How to Choose Self Clinching Nuts/PEM Nuts for Stainless Steel?
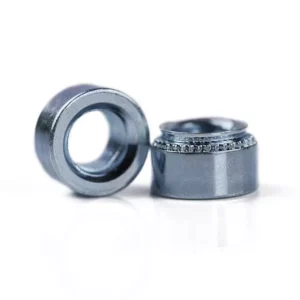
Leading Self-Clinching Fasteners Manufacturer and Supplier in China
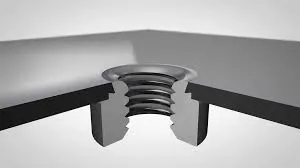
Choosing the right PEM nuts for stainless steel is crucial for ensuring strong, reliable connections in demanding applications. This guide covers essential factors, such as material compatibility, installation challenges, and best practices, helping you select the optimal self-clinching nuts for your stainless steel projects.
Table of Contents
What Do I Need to Know About PEM Nuts?
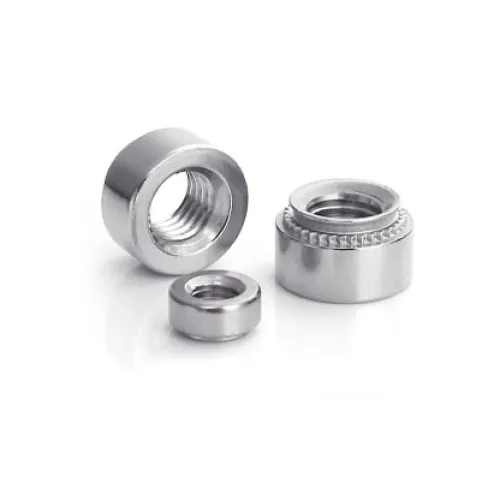
1. Definition
A Self-Clinching Nut is a fastener that permanently embeds into thin metal sheets through mechanical deformation, creating a high-strength internal thread on one side of the sheet without the need for welding, adhesives, or additional nuts.
- Common Names: Brand terms like “PEM® Nut” are specific types of self-clinching nuts; the general term is “Self-Clinching Nut.”
- Core Features:
- Once embedded in the sheet, the nut cannot be removed, ensuring strong thread stability.
- Space-saving, ideal for thin sheet applications (0.5~3mm), preventing protrusions on the back side.
2. Working Principle
A pem nut achieves permanent installation through pressure-driven plastic deformation:
- Pre-punched Hole: A hole matching the outer diameter of the nut is pre-made in the sheet (the hole diameter must be precisely controlled).
- Insertion and Embedding: Using a press tool or hydraulic press, vertical pressure is applied to the nut. The nut’s bottom ring structure (saw teeth or grooves) compresses the sheet, causing the material to flow into the grooves.
- Locking Completed: The material of the sheet interlocks with the nut’s structure, forming a secure threaded interface that resists rotation and can withstand high pull-out forces.
Key Design:
- Saw Teeth/Grooves: The core structure that interlocks with the sheet (non-threaded portion).
- Guide Ring: Ensures proper alignment and vertical pressure during installation.
3. Application Scenarios
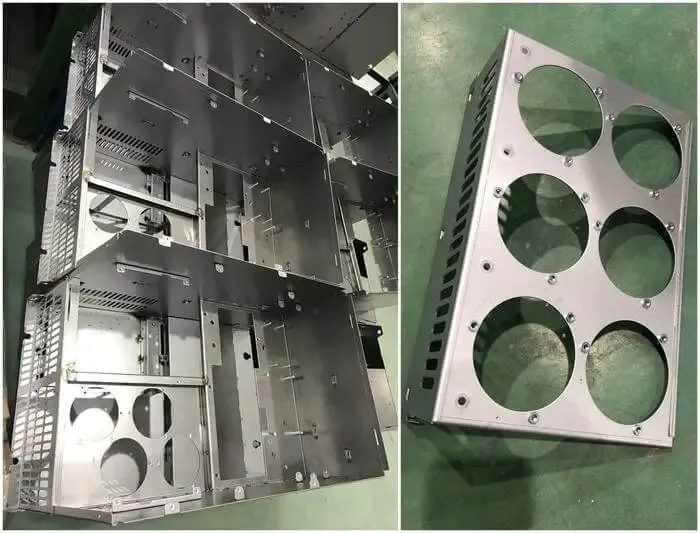
Electronic Product Enclosure Assembly
Common electronic devices like computers, televisions, and audio systems typically have enclosures made from thin metal sheets (e.g., aluminum, steel). Using pem nuts in these metal sheets allows for the rapid creation of stable threaded connection points on the device enclosures, making subsequent fastening and maintenance processes more convenient.
