Why You Should Use Blind Threaded Inserts Rivet Nuts Fasteners
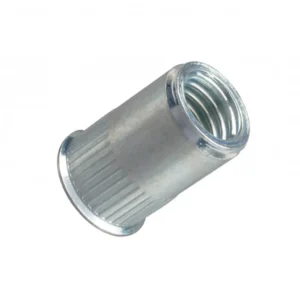
Leading Rivet Nut Manufacturer and Supplier in China
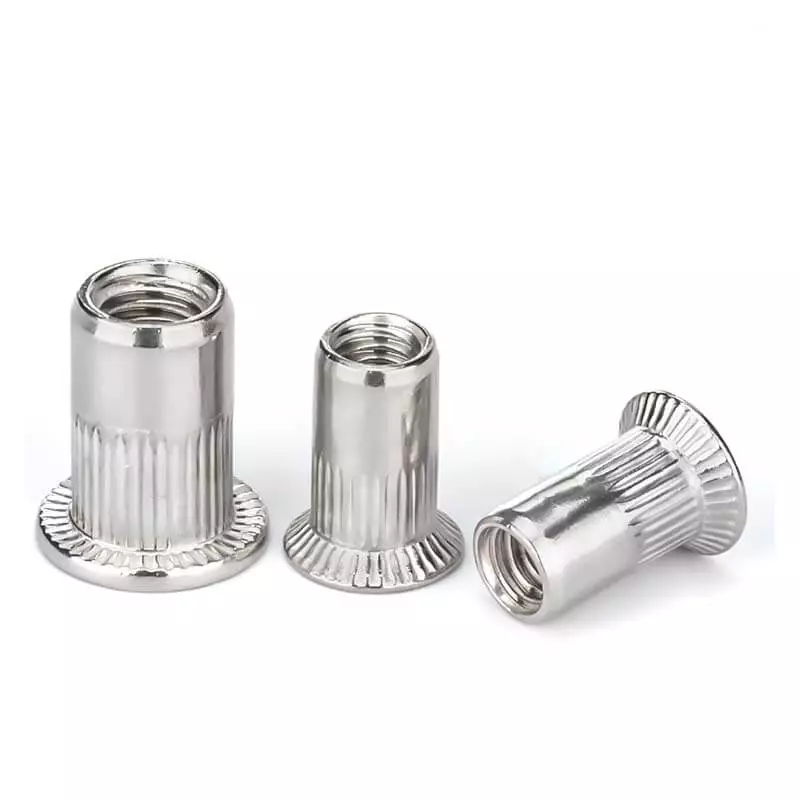
Blind threaded inserts rivet nuts are essential fasteners for creating strong, reliable connections in a variety of materials. Whether you’re working with metal, plastic, or composites, these versatile fasteners provide a secure, durable solution for applications that require high strength and ease of installation. Here’s why you should consider using blind threaded inserts rivet nuts in your next project.
