10 Types of Rivet Nuts You Need to Know
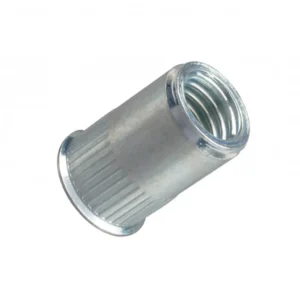
Leading Rivet Nut Manufacturer and Supplier in China
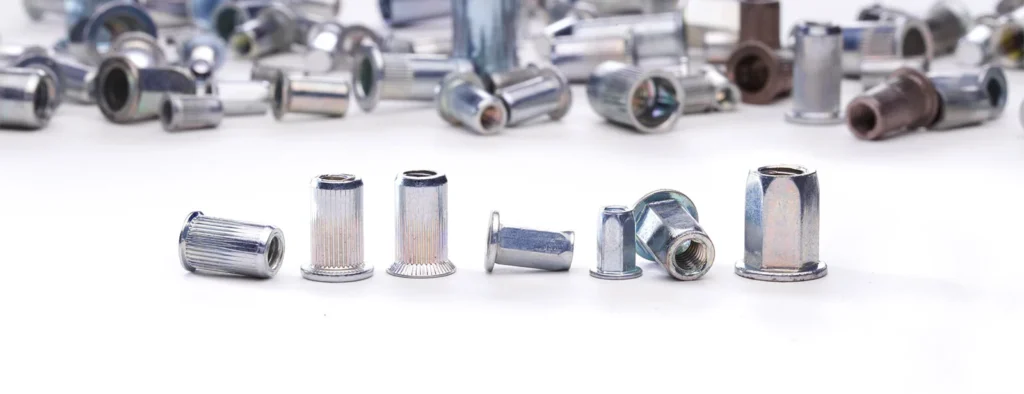
Rivet nuts are a common fastener designed to create strong threaded connections on thin sheets or soft materials. You must know the 10 types of rivet nuts classified by material and design, each has its specific purpose.
Read this blog to help you choose the type of riveted nut that best suits your project needs.
Table of Contents
Basics of Rivet Nut
A rivet nut is a fastener that can create threaded connections on thin sheets or soft materials, suitable for substrates where threading cannot be directly machined.
After installation with special tools, the rivet nut forms a strong threaded connection point within the material, which is commonly used in metals, plastics and composites.
Common use applications are automotive, aerospace, electronics, and other industries that require reliable connectivity and lightweight design.
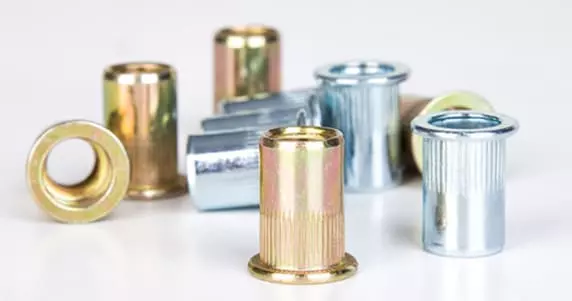
How do rivet nuts form stable joints?
- Insertion: Place a rivet nut (or rivet nut insert) into a pre-drilled hole in the material.
- Deformation: The rivet nut is then deformed using a specialized tool, typically a mandrel or a setting tool. The tool applies pressure to the flange of the rivet nut, causing the material around the nut to expand and securely grip the surrounding surface.
- Formation of a Strong Bond: As the rivet nut deforms, it creates a stable mechanical bond between the nut and the base material. This process locks the rivet nut in place and ensures the joint can withstand high levels of torque and stress.
- Threaded Connection: The thread in the riveted nut provides a solid connection point for the bolt or screw, ensuring a reliable and anti-loosening joint.
The deformation and threaded engagement ensure the rivet nut remains strong under pressure, vibration, or stress, creating a durable joint resistant to loosening.
Do You Have Any Questions?
