How to Choose Thick Wall Rivet Nuts?
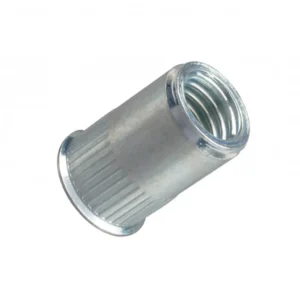
Leading Rivet Nut Manufacturer and Supplier in China
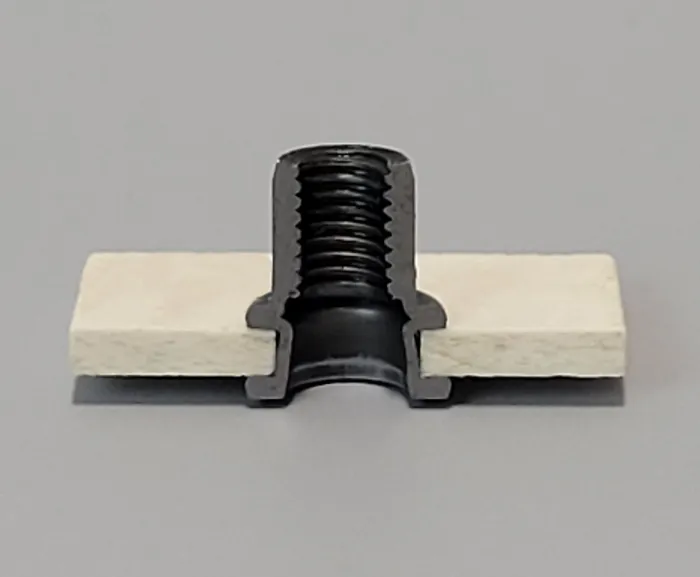
Choosing the right thick wall rivet nuts is essential for ensuring strong and reliable fastening in heavy-duty applications. With various types, materials, and grip ranges available, selecting the best option depends on factors like wall thickness, load requirements, and installation methods. Using the wrong rivet nut can lead to loosening, rotation failure, or weak joints. In this guide, we’ll explore key considerations for choosing the most suitable thick wall rivet nuts, helping you achieve secure and long-lasting connections in demanding environments.
Table of Contents
What is a Thick Wall Rivet Nut?
A thick-wall rivet nut is a type of fastener designed for use in thin or non-threaded base materials, providing a strong internal thread for bolted connections. Unlike standard thin-wall rivet nuts, thick-wall variants have a greater wall thickness, offering higher strength and load-bearing capacity. They are installed through a riveting process, ensuring secure attachment to the workpiece while withstanding higher torque and tensile forces.
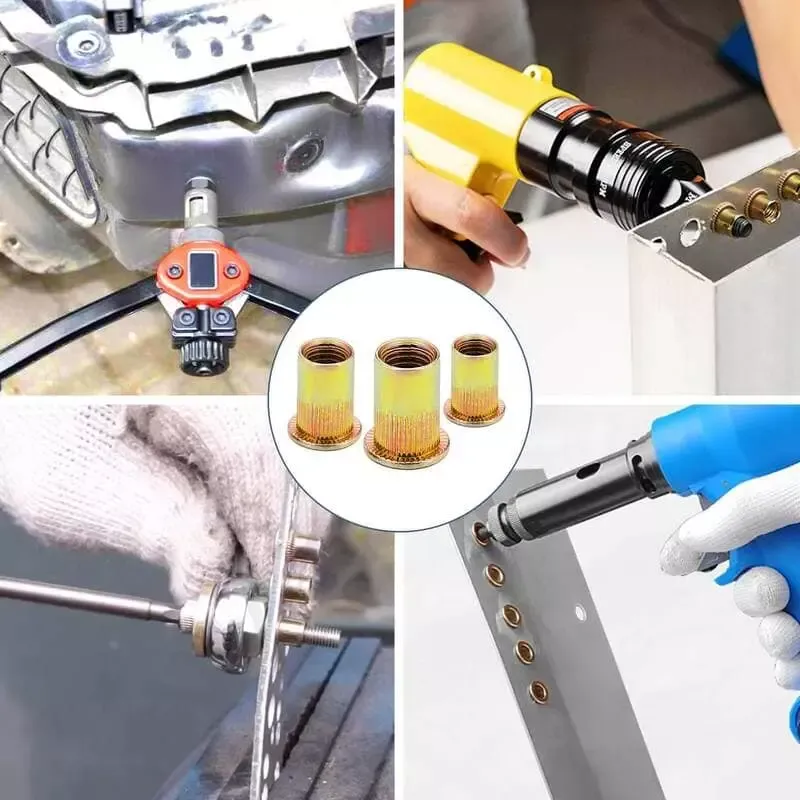
Main Applications of Thick-Wall Rivet Nuts
Thick-wall rivet nuts are widely used in various industries, including:
- Automotive Manufacturing – Structural components, chassis, seats, doors, and other critical connections.