Advantages: By using pem nuts, no additional processing or specialized tools are needed for the enclosure. This helps save assembly time and avoids the heat-affected zone created by welding, reducing the risk of enclosure deformation.
Automotive Manufacturing
Automotive components often use thin metal sheets, and traditional bolt installation methods can result in unstable parts or structural weaknesses. PEM nuts embed securely into the metal sheet, creating strong and reliable threaded connection points.
Advantages: This technology reduces the complexity of welding and bolt installation, helping to lower production costs while providing high-strength connections that avoid the space required by traditional bolts.
Aerospace Equipment
Aerospace equipment has strict requirements for weight and structural strength, and pem nuts can provide high-strength connections while reducing unnecessary weight. Especially in the fixation of aircraft fuselages, engine components, or electronic control systems, they offer a lightweight connection method while ensuring connection reliability.
Advantages: Self-clinching nuts are suitable for thin metal sheet installations and can withstand high stress and vibration environments, making them ideal for the high strength and safety demands of aerospace components.
Home Appliances Industry
In the manufacturing of home appliances like washing machines, refrigerators, microwaves, etc., pem nuts are commonly used in the assembly of metal frames and enclosures. Home appliances often require efficient and long-lasting fastening solutions, and self-clinching nuts not only provide stable threaded connections but also avoid issues such as loosening or corrosion that can arise with traditional fasteners.
Advantages: The use of self-clinching nuts simplifies the manufacturing process of home appliances, reduces production costs, and increases the reliability and durability of the products.
Industrial Automation Equipment
Industrial automation equipment, such as robots, automated production lines, and sensor mounting brackets, requires high-strength connections that are easy to assemble and disassemble. PEM nuts provide strong threaded connection points in the thin metal sheets of these automated devices, ensuring stable and reliable operation over the long term.
Advantages: Self-clinching nuts not only improve assembly efficiency but also reduce the time and costs of equipment maintenance, while enhancing product reliability.
4. Advantages and Limitations of PEM Nuts
Advantages:
- Simplified Assembly Process, Cost Reduction: Self-clinching nuts eliminate the need for additional processes like welding or riveting, reducing both assembly time and overall costs.
- Permanent Thread, Reduces the Risk of Loosening: The nut creates a permanent, strong thread in the sheet metal, which is resistant to loosening, making it especially reliable in high-frequency vibration environments.
Limitations:
- Limited to Thin Sheets: PEM nuts are primarily suitable for thin metal sheets (typically between 0.5–3mm thick). Thicker sheets are difficult to plastically deform, making the self-clinching process impractical.
- Requires Specialized Tools for Installation: The installation process requires a press machine or specialized molds, leading to higher initial equipment investment. This can increase the upfront cost for small-scale or non-automated production setups.