Let Us Solve Your Problem
10 Different Types of Rivet Nuts
Let’s get to know the most essential 10 types of rivet nuts in terms of material (e.g., steel, stainless steel, aluminum, copper) and design (e.g., countersunk head, reduced head, flat head, hex body, knurled body, round body).
1. Steel Rivet Nut
A steel rivet nut is a type of threaded fastener made from steel, designed for creating a secure, load-bearing thread in thin or soft materials where conventional threading isn’t possible. Known for its high strength and durability, it is ideal for heavy-duty applications in industries such as automotive, construction, and machinery.
2. Stainless Steel rivet Nut
Stainless steel rivet nuts are more corrosion resistant and durablen tha steel rivet nuts, provide a smooth and polished appearance and more beautiful, of course, the price is higher. These rivets nuts are ideal for applications in harsh environments, such as the Marine, automotive and construction industries, where durability and rust protection or chemical exposure are critical.
3. Aluminum Rivet Nut
A aluminum rivet nuts is a type of threaded insert made from lightweight, corrosion-resistant aluminum. Industries like aerospace, automotive, and electronics commonly use aluminum rivet nuts to reduce overall weight while maintaining reliable fastening solutions. They are easy to install and are suitable for use in environments where corrosion resistance is required but without the weight of steel or stainless steel rivet nuts.
4. Copper Rivet Nut
A copper rivet nut is a threaded insert made from copper, known for its excellent electrical conductivity and corrosion resistance. Electronics and power systems often use these rivet nuts to create efficient electrical connections. Industries such as aerospace and automotive favor copper rivet nuts for their high conductivity, durability, and ease of installation.
5. Countersunk Head Rivet Nut
A countersunk head rivet nut is a type of rivet nut designed with a conical shape at the top, allowing it to fit flush with the surface of the material. This design is ideal for applications where a smooth, flat finish is required, such as in aerospace or automotive industries. Countersunk head rivet nuts help prevent snagging and provide a more aesthetically pleasing appearance while maintaining a strong threaded connection.
6. Reduced Head Rivet Nut
Manufacturers design reduced head rivet nuts with smaller, thinner heads compared to standard rivet nuts. This design is ideal for applications where space is limited or surfaces need to be washed, such as the automotive, electronics and aerospace industries. In these industries, space constraints or the need for a more streamlined look are important factors.
7. Flat Head Rivet Nut
A flat head rivet nut features a wide, flat surface that provides a larger bearing area when installed. This design ensures that the rivet nut sits flush against the material, distributing load more evenly and preventing damage to thin or soft materials. Industries like automotive, electronics, and manufacturing commonly use flat head rivet nuts when both aesthetics and strength are equally important.
8. Hex Body Rivet Nut
A hex body rivet nut features a hexagonal shape on its body, which prevents the rivet nut from spinning in the hole after installation. This type is particularly useful for applications where the rivet nut needs to be securely fastened in materials that may be prone to rotation. Automotive, construction, and other industries commonly use hex body rivet nuts for applications requiring high torque and secure fastening.
9. Knurled Body Rivet Nut
A knurled body rivet nut has a textured surface (knurling) on its body. The knurling enhances the nut’s holding power, making it ideal for applications where a secure, non-rotating fastening is essential. Automotive, electronics, and manufacturing widely use this type of rivet nut for reliable and secure threaded connections.
10. Round Body Rivet Nut
A round body rivet nut features a cylindrical design with a smooth, rounded surface. This is the most common and versatile type of rivet nut, used in general applications where a simple, reliable threaded insert is needed. Industries such as automotive, electronics, and general manufacturing widely use them.
Do You Have Any Questions?
Let Us Solve Your Problem
Comparison Between Different Rivet Nuts
This table provides a quick comparison of the above 10 different rivet nuts based on material, key features and best applications.