- Rail Transportation – High-strength threaded connections in high-speed trains, subways, and railway infrastructure.
- Aerospace Industry – Lightweight yet strong fastenings for aircraft and spacecraft structures.
- Construction and Heavy Machinery – Structural fastening in excavators, cranes, and industrial equipment.
- Electrical and Cabinet Manufacturing – Secure threading in sheet metal enclosures and electronic device housings.
- Shipbuilding and Marine Equipment – Corrosion-resistant applications in harsh marine environments.
Differences Between Thick-Wall and Thin-Wall Rivet Nuts
Comparison | Thick-Wall Rivet Nut | Thin-Wall Rivet Nut |
Wall Thickness | Thicker, providing higher strength and durability | Thinner, suitable for lighter load applications |
Load Capacity | Withstands higher tensile and torque forces | Suitable for medium or light-duty connections |
Material Thickness | Ideal for thicker base materials (>1.5mm) | Works well with thin materials (0.5–3.0mm) |
Application Scenarios | High-strength and heavy-load environments (e.g., automotive, machinery, rail transport) | Lightweight structures or general sheet metal fastening |
Cost | Higher, but offers better durability | Lower cost, suitable for standard applications |
Types of Thick Wall Rivet Nuts
Choosing the right rivet nut is crucial for applications involving thick-wall materials. Different types of rivet nuts vary in structure, installation methods, and suitability. Below are the most common types of rivet nuts and their applicability to thick-wall materials.
Features:
- Flat head design sits flush with the workpiece surface, ideal for applications requiring surface smoothness.
- Provides a larger bearing surface, enhancing pull-out resistance.
- Compatible with various materials, including steel, aluminum, and stainless steel.
Application Scenarios:
- Industrial equipment installations requiring high load-bearing capacity.
- Metal connections in machinery manufacturing and the automotive industry.
Usage on Thick-Wall Materials:
- Suitable for metal sheets over 3mm thick.
- Extended flat head rivet nuts should be used to ensure proper fastening strength.
Features:
- Conical head design allows the nut to be embedded into the material, creating a completely flush surface.
- Ideal for applications where protruding fasteners could affect appearance or assembly.
- Provides high-strength fastening and can withstand significant axial and radial loads.
Application Scenarios:
- Aerospace, automotive, and other industries requiring high surface flatness.
- Threaded connections in electronic devices and precision machinery.
Usage on Thick-Wall Materials:
- Requires pre-drilled countersunk holes to accommodate the nut’s head.
- Best suited for materials with a thickness of 5mm or more to ensure proper countersinking.
Features:
- Smaller head diameter makes it ideal for installations in confined spaces.
- Prevents interference with assembly or appearance.
- Offers good fastening performance but slightly lower pull-out strength due to its smaller head.
Application Scenarios:
- Mounting small electronic devices, instruments, and panels.
- Assemblies where rivet nuts need to be hidden.
Usage on Thick-Wall Materials:
- Suitable for materials over 4mm thick.
- For high-hardness materials, stainless steel versions are recommended for better strength.
Best for Thick-Wall Materials | Maximum Anti-Rotation Strength
Features:
- Hexagonal exterior prevents the nut from rotating under torque.
- Ideal for high-torque applications, providing superior locking strength.
- Suitable for high-strength and high-hardness materials, such as steel and stainless steel.
Application Scenarios:
- Machinery manufacturing and heavy-duty equipment installation.
- High-vibration environments, such as automotive chassis and railway industries.
Usage on Thick-Wall Materials:
- Suitable for materials 5mm and thicker.
- Requires pre-drilled hexagonal holes to ensure a secure fit.
Features:
- Partially hexagonal exterior provides better stability than round rivet nuts in high-torque environments.
- Offers strong fastening while requiring less complex hole preparation than full hex rivet nuts.
Application Scenarios:
- Applications requiring some resistance to rotation but where hexagonal holes cannot be machined.
- Engineering machinery, shipbuilding, and heavy-duty industries.
Usage on Thick-Wall Materials:
- Suitable for materials over 4mm thick.