Key Features & Challenges of Stainless Steel
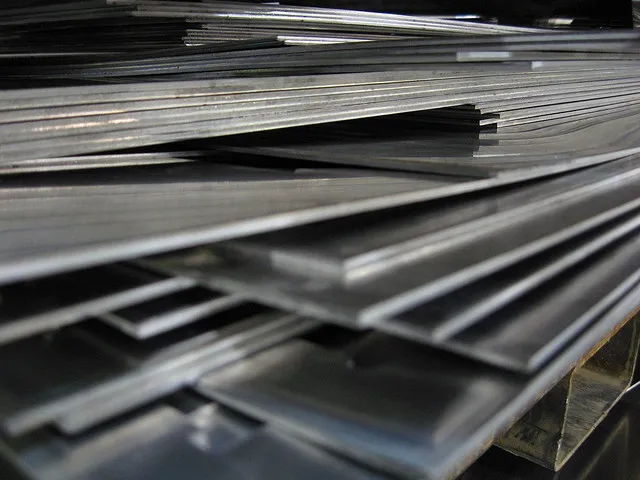
1. Material Features
a. High Hardness
- Specific Performance: The typical hardness of austenitic stainless steels (such as 304/316) is HRB 70-90, much higher than that of standard carbon steel (HRB 50-60).
- Impact on Installation:
- Pressure Requirements: Higher clamping forces are needed due to the material’s increased hardness. For example, an M4 nut may require 3-5 tons of pressure to be installed in 304 stainless steel, compared to only 1-3 tons in carbon steel.
- Mold Wear: The higher hardness accelerates mold wear, which makes it advisable to use tungsten carbide molds instead of regular steel molds to ensure longevity and performance.
b. Tendency for Work Hardening
- Definition: Stainless steel undergoes work hardening (increased hardness) during cold deformation processes such as drilling or stamping. This can make subsequent machining or installation more difficult.
- Risks: During punching, the edges of holes can harden, affecting the material’s ability to deform during the nut insertion process, potentially leading to cracking or poor installation.
- Solutions:
- Step-by-step Processing: Perform punching followed by annealing (locally heating the material to 700-800°C to relieve work hardening), and then install the nut.
- Low-speed Punching: Reducing punching speed can help minimize the thickness of the work-hardened layer.
c. Corrosion Resistance (304 vs 316)
Material Type | Main Elements | Corrosion Resistance Scenario |
304 Stainless Steel | 18% Cr, 8% Ni | General acidic or alkaline environments (e.g., ordinary humid air, weak acidic media) |
316 Stainless Steel | 16% Cr, 10% Ni, 2% Mo | High chloride environments (e.g., marine atmosphere, chemical equipment, medical sterilizing agents) |
Selection Criteria: Based on salt spray testing (ASTM B117), 316 typically exhibits 3 times higher corrosion resistance than 304. For example, 304 can resist salt spray for around 500 hours, while 316 can endure for about 1500 hours under the same conditions.
2. Selection Challenges in Stainless Steel Applications
a. High Hardness Leading to Installation Difficulty
- Problem Manifestation:
- Sheet Cracking: Excessive clamping pressure can cause the sheet to crack.
- Incomplete Nut Insertion: Insufficient pressure may result in the nut not fully embedding into the sheet.
- Optimization Strategies:
- Reduce Material Hardness: Choose “soft” (annealed) stainless steel, such as ASTM A666 304-1/4H (with a hardness of HRB ≤ 90).
- Adjust Mold Design: Increase the guide angle (e.g., 30°) to distribute the clamping force more evenly and reduce edge stress concentration.
- Process Monitoring: Use pressure sensors for real-time feedback of clamping pressure, aiming to control the target tolerance within ±10%.
b. Galvanic Corrosion Risk
- Mechanism: When stainless steel comes into contact with dissimilar metals (e.g., aluminum, carbon steel), a potential difference is created in an electrolyte (e.g., humid air), accelerating the corrosion of the anode metal.
- Typical Case:
- Aluminum Nut (Anode) + 304 Stainless Steel Plate (Cathode) → Rapid corrosion of aluminum, leading to failure within 2-3 years.
- Protective Measures:
- Material Matching: Prefer using nuts made from the same material as the sheet metal (e.g., 304 nuts for 304 stainless steel plates).