Rank | Rivet Nut Type | Material | Key Features | Best For |
1 | Steel Rivet Nut | Steel | High strength, cost-effective | Heavy-duty applications |
2 | Stainless Steel Rivet Nut | Stainless Steel | Corrosion-resistant, durable | Harsh or outdoor environments |
3 | Aluminum Rivet Nut | Aluminum | Lightweight, corrosion-resistant | Aerospace, automotive, electronics |
4 | Copper Rivet Nut | Copper | Excellent electrical conductivity, durable | Electrical systems, conductive applications |
5 | Countersunk Head Rivet Nut | Various materials | Flush finish, conical design | Applications requiring a smooth surface |
6 | Reduced Head Rivet Nut | Various materials | Smaller head for tight spaces | Limited space or thinner materials |
7 | Flat Head Rivet Nut | Various materials | Wide, flat bearing surface | Applications requiring load distribution |
8 | Hex Body Rivet Nut | Various materials | Hexagonal shape to prevent spinning | Secure fastening in soft materials |
9 | Knurled Body Rivet Nut | Various materials | Textured surface for improved grip | Soft materials, higher holding power |
10 | Round Body Rivet Nut | Various materials | Cylindrical, simple design | General-purpose fastening |
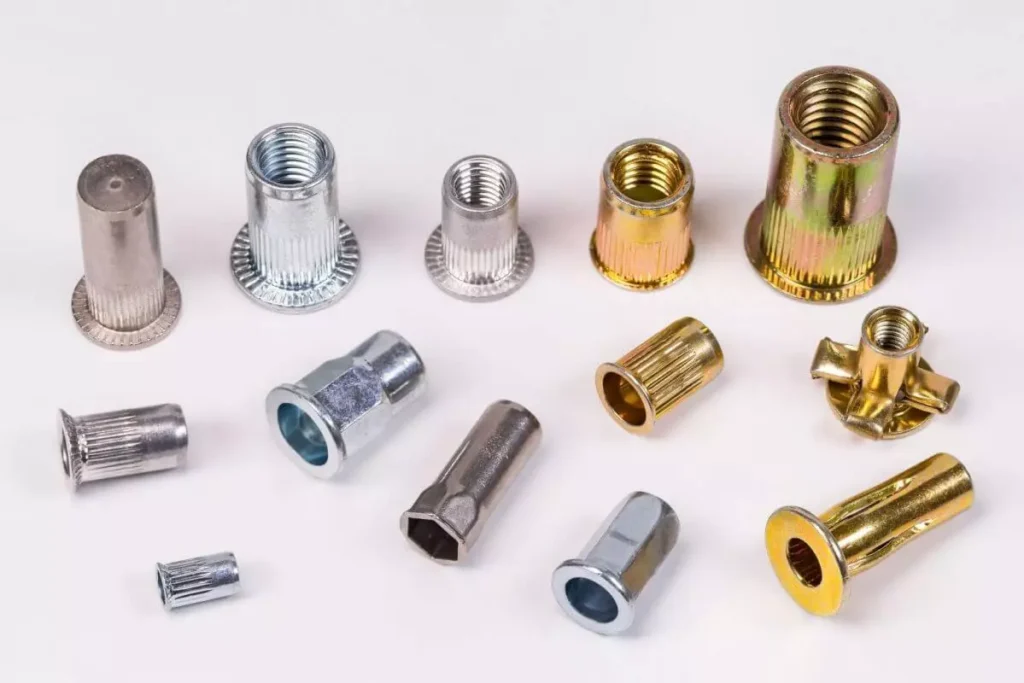
Which Type of Rivet Nut to Choose?
When selecting a rivet nut, various factors must be kept in mind in order to decide on the right type of rivet nut for the right application scenario. Some of the factors to be considered in this regard are as follows:
1. Materials
Select materials suitable for your application (e.g., steel, stainless steel, aluminum, copper, etc.), taking into account strength, corrosion resistance, and weight.
- Steel: Suitable for heavy duty applications, high strength but easy to rust.
- Stainless steel: Corrosion resistant, suitable for harsh environments, such as Marine or chemical environments.
- Aluminum: Lightweight and corrosion resistant, suitable for applications with high weight requirements, such as aviation.
- Copper: Strong conductivity, suitable for electrical and electronic applications.
2. Design Type
According to the installation space and aesthetic requirements to choose the appropriate head and body type (such as flat head, hexagonal body, heavy class).