- Requires appropriately sized pre-drilled holes for optimal fastening.
Features:
- Sealed-end design prevents the entry of liquids, dust, or gases.
- Ideal for environments requiring high sealing performance.
Application Scenarios:
- Marine applications, outdoor equipment, and medical instruments.
- Environments where contamination or liquid intrusion must be prevented.
Usage on Thick-Wall Materials:
- Suitable for metal or plastic materials over 4mm thick.
- Stainless steel or zinc-plated versions are recommended for better corrosion resistance.
Do You Have Any Questions?
Let Us Solve Your Problem
How to Choose Thick Wall Rivet Nuts?
Thick wall materials are typically 3mm or more in thickness. Standard rivet nuts may not provide sufficient clamping force, so it’s necessary to choose extended-length rivet nuts or specialized thick-wall rivet nuts.
Recommended choices:
- 3-5mm thickness: Standard rivet nuts can be used, but longer models are recommended.
- 5-10mm thickness: Use extended-length rivet nuts to ensure full expansion and secure fastening.
- Above 10mm thickness: Specialized mechanical lock rivet nuts, such as full hex rivet nuts or threaded inserts, may be required.
2. Material Selection
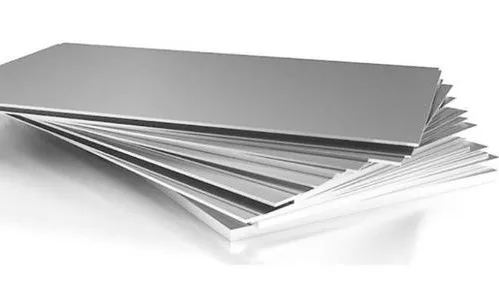
The material of the rivet nut should match the base material to ensure good mechanical performance and corrosion resistance.
Common materials and their applications:
- Carbon Steel: High strength, suitable for heavy-duty industrial equipment and machinery manufacturing.
- Stainless Steel: Excellent corrosion resistance, ideal for outdoor, high-humidity, or chemical environments, such as marine and food processing equipment.
- Aluminum: Lightweight, suitable for aerospace and electronic applications, but has lower strength.
3. Rivet Nut Type
Different types of rivet nuts perform differently in materials. The choice should be based on the specific application.
Recommended choices:
- High torque resistance needed ➝ Choose full hex rivet nuts or half hex rivet nuts to prevent spinning.
- Smooth surface required ➝ Choose countersunk rivet nuts to avoid protrusions affecting assembly.
- Sealing required ➝ Choose sealed-end rivet nuts to prevent moisture and dust ingress.
- Limited installation space ➝ Choose reduced head rivet nuts, suitable for compact spaces.
4. Load Capacity
Rivet nuts must withstand both axial tensile loads and radial shear loads. If the load is too high, the fastening may fail.
Recommended choices:
- For high-strength applications ➝ Choose steel or stainless steel rivet nuts to prevent deformation or loosening.
- For heavy-duty equipment ➝ Choose thick-wall-specific rivet nuts, such as mechanical lock types, to ensure sufficient fastening strength.
5. Hole Shape and Preparation
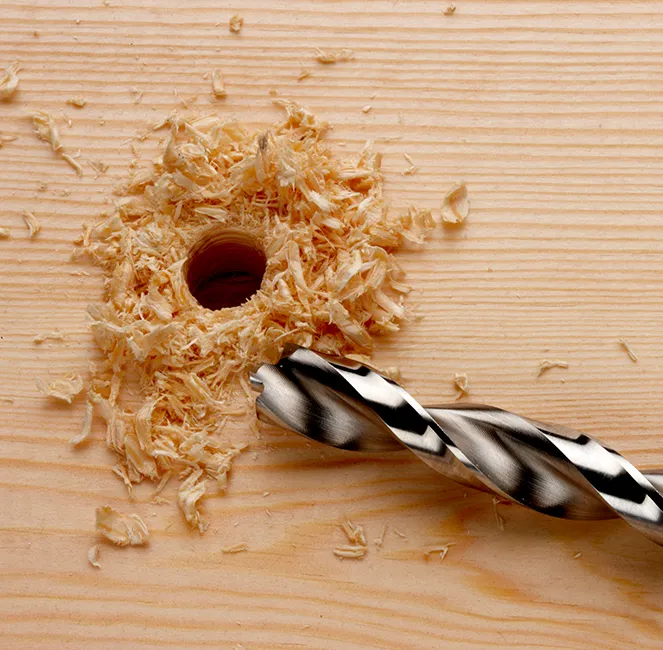
Different rivet nut types have specific hole shape requirements. Improper hole design can lead to installation failure.
