What Tool Is Used to Install Rivnuts?
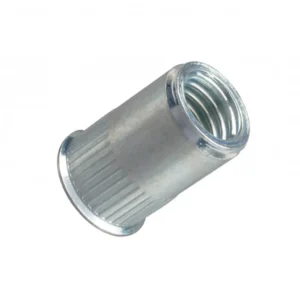
Leading Rivet Nut Manufacturer and Supplier in China
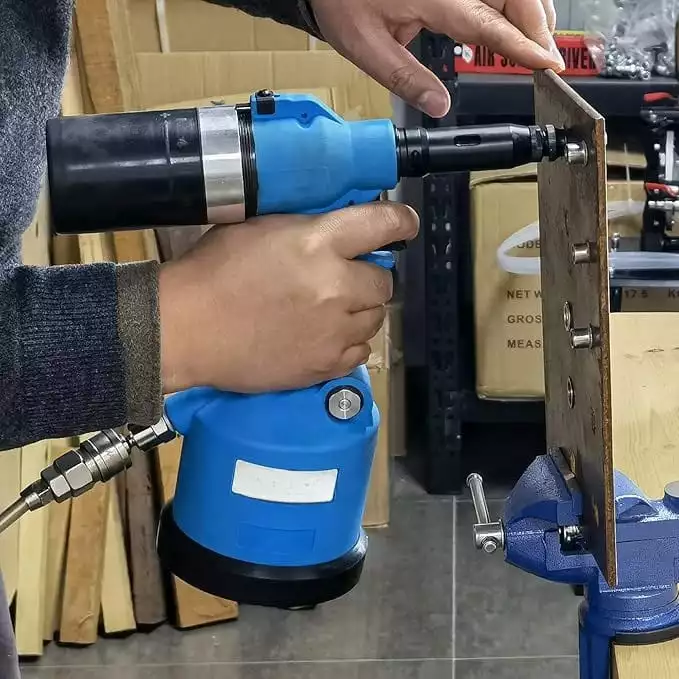
If you’re working with thin metal sheets, tubing, or enclosed structures, Rivnuts—also known as rivet nuts or threaded inserts—are one of the most effective ways to create strong internal threads. But to install them properly, using the right tool is essential. So, what tool is used to install Rivnuts, and how do you choose the best one for your application? In this guide, we’ll explore the most common types of Rivnut installation tools, their working principles, advantages, and how to select the ideal tool based on your needs, whether you’re doing a DIY project or managing a high-volume industrial assembly line.
Table of Contents
What Are Rivnuts and Why Do They Require Special Installation Tools?
1. Definition and Structural Features of Rivnuts
Rivnuts, also known as rivet nuts or threaded inserts, are fastening components designed to create strong internal threads in thin sheet materials or tubes. Their basic structure includes:
A hollow cylindrical body with internal threads;
A deformable tail section, often conical or cylindrical, that allows plastic deformation during installation;
A flange (such as round, countersunk, or reduced flange) that enhances the locking surface area.
Rivnuts are compatible with various materials including aluminum, steel, and stainless steel. They are widely used in industries such as automotive, aerospace, electrical enclosures, sheet metal fabrication, and equipment assembly.
Insert the rivet nut into a pre-drilled hole in the base material;
Insert the rivet nut into a pre-drilled hole in the base material;
Use a special tool to pull a mandrel through the internal threads of the rivet nut;
As the mandrel is pulled, the tail section compresses and expands outward, forming an “umbrella-like” shape;
This deformation clamps the base material between the flange and the expanded tail, forming a secure and vibration-resistant connection;
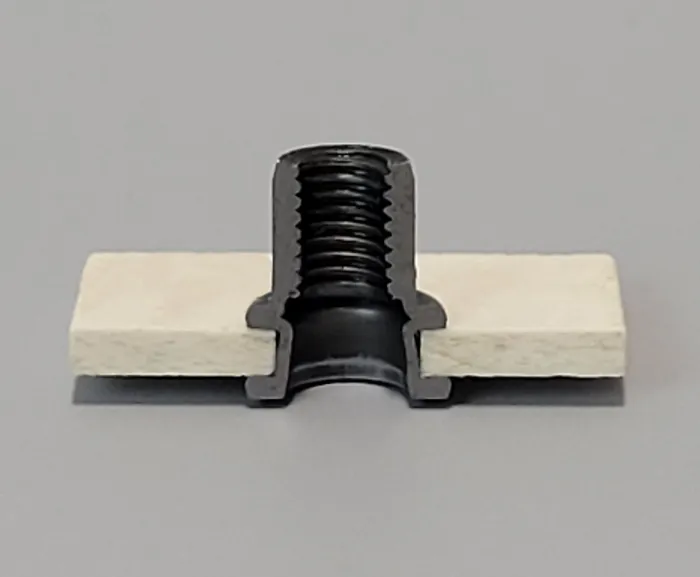
- The installation can be completed from one side only, making it ideal for blind or enclosed applications.
