Can I Use Steel Rivet Nuts on Aluminum?
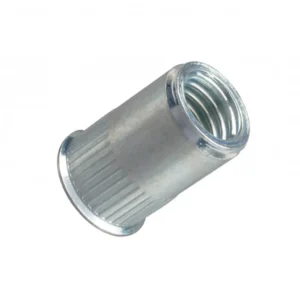
Leading Rivet Nut Manufacturer and Supplier in China
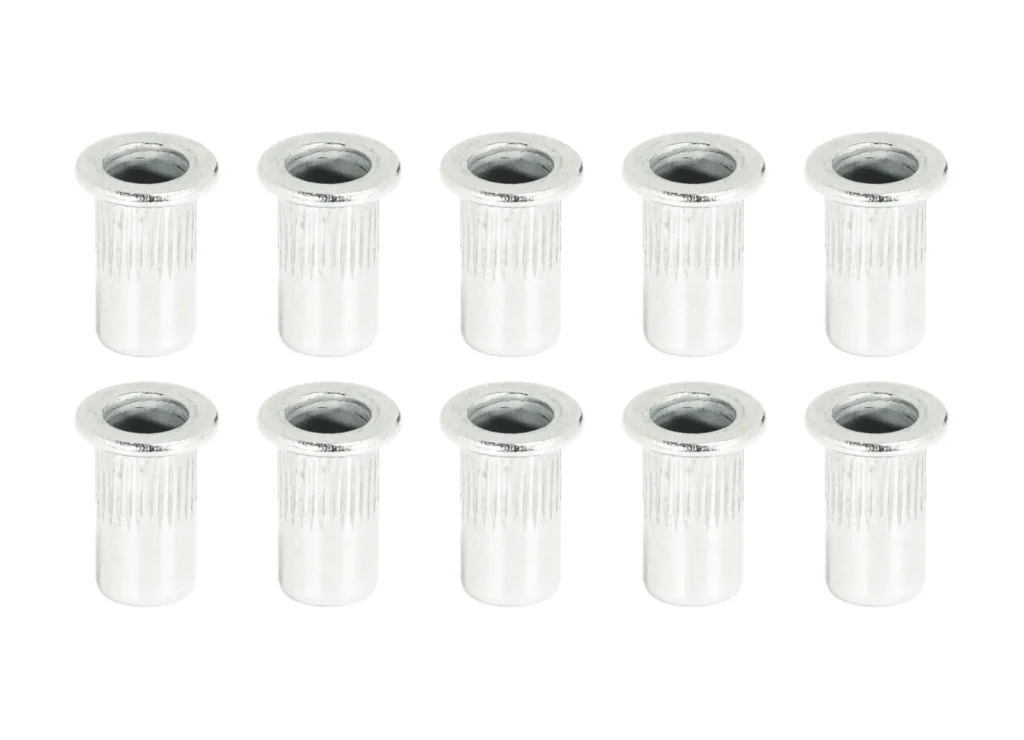
If you’re working with aluminum components and wondering “can I use steel rivet nuts on aluminum?“. This is a common question among engineers and fabricators dealing with mixed-material assemblies. While steel rivet nuts offer superior strength and load-bearing capacity, their use on aluminum requires careful consideration of material compatibility, potential for galvanic corrosion, and proper installation methods. In this guide, we’ll explore when it’s appropriate to use steel rivet nuts on aluminum, what risks to watch out for, and how to ensure a safe, long-lasting connection.
Table of Contents
Why Consider Using Steel Rivet Nuts on Aluminum?
In modern manufacturing, aluminum is widely used across various industries due to its lightweight, high strength-to-weight ratio, excellent corrosion resistance, and ease of machining. Typical applications include:
Sheet metal components: such as electrical enclosures and precision equipment housings;
Aluminum profile structures: such as automation equipment frames, heat dissipation structures, and display racks;
Transportation industry: including aerospace, rail transit, and automotive manufacturing, where weight reduction is a critical requirement.
