How to Choose PEM Nuts/Self Clinching Nuts for Plastic?
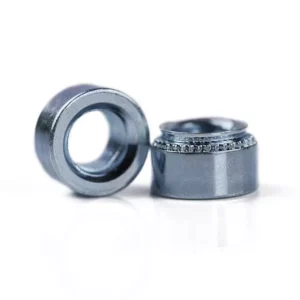
Leading Self-Clinching Fasteners Manufacturer and Supplier in China
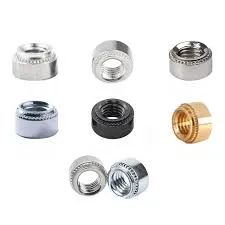
When selecting PEM nuts for plastic materials, it’s essential to consider factors such as material compatibility, size specifications, and installation methods. Understanding these key elements ensures a secure, durable connection without damaging the plastic, making it crucial to choose the right PEM nut for your specific application.
Table of Contents
What are PEM Nuts/Self-Clinching Nuts?
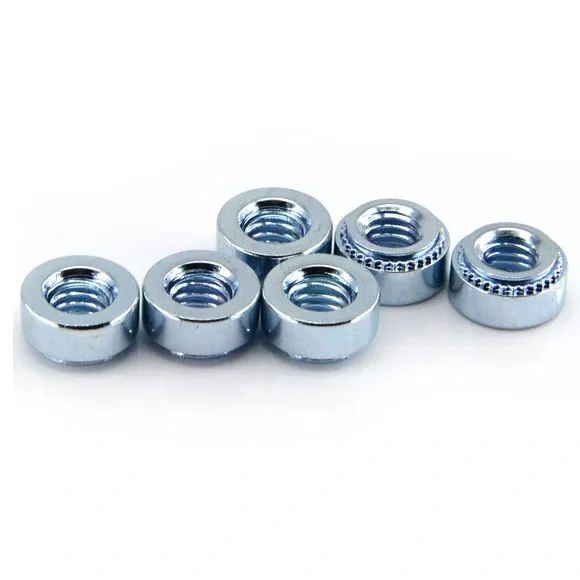
PEM nuts (self-clinching nuts) are fasteners with a self-locking function, typically used for connecting thin sheets or lightweight materials. The principle of operation involves mechanically pressing the nut into the material, creating a permanent fixation through plastic deformation or a studded structure (such as teeth or protrusions). This allows the nut to be securely fixed to the material without the need for welding, thread cutting, or glue.
PEM nuts are widely used in industries such as electronics, automotive, and aerospace. They are particularly suitable for applications that require fast, reliable, and cost-effective fastening methods.
Basic Principle:
- Pressure Insertion: The nut is pressed into the material using specialized tools during installation.
- Plastic Deformation/Studded Structure: A secure fix is achieved through the plastic deformation of the material or the nut’s studded structure.
- No Welding or Glue: This design avoids the complexity of traditional joining methods such as welding and glue use.
Why Do Plastics Need Self-Clinching Nuts?
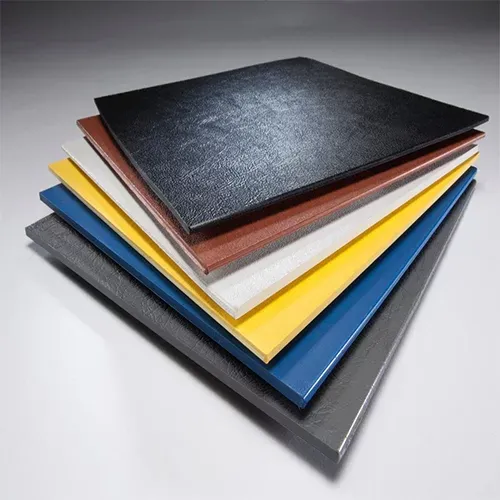
The low strength, tendency to deform, and heat sensitivity of plastics require special designs when using traditional fasteners. Specialized self-clinching nuts solve these issues with innovative designs and installation methods, providing stronger and more stable connections for plastic parts.
1. Low Strength and Susceptibility to Deformation
Plastics generally have lower strength than metals, especially thin-walled plastic parts. In traditional bolt and nut connections, plastics may not be able to withstand the pressure exerted by conventional fasteners, leading to material cracking or deformation.
Specialized self-clinching nuts feature designs such as studded or pressure-insertion methods that ensure a firm attachment to plastic materials, avoiding damage to the plastic structure.