Recommended choices:
- Standard round hole ➝ Suitable for flat head and countersunk rivet nuts.
- Hexagonal hole ➝ Required for full hex rivet nuts to prevent rotation.
- Countersunk hole design ➝ Necessary for countersunk rivet nuts, ensuring a flush surface.
6. Matching Installation Tools
Thick wall materials require greater fastening force, so the appropriate installation tools must be used.
Recommended tools:
- Hand Rivet Nut Tool: Suitable for small-scale assembly or light-duty applications.
- Pneumatic/Hydraulic Rivet Nut Gun: Ideal for high-strength fastening, recommended for thick-wall materials.
- Torque-Controlled Tools: Ensures secure fastening in high-load environments.
7. Corrosion Resistance Requirements
Rivet nuts exposed to moisture or corrosive environments are prone to rust and damage.
Recommended choices:
- Indoor environment ➝ Choose zinc-plated steel rivet nuts for cost-effectiveness.
- Outdoor or high-humidity environments ➝ Choose stainless steel rivet nuts for enhanced corrosion resistance.
- Extreme corrosion environments (chemical, marine) ➝ Choose 316 stainless steel or nickel-plated rivet nuts.
Summary: Thick Wall Rivet Nut Selection Guide
Key Factor | Recommended Choice |
Material Thickness | 3-5mm: Standard rivet nuts; 5mm+: Extended-length or hex-type rivet nuts |
Material | Steel (high strength), Stainless Steel (corrosion-resistant), Aluminum (lightweight) |
Rivet Nut Type | Flat head (general use), Countersunk (flush surface), Hexagonal (anti-rotation) |
Load Capacity | Use extended-length or hex-type rivet nuts for high-load applications |
Hole Shape | Round hole (standard), Hexagonal hole (anti-rotation), Countersunk hole (flush surface) |
Installation Tools | Pneumatic/Hydraulic tools recommended for thick-wall materials |
Corrosion Resistance | Zinc-plated steel for indoor use, stainless steel for outdoor, 316 stainless steel for extreme conditions |
How to Install Thick Walls Rivet Nuts?
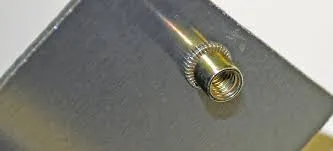
When installing rivet nuts on thick wall materials, it is essential to ensure the correct hole diameter, proper installation pressure, and appropriate tools to guarantee a secure and reliable fastening. The following are key technical points in the installation process:
If the hole is too large, the rivet nut may not be securely fastened; if too small, it may deform or be difficult to install.
Hole Diameter Calculation:
- Hole diameter = Rivet nut outer diameter + 0.1mm to 0.2mm (standard tolerance)
- Example data (for M6 rivet nuts):
- Full hex rivet nut: Recommended hole diameter 9.05mm ± 0.1mm
- Round rivet nut: Recommended hole diameter 9.1mm ± 0.2mm
- Countersunk rivet nut: Recommended hole diameter 9.2mm ± 0.1mm (requires countersinking)
Special requirements for thick wall materials:
- For thickness ≥5mm, hexagonal holes are recommended for hex rivet nuts to prevent rotation failure.
- High-strength materials (e.g., stainless steel) require precision drilling or laser cutting to ensure hole accuracy.
2. Installation Pressure and Riveting Force
Insufficient pressure may cause the rivet nut to be incompletely expanded, reducing fastening strength. Excessive pressure may damage the rivet nut or deform the material.
Recommended Installation Force (Tensile Load):
Rivet Nut Size | Required Tensile Load (N) | Recommended Installation Pressure (MPa) |
M4 | 8,000 – 12,000 | 35 – 50 |
M5 | 12,000 – 16,000 | 40 – 55 |
M6 | 15,000 – 22,000 | 50 – 70 |
M8 | 20,000 – 30,000 | 65 – 90 |
M10 | 30,000 – 45,000 | 80 – 110 |
Additional requirements for thick wall materials:
- If thickness > 8mm, use high-strength rivet nuts (e.g., extended type, hex type) for better fastening.
- Stainless steel rivet nuts require higher installation force and should be installed using hydraulic or pneumatic tools for stability.
3. Selection of Installation Tools
Manual tools may not provide sufficient force for thick wall materials, leading to incomplete riveting. Choosing the right installation tool is crucial.