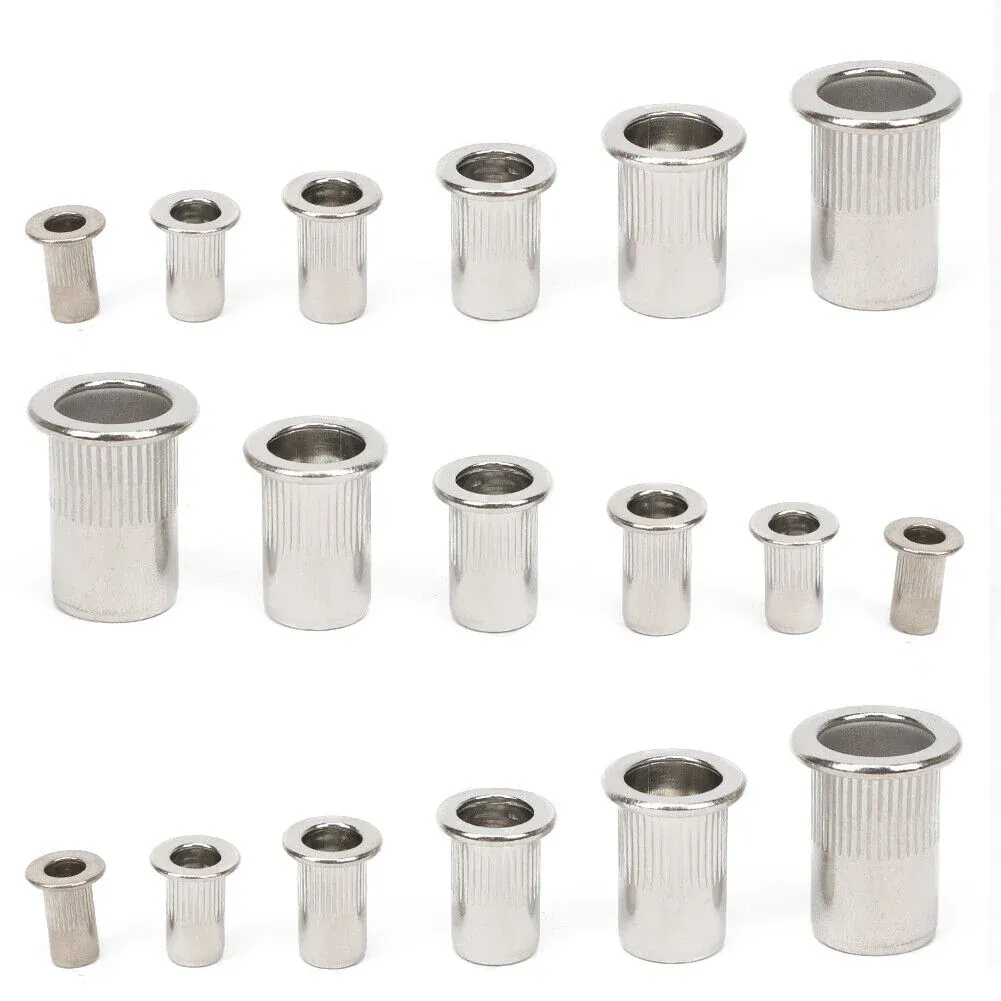
Can I Use Steel Rivet Nuts on Aluminum?
Can I Use Steel Rivet Nuts on Aluminum?While this may seem like a straightforward question, it actually involves multiple factors such as mechanical property compatibility, electrochemical potential differences, joint stability, and long-term durability.
Steel rivet nuts offer high strength and cost-efficiency, with excellent performance in terms of shear and pull-out resistance. However, aluminum is relatively soft, and improper selection or installation of steel rivet nuts may lead to localized indentation, loosening of the joint, or even material damage.
Therefore, before deciding to use steel rivet nuts on aluminum, it is essential to understand the material differences between steel and aluminum, as well as the potential risks of mechanical mismatch and galvanic corrosion. This understanding will enable engineers and designers to make more informed choices, ensuring structural safety, durability, and long-term reliability in actual applications.
What Are the Material Differences Between Steel Rivet Nuts and Aluminum?
1. Advantages of Steel Rivet Nuts
Steel rivet nuts are made from high-strength alloy steel and offer outstanding mechanical properties ( How Strong Are Steel Rivet Nuts? ), including:
- High Strength: Steel has significantly higher yield and tensile strength than aluminum, allowing steel rivet nuts to withstand greater loads and impact forces.
