Top 10 Questions Answered About Rivet Nut Applications
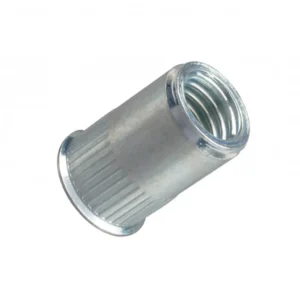
Leading Rivet Nut Manufacturer and Supplier in China
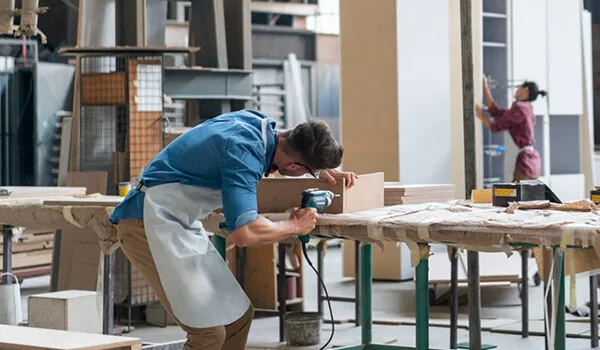
Rivet nuts are widely used in various industries, providing strong and reliable threaded connections in thin or soft materials. Understanding the key aspects of rivet nut applications can help you choose the right type for your specific needs. In this blog, we will answer the top 10 most common questions about rivet nut applications, covering materials, installation methods, load requirements, and more. These insights will help you make informed decisions and ensure the best performance for your fastening needs.
Table of Contents
What Are the Main Rivet Nut Applications?
a. Main Application Materials:
Rivet nuts are fasteners widely used across various industries, providing reliable threaded connections in thin-walled, soft, or composite materials. They are easy to install, have strong load-bearing capacity, and can adapt to various materials and conditions.
- Metal Materials: Such as steel, stainless steel, aluminum alloys, copper, etc.
- Plastics: Engineering plastics like ABS, PVC, PC, etc.
- Composite Materials: Carbon fiber, fiberglass, laminate boards, etc.
b. Main Application Scenarios:
1. Automotive Industry
- Body and Interior: For securing parts like dashboards, seats, door panels, etc.
- External Accessories: For installing roof racks, bumpers, guard rails, etc.
- Chassis and Structural Parts: For reinforcing brackets, suspension systems, battery pack enclosures (electric vehicles), etc.
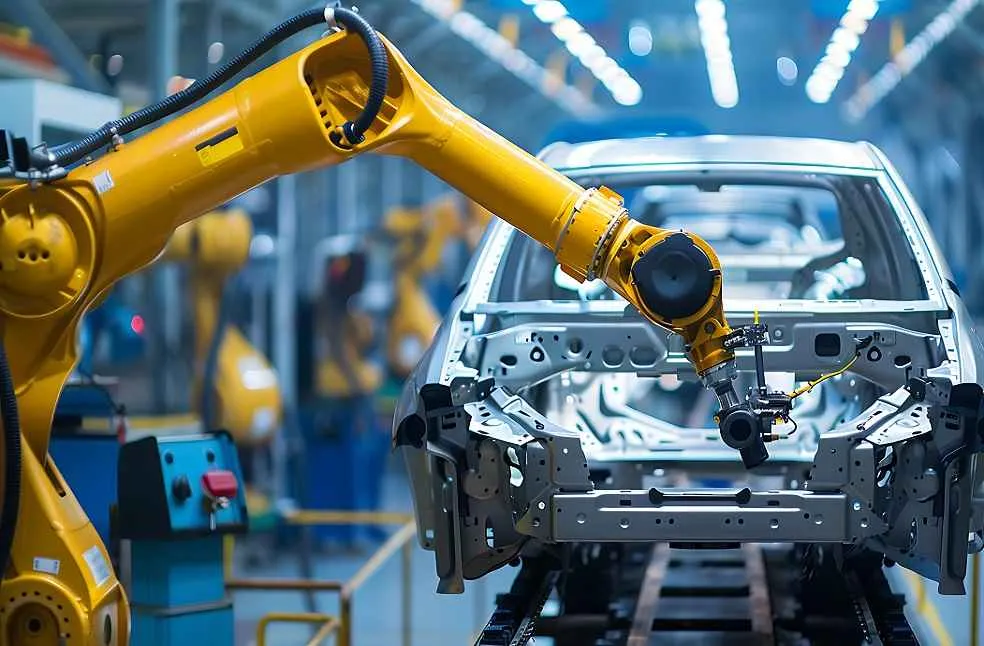
2. Aerospace
- Fuselage Structure: For connecting bulkheads, skins, and internal components of the fuselage.