Table of Contents
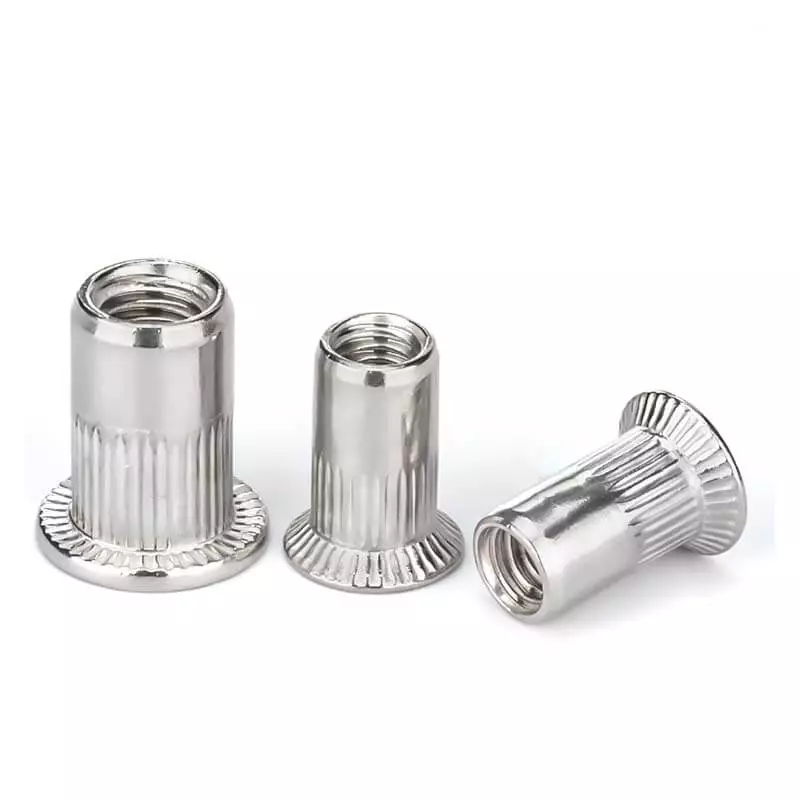
A blind threaded insert, commonly known as a rivet nut, is a special type of fastener designed to create a strong threaded connection on thin sheets, pipes, hollow profiles, or soft materials. It functions both as a nut (with internal threads) and as an insert, allowing for installation on one side, similar to a rivet. Blind rivet nuts are widely used in various industries, including automotive manufacturing, aerospace, rail transportation, machinery, electronics, and furniture manufacturing.
How Do Rivet Nuts Differ from Traditional Nuts and Other Fastening Methods?
Compared to traditional nuts, welding nuts, self-tapping screws, and regular rivets, rivet nuts have the following significant advantages:
1. Suitable for One-Sided (Blind Spot) Installation
Traditional nuts require access to both sides for installation, meaning the bolt must be inserted from one side and the nut tightened from the other. Rivet nuts, however, can be installed from a single side, making them ideal for workpieces that cannot be accessed from the back, such as closed structures, pipes, enclosures, and sheet metal.
2. No Welding Required, Avoiding Heat Impact
Welding nuts require high temperatures, which may cause material deformation, stress concentration, and even damage coatings or corrosion resistance. Rivet nuts, on the other hand, are installed using cold connection methods, preventing changes to material properties and making them suitable for temperature-sensitive materials like aluminum alloys, stainless steel, plastics, and composite materials.
3. Provide Strong and Durable Threaded Connections
In thin materials or low-strength substrates, directly tapping threads or using regular nuts can result in damage due to the material being too thin or the thread strength being insufficient. Rivet nuts can create high-strength threads on these materials and maintain a secure connection even after repeated disassembly.
4. Removable and Maintainable, Ideal for Long-Term Use Equipment
Traditional riveting methods (such as solid rivets or explosion bolts) cannot be disassembled after installation, but rivet nuts have a reusable threaded structure, making maintenance and part replacement more convenient when needed.
5. Suitable for a Variety of Materials, Expanding Application Range
Rivet nuts can be used on metals (steel, stainless steel, aluminum), plastics, composite materials, wood, and more, whereas traditional nuts and welding nuts are often unsuitable due to material limitations.