Heavy Load Resistance: In fastening applications, steel rivet nuts provide superior resistance to shear and tensile forces, ensuring connection stability and long-term durability.
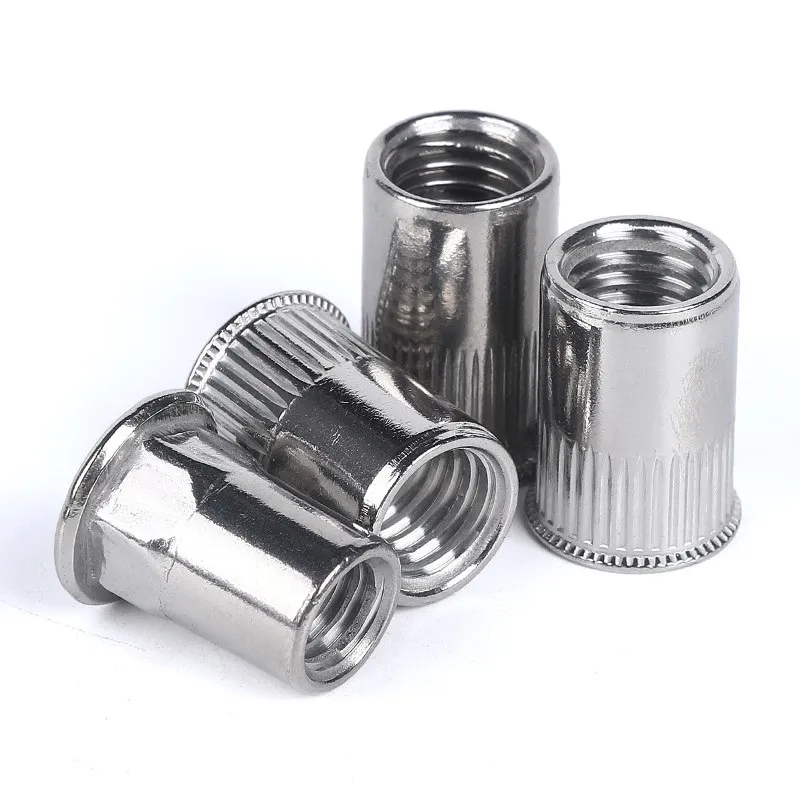
- Excellent Shear and Tensile Performance: With consistent mechanical performance, steel rivet nuts are ideal for load-bearing or structurally demanding applications, such as in automotive, heavy machinery, and aerospace industries.
Superior Wear Resistance: Steel has a harder surface and better wear resistance, making it suitable for repeated assembly and disassembly, or high-vibration environments.
2. Characteristics of Aluminum Materials
Aluminum and its alloys are widely used in lightweight design due to their unique physical and chemical properties:
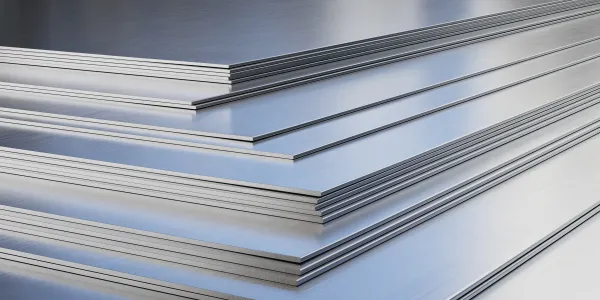
Lightweight: Aluminum’s density is about one-third that of steel, significantly reducing overall structure weight—ideal for weight-sensitive applications.
Soft and Ductile: Aluminum has relatively low hardness and strength, making it easy to form into complex shapes.
Corrosion Resistance: A natural oxide film on the surface offers good protection against corrosion, suitable for outdoor or humid environments.
Soft Structure: Aluminum is prone to dents, deformation, or even cracking under high pressure or localized load—especially when paired with harder fasteners like steel rivet nuts, which may cause stress concentration and local damage.
3. The “Stiffness Mismatch” Problem When Using Steel Rivet Nuts on Aluminum
a. Nature of the Stiffness Mismatch
The stiffness mismatch refers to the mechanical incompatibility between steel rivet nuts and aluminum substrates. This is mainly due to large differences in Young’s modulus (elastic modulus) and hardness between the two materials. Under the same load, steel deforms far less than aluminum, making the aluminum more susceptible to plastic deformation and local denting.