2. Heat Sensitivity
Plastics are more sensitive to temperature changes, and thermal expansion and contraction can lead to the failure of traditional bolt connections or stress concentration.
Conventional nuts may loosen or fail to maintain a secure fit in high-temperature environments. However, PEM self-clinching nuts are designed with consideration for thermal expansion and contraction, ensuring a stable connection even under temperature fluctuations.
3. Avoiding Direct Thread Cutting
Cutting threads in plastic parts, especially brittle materials, can lead to cracking or material damage. Traditional bolts require threading in plastics, which can compromise the structural integrity of the plastic. Self-clinching nuts install by being pressed in, avoiding the need for direct thread cutting, preventing damage to the plastic material while providing a reliable connection.
4. Preventing Over-Pressing and Deformation
Plastics are prone to permanent deformation under pressure, especially at connection points. Using traditional nuts may result in plastic material deformation due to excessive pressure.
The design of specialized self-clinching nuts controls the pressure distribution, allowing the nut to be smoothly pressed into the plastic, preventing excessive local stress and avoiding deformation of the plastic.
5. Improving Connection Strength
Plastic materials generally have a lower surface friction, which can cause traditional nuts and bolts to slip or loosen. Self-clinching nuts, with their studded or toothed structures, create a stronger mechanical grip with the plastic surface, ensuring a stable connection and preventing loosening during use.
The Impact of Plastic Properties on Nut Selection
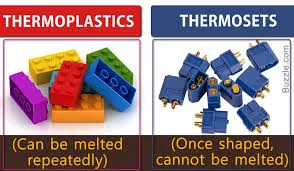
- Thermoplastic materials (such as ABS, polycarbonate (PC)) have good plasticity and can soften when heated, making them suitable for heat-insertion or self-clinching nut installation. The reflow temperature of these materials must be considered, as thermoplastics may soften at high temperatures, which could affect the fixation of the nut. Therefore, when selecting a nut, it is important to ensure it can withstand the material’s melting temperature.
- Thermosetting plastics (such as epoxy resins) cannot be re-molded once they have cured, which makes the requirements for nuts more stringent. When installing self-clinching nuts in thermoset plastics, special attention should be paid to preventing cracking due to stress concentration during installation, which could damage the material.
2. Strength and Toughness
- Glass-fiber reinforced plastics (such as glass-filled nylon) are stronger and harder but also more brittle. When using these materials, a self-clinching nut with higher grip strength is required to ensure that the nut securely holds without loosening. Additionally, glass-fiber reinforced plastics are prone to damage during installation, so the nut’s design should distribute pressure effectively to avoid material damage.
- For low-strength and flexible plastics, such as standard ABS or PVC, the nut selection should accommodate the lower mechanical strength and load-bearing capacity. Typically, a standard self-clinching nut will suffice in these applications.
3. Thickness and Hardness
- Thin-walled plastics (e.g., 1-2 mm thick sheets) often require shallow-insertion design self-clinching nuts to ensure that the nut does not penetrate or damage the surface of the material during insertion. The depth of nut insertion should be precisely designed to avoid excessive pressure, which could cause plastic material cracking.
- Hard plastics (such as PEEK, polyamide) with higher hardness and strength may require pre-drilling before installation, particularly when using standard self-clinching nuts. Pre-drilling ensures the nut can be smoothly inserted and achieve the desired secure fit. It also prevents excessive friction between the nut and the hard plastic, reducing the risk of material damage.
4. Coefficient of Thermal Expansion
Thermal Expansion Differences: The difference in thermal expansion coefficients between plastic and metals (e.g., stainless steel) can cause stress accumulation at the connection points when the temperature changes. For example, high-temperature plastics (like PEEK, PPS) often pair with metals (like stainless steel, aluminum alloys), but their thermal expansion properties must be considered. If the difference in thermal expansion coefficients is too large, it could lead to loosening or cracking of the fastener.
Do You Have Any Questions?
Let Us Solve Your Problem
How to Choose PEM Nuts/Self-Clinching Nuts for Plastic?