Table 1: Blind Threaded Inserts Rivet Nuts vs. Traditional Nuts
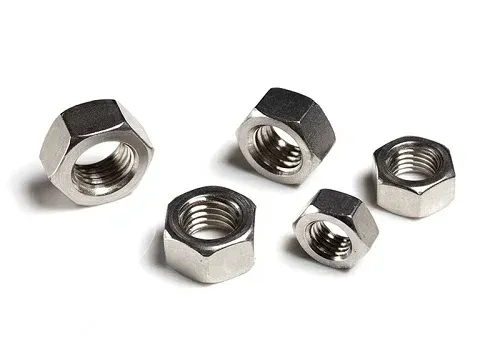
Comparison Item | Blind Threaded Insert Rivet Nuts | Traditional Nuts |
Installation Method | Single-side installation (blind installation), no need for access to the back | Requires access to both sides for installation |
Suitable Materials | Suitable for thin sheets, soft materials, hollow structures | Primarily used for thicker materials |
Connection Strength | Provides stable internal threads, suitable for high-strength connections | Relies on bolts or welding, threads may be damaged |
Removability | Reusable, easy to maintain and replace | May require welding or additional fasteners, difficult to remove |
Processing Requirements | Only requires drilling a hole for installation | May require tapping, welding, or additional fastening components |
Table 2: Blind Threaded Inserts Rivet Nuts vs. Welding Nuts
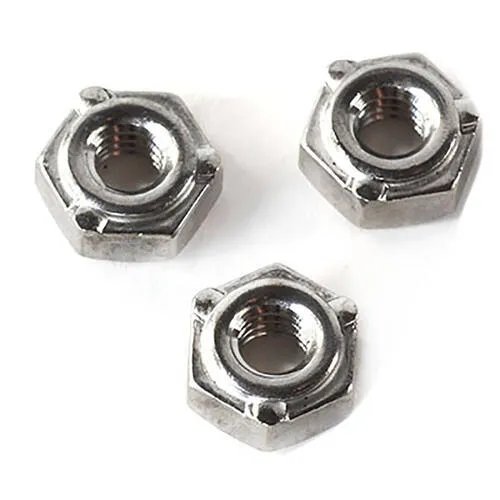
Comparison Item | Blind Threaded Insert Rivet Nuts | Welding Nuts |
Installation Process | Mechanically expanded and secured, no high temperature | Requires high-temperature welding |
Suitable Environment | Suitable for materials that are prone to deformation or cannot be welded (such as plastics, aluminum alloys) | Only suitable for weldable metals |
Strength | Secured by expansion deformation, providing reliable threaded connection | Permanent connection formed after welding, higher strength |
Reversibility | Removable and replaceable | Cannot be removed after welding |
Why You Should Use Blind Threaded Inserts Rivet Nuts Fasteners?
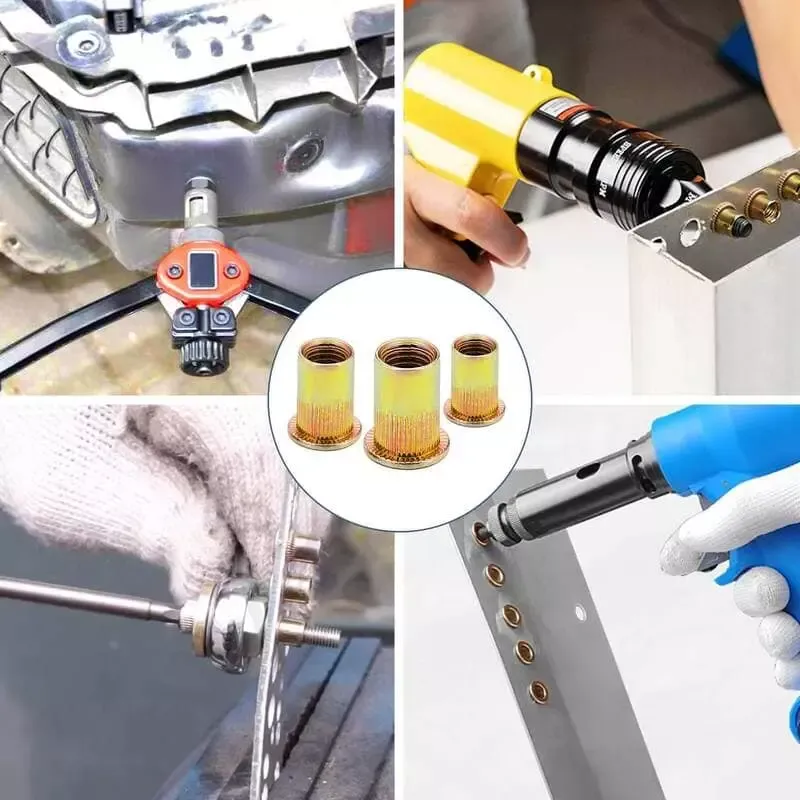
1. Suitable for Blind Hole Installation (Single-Side Operation)
In many structures, the backside is inaccessible or difficult to operate on, such as in closed pipes, body panels, and electronic device enclosures. Blind threaded insert rivet nuts can be installed from one side, without the need for support or additional operations on the back. This makes them an ideal choice for many assembly scenarios. Examples include:
- Automotive Industry: Dashboard brackets, door panels, roof frames
- Cabinet Manufacturing: Metal cabinets, server enclosures, electronic device housings
- Aerospace: Fuselage skins, seat brackets, luggage compartment fasteners
Compared to regular nuts, rivet nuts do not require access to both sides, making installation more convenient and efficient.