- Seats and Interior: For securing seats, partitions, overhead bins, etc.
- Electronic Equipment: For installing avionics and instrument panels.
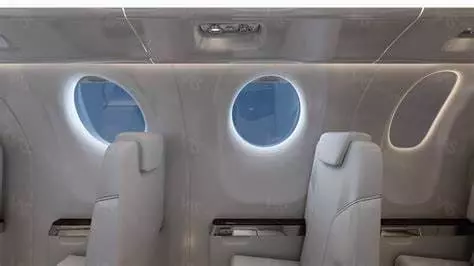
3. Construction and Infrastructure
- Curtain Walls and Steel Structures: For securing metal frames and structural components.
- HVAC Systems: For installing ducts, ventilation equipment, and brackets.
- Photovoltaic Solar Systems: For securing mounts and panels.
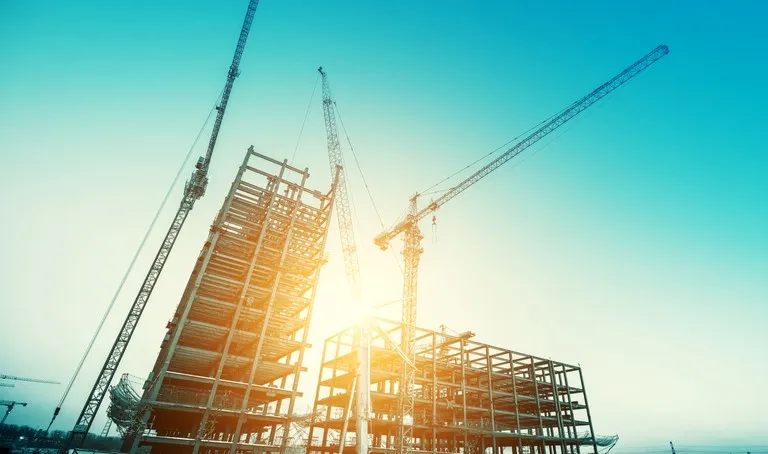
4. Electronics and Electrical Industry
- Electronic Enclosures: For assembling electrical appliances, instrument boxes, server racks, etc.
- Circuit Board Mounting: For attaching heat sinks, terminal connections, etc.
- Industrial Control Cabinets: For electrical connections and enclosure mounting.
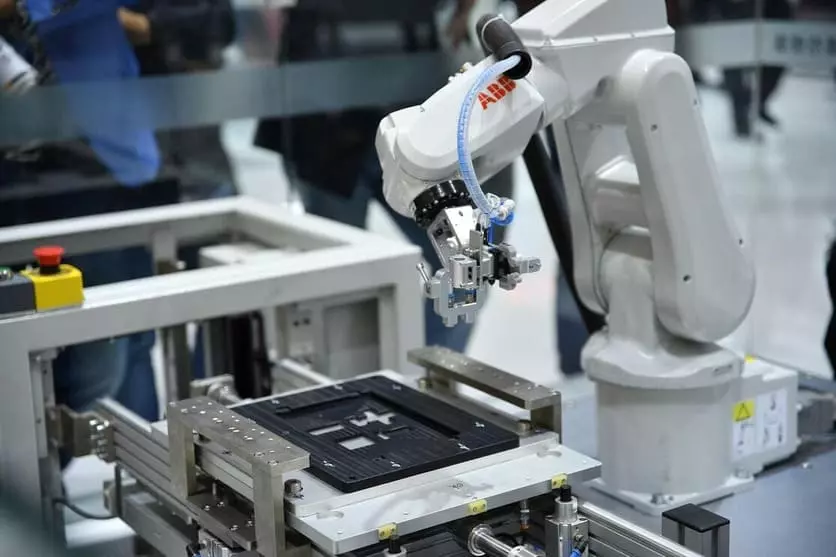
5. Furniture and Home Appliances
- Modular Furniture: For assembling aluminum frames, wood, or plastic components.
- Home Appliances: For internal fastening in products like washing machines, refrigerators, ovens, etc.