Material | Young’s Modulus (GPa) | Hardness (HV) | Yield Strength (MPa) | Typical Local Pressure (MPa) |
Steel Rivet Nut | 200 | 350–500 | 400–800 | 400–600 (self-loaded) |
Aluminum (6061-T6) | 70 | 95–150 | 275–310 | 350–450 (hole wall pressure) |
- Steel’s Young’s Modulus is around 200 GPa,
- Aluminum’s Young’s Modulus is only 70 GPa — about one-third of steel.
- In typical installation conditions, local pressure from the rivet nut often exceeds the yield strength of aluminum, leading to plastic deformation.
- Dent depth at the hole wall in aluminum is typically 0.1–0.3 mm, which may be critical in precision assemblies.
b. Stress Concentration and Deformation
- During installation, the tail of the steel rivet nut plastically deforms to grip the aluminum wall.
- Due to its higher hardness, the rivet nut exerts concentrated pressure on the aluminum hole wall, creating a stress concentration zone.
- This concentrated stress can reach 1.5× the yield strength of aluminum, causing permanent deformation, dents, or even cracks.
c. Vibration and Fatigue Life Impact
When steel rivet nuts are installed on aluminum, the stiffness mismatch leads to significant concerns under vibration or dynamic loading, impacting long-term joint reliability:
Stress Concentration Accelerates Crack Initiation
- Steel’s much higher stiffness causes excessive stress to concentrate at the aluminum hole wall.
- Under vibration or cyclic loads, these zones experience higher stress amplitudes than the average stress in aluminum, promoting microcrack initiation.
- These cracks propagate over time, reducing connection strength and causing fatigue failure.
Significantly Reduced Fatigue Life
- Experimental data show that fatigue life of aluminum joined with steel rivet nuts is reduced by 30%–50% compared to aluminum-only joints.
- Under the same vibration frequency and load conditions, aluminum with steel rivet nuts fails after far fewer cycles than aluminum with softer or matching materials.
Fatigue Life Illustration (Vibration Environment)
Material Combination | Fatigue Life (Load Cycles) | Notes |
Pure Aluminum Structure | 1,000,000 cycles | Baseline life without rivet nut |
Aluminum + Steel Rivet Nut | 500,000–700,000 cycles | Reduced life due to stiffness mismatch |
Aluminum + Aluminum Rivet Nut | 700,000–900,000 cycles | Better matching, fatigue life improved |
Aluminum + Steel Rivet Nut + Washer Pad | 700,000–850,000 cycles | Load dispersed, fatigue resistance enhanced |
Loosening and Structural Instability Under Vibration
- Micro-motion wear (fretting) tends to occur at the interface between the steel rivet nut and aluminum, gradually weakening the fastening strength.
- Fretting also leads to pitting, surface damage, and crack formation, reducing joint stiffness.
- Once the structure loosens, load redistribution occurs, causing abnormal stress elsewhere and accelerating overall fatigue failure.
Research and Case Studies
- A fatigue test on aluminum alloy structures showed that using aluminum rivet nuts improved fatigue life by 20%–30% compared to steel ones.
- Other studies found that adding interface lubricants and buffer gaskets could enhance fatigue life by up to 40%, mitigating stress concentration caused by stiffness mismatch.
d. How to Avoid or Minimize Stiffness Mismatch Issues?
To safely use steel rivet nuts on aluminum without causing damage, consider the following engineering practices:
- Use Washers or Soft Pads: Add nylon or rubber washers between the rivet nut and aluminum to distribute load and reduce local pressure.
- Optimize Hole Design: Proper hole sizing and tolerance reduce stress concentration and prevent excessive interference fits.
- Control Installation Torque and Tool Settings: Avoid over-tightening or excessive deformation during installation.
- Use Composite or Coated Rivet Nuts: Plastic-coated steel rivet nuts or aluminum rivet nuts minimize stiffness differences.
- Surface Treatment of Aluminum: Anodizing or hard coating aluminum can enhance hardness and wear resistance at the contact interface.
Is There Any Risk In Using Steel Rivet Nuts on Aluminum?
1. Electrochemical Corrosion Risk (Galvanic Corrosion)
a. What Is Galvanic Corrosion?