2. Enhanced Thread Strength (Especially Suitable for Thin Sheet Materials)
When regular nuts are used on thin sheets or soft materials, they are prone to thread damage or instability due to insufficient material thickness. Blind threaded rivet nuts, through their own deformation and expansion, can provide a more stable threaded connection than direct tapping or self-tapping screws, ensuring long-term reliability.
Suitable scenarios include:
- Thin-walled metals (such as aluminum alloy, stainless steel)
- Plastic products (such as automotive interiors, electronic housings)
- Composite materials (such as carbon fiber boards, fiberglass boards)
On these materials, direct tapping often causes thread stripping or damage, whereas blind threaded rivet nuts provide stronger clamping force, preventing thread loosening or falling off.
3. Suitable for a Variety of Materials (Broad Compatibility)
Blind threaded rivet nuts can be used with a wide range of materials, including metals, plastics, composite materials, unlike traditional welding nuts, which are typically only suitable for metal materials. This makes them highly adaptable, especially in industries requiring lightweight, composite structures or special materials, such as:
- New Energy Automotive Industry (aluminum alloy + composite materials)
- Rail Transportation (lightweight corrosion-resistant materials)
- Electronic Devices (plastic housings + metal brackets)
Additionally, depending on the operating environment, different materials like stainless steel, aluminum, and galvanized carbon steel can be chosen for rivet nuts to meet specific needs for corrosion resistance, rust resistance, and high strength.
4. Quick Installation, Reduces Production Costs
Compared to traditional welding nuts or thread tapping methods, blind threaded rivet nuts offer the following installation advantages:
- No high-temperature welding is required, avoiding the heat-affected zone (HAZ) produced by welding, which could damage the material strength or surface coating;
- No tapping required, eliminating the complex tapping process on thin sheets or hard-to-machine materials, making them especially suitable for high-strength or coated materials;
- Fast installation with dedicated rivet nut guns or tools, improving production efficiency and reducing labor costs.
For industries requiring mass assembly, such as automotive manufacturing, home appliance assembly, and sheet metal processing, blind threaded rivet nuts effectively improve production efficiency and reduce assembly costs.