- Insulated Isolation: When matching materials is not possible, use nylon washers or polyurethane coatings to block the current path and prevent galvanic corrosion.
- Sacrificial Anode Design: Add zinc alloy blocks in corrosion-sensitive areas to corrode first and protect the main structure.
Do You Have Any Questions?
Let Us Solve Your Problem
How to Choose PEM Nuts/Self-Clinching Nuts for Stainless Steel?
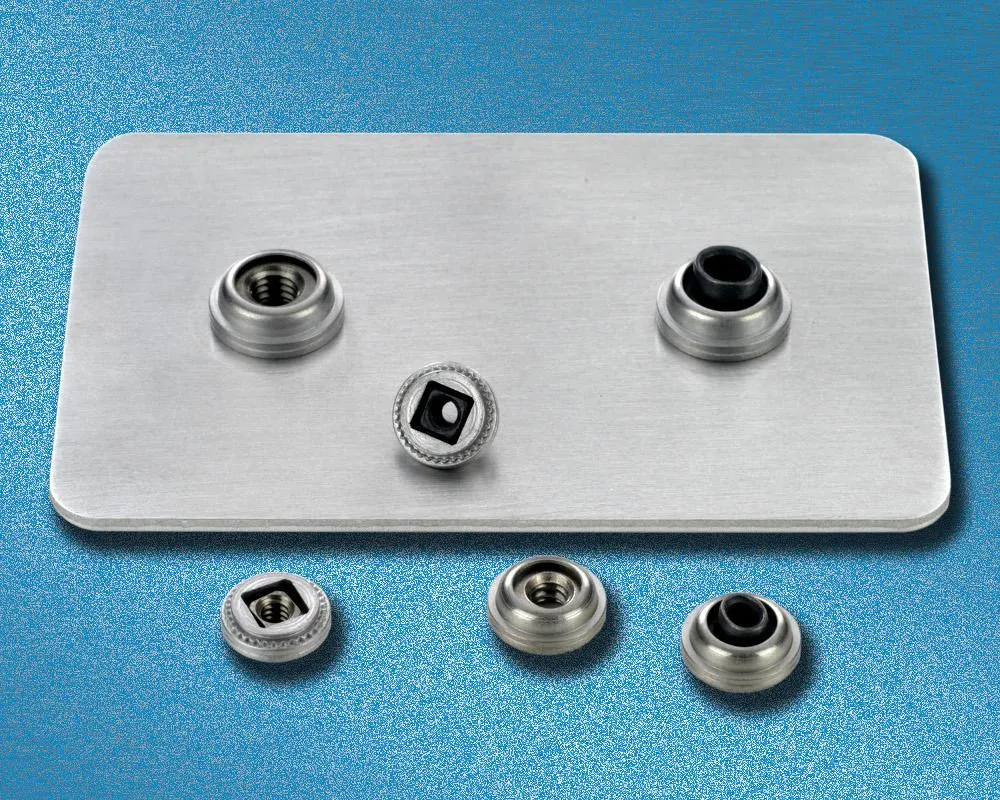
Core Considerations in Selecting PEM Nuts for Stainless Steel
1. Material Compatibility
- Preferred Combination: For stainless steel sheets, choose nuts made of the same material (e.g., 304/316 stainless steel).
- 304 Stainless Steel (18-8): Suitable for general environments (humid air, weak acidic/alkaline media).
- 316 Stainless Steel (contains 2% molybdenum): Resistant to chloride corrosion (marine environments, chemical industries, medical sterilization).
- Dissimilar Metal Combinations (Handle with Care):
- Aluminum Nuts: High risk of galvanic corrosion (self-clinching nuts are not recommended).
- Carbon Steel Nuts: Must be electroplated (zinc or dacromet) or have an isolating coating.