- Office Equipment: For securing casings of printers, copiers, industrial machines, etc.
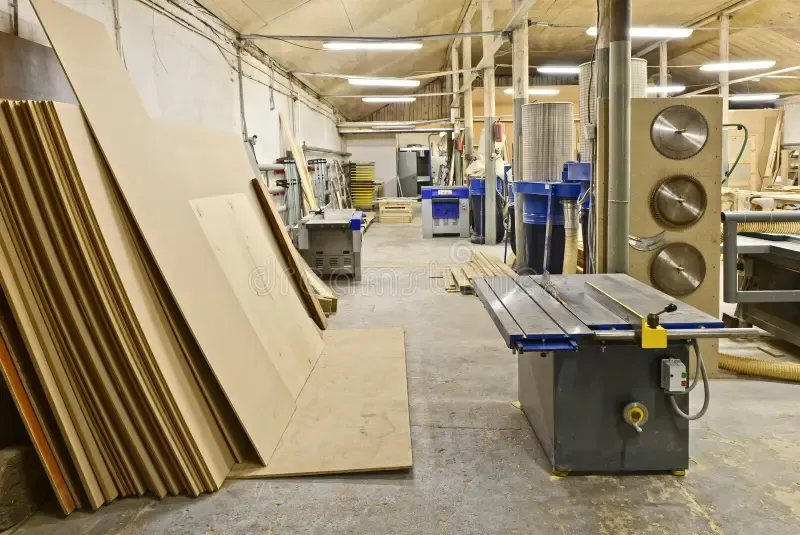
Do You Have Any Questions?
Let Us Solve Your Problem
Choose the Most Suitable Rivet Nut for Your Project - Top 10 Questions to Answer Before Getting a Quote
1. What Material Are You Fastening Into?
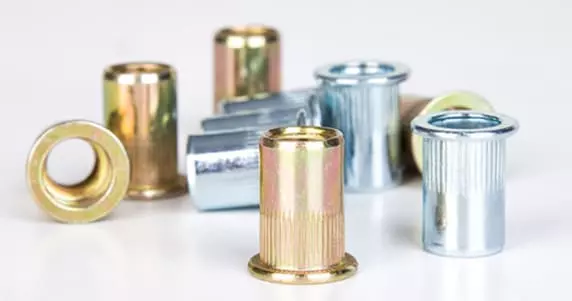
a. Metal (Steel, Aluminum, Stainless Steel)
Requires high-strength rivet nuts for durability.
- Steel rivet nuts are ideal for heavy-duty applications.
- Aluminum rivet nuts are lightweight and corrosion-resistant.
- Stainless steel rivet nuts offer superior corrosion resistance for harsh environments.
b. Plastic & Composites
For non-structural applications in plastics and composites—such as securing panels, electrical components, or enclosures—jack nuts provide a more secure and reliable fastening solution.
- Better Load Distribution: Expands behind the material, preventing stress concentration.
- Vibration Resistance: Absorbs movement and reduces loosening over time.
- Ideal for Thin or Fragile Materials: Works well where rivet nuts might be too rigid or cause damage.
c. Fiberglass & Carbon Fiber
- Needs specialized rivet nuts to distribute load evenly.
- Large-flange or countersunk rivet nuts help prevent cracking or delamination.
2. What Load and Strength Requirements Must Be Met?
Factor | Description | Example Data |
---|---|---|
Load Type | Determines the type of load (tensile or shear) the fastener will handle. | Tensile strength: 6000 N (steel rivet nut) Shear strength: 4500 N (aluminum rivet nut) |
Material Compatibility | The material being fastened will affect the load capacity. | Steel: 6000 N (steel rivet nut) Aluminum: 3500 N (aluminum rivet nut) |
Application-Specific Requirements | Consider if the fastener needs resistance to dynamic loads or vibration. | Automotive: 4500 N tensile strength for undercarriage Aerospace: 7000 N for structural parts |
Size & Thread Specifications | Size of the rivet nut affects its load-bearing capacity. | M10 steel rivet nut: 5000 N M8 steel rivet nut: 3500 N |
Safety Margin | A margin to account for unexpected forces. | 1.5× safety margin: 4500 N design load becomes 6750 N for safety |
3. What Thread Size Is Required?
a. External Thread Size
- The external thread size corresponds to the diameter of the rivet nut’s outer threads, which will fit into the hole of the material being fastened.