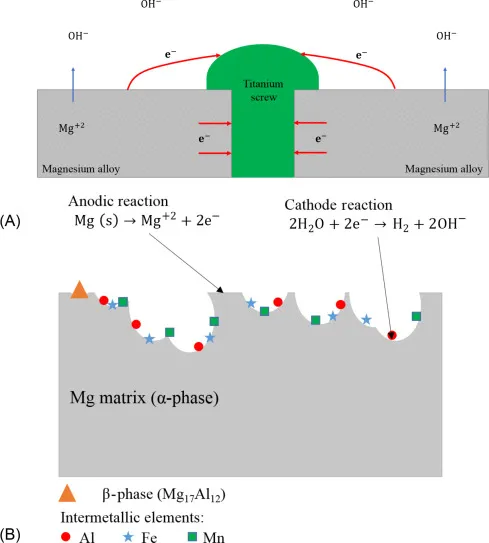
- Definition: Galvanic corrosion occurs when two dissimilar metals are in direct contact and exposed to an electrically conductive electrolyte (such as water, salt spray, or humid air). This creates a miniature electrochemical cell where the more active metal (anode) undergoes oxidation and corrosion, while the more noble metal (cathode) is relatively protected.
- At the contact interface between steel (more noble) and aluminum (more active), electrons flow from aluminum to steel. Aluminum loses electrons, forming aluminum ions, which leads to accelerated corrosion of the aluminum base.
Activity Levels of Common Metals
More Active Metals (Anode): These metals lose electrons more easily and are more prone to corrosion in electrochemical reactions.
Common examples:
- Sodium (Na)
- Magnesium (Mg)
- Aluminum (Al)
- Zinc (Zn)
- Iron (Fe), especially unalloyed
More Noble Metals (Cathode): These resist losing electrons and are less prone to corrosion. However, they can accelerate the corrosion of adjacent active metals.
Common examples:
- Platinum (Pt)
- Gold (Au)
- Noble metal group
- Stainless steel (Cr-Ni alloys)
- Copper (Cu)
Common Galvanic Corrosion Metal Pairings
Pairing | Description | Galvanic Corrosion Behavior |
Aluminum + Steel | Aluminum acts as anode, steel as cathode | Aluminum corrodes locally; steel remains intact |
Magnesium + Copper | Magnesium corrodes rapidly | Copper remains unaffected |
Pairing | Description | Galvanic Corrosion Behavior |
Zinc + Iron | Zinc acts as sacrificial anode | Zinc corrodes first, protecting iron |
Copper + Aluminum | Copper more noble than aluminum | Aluminum corrodes faster; copper stays intact |
- Active metals tend to corrode and act as the anode.
- Noble metals promote corrosion in the active metal and act as the cathode.
- In engineering practice, avoid direct contact between dissimilar metals, or use insulating barriers to prevent galvanic corrosion.
b. Environmental Factors Influencing Galvanic Corrosion
- Humidity and Moisture: Water acts as the electrolyte. A humid environment significantly increases the corrosion rate.
- Salt Spray and Marine Conditions: Salt enhances the conductivity of the electrolyte, dramatically increasing the corrosion rate—especially near coastlines, alkaline soils, or industrial areas.
- Temperature: Higher temperatures accelerate corrosion reactions by increasing electrochemical activity.
c. Effects of Galvanic Corrosion on Aluminum
- Corrosion Product Formation: Aluminum oxidizes into white or grayish-white products (aluminum hydroxide), which accumulate at the interface with the rivet nut, affecting appearance and possibly mechanical function.
- Local Pitting and Perforation: Over time, pitting can develop on the aluminum surface, gradually penetrating the material and reducing structural integrity.
- Loosening Risk: The expansion of corrosion products increases the gap between the rivet nut and the aluminum base, reducing clamping force and potentially causing the connection to loosen or detach.
- Safety Hazards: Corrosion-related failure of structural components may lead to mechanical malfunctions, leakage, or other safety incidents.
d. Real-World Example of Galvanic Corrosion
Example: On an outdoor aluminum alloy enclosure, steel rivet nuts without anti-corrosion treatment were used. After 6 months in a coastal environment, white corrosion products formed around the rivet nuts, along with several pinhole perforations in the aluminum, severely compromising the structural integrity.