5. Provides Removable Connections, Facilitates Maintenance and Replacement
After installation, blind threaded rivet nuts form stable internal threaded connections that can be fastened and removed using bolts like regular nuts. This means they are ideal for applications requiring later maintenance, repair, or part replacement, such as:
- Removable enclosures (e.g., servers, industrial control devices)
- Automotive repair (e.g., interior, engine brackets)
- Rail transportation equipment (e.g., seat fasteners)
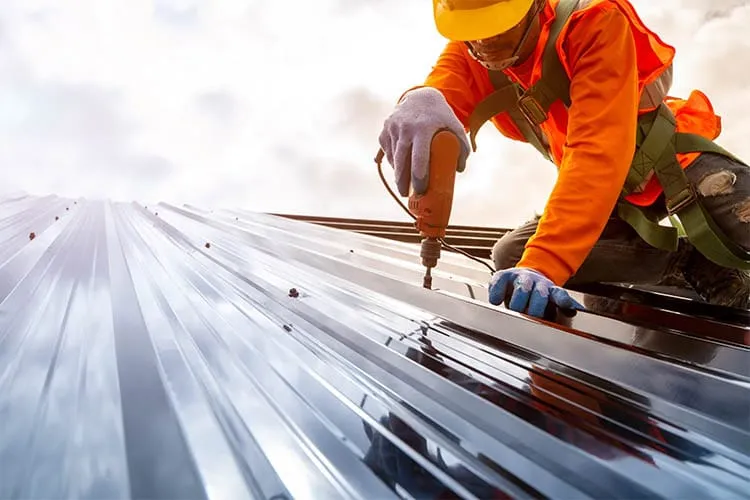
1. Automotive Industry
Blind threaded rivet nuts are widely used in automotive manufacturing, especially for body structures, chassis components, and internal assemblies. They are primarily used in the following areas:
- Body panels: Securing components such as doors, hoods, tailgates, etc.
- Chassis components: Brackets, shields, exhaust system mounting points.
- Automotive interiors: Dashboard, seat brackets, mounting points for in-car electronics.
Given the automotive industry’s demand for lightweight and high-strength connections, blind threaded rivet nuts are particularly suitable for lightweight materials such as aluminum alloys, galvanized steel, and composite materials.
2. Aerospace Industry
In the aerospace industry, fastening components must meet high requirements for weight, strength, and corrosion resistance. Blind threaded rivet nuts, with their ability to provide strong threaded connections in lightweight materials, make them an ideal choice for the sector. Applications include:
- Fuselage skins and frame structures: Providing stable connection points while avoiding damage to materials by traditional bolts.
- Seat fastening and cabin components: Removable connections on lightweight materials such as carbon fiber and aluminum alloys.
- Cargo and luggage compartment structures: Components that require maintainable and high-strength threaded connections.
Blind threaded rivet nuts are typically made from high-strength aluminum alloys or stainless steel to withstand extreme temperatures and vibration conditions in aerospace environments.
3. Electronics & Enclosures
In the manufacturing of electronic devices and precision instruments, blind threaded rivet nuts are widely used for assembling metal housings, enclosures, and cabinets. Key reasons for their use include:
- Suitable for thin-walled metal enclosures, offering more durability than direct tapping.
- Avoiding welding, which prevents high-temperature damage to electronic components.
- Providing stable and removable threaded connections, which facilitate maintenance and component replacement.
Typical applications include:
- Server cabinets, data center enclosures, communication equipment housings.
- Portable electronic devices (e.g., medical devices, industrial control terminals).
- Electronic product housings (e.g., audio equipment, smart home devices).
4. Furniture Manufacturing
The use of blind threaded rivet nuts in furniture manufacturing is becoming more common, particularly for connecting metal frames to wood. Compared to traditional wood screws or adhesive connections, they offer the following advantages:
- Improved assembly strength, preventing screws from loosening over time.
- Suitable for soft materials (e.g., particleboard, MDF), providing stronger connections.
- Easy to disassemble and reinstall, facilitating maintenance or structural adjustments.
Common applications include:
- Metal frame furniture (e.g., office desks, chairs, cabinets).
- Wooden furniture (e.g., bed frames, wardrobes, bookshelves).
- DIY assembly furniture, enhancing installation efficiency and stability.
5. Industrial Equipment
In the industrial equipment and machinery manufacturing sectors, blind threaded rivet nuts are commonly used due to their high strength, corrosion resistance, and adaptability to various materials. They are used in the following applications:
- Machine enclosures and sheet metal parts: Such as machine tool guards, equipment cabinets.
- Equipment frames and brackets: For industrial robots, conveyor systems.
- Heavy machinery structures: Including construction machinery, power equipment, and wind energy devices.
In industrial applications, blind threaded rivet nuts provide strong threaded connections on metals or composite materials of limited thickness while minimizing the impact of welding on material performance, improving assembly efficiency and reliability.