3. Why Do Rivnuts Require Special Tools?
Since rivnut installation involves precise control of high pulling force and deformation, special tools are essential to ensure quality and consistency:
Hand rivet nut tools: Ideal for small batches and lightweight nuts (e.g., aluminum M4–M6);
Electric or pneumatic rivet nut guns: Suitable for medium-to-large rivet nuts or higher volume production, offering stable and adjustable pulling force;
Hydraulic rivet nut equipment: Used in industrial assembly lines for heavy-duty or large-size rivet nuts (e.g., M10–M12);
Mandrel and anvil sets: Must match the specific rivnut size to ensure effective force transmission during installation.
Different rivnut types and materials (e.g., stainless steel or thick-wall nuts) require higher torque or pulling force. Improper tool selection or settings can lead to:
Loose installation, spinning, or pull-out failures;
Incomplete or over-deformation of the tail, causing damage to the base material;
Uneven force distribution during installation, leading to poor fastening performance.
What Tool Is Used to Install Rivnuts?
A hand rivnut tool is a manually operated device that installs rivet nuts by leveraging mechanical force. It typically uses a lever mechanism where pulling the handle stretches the tail of the rivet nut, causing it to deform plastically and securely fasten to the sheet material. This tool features a simple structure, making it portable and easy to maintain—ideal for small-batch jobs, field repairs, or temporary installations.
Working Principle:
The user manually pulls the handle, which drives the mandrel to stretch the tail of the rivet nut, forming a tight mechanical lock.
Application Range:
Best suited for smaller rivet nut sizes (typically M3–M6), as the pulling force is limited.
Advantages:
- Low cost and easy to use for beginners.
- No need for power or air supply—suitable for remote or field applications.
- Compact design, easy to carry and operate.
Disadvantages:
High manual labor—can cause fatigue with prolonged use.
Low installation efficiency—not suitable for mass production.
Limited torque and pulling force may lead to incomplete installation or reduced fastening strength.
An electric rivnut tool uses a motor to drive the mandrel, stretching the rivet nut and securing it in place. It is an upgraded alternative to manual tools, ideal for medium-batch production or maintenance tasks in manufacturing and assembly environments.
Working Principle:
The internal motor pulls the mandrel automatically. The user only needs to hold the tool and press the trigger—very simple to operate.
Application Range:
Suitable for M4–M10 rivet nuts, covering most industrial installation needs.
Advantages:
- Effortless operation reduces fatigue and improves efficiency.
- Features torque and force control for consistent, high-quality installation.
- Many models offer adjustable speed and force to suit different materials and rivnut sizes.
- Available in both corded and cordless (battery-powered) versions for greater flexibility.
Disadvantages:
- More expensive than manual tools.
- Requires regular maintenance of the motor and battery.
- Some models may be bulky, making them harder to use in confined spaces.
This type of industrial-grade tool uses compressed air or hydraulic power to drive rivet nut installation. It is designed for high-frequency, high-volume production and is widely used in automotive manufacturing, aerospace, and mechanical assembly lines.
Working Principle:
Pneumatic rivet nut guns generate powerful and consistent pulling force on the mandrel, causing the rivet nut to deform and lock tightly to the base material.
Application Range:
Ideal for larger rivet nuts (M6–M12) and fastening on medium to heavy-duty components.
Advantages:
High pulling force—can reach 10–20 kN, suitable for heavy-duty applications.
Fast installation speeds—ideal for improving production efficiency on assembly lines.
Excellent repeatability—ensures uniform installation quality.
Reduces operator fatigue and human error due to automated operation.