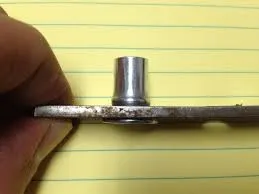
How to Prevent Galvanic Corrosion?
- Use rivet nuts with anti-corrosion coatings such as zinc or nickel plating; anodize aluminum surfaces to increase corrosion resistance.
- Add insulating washers (e.g., nylon) or apply anti-corrosion sealants between steel rivet nuts and aluminum.
- Choose more corrosion-resistant materials, such as stainless steel or aluminum rivet nuts.
- Conduct regular inspections and clean corrosion products promptly.
2. Risk of Aluminum Deformation
a. Mechanism and Manifestations of Aluminum Deformation
Hole Wall Indentation (Dents)
When installing a steel rivet nut, axial force is applied to expand the rear section of the nut, forming a locked joint. Due to the high rigidity and hardness of steel, pressure is concentrated at the contact area on the aluminum hole wall, resulting in visible indentations or dents.
- Typical dent depth: 0.1–0.3 mm; excessive denting may affect the fit and precision of subsequent assembly.
Hole Wall Tearing or Fracture
If the compressive force exceeds the local bearing capacity of the aluminum, the hole wall may fail plastically, initiating cracks that expand and lead to tearing.
- Thin-walled aluminum is especially vulnerable, particularly if wall thickness is below the recommended minimum.
Abnormal Deformation of the Rivet Nut
Excessive pulling force or mismatched rivet nut sizes may cause over-deformation of the tail section, resulting in an unstable or loose joint.
b. Main Causes of Aluminum Deformation
Incorrect Grip Range
The grip range is the material thickness that the rivet nut is designed for. If it’s too small, the tail cannot expand fully. If too large, excessive compressive force is localized, increasing the risk of aluminum deformation.
The grip range is the material thickness that the rivet nut is designed for. If it’s too small, the tail cannot expand fully. If too large, excessive compressive force is localized, increasing the risk of aluminum deformation.
Excessive Installation Force
Aluminum’s lower rigidity makes it more vulnerable to excessive force during installation, especially when operators or tools apply inconsistent or excessive pulling force.
Improper Hole Edge Preparation
Burrs or sharp edges from machining cause stress concentrations. These act as initiation points for cracks during the riveting process.
Variability in Material Thickness and Hardness
Inconsistencies in the aluminum’s hardness or thickness can cause weak zones that are more prone to deformation.
c. How to Prevent Aluminum Deformation
Strict Control of Installation Parameters
- Use automated rivet tools with pressure and torque feedback to control force accurately.
- Establish standard operating procedures (SOPs) and provide operator training.
Select Proper Rivet Nut Specifications
- Measure base material thickness and hardness precisely to select rivet nuts with matching grip ranges.
- Use professional inspection tools to ensure accurate hole diameters and material properties.
Chamfer and Deburr Hole Edges
- Apply chamfers of 0.2–0.5 mm and remove burrs to reduce stress concentration.
- Use mechanical chamfering, deburring, or laser cutting for higher precision.
Add Buffer Washers
- Insert soft washers (nylon, rubber) between the rivet nut and aluminum to distribute pressure and reduce localized stress.
- Washers also help minimize wear due to vibration and increase joint stability.
Material Selection and Quality Control
- Use higher-strength aluminum alloys (e.g., 6061-T6) with better mechanical properties.
- Perform batch hardness and thickness checks to ensure uniformity.
d. Reference Data
Parameter | Range | Notes |
Aluminum Hole Wall Thickness | 1.0–3.0 mm | Thin walls are more prone to damage |
Aluminum Yield Strength | 240–310 MPa | Typical for 6061-T6 aluminum alloy |
Rivet Nut Tail Expansion Pressure | 350–600 MPa | Above aluminum yield strength = risk |
Hole Dent Depth | 0.1–0.3 mm | Typical for well-controlled installs |
How Can I Use Steel Rivet Nuts on Aluminum?
Due to the significant electrochemical and mechanical rigidity differences between steel and aluminum, improper use can lead to galvanic corrosion, aluminum deformation, and even connection failure. Therefore, in engineering design and installation, scientific and preventive measures must be adopted to reduce these potential risks and ensure the reliability and longevity of the fastening structure.