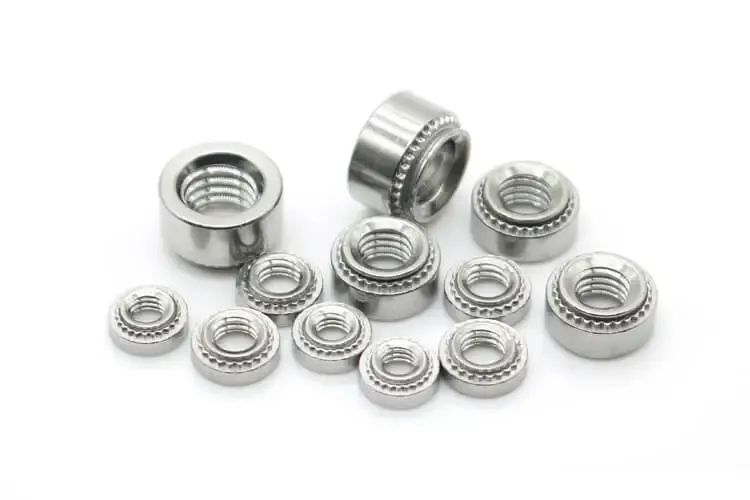
1. Material Compatibility
Nut Material:
- Stainless Steel (e.g., 304, 316): Known for strong corrosion resistance, ideal for outdoor, chemical contact, or marine environments. 316 stainless steel is particularly suitable for high salt or moisture conditions due to its superior resistance to oxidation. However, its cost is higher.
- Aluminum (e.g., 6061-T6, 7075-T6): Aluminum nuts are suitable for applications where weight reduction is a priority, especially in the aerospace and automotive industries. They are lightweight, but not as strong as stainless steel. Aluminum nuts offer good heat dissipation and a lower risk of corrosion.
- Carbon Steel (e.g., galvanized, nickel-plated): Carbon steel nuts are more cost-effective than stainless steel and aluminum, suitable for medium-strength applications in regular environments. Galvanizing or nickel plating provides additional corrosion protection, making them suitable for indoor or low-corrosion environments.
Surface Treatment:
- Galvanizing: Provides basic rust protection through a zinc coating, typically used on carbon steel nuts for general environments.
- Passivation: Used on aluminum nuts to form a thin oxide film, offering mild corrosion resistance.
- Anodizing: Ideal for aluminum alloy nuts, it not only enhances corrosion resistance but also increases surface hardness, widely used in automotive, electronics, and outdoor equipment.
- Anti-corrosion Coatings: Some special applications may require higher corrosion resistance, such as using PTFE (polytetrafluoroethylene) or epoxy coatings to prevent erosion from certain plastics or chemicals.
2. Size and Load Capacity
Thread Specifications:
- Common thread sizes include M3, M4, M5, M6, etc. Choosing the right thread size is key to ensuring that the PEM nut matches the hole diameter of the material. Too tight of a thread can put pressure on the material, leading to cracking or detachment, while too loose a thread may result in an unstable connection.
- When selecting the thread size, consider the actual load requirements. For example, larger thread sizes (e.g., M6 or M8) are suitable for applications subject to greater pulling forces, while smaller sizes (e.g., M3 or M4) are appropriate for light-load scenarios.
Installation Height:
- Installation height refers to how far the PEM nut protrudes or is recessed from the surface of the material. The nut height should ensure it is fully embedded within the material, avoiding excessive protrusion that could affect appearance or installation space.
- For thin sheet materials (such as 1-2mm aluminum), excessive height could result in poor contact or unnecessary impact loads. Choosing the correct nut model is crucial.
Pullout Strength and Torque Resistance:
- Pullout Strength refers to the nut’s resistance to detachment under tension, usually measured in Newtons (N). Different PEM nut models have varying pullout strengths, such as an M4 nut with a pullout strength of up to 500N and an M6 nut with a pullout strength of 1500N.
- Torque Resistance refers to the nut’s ability to withstand rotational torque, impacting its ability to prevent loosening during bolt tightening. The right pullout strength and torque resistance should be chosen based on actual load and operational conditions.
3. Installation and Processing Requirements
Hole Size and Tolerance Control:
- Selecting the correct installation hole size is essential. PEM nuts need to be installed in accurately sized holes to ensure proper embedding and mechanical locking. Typically, hole tolerances should be controlled to H11 grade (e.g., Φ4.3±0.05mm).
- It is recommended to use high-precision drills (e.g., carbide drills) and CNC machinery to ensure hole size accuracy. Oversized or poorly positioned holes may prevent the nut from being securely embedded, compromising the connection strength.
Material Thickness:
PEM nuts are suitable for various material thicknesses, but different thicknesses influence nut selection. For aluminum sheets thicker than 6mm, it is recommended to use clinch nuts or weld nuts, while thinner aluminum sheets (e.g., 0.5mm to 3mm) require specific thin-sheet PEM nuts (e.g., PEM® FH series).