Do You Have Any Questions?
Let Us Solve Your Problem
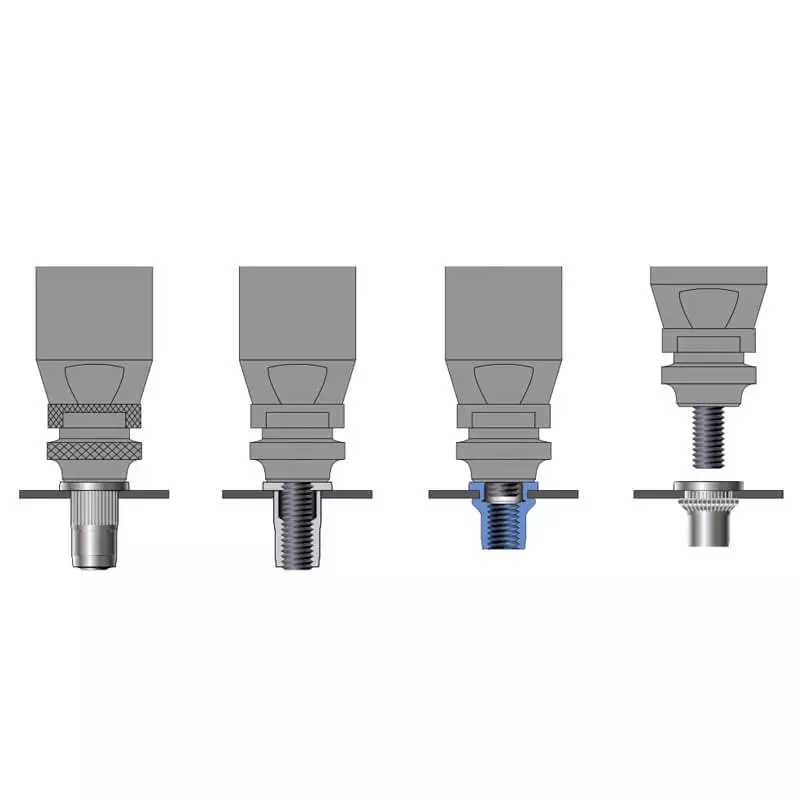
Based on installation needs and production scale, different types of installation tools can be selected:
- Hand Tools: Suitable for small-scale production or maintenance, simple operation, and low cost.
- Pneumatic Tools: Suitable for medium-scale production, fast installation speed, and ideal for standard production lines.
- Electric Tools: Suitable for high-efficiency production, offering precise torque control to improve installation quality and consistency.
2. Installation Steps
1. Drilling the Hole
- Use the appropriate size drill bit to drill the hole according to the rivet nut specifications, ensuring the hole diameter matches the rivet nut.
- Remove any burrs and debris from the hole to ensure smooth insertion of the rivet nut.
2. Insert the Rivet Nut
- Place the rivet nut into the drilled hole, ensuring that the flange or head is flush against the surface of the workpiece.
- Ensure that the rivet nut is aligned properly to avoid tilting, which could affect installation quality.
3. Set the Rivet Nut with the Tool
- Screw the tool’s rod into the internal threads of the rivet nut.
- Trigger the tool (manual/pneumatic/electric) to pull the rod, causing the rivet nut to deform and clamp tightly onto the material.
- Release the rod to separate the tool from the rivet nut, completing the installation.
4. Check Fastening Strength
- Gently twist the rivet nut to ensure it is firmly fixed and does not loosen or rotate.
- Test the bolt installation to ensure the threads are intact and can withstand the appropriate tensile and torque loads.
3. Installation Considerations
Proper Hole Size
- A hole that is too large may cause the rivet nut to loosen, while a hole that is too small may affect the installation quality. Be sure to select the correct hole size based on the specifications.
Material Thickness Requirements
- Ensure that the rivet nut’s grip range is suitable for the material thickness, as incorrect thickness may result in the rivet nut failing to deform properly and secure the material.