- Common external thread sizes include M3, M4, M5, M6, M8, M10, M12, etc.
- For example, an M6 rivet nut would have an external thread diameter of 6mm.
b. Internal Thread Size
- The internal thread size corresponds to the diameter of the threaded hole inside the rivet nut, where the bolt or screw will be inserted.
- Typical internal thread sizes may also be expressed as M followed by the size, such as M6, M8, M10, etc., corresponding to the bolt size.
- For example, an M8 rivet nut can accommodate an M8 bolt with a 8mm diameter.
c. Thread Pitch
- Thread pitch refers to the distance between each thread crest and is crucial for ensuring a secure connection between the bolt and rivet nut.
- Common thread pitches for metric sizes are:
- Coarse thread (e.g., M6x1.0) – A standard thread pitch, suitable for most applications.
- Fine thread (e.g., M6x0.75) – Provides stronger connections due to the finer threads, ideal for high-torque applications.
d. Material and Load Requirements
- The thread size should align with the material thickness and load-bearing capacity required.
- For heavier-duty applications (e.g., aerospace, automotive), use larger thread sizes such as M12 or M16.
- For lighter-duty applications (e.g., electronics, furniture), M4 or M6 thread sizes may suffice.
4. What Grip Range Is Needed?
When selecting a rivet nut, the grip range specifies the thickness of material that the rivet nut can fasten effectively. The grip range is crucial to ensuring the rivet nut expands correctly, providing a secure and lasting connection.
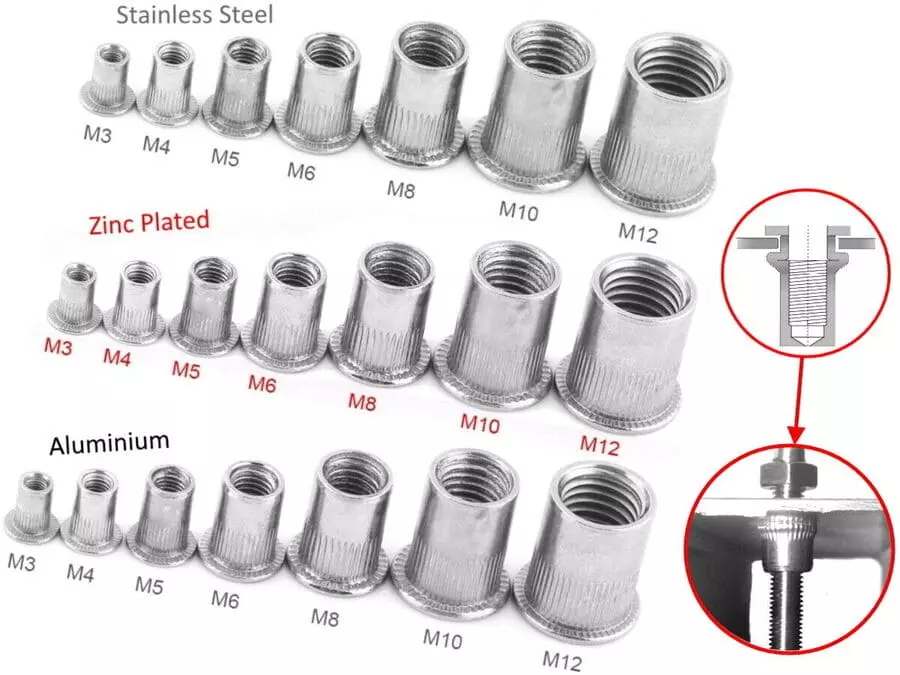
M6 Rivet Nut
- Grip Range: 1mm to 4mm
- This rivet nut is suitable for materials with thicknesses ranging from 1mm to 4mm. For example, if you’re working with aluminum sheet of 2.5mm thickness, an M6 rivet nut with this grip range would be an ideal fit.
M8 Rivet Nut
- Grip Range: 2mm to 6mm
- This rivet nut works well with materials from 2mm to 6mm thickness. If you’re fastening steel sheet that is 5mm thick, an M8 rivet nut with this grip range would be appropriate.
M10 Rivet Nut
- Grip Range: 3mm to 8mm
- Suitable for materials with thickness between 3mm and 8mm. For instance, if you’re working with composite panels that are 6mm thick, this rivet nut would provide the necessary grip.