4. Environmental and Special Requirements
Environmental Adaptability:
- Material corrosion resistance is crucial in different environments. For example, PEM nuts can be selected based on the application environment by choosing the appropriate material and surface treatment. For marine or chemical exposure applications, 316 stainless steel or titanium alloys should be chosen to reduce the risk of galvanic corrosion.
- For high-temperature or extreme environments, high-temperature alloys such as Inconel or anodized aluminum should be chosen. Zinc-coated steel nuts should not be used in environments exceeding 150°C, as the zinc coating may melt.
Special Function Requirements:
- In some precision equipment (e.g., medical or electronics devices), sterile or anti-static PEM nuts may be required. In these cases, surface electropolishing or coating treatments should be chosen to meet these specific technical demands.
- If the application requires the nut to withstand higher vibration or shock, PEM nuts with special designs (e.g., anti-loosening type) should be selected, or additional thread adhesive may be used to enhance the fixation strength.
How to Install PEM Nuts on Plastic?
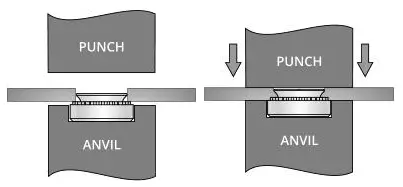
Tool Requirements
- Hydraulic Press: Suitable for large-scale production, capable of accurately controlling pressure and positioning.
- Ultrasonic Welding Machine: Suitable for high-precision plastic materials, providing finer control through sound wave vibrations.
- Manual Tools: Such as KJ Tools hand presses, suitable for small-scale production or on-site maintenance, allowing for quick nut installation.
Installation Steps Example
1. Positioning:
- Use measuring tools to mark the exact location and ensure that the hole and nut are aligned. Check the back of the aluminum or plastic sheet to ensure there is no cracking or damage during the pressing process.
- Ensure that the nut is aligned perpendicular to the material during installation, using positioning clamps or guiding sleeves to assist with fixation.
2. Pressure Control:
- Set the pressure on the hydraulic press or other pressing tools according to the manufacturer’s recommended pressure range (e.g., 500-1500 psi). Excessive pressure can cause deformation or cracking of the plastic, so it is crucial to avoid applying too much pressure.
- Check the nut depth during the pressing process to ensure it is fully embedded into the material’s surface.
3. Temperature Control:
- or certain types of plastic materials (such as nylon or polyamide), preheating may help reduce stress concentration and prevent cracking. Typically, preheating to 50-80°C can improve the plastic’s formability.
- If using temperature control equipment, ensure that the temperature is evenly distributed to avoid overheating or cooling that could make the plastic brittle.
PEM Nut Installation Pressure Parameter Table
Parameter Category | Control Points | Typical Values/Range | Explanation |
Plate Thickness Range | Applicable Plate Thickness | Plastic: 1.0-4.0 mmMetal: 0.8-3.0 mm | Plastic requires a larger contact area, and insufficient thickness may lead to plastic collapse. |
Installation Hole Diameter | Hole Tolerance | Plastic: D+0.05~0.10 mmMetal: D±0.03 mm | Oversized holes reduce gripping force, and undersized holes increase pressing force (plastic requires stricter tolerance control). |
Pressing Force (Pressure) | Vertical Pressing Pressure (Static Pressure) | Plastic: 200-800 NMetal: 500-3000 N | The force should be adjusted based on substrate hardness (e.g., 300 N for ABS, 600 N for PA66+GF). |
Pressing Rate | Pressing Speed Control | 1.0-5.0 mm/s | Fast pressing speeds may cause cracks in plastic (stepwise pressurization is required). |
Temperature Control | Preheating Temperature (if needed) | Plastic: 80-120°C (near Tg)Metal: Room temperature or localized heating | Thermal installation can reduce pressing force (e.g., heating nylon above Tg reduces force by 30%-50%). |
Common Installation Errors
Fault Phenomenon | Possible Causes | Solutions |
Nut Rebounding or Falling Out | Insufficient pressing force / Hole diameter too large | Increase pressure by 10% or reduce hole diameter by 0.03 mm |
Material Cracking | Pressing speed too fast / Overloaded pressure | Reduce speed to 2 mm/s, increase preheating |
Thread Stripping | Material creep / No holding pressure | Use nuts with serrated designs + extend hold time to 1.5 s |
Do You Have Any Questions?
Let Us Solve Your Problem
How to Choose a PEM Nuts Supplier?