- Flat head rivet nuts: With a wide bearing surface, suitable for applications requiring a distributed load.
- Countersunk head rivet nuts: Designed to be flush with the surface and suitable for applications requiring a smooth surface effect.
- Hex rivet nuts: Hexagonal design to avoid rotation during installation, suitable for soft materials.
- Knurled rivet nuts: with knurled surface to provide better grip, suitable for soft materials.
3. Installation Method
Determine the feasibility of using manual, pneumatic or hydraulic tools, choosing the appropriate installation method depends on the production scale, tool availability and accuracy requirements.
- Manual installation: Suitable for small batches or simple applications, usually using a rivet gun or hand tool for installation.
- Pneumatic/Hydraulic installation: suitable for mass production, providing greater efficiency and accuracy.
- Mechanical installation: installation by specialized machines, usually used in industrial applications requiring high strength and consistency.
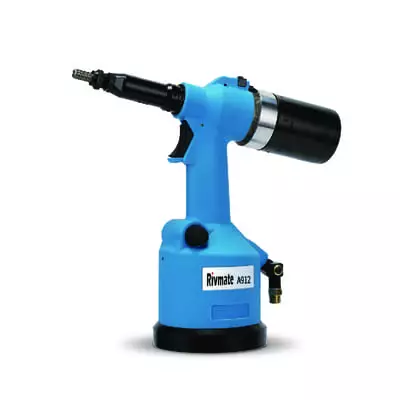
4. Load Requirements
Depending on the application, the riveted nut must be able to withstand specific pulling forces and pressures.
Applications with high load requirements require the selection of rivet nuts with higher tensile strength, such as steel or stainless steel.
For light loads or conventional connections, aluminum or copper rivet nuts are available. Reasonable selection of load requirements helps to ensure the stability and durability of the connection.
5. Environmental Conditions:
- Temperature: Some riveted nuts have special requirements for high or low temperature, especially for automotive, aviation and other fields.
- Humidity and corrosion: For example, in humid and corrosive environments, it is more appropriate to choose corrosion resistant materials such as stainless steel or copper.
- Chemical exposure: In a specific environment, it is necessary to select the type of rivet nut that is resistant to chemical corrosion, such as acid and alkali resistance.
Do You Have Any Questions?
Let Us Solve Your Problem
An Overview of 10 Types of Rivet Nuts
By reading the detailed guide above, you are now clear about the different types of rivet nuts and their suitable application scenarios.
These rivet nuts have been widely used in all walks of life, providing great convenience for manufacturing and assembly. Selecting the right riveted nut can not only optimize the performance, but also improve the engineering efficiency.
FAQ About Different Types of Rivet Nuts
Which performance of different types of riveted nuts is more outstanding?
- Anti-spinning property:Hex Body Rivet Nut>Knurled Body Rivet Nut>Round Body Rivet Nut
- Clamping strength:Countersunk Head Rivet Nut > Flat Head Rivet Nut
- Appearance Requirement: Countersunk Head Rivet Nut (smooth surface)
- Adaptability:Round Body Rivet Nut (the most versatile)
What are open- end and closed-end rivet nuts?
Open-End:Threaded throughout the riveted nut for standard connections
Closed-End: They seal the threaded end to prevent liquid or dust from entering, making it suitable for applications requiring water or dust protection.
Which type of rivet nut is suitable for high torque applications?
Hex body rivet nut or knurled body rivet nut, cause its anti-spin design is more suitable for high-torque scenarios.
Rivetfix: Quality Determines World Influence
Choose a high-quality and reliable rivet nut supplier for your engineering and project needs. At Rivetfix, we ensure rapid response times and deliver the best customer experience. With our expertise, we help maximize your project efficiency and keep your progress on track.
Contact Rivetfix today and take the first step toward seamless project execution!
Get High Quality Rivet Nuts Quote!
Send Your Rivet Nut Request
For more than 20 years, Rivetfix has helped customers solve many rivet nuts sourcing needs and technical challenges.
Have a question? Contact us and we’ll provide you with the perfect solution.