Disadvantages:
High equipment cost and the need for compressed air or hydraulic systems increase setup complexity.
Bulky size reduces flexibility—less suitable for confined spaces or mobile work.
Higher maintenance costs—requires regular servicing of pneumatic or hydraulic components.
4. Electric Drill with Rivnut Adapter (Mandrel Kit)
This solution uses a standard electric drill paired with a rivnut adapter or mandrel kit to perform installation. It is ideal for light-duty, occasional use, especially in DIY projects or small-scale field repairs.
Working Principle:
The rotating motion of the drill drives the adapter’s mandrel, which stretches and deforms the rivet nut to lock it in place.
Application Range:
Suitable for installing small to medium rivet nuts (typically M3–M6) where high precision is not critical.
Advantages:
Low-cost and widely available, ideal for budget-conscious users.
Lightweight and portable—great for on-site use.
Simple to operate—perfect for those without specialized riveting equipment.
Disadvantages:
Lacks precise torque or pulling force control—may result in inconsistent or weak installations.
Not suitable for high-frequency or large-scale industrial applications.
Pulling force generated by rotational motion is often less effective than specialized rivnut tools.
What Is The Best Rivet Nut Tool?
Ideal for small-batch installation or on-site repair work. Easy to operate and low in cost, but less efficient and can cause fatigue with prolonged use. Suitable for installing rivet nuts from M3 to M6.
Suitable for medium-volume production. Offers easier operation and higher efficiency. Generally supports rivet nuts from M4 to M10. The downside is its higher cost compared to manual tools and the need for a power supply.
Designed for high-volume industrial assembly lines. Offers fast and stable installation performance and supports M4 to M12 rivet nuts. The drawbacks include higher equipment cost and the need for a compressed air system.
Drill with Rivnut Attachment
Suitable for DIY or portable use. Lightweight and widely available, it can install rivet nuts from M3 to M8. However, it has lower installation accuracy and stability, making it less suitable for industrial-scale production.
Comparison Table: Choosing the Right Rivet Nut Installation Tool
Tool Type | Suitable Scenario | Installation Size Range | Advantages | Disadvantages |
---|---|---|---|---|
Manual Rivet Tool | Small batch / Repair | M3–M6 | Low cost, simple to use | Low efficiency, tiring |
Electric Rivet Tool | Medium batch production | M4–M10 | Easy operation, efficient | Medium cost, needs power |
Pneumatic Rivet Tool | High-volume assembly line | M4–M12 | Fast, stable, industrial | High cost, needs air supply |
Drill + Attachment | DIY / Portable use | M3–M8 | Lightweight, accessible | Lower precision, unstable |
How To Choose Rivet Nut Tools?
Choosing the right rivet nut installation tool depends on several key factors, including application scenario, installation frequency, required fastening strength, and budget. Below is a detailed guide tailored to different needs:
a. For Personal Repair / DIY Users
For personal or DIY projects, high-frequency or high-strength installation is usually not required.
A manual rivet nut tool or a drill with a rivnut attachment is an ideal choice. These tools are affordable and easy to use, making them suitable for occasional use. However, they offer limited efficiency and stability, and are best suited for small-size rivet nuts (e.g., M3–M6).
b. For Small to Medium-Scale Factories / Industrial Use
Small to mid-sized production environments require more efficient and reliable tools.
An electric rivet nut tool meets the needs of medium-batch installation and supports a wide range of thread sizes (typically M4–M10). It is labor-saving and faster in operation. Electric tools often come with torque control features to ensure consistent installation quality, making them a highly recommended option for most small and medium factories.