M12 Rivet Nut
- Grip Range: 4mm to 10mm
- Ideal for thicker materials, such as plastic sheets or thin metal plates, ranging from 4mm to 10mm thick.
5. What Material Should the Rivet Nut Be Made Of?
- Steel: High strength, good for heavy-duty applications.
- Aluminum: Lightweight and corrosion-resistant.
- Stainless Steel: Excellent corrosion resistance for harsh environments.
- Brass: Good electrical conductivity for electronic applications.
6. What Type of Flange Is Required For Different Rivet Nut Applications?
- Small Flange: For flush installation with minimal protrusion.
- Large Flange: Provides more surface area for load distribution.
- Countersunk: Allows for a completely flush finish.
7. What Installation Method Will You Use?
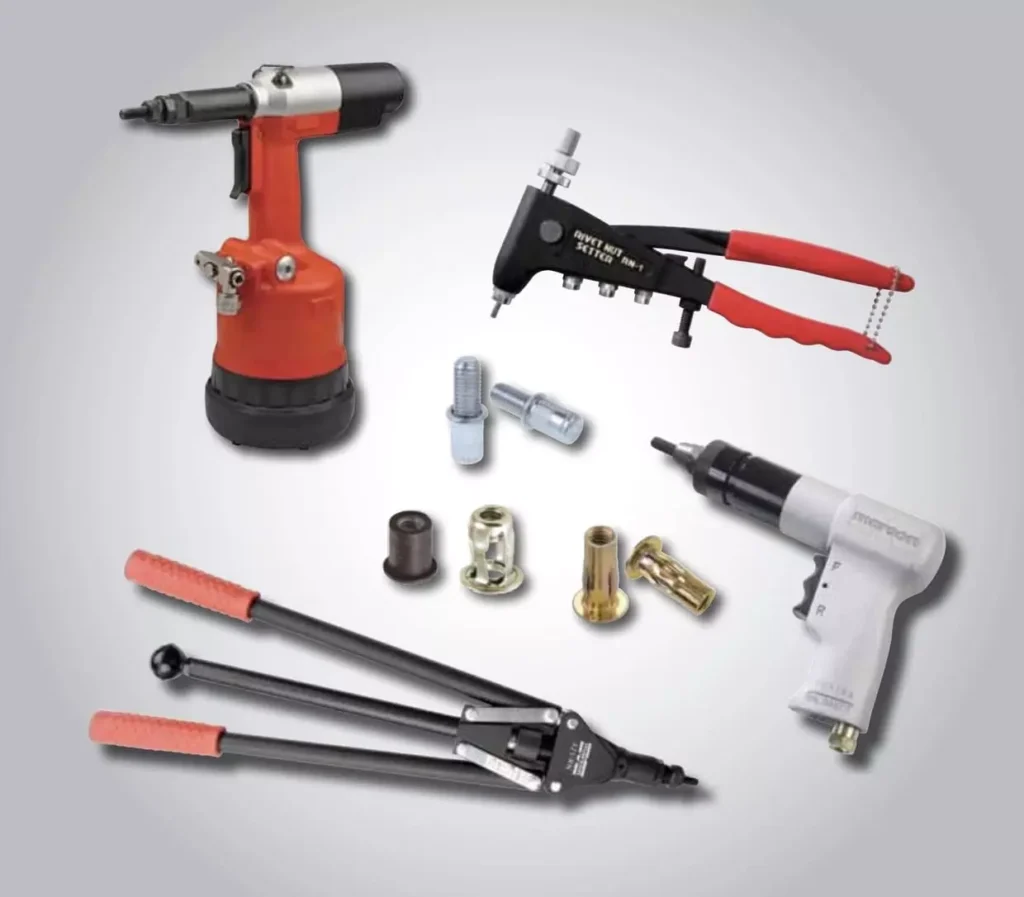
- When to Use: Ideal for small-scale projects, prototypes, or situations with limited space. Manual tools are generally more cost-effective and suitable for low-volume work.
- Considerations: Requires more labor, and can be time-consuming for larger quantities. Consistency of installation force may be harder to control.
- When to Use: Best for medium to high-volume applications. Pneumatic tools provide faster installation, requiring less physical effort while offering better control over the installation force.