Combination Example | Application Scenario | Risk Description |
316 Nut + 316 Stainless Steel Plate | Seawater immersion equipment, chemical plant reactors | Optimal corrosion resistance combination |
304 Nut + 304 Stainless Steel Plate | Indoor enclosures, food processing equipment | Cost-effective, avoids dissimilar metal contact |
Zinc-Plated Carbon Steel Nut + 304 Plate | Temporary structures (scaffolding, non-load-bearing brackets) | Requires regular inspection of coating integrity |
2. Plate Material Parameters Adaptation
- Thickness Selection: Commonly used thickness for self-clinching nuts is 0.8-3mm. For thicknesses exceeding 3mm, you may need to customize the driving pressure or nut structure.
- Over-thick Plates (>3mm): Verify the mold’s maximum pressure capacity (may require customized enhanced molds).
- Material State: Prefer annealed (soft) stainless steel (e.g., 304-2B). Avoid cold-worked hardened stainless steel (e.g., 304-Hard), which is more prone to cracking.
3. Load and Environmental Requirements
- Load Type:
- Static Load (e.g., enclosures, casings): Standard self-clinching nuts are sufficient.
- Dynamic Load (e.g., vibrating environments): Choose floating nuts (allowing for ±0.5mm displacement).
- Temperature Range:
- 50°C to 200°C: Regular stainless steel (304/316) is suitable.
- >300°C: Special high-temperature alloys (e.g., Inconel 625) are required for extreme conditions.
Common Selection Errors and How to Avoid Them
1: Ignoring Environmental Corrosiveness
- Case Example: Using 304 stainless steel nuts on coastal outdoor equipment, which leads to rust and jamming of threads after 3 months.
- Solution:
- Use 316 stainless steel with passivation for salt spray environments.
- For mixed-metal assemblies, add insulating washers (nylon or rubber) to prevent galvanic corrosion.
2: Using Excessively Hard Plate Material
- Case Example: Cracking of cold-rolled hardened stainless steel (HRB 95) during clamping.
- Solution:
- Prioritize annealed materials (HRB ≤ 90).
- Step-by-step Processing: First punch the holes, then anneal, and finally clamp the nuts.
3: Exceeding Dimensional Tolerances
- Case Example: Pre-punched hole diameter being too small (by 0.1mm), leading to nut loosening.
- Solution:
- Strict Hole Tolerances: Ensure tolerance is ±0.05mm (e.g., for M4 nuts, hole diameter should be Φ4.3±0.05mm).
- Use precise CNC punching or laser cutting to ensure accurate hole sizes.
Considerations for Using PEM Nuts on Stainless Steel
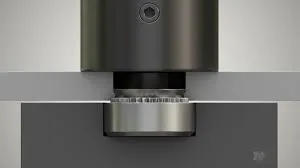
1. Necessary Tools
Clinch Tooling:
- Preferred Material: Tungsten carbide or powder metallurgy tooling, hardness ≥ HRC 70, to handle the high hardness of stainless steel.
- Recommended Models:
- PEM® KH Series Tools (designed for stainless steel).
- Böllhoff HC-Max Tools.
- Tool Design Details:
- Taper Angle: 30°-45°, to distribute clamping forces evenly (sharp 90° angles may cause edge cracking).
- Alignment Mechanism: Tools with built-in locating pins or laser-guided systems (precision ±0.02mm).
Pressure Equipment:
- Minimum Pressure Requirements: When selecting PEM Nuts for stainless steel, note that stainless steel requires at least 5 tons of pressure for M5 and above (e.g., 10 tons for M5 nuts).
- Recommended Equipment:
- Servo-electric presses (e.g., Yamaha YH Series), with ±1% accuracy.
- CNC-controlled hydraulic presses (e.g., Schuler Hydrap 5000), with pressure feedback capabilities.
- Prohibited Tools:
- Hammering Tools (instant impact can cause cracking at the hole edges).
- Handheld Pneumatic Punching Tools (pressure instability can lead to poor performance).