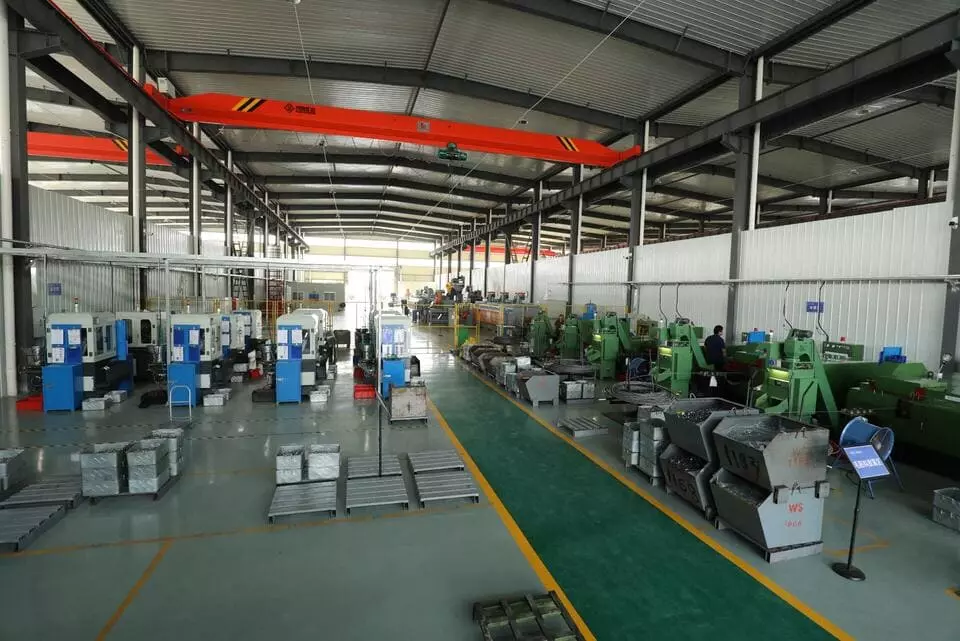
Certification Standards
- ISO 9001 Certification: Choose suppliers that comply with the ISO 9001 quality management system standard, as this indicates that they maintain high standards and consistency in product design, production, and quality control.
- RoHS Certification: For industries with high environmental requirements, ensure that the supplier provides products that meet RoHS (Restriction of Hazardous Substances) standards to avoid the use of materials containing harmful substances, in compliance with international environmental regulations.
Customization Services
- Special Sizes: If your project requires specific dimensions (e.g., non-standard threads, specific insertion depths, or fastening force requirements), it is crucial to find suppliers that offer customization services.
- Coating Requirements: Based on the environmental conditions of the specific application (e.g., corrosion resistance, high-temperature resistance), inquire whether the supplier provides customized coating options (e.g., nickel plating, zinc plating, stainless steel, etc.) to ensure durability under specific operating conditions.
Testing Support
- Sample Verification: Choose suppliers who can provide sample installation verification services. This allows for verifying the compatibility, durability, and installation quality of the products before making a large-scale purchase, reducing project risks.
- Quality Assurance: Understand whether the supplier provides detailed test reports, tensile testing, or reliability testing data to ensure the products meet the required load and application standards.
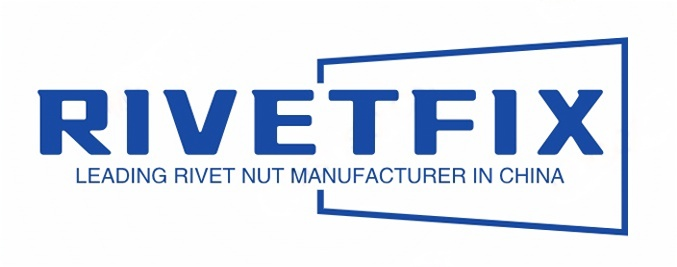
With over 15 years of expertise in fastener manufacturing, Rivetfix has become a trusted global supplier. Our team of 200+ skilled workers and 40+ sales professionals ensures reliable service and consistent supply.
Partnering with Rivetfix means access to top-quality fasteners, cost-saving solutions, and custom designs. We focus on boosting your efficiency, enhancing product durability, and providing on-time delivery. Count on our expert support and continuous innovation for your fastening needs. Choose Rivetfix for premium PEM fasteners and more!
Get High Quality Rivet Nuts Quote!
Send Your Rivet Nut Request
For more than 20 years, Rivetfix has helped customers solve many rivet nuts sourcing needs and technical challenges.
Have a question? Contact us and we’ll provide you with the perfect solution.