- Considerations: Ideal for projects where speed and precision are important but doesn’t require fully automated systems. Pneumatic tools are generally more expensive than manual tools and require a compressed air source.
c. Automated Assembly:
- When to Use: Most suitable for large-scale, high-volume production lines where efficiency, speed, and consistency are critical. Automated assembly systems can handle hundreds or thousands of rivet nuts in a short period.
- Considerations: High initial investment and setup cost. Best for mass production where high volumes are needed with minimal human intervention. Automated systems typically offer the most consistent and reliable results.
8. Will the Rivet Nut Be Exposed to Corrosive Environments?
- Plating or coatings (zinc, nickel, passivation, etc.) may be needed for corrosion resistance.
- Stainless steel is ideal for marine, outdoor, or chemical applications.
9. Do You Need a Closed-End or Open-End Rivet Nut?
- Design: The blind rivet nut has a sealed bottom, which provides a barrier that prevents any material from entering the threaded insert.
- Advantages:
- Sealing Capability: Closed-end rivet nuts offer better sealing properties, preventing the ingress of dust, water, and other contaminants, making them ideal for environments that require moisture or air-tight seals.
- Corrosion Resistance: Ideal for applications where water or chemicals may come into contact with the fastener, as the closed-end helps protect the threads and prevent corrosion.
- Pressure Containment: Useful in applications where the rivet nut needs to withstand internal pressure, like in plumbing or fluid systems.
- Applications: Commonly used in automotive, plumbing, aerospace, and electronics where sealing and preventing contamination are critical.
Open-End Rivet Nuts:
- Design: Open-end rivet nuts have an open bottom, allowing for easy insertion of bolts or screws from either side.
- Advantages:
- Ease of Insertion: Open-end rivet nuts are simpler to install, especially in applications where accessibility from both sides of the material is possible.
- Faster Installation: Open-end rivet nuts can be installed quickly, making them ideal for projects where speed is a factor.
- Versatility: They can be used in situations where sealing isn’t a priority, and a more straightforward threaded connection is needed.
- Applications: Commonly used in electronics, automotive, and light manufacturing, particularly where sealing is not a concern.
10. What Are Your Quantity and Budget Considerations?
Bulk Orders:
Cost Advantage: Ordering rivet nuts in bulk typically reduces the per-unit cost due to economies of scale. Manufacturers often offer discounts for larger orders, making it a more cost-effective option for projects that require a high volume of fasteners.
Custom Designs:
- Initial Cost: Custom rivet nuts may come with a higher upfront cost due to design and manufacturing adjustments. Because they are tailored to specific application needs (e.g., custom dimensions, material, or finishes).
- Long-Term Benefits: Although the initial investment might be higher, custom rivet nuts are often more efficient in meeting your specific performance requirements, potentially saving costs on installation, repairs, or failures. They may also enhance the overall quality and longevity of your project.
Do You Have Any Questions?
Let Us Solve Your Problem
Choose Rivetfix to Buy High Quality Rivet Nuts
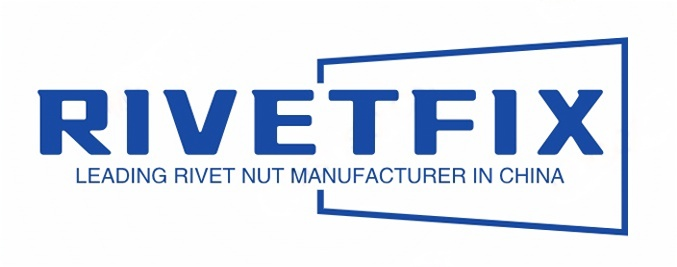
As a leading fastener manufacturer in China with more than 15 years in the industry, Rivetfix are committed to providing first-class quality fasteners and responsive services to the world.
Our commitment to quality, innovation, and customer satisfaction has established Rivetfix as a trusted partner for businesses seeking reliable fasteners. We prioritize the use of premium materials, cutting-edge technology, and rigorous quality control processes to ensure that our jack nuts meet international standards and exceed customer expectations. As a global supplier, Rivetfix offers competitive pricing and fast delivery, making us the ideal choice for your jack nut needs.
Contact us for project advice and the latest rivet nut quote!
Get High Quality Rivet Nuts Quote!
Send Your Rivet Nut Request
For more than 20 years, Rivetfix has helped customers solve many rivet nuts sourcing needs and technical challenges.
Have a question? Contact us and we’ll provide you with the perfect solution.