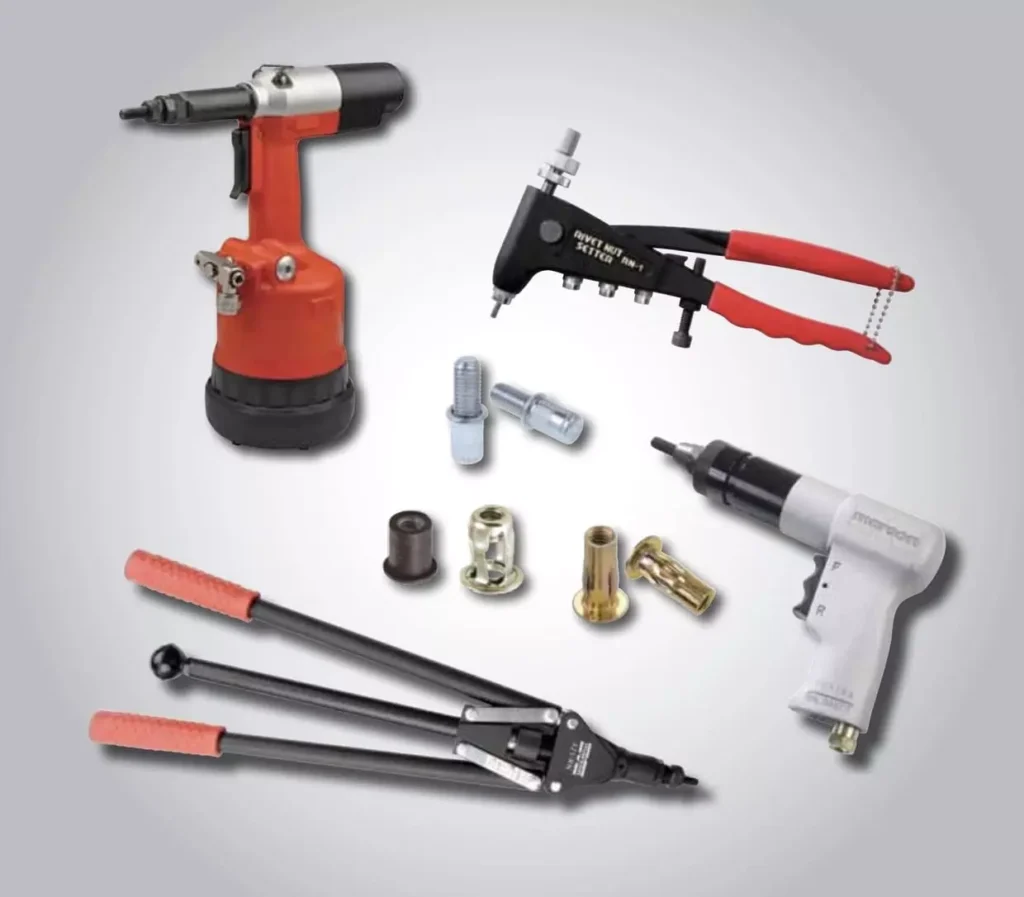
c. For Automated Production Lines / Heavy-Duty Applications
In high-volume assembly lines or for installing large-size rivet nuts (e.g., M10–M12) and structural components, pneumatic or hydraulic rivet nut tools are the best choice.
These industrial-grade tools offer high pulling force (10–20 kN or more), fast installation speed, and excellent repeatability. They are ideal for demanding fastening applications but require a higher equipment investment and maintenance cost, as well as access to compressed air or hydraulic systems.
d. For High Strength or Precision Applications
When connection strength, reliability, and consistency are critical, it is recommended to use electric or pneumatic rivet nut tools with torque control features.
Torque control helps prevent over- or under-installation, ensuring that each rivet nut achieves the designed clamping force and anti-rotation performance, thereby avoiding structural safety issues caused by installation defects.
What Installation Tips Should You Know for Rivnut Tools?
① Use the Correct Mandrel and Anvil Sizes
When installing rivet nuts, the mandrel and anvil used with the tool must match the rivet nut’s thread size exactly. Using the wrong mandrel size can cause uneven force distribution, poor installation quality, or even damage to the rivet nut or base material.
For example, when installing an M6 rivet nut, you should use a dedicated M6 mandrel and matching anvil to ensure smooth and secure fastening.
② Adjust Pull Force and Stroke Based on Rivet Nut Specifications
Different rivet nut sizes, materials, and grip ranges require different levels of pull force and stroke distance. The tool should be adjusted according to the rivet nut manufacturer’s recommended settings to avoid over-stretching (which can damage the nut or base material) or under-stretching (which can lead to weak fastening).
For instance, an M5 rivet nut typically requires a pull force of 5.0–7.5 kN and a stroke of approximately 5.0–6.0 mm.
③ Perform Regular Maintenance and Replace Worn Parts
Over time, mandrels, anvils, and other tool components wear out, leading to unstable pull force and substandard installation results. To maintain installation quality and tool longevity, establish a routine maintenance schedule and replace worn parts promptly. This ensures your tool remains in optimal working condition and maintains consistent performance.