Torque Control
- Excessive torque can damage the rivet nut or cause material deformation, while too little torque may result in an insecure installation. When using electric tools, set the appropriate torque parameters.
Prevent Spinning
- For high-torque applications, consider using hexagonal rivet nuts to enhance anti-rotation capabilities. For standard round rivet nuts, anti-spin grooves can be added to the material to prevent rotation during use.
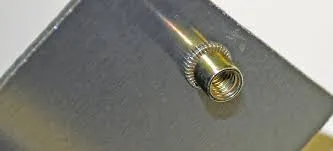
1. Material Type
Different base materials (such as metals, plastics, or composites) require different types and materials of rivet nuts. Depending on the hardness, thickness, and use of the base material, select the appropriate rivet nut material. For example:
- Metal Base Materials: Choose carbon steel or stainless steel rivet nuts to ensure strength and durability.
- Rivet nuts for Plastic and Composite Materials: Choose Jack Nuts to avoid damaging the material during installation.
2. Load Requirements
Select the appropriate rivet nut material and specifications based on the load demands of the application:
- High-Strength Applications: Choose high-strength materials like carbon steel or stainless steel rivet nuts to withstand higher tensile forces and torque.
- Light Load Applications: Opt for lightweight materials like aluminum alloy to reduce weight and cost.
Ensure the rivet nut specifications meet the load requirements to avoid overloading or loosening.
3. Environmental Factors
Rivet nuts perform differently in various environmental conditions, so choose the right material and type based on the operating environment:
- Moist or Corrosive Environments: It is recommended to choose sealed rivet nuts with a closed-end design, which helps prevent moisture, dust, or contaminants from entering, protecting the internal threads from corrosion.
- High-Temperature or Special Chemical Environments: Select rivet nut materials that are resistant to high temperatures or chemical corrosion, such as stainless steel or nickel alloys, to ensure reliability in extreme conditions.
When selecting a rivet nut, it is crucial to ensure the correct matching of thread specifications, outer diameter, and installation hole size:
- Thread Specifications: Choose a thread specification that is compatible with the bolts or screws that will be used, with common sizes such as M3, M4, M5, M6, etc.
- Outer Diameter: Ensure that the outer diameter of the rivet nut matches the installation hole to prevent loosening or installation issues.
- Installation Hole Size: Select the correct hole diameter based on the rivet nut’s outer diameter and type, and ensure the hole depth and shape are compatible.
Do You Have Any Questions?
Let Us Solve Your Problem
Where to Buy Rivet Nuts?
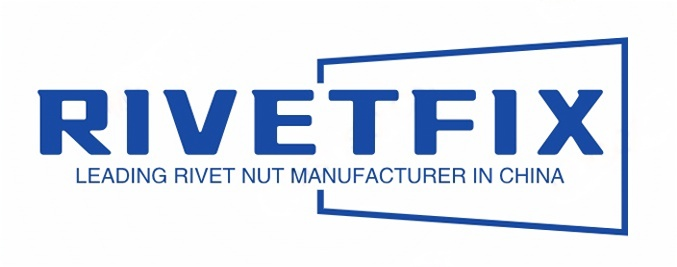
As a leading fastener manufacturer in China with more than 15 years in the industry, Rivetfix are committed to providing first-class quality fasteners and responsive services to the world.
Rivetfix offers a wide range of rivet nuts designed to meet the unique demands of your projects. With different sizes and types of rivet nuts, Rivetfix ensures you have the right solution for every application. Choose Rivetfix for versatile, cost-effective, and durable fastening solutions tailored to your specific needs. In addition, we can also provide customized rivet nuts service according to your requirements.
Contact us for project advice and the latest rivet nut quote!
Get High Quality Rivet Nuts Quote!
Send Your Rivet Nut Request
For more than 20 years, Rivetfix has helped customers solve many rivet nuts sourcing needs and technical challenges.
Have a question? Contact us and we’ll provide you with the perfect solution.