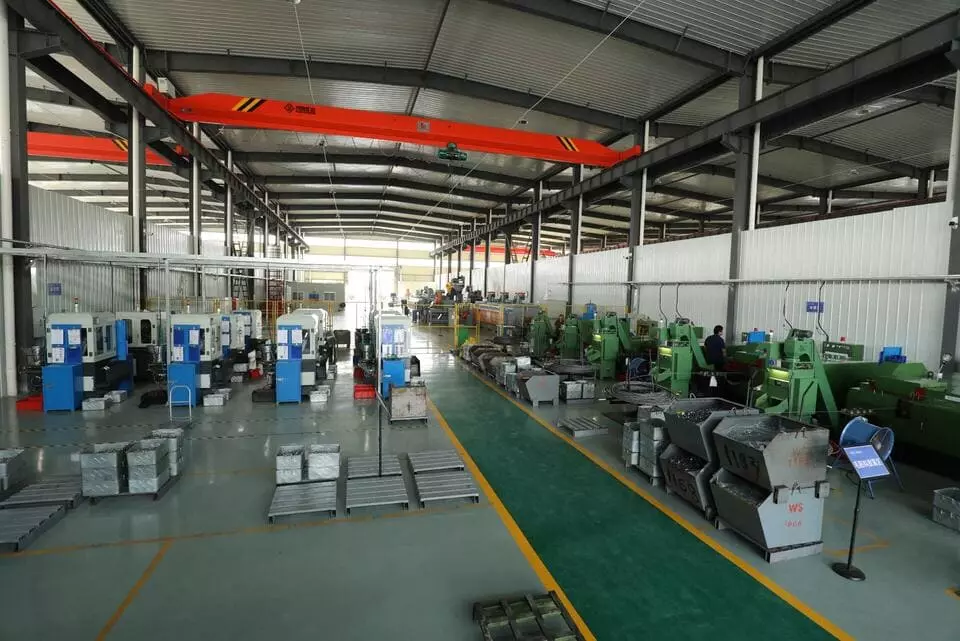
1. Expertise and Experience
With over 15 years of experience in manufacturing self-clinching fasteners, Rivetfix has developed a deep understanding of the unique needs and demands of various industries. This experience allows the company to offer high-quality, reliable solutions tailored to specific customer needs.
2. Innovative Manufacturing Processes
Rivetfix uses cutting-edge technologies and processes to ensure precision and durability in its self-clinching nuts. The company’s commitment to advanced manufacturing techniques guarantees that each product meets stringent quality standards.
3. High-Quality Materials
Rivetfix only uses premium materials such as stainless steel, aluminum, and other corrosion-resistant alloys to produce its self-clinching nuts. This ensures exceptional strength, reliability, and resistance to wear and corrosion, making them suitable for a wide range of applications.
4. Customizable Solutions
Rivetfix offers a wide range of customizable self-clinching nuts. Whether it’s thread sizes, material specifications, or specific finishes, the company works closely with customers to provide the best solution for their specific applications.
5. Global Reach and Customer Support
Rivetfix serves customers worldwide, backed by a dedicated support team. The company’s responsiveness and ability to provide timely solutions help ensure that customers receive the right products, when we need them. You can buy pem nuts directly online.
6. Competitive Pricing
While maintaining high quality, Rivetfix offers competitive pricing. This makes our products an attractive option for both small and large-scale projects, delivering excellent value for money.
7. Commitment to Innovation
Rivetfix continually invests in research and development to enhance the performance and capabilities of its self-clinching nuts. The company stays ahead of the curve in terms of materials, technology, and manufacturing methods, ensuring its products are always at the forefront of the industry.
Summary of Self Clinch Nut Manufacturers
Self-clinch nut manufacturers specialize in providing durable, high-quality fastening solutions for thin sheet metals. Companies like Rivetfix, PennEngineering, and Bossard Group offer custom products for industries such as electronics, automotive, and aerospace. Their focus on precision, advanced materials, and reliable support makes them leaders in the fastener industry.
Custom Self Clinch Nuts Solutions for Your Business with Rivetfix
In this list, Rivetfix is the first choice for the manufacturer of self clinching nuts with its wide range of solutions, services and corporate vision. Whatever your field and nature of the project, we can choose the best product for your needs.
Get free sample proofing or request an instant quote to improve the efficiency of your project now.
Get High Quality Rivet Nuts Quote!
Send Your Rivet Nut Request
For more than 20 years, Rivetfix has helped customers solve many rivet nuts sourcing needs and technical challenges.
Have a question? Contact us and we’ll provide you with the perfect solution.