Recommended Tools:
Tool Type | Applicable Rivet Nut Size | Suitable Thickness | Features |
Manual Rivet Nut Tool | M3 – M6 | 3-5mm | Suitable for small-scale installation, low torque |
Pneumatic Rivet Nut Tool | M4 – M10 | 3-8mm | Fast installation, ideal for medium production volumes |
Hydraulic Rivet Nut Tool | M6 – M12 | 5-12mm | High-strength riveting, suitable for heavy-duty applications |
Electric Rivet Nut Tool | M8 – M12 | 5mm+ | Precision fastening, prevents overloading |
Recommended Installation Methods for Thick Wall Materials:
- Thickness <5mm: Manual or pneumatic rivet nut tools can be used.
- Thickness 5-8mm: Pneumatic or hydraulic rivet nut tools are recommended.
- Thickness >8mm: Hydraulic tools or torque-controlled tools must be used to ensure sufficient installation force.
4. Grip Range and Rivet Nut Selection
Grip range is the material thickness that the rivet nut can properly fasten. If the grip range is insufficient, the nut cannot be securely installed.
Recommended Grip Range Calculation:
Grip Range = Material Thickness + 0.5mm (installation tolerance)
Rivet Nut Size | Standard Grip Range (mm) | Extended Grip Range (mm) |
M4 | 0.5 – 3.0 | 2.5 – 6.0 |
M5 | 0.5 – 3.5 | 3.0 – 7.0 |
M6 | 0.5 – 4.0 | 3.5 – 9.0 |
M8 | 1.0 – 4.5 | 4.0 – 10.0 |
M10 | 1.5 – 5.5 | 5.0 – 12.0 |
Considerations for Thick Wall Materials:
- Standard rivet nuts are suitable for 3-5mm thick plates, but for thickness >5mm, extended-type rivet nuts must be used.
- The grip range must cover the material thickness; otherwise, the rivet nut will not be properly secured.
5. Quality Inspection and Installation Check
After installation, the rivet nuts should be inspected to ensure they meet the required standards. Improper installation may lead to loosening or failure.
Recommended Inspection Methods:
- Visual Inspection: The rivet nut should be fully expanded and the threads undamaged.
- Torque Test: Use a torque wrench to verify the rivet nut withstands the required torque (e.g., M6 rivet nut should withstand 10-12 N·m).
- Tensile Load Test: Use a pull-out test machine to check the riveting strength (e.g., M8 rivet nuts should withstand at least 20,000N).
Common Installation Issues and Solutions:
Issue | Possible Cause | Solution |
Rivet nut spins in place | Hole too large or insufficient torque | Use hex rivet nuts or increase installation torque |
Rivet nut not fully expanded | Insufficient pulling force | Use a stronger rivet nut tool |
Material deformation | Excessive installation pressure | Choose the correct grip length |
Thread damage | Excessive torque | Use torque-controlled tools |
Do You Have Any Questions?
Let Us Solve Your Problem
Rivetfix - Leading Rivet Nuts Supplier in China
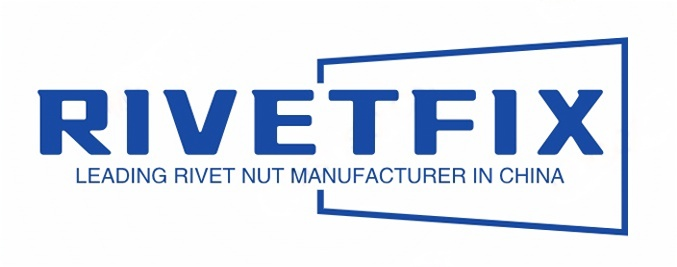
As a leading fastener manufacturer in China with more than 15 years in the industry, Rivetfix are committed to providing first-class quality fasteners and responsive services to the world.
Rivetfix offers a wide range of rivet nuts designed to meet the unique demands of your projects. With options like countersunk, flat, and hex heads, as well as knurled and round body types, Rivetfix ensures you have the right solution for every application. Choose Rivetfix for versatile, cost-effective, and durable fastening solutions tailored to your specific needs. In addition, we can also provide customized rivet nuts service according to your requirements.
Contact us for project advice and the latest rivet nut quote!
Get High Quality Rivet Nuts Quote!
Send Your Rivet Nut Request
For more than 20 years, Rivetfix has helped customers solve many rivet nuts sourcing needs and technical challenges.
Have a question? Contact us and we’ll provide you with the perfect solution.