1. Surface Corrosion Protection
To prevent galvanic corrosion and extend the service life of riveted joints, it’s crucial to focus on corrosion prevention at both the rivet nut and the surrounding area:
- Choose Steel Rivet Nuts with Anti-Corrosion Coating:
Use steel rivet nuts with protective surface treatments such as zinc plating, Dacromet, or zinc-nickel alloy coating. These coatings create a dense barrier that blocks moisture and air, significantly reducing the likelihood of corrosion.
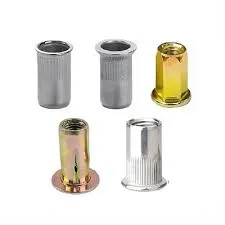
- Add Electrical Insulating Washers or Plastic Coatings:
Insert nylon washers, plastic coatings, or epoxy insulation layers between the rivet nut and the aluminum surface to physically separate the metals and break the galvanic circuit. - Seal the Joint with Anti-Corrosion Sealants:
After installation, apply polyurethane sealant, silicone, or other protective sealants around the nut to block moisture ingress. This is especially important in marine, salty, or humid environments.
2. Select the Correct Size and Hole Tolerance
Choosing rivet nuts that match the structure is critical to avoid aluminum deformation and prevent nut spinning:
Ensure the Grip Range Covers the Aluminum Thickness:
Every rivet nut model has a specified grip range. Ensure the chosen model covers the actual thickness of the aluminum. Undersized or oversized grip ranges can lead to tearing, loose joints, or installation failure.Control Hole Size Tolerances to Avoid Excessive Gaps:
Keep the hole diameter tolerance within ±0.1 mm. Oversized holes can lead to spinning or loosening of the rivet nut, while undersized holes can damage the hole wall during installation.Prefer Anti-Rotation Designs:
Choose knurled body or hex body rivet nuts, which engage mechanically with the hole through friction or shape-matching, significantly enhancing rotation resistance and joint reliability.
3. Alternative Solutions
In applications with lower load requirements but higher corrosion resistance needs, alternative fasteners can minimize risks of corrosion and material damage:
Use Aluminum Rivet Nuts:
Being the same material as the aluminum base, these eliminate galvanic corrosion risk. They are lightweight and easy to install—suitable for light to moderate load-bearing applications.Use Stainless Steel Rivet Nuts:
While stainless steel also has a potential difference with aluminum, it is more corrosion-resistant than carbon steel. Grades like A2 (304) or A4 (316) stainless steel, when used with proper isolation measures, perform well in corrosive environments.Use Insulated or Composite Rivet Nuts:
Some manufacturers offer steel rivet nuts with insulated coatings, such as nylon- or epoxy-coated bodies. These combine the strength of steel with non-conductive surfaces, ideal for precision or electrically sensitive applications.
Summary – Safely Use Steel Rivet Nuts on Aluminum
To safely use steel rivet nuts on aluminum, the core strategy is to combine three key protections:
Anti-corrosion + Anti-deformation + Anti-loosening.
By choosing properly coated products, controlling installation tolerances, and selecting alternative materials when necessary, you can effectively reduce potential risks, ensuring long-term structural stability, reliability, and aesthetic integrity.
When Is It Appropriate (or Not) to Use Steel Rivet Nuts on Aluminum?
✅ Appropriate Scenarios for Using Steel Rivet Nuts on Aluminum
Steel rivet nuts can be reliably used with aluminum structures if proper installation techniques and corrosion protection measures are taken, especially in the following conditions:
1. Indoor or Dry Environments
Applications such as internal components of machinery, office furniture, enclosures, or control cabinets where aluminum parts remain in dry, moisture-free conditions;
No exposure to water vapor, condensation, or salt spray—minimal risk of galvanic corrosion;
Allows full utilization of steel rivet nuts’ high strength to ensure secure fastening.
2. Structures Requiring High Load Capacity
Situations like load-bearing frames, aluminum profile joints, or industrial racks that demand greater tensile or shear strength;
When aluminum or nylon rivet nuts lack sufficient strength, steel rivet nuts can be used with insulating washers and corrosion sealants to balance performance and reliability.
3. Structures with Effective Corrosion Prevention Measures
Where the structure allows post-installation sealing, application of protective coatings, or use of electrical insulation components;
Examples include outdoor enclosures, transportation infrastructure, or solar panel mounts—as long as design ensures no direct metal-to-metal contact, corrosion can be prevented.
❌ Scenarios Where Steel Rivet Nuts Are Not Recommended
In the following cases, using steel rivet nuts directly with aluminum is not advisable, as it can lead to severe galvanic corrosion or structural failure:
1. Highly Corrosive Environments
Such as coastal areas, marine vessels, offshore facilities, salt spray test chambers, or any location with prolonged exposure to moisture, salt, and high humidity;
In these environments, the galvanic potential between steel and aluminum becomes critical—aluminum corrodes rapidly, leading to pitting and perforation.
2. Structures That Cannot Be Properly Sealed
For example, thin-walled aluminum enclosures or covers that cannot be sealed from the back or edges, allowing moisture to enter through the mounting holes;
Corrosion at the hole edges can quickly weaken the fastening strength, compromising overall structural safety.
3. Lightweight Structures Frequently Exposed Outdoors
Such as temporary display stands, outdoor light poles, or advertising frames, which are exposed to rain, dust, and infrequent maintenance;
In these applications, corrosion can go unnoticed until structural fatigue or failure occurs, especially when using steel rivet nuts without protection.
Conclusion - Can I Use Steel Rivet Nuts on Aluminum?
Steel rivet nuts can be used on aluminum, but proper corrosion protection, galvanic isolation, and controlled installation force are essential.
For applications in outdoor, high-humidity environments or where long-term durability is critical, it is recommended to use more compatible material combinations, such as stainless steel rivet nuts or insulated rivet nuts.
With the right selection and installation, you can achieve strong fastening performance while avoiding corrosion and material damage.
Do You Have Any Questions?
Let Us Solve Your Problem
Buy Steel Rivet Nuts from Rivetfix
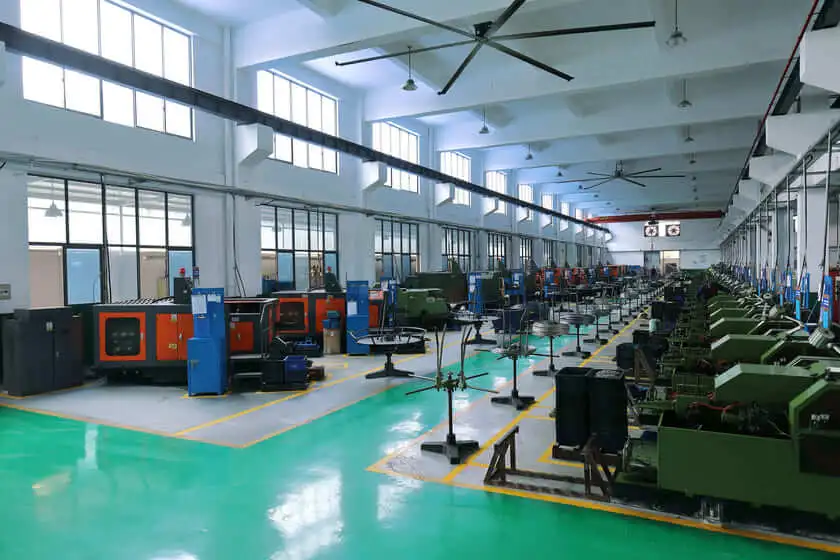
As a leading fastener manufacturer in China with more than 15 years in the industry, Rivetfix are committed to providing first-class quality fasteners and responsive services to the world. We offers a wide range of rivet nuts and clinch nuts designed to meet the unique demands of your projects. Rivetfix ensures you have the right solution for every application. Choose Rivetfix for versatile, cost-effective, and durable fastening solutions tailored to your specific needs. In addition, we can also provide customized rivet nuts service and clinch nuts according to your requirements.
Contact us now for more information and customization options on Rivet Nuts!
Get High Quality Rivet Nuts Quote!
Send Your Rivet Nut Request
For more than 20 years, Rivetfix has helped customers solve many rivet nuts sourcing needs and technical challenges.
Have a question? Contact us and we’ll provide you with the perfect solution.