2. Pressure Calibration
Stainless Steel Condition | Typical Hardness (HRB) | M5 Nut Pressure (tons) | M3 Nut Pressure (tons) |
Annealed (Soft) | 70-80 | 3.0-3.5 | 1.2-1.5 |
Half-Hard | 80-90 | 3.5-4.5 | 1.5-2.0 |
Fully Hard | >90 | Not Applicable (Requires Annealing) | Not Applicable (Requires Annealing) |
3. Inspection Methods
a. Visual Inspection
- Acceptance Criteria:
- Front Side: Nut edges should be flush with the plate surface (height difference ≤0.1mm) with no visible cracks.
- Back Side: Plate bulging should not exceed 1.2 times the nut diameter, with a bulging height of 0.1-0.3mm.
- Inspection Tools:
- 10x Magnifying Glass (for micro crack detection).
- Surface Profilometer (e.g., Mitutoyo Surftest SJ-410, to measure bulging height).
b. Torque Testing
- Testing Procedure:
- Use a torque wrench (e.g., Norbar 3003E) to pre-tighten to 80% of the nominal torque (e.g., for M5 nuts with a nominal torque of 5Nm, pre-tighten to 4Nm).
- After holding for 30 seconds, loosen and check if the thread has stripped or the nut is loose.
- Minimum Destructive Torque Reference:
Thread Size | Stainless Steel to Stainless Steel | Stainless Steel to Zinc-Plated Carbon Steel |
M3 | 1.5 Nm | 1.0 Nm |
M5 | 6.0 Nm | 4.0 Nm |
M8 | 18 Nm | 12 Nm |
4. High-Frequency Failure Cases and Countermeasures
Failure Phenomenon | Root Cause | Solution |
Nut thread stripping after insertion | Plate hardness too high, preventing full nut fill | Anneal the plate or use high-pressure tooling |
Plate edge tearing | Tooling guide angle too small (<20°) | Use tooling with a guide angle ≥30° |
Nut loosening after installation | Pre-punched hole diameter exceeding tolerance (+0.1mm) | Use laser cutting for hole control (tolerance ±0.03mm) |
Corrosion leading to thread failure | Dissimilar metal contact (e.g., aluminum nuts) | Replace with same-material nuts and apply insulation coating |
Do You Have Any Questions?
Let Us Solve Your Problem
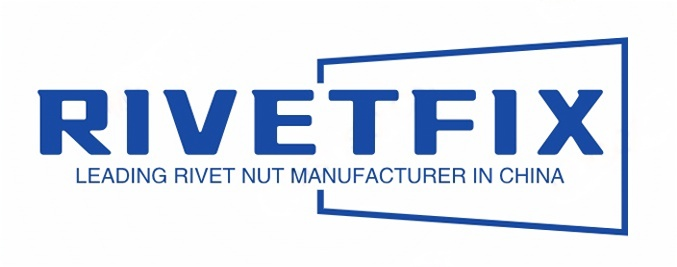
With 15+ years of experience in fastener manufacturing, Rivetfix has grown into a trusted global supplier. Today, we have a dedicated team of 200+ skilled production workers and 40+ professional sales representatives, ensuring seamless service and reliable supply.
Our vision is simple yet powerful: to provide the highest-quality fasteners at competitive prices to customers worldwide. In doing so, we combine precision manufacturing, efficient operations, and exceptional customer support. As a result, we are committed to helping businesses build stronger, more cost-effective solutions. Through this approach, we aim to consistently exceed customer expectations and foster long-term partnerships.
Partnering with Rivetfix means stable supply, top-quality fasteners, and custom solutions. We help you cut costs, boost efficiency, and enhance durability. Expect on-time delivery, expert support, and innovation. Buy PEM fasteners now!
Get High Quality Rivet Nuts Quote!
Send Your Rivet Nut Request
For more than 20 years, Rivetfix has helped customers solve many rivet nuts sourcing needs and technical challenges.
Have a question? Contact us and we’ll provide you with the perfect solution.