FAQs
1. Can Different Tools Install All Types of Rivnuts?
Not all tools are suitable for installing every type of rivnut.
Manual rivet nut tools are suitable for installing aluminum or small carbon steel rivnuts (e.g., M3–M6);
Electric rivet nut tools generally cover aluminum, carbon steel, and stainless steel rivnuts from M4 to M10, provided they have sufficient torque;
Pneumatic/hydraulic tools are the only reliable option for stainless steel and large-size rivnuts (e.g., M10–M12), due to their higher pull force and stability.
2. If the Rivnut Rotates After Installation, Is It a Tool Issue or a Hole Issue?
In most cases, it is a hole issue, though improper tool settings can also contribute.
If the hole diameter is too large or has burrs, the rivnut cannot tightly fit, causing rotation;
If the tool does not provide enough pull force or the stroke is incorrectly set, the rivnut will not expand and lock properly, leading to rotation.
It is recommended to check if the hole diameter is within the recommended tolerance (±0.1 mm) and verify if the tool parameters meet specifications.
3. What Are Common Causes of Installation Failure with Electric Tools?
Though electric tools are efficient, improper operation or settings can lead to installation failures:
Insufficient pull force or torque settings, resulting in incomplete swaging;
Worn mandrels or anvils causing uneven force or slipping;
Workpiece not clamped or aligned properly, causing misalignment during installation;
Rivnut not centered correctly in the hole;
Installation clearance too tight, causing insufficient clamping force.
4. What Happens When Rivnuts and Tools Are Incompatible?
When tools do not match the rivnut, the following issues may occur:
Mandrel cannot thread into the rivnut or spins freely after threading;
Rivnut loosens, rotates, or collapses after installation;
Tool damage such as broken mandrel or stripped anvil;
Rivnut does not fully deform, causing insufficient clamping force.
Always verify that the thread size and pitch match the tool accessories, especially ensuring mandrel thread profile compatibility before use.
5. How to Determine if a Rivnut Is Properly Installed?
The following methods can quickly verify correct installation:
Visual inspection: The rivnut flange should sit flush against the workpiece surface without obvious lifting or deformation;
Manual test: Twist the rivnut by hand or with a torque tool to confirm no rotation or looseness;
Pull-out test: Check if the rivnut’s pull-out force meets technical requirements (e.g., M6 ≥ 4.5 kN);
Bolt test fit: Ensure the bolt screws in smoothly without binding or thread stripping;
Sampling inspection: For mass production, randomly test 2%–5% of rivnuts using pull testers or torque wrenches to verify clamping quality.
Do You Have Any Questions?
Let Us Solve Your Problem
Buy Rivet Nuts or Rivet Nut Tools from Rivetfix
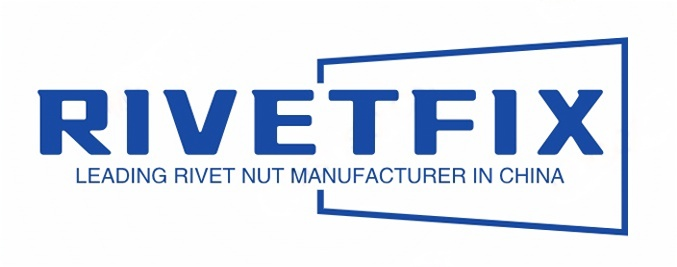
As a leading fastener manufacturer in China with more than 15 years in the industry, Rivetfix are committed to providing first-class quality fasteners and responsive services to the world.
Rivetfix offers a wide range of rivet nuts and rivet nut tools designed to meet the unique demands of your projects. Rivetfix ensures you have the right solution for every application. Choose Rivetfix for versatile, cost-effective, and durable fastening solutions tailored to your specific needs. In addition, we can also provide customized rivet nuts service according to your requirements.
Contact us for project advice and the latest rivet nuts and rivet nut tools quote!
Get High Quality Rivet Nuts Quote!
Send Your Rivet Nut Request
For more than 20 years, Rivetfix has helped customers solve many rivet nuts sourcing needs and technical challenges.
Have a question? Contact us and we’ll provide you with the perfect solution.