How to Use Rivet Nut Tool
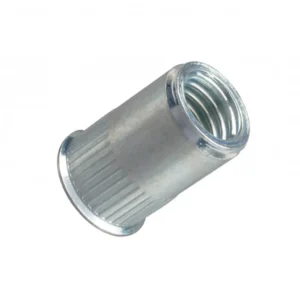
Leading Rivet Nut Manufacturer and Supplier in China
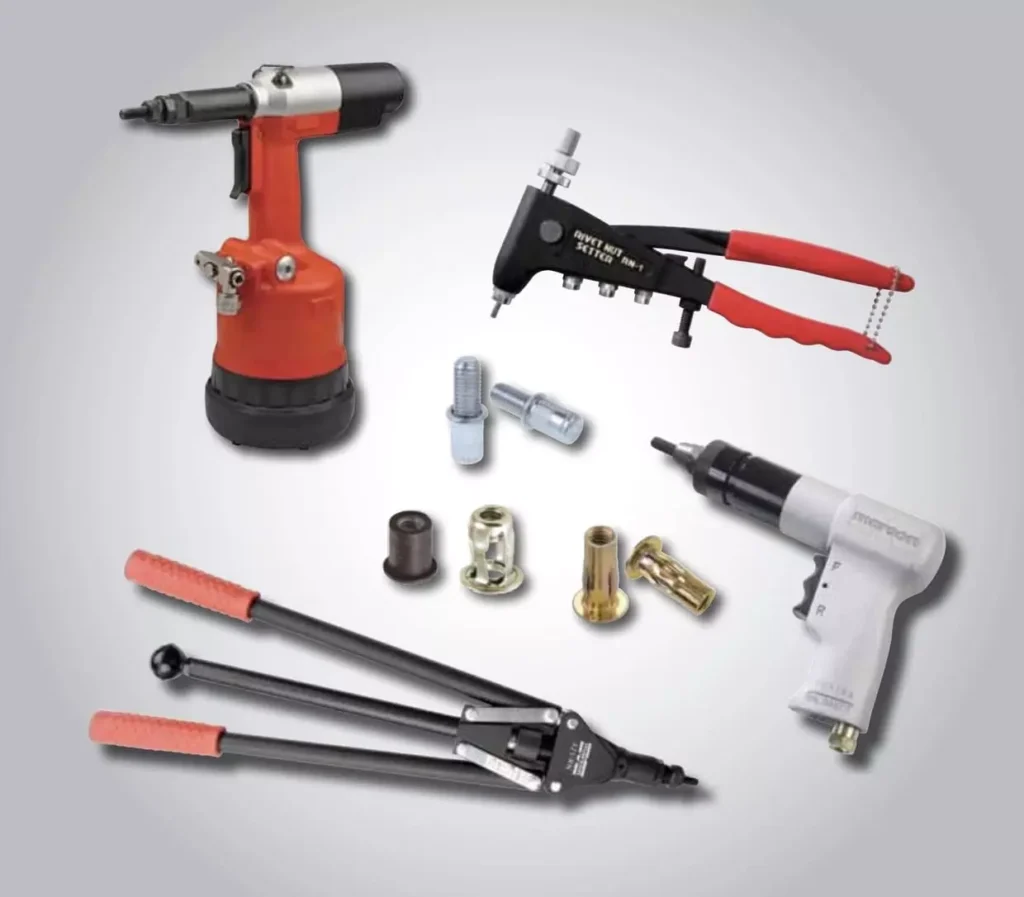
Learning how to use a rivet nut tool correctly is essential for achieving secure and reliable fastenings. Whether you’re working with metal, plastic, or composite materials, this guide will walk you through the proper steps to ensure a smooth installation process and prevent common issues.
Table of Contents
What Is a Rivet Nut Tool?
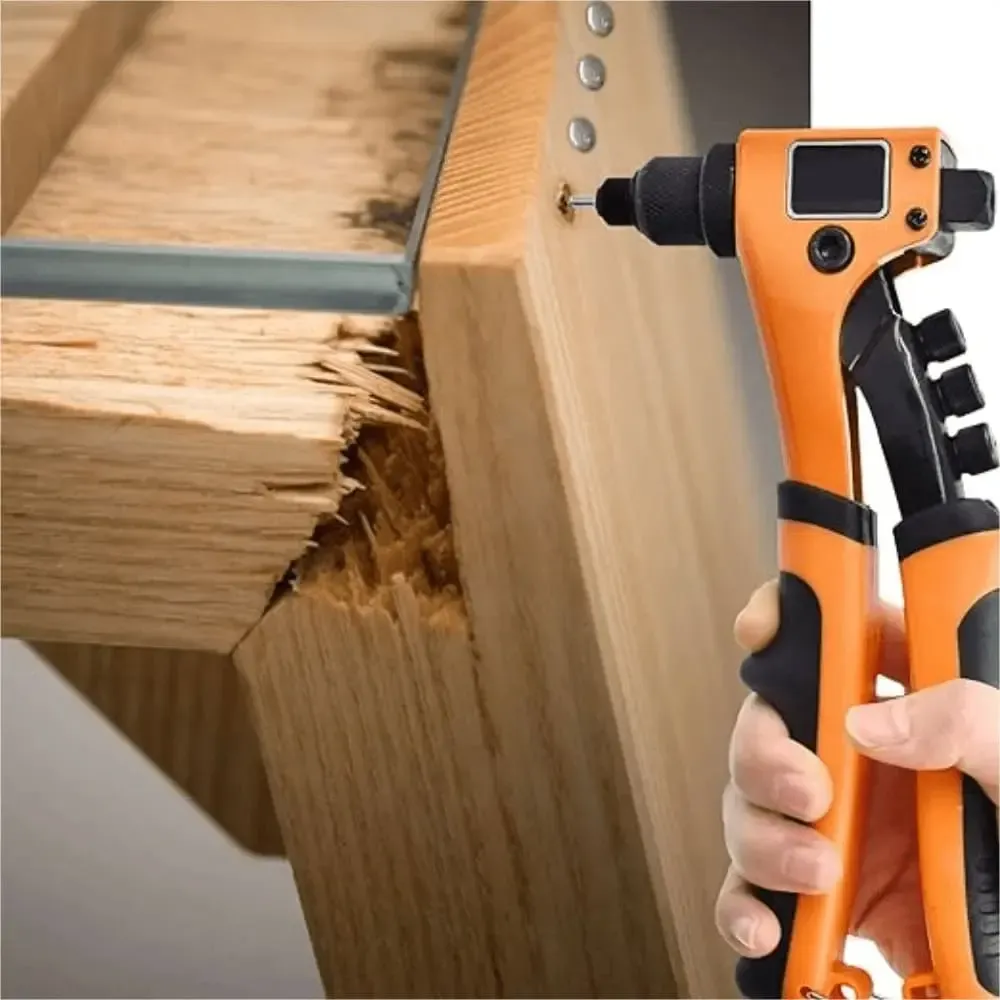
1. Definition of Rivet Nut Tool
A Rivet Nut Tool is a specialized fastening tool used to install rivet nuts (also known as blind rivet nuts). Its primary function is to create a threaded connection in thin-walled materials or materials that cannot be directly threaded, securely fixing the rivet nut inside the base material. This provides a stable threaded structure for installing bolts or other fasteners.
Unlike traditional threading methods, a rivet nut tool can complete the threaded connection on workpieces where access from the back side is impossible (such as closed pipes or thin metal sheets), making it especially suitable for thin sheet materials or soft materials.
2. Uses and Functions of a Rivet Nut Tool
The primary function of a rivet nut tool is to create a reliable threaded connection in thin-walled materials, and it is widely used in the following scenarios:
- Blind Installation: When the back side is inaccessible or cannot be fastened with a nut (such as closed pipes, internal frames of machinery), a rivet nut provides a reliable internal thread.
- Enhancing Thread Strength: For thin sheet materials, directly tapped threads may be too fragile. A rivet nut, through expansion and fixation, provides a stronger thread-bearing capacity.
- Improving Fastening Efficiency: Compared to traditional welded nuts or threading, rivet nuts install faster, require no high-temperature operation, and avoid material deformation issues.
- Adaptability to Various Materials: Whether for hard metals or soft plastics, a suitable rivet nut type can be used for installation.
3. Materials Suitable for Rivet Nut Tools
Rivet nut tools are suitable for a wide range of materials, including but not limited to:
(1) Metal Materials
Applicable for thin sheet structures made of the following metals:
- Steel: Used in high-strength structures such as automobiles and electromechanical equipment.
- Aluminum: Commonly used in aerospace and automotive body applications for lightweight purposes.
- Stainless Steel: Used in corrosive environments such as shipbuilding and medical equipment.
(2) Plastic Materials
Some high-strength plastics can also be used with rivet nut tools, including:
- ABS (Acrylonitrile Butadiene Styrene): Often used in electronic device housings and automotive interiors.
- PVC (Polyvinyl Chloride): Widely used in piping systems and construction materials.
- PC (Polycarbonate): Suitable for high-strength, impact-resistant transparent materials.
For plastic materials, it is generally recommended to use knurled rivet nuts to enhance grip strength and prevent the nut from rotating or loosening during installation.
(3) Composite Materials
Rivet nut tools are also suitable for the following composite materials:
- Fiberglass: Used in boat manufacturing, sports equipment, and other fields.
- Carbon Fiber: Applied in aerospace, high-end bicycles, racing cars, and other industries.
For composite materials, special care must be taken to avoid cracking and delamination. It is recommended to use low-speed drilling and enhance the area around the hole with epoxy resin treatment.
Types of Rivet Nut Tools
A Rivet Nut Tool is used to securely install rivet nuts into base materials, creating reliable threaded connections. Based on different application needs, installation scale, and operation modes, rivet nut tools are mainly divided into Hand Rivet Nut Tools, Pneumatic/Electric Rivet Nut Tools, and Hydraulic Rivet Nut Tools. Below is a detailed introduction to each type of tool.
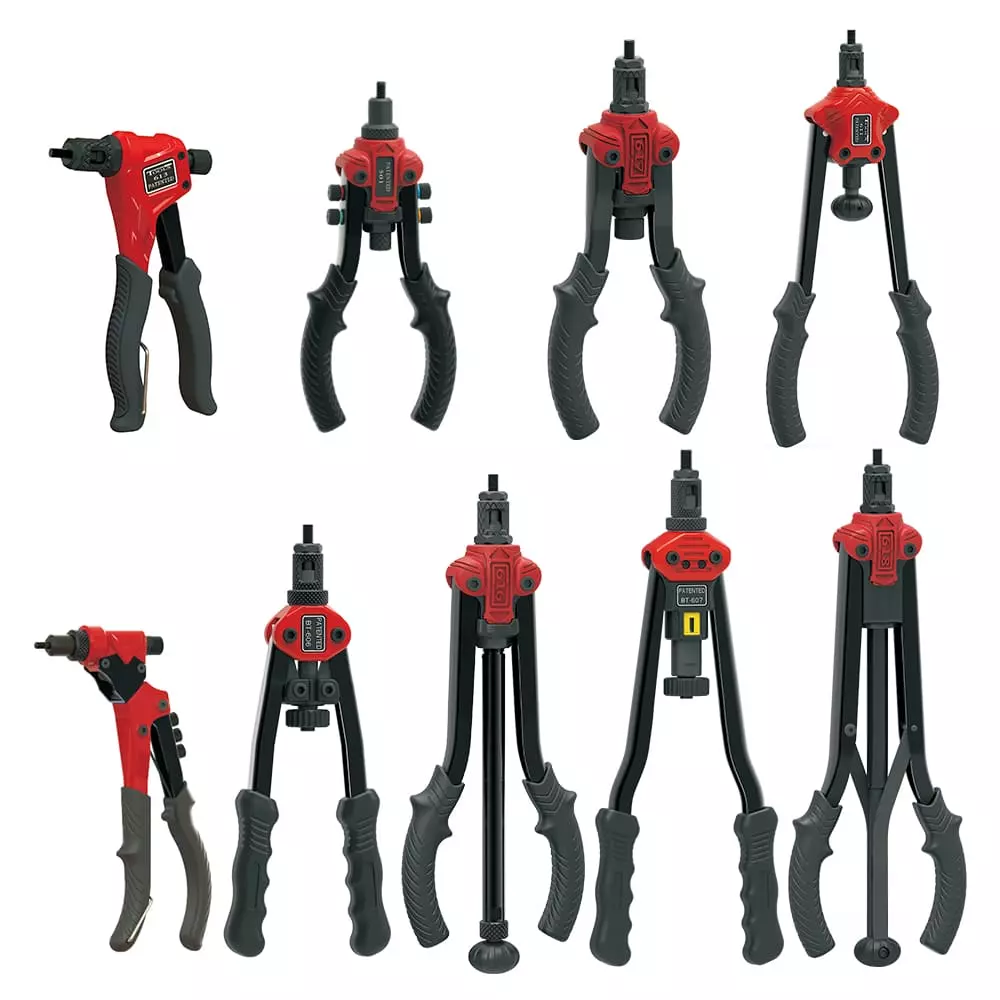
Features:
- Operation Mode: Operates completely manually, using leverage or a rotating mechanism to install rivet nuts into the base material.
- Applicable Nut Sizes: Generally suitable for rivet nuts of M3-M8 (imperial sizes from 6-32 to 5/16-18); larger sizes may require more force.
- Simple Structure: Typically consists of handles, a riveting rod, and interchangeable heads, making it portable and easy to use.
- Low Cost: More affordable, ideal for users with limited budgets.
- Suitable for Softer Materials: Such as aluminum, thin steel sheets, plastics, etc. However, for high-strength metals, more force may be needed, or the installation may not be feasible.
Suitable Scenarios:
- DIY & Repair Work: Ideal for small repairs, garage fixes, furniture assembly, and other low-frequency use cases.
- Light Industrial Applications: Such as electronic device assembly, cabinet installation, etc.
- Mobile Construction: Due to its portability, it is suitable for fieldwork or environments without power supply.
Disadvantages:
- Lower Efficiency: Requires manual installation, and the installation time for each rivet nut is relatively long.
- Fatigue Risk: During large batch installations, operators may become fatigued, impacting work efficiency.
- Not Suitable for Thick Plates or High-Strength Materials: For high-strength steel plates or stainless steel, installation may be difficult or impossible.
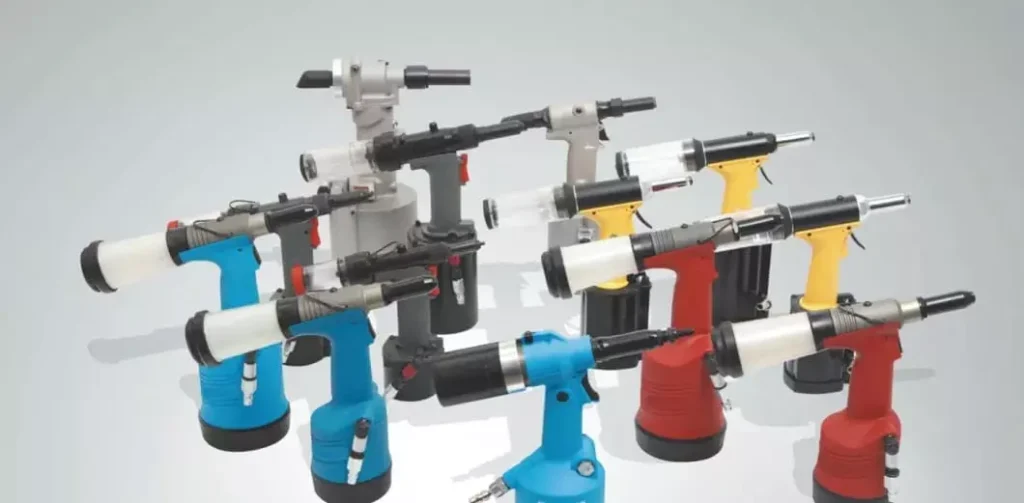
Features:
- Operation Mode: Driven by compressed air or an electric motor, requiring no manual force, enabling fast installation of rivet nuts.
- Applicable Nut Sizes: Typically supports M4-M12 (imperial sizes from 8-32 to 1/2-13); some high-power models can support larger sizes.
- Fast Installation Speed: Compared to hand tools, significantly improves installation efficiency, ideal for mass production.
- High Stability: Fixed torque or stroke settings ensure consistent installation quality.
- Suitable for Various Materials: Including aluminum, steel, stainless steel, plastics, and composite materials, making it highly adaptable.
Suitable Scenarios:
- Factory Production Lines: Such as automotive manufacturing, home appliance assembly, electromechanical equipment production, etc.
- High-Precision Installation: For industries requiring high precision, such as aerospace, medical equipment, and electronic products.
- Mass Production: Suitable for industries that need to install a large number of rivet nuts daily, significantly improving efficiency.
Disadvantages:
- Higher Equipment Cost: Pneumatic/electric rivet nut tools are more expensive than hand tools, making them more suitable for long-term use by enterprise users.
- Dependence on Air or Power Supply: Pneumatic tools require connection to a compressed air system, while electric tools require a stable power supply, which is not suitable for environments without power.
- Higher Maintenance Costs: Pneumatic or electric tools require regular maintenance to ensure stable long-term operation.
3. Hydraulic Rivet Nut Tool
Features:
- Operation Mode: Uses hydraulic drive, providing extremely high riveting pressure, ideal for thick plates and high-strength materials.
- Applicable Nut Sizes: Typically supports M6-M20 (imperial sizes from 1/4-20 to 3/4-10), and can even accommodate larger rivet nuts.
- Super Strong Clamping Force: Suitable for thick steel plates, stainless steel, and alloy materials, ensuring the rivet nut is securely fixed.
- Stationary Use: Generally used in industrial production lines, the tool is heavier and not suitable for portable use.
- High Precision: The hydraulic system ensures stable pressure control, guaranteeing consistent installation and reducing human error.
Suitable Scenarios:
- Automotive Manufacturing: Such as high-strength rivet nut installation in vehicle frames, chassis, and engine compartments.
- Heavy Machinery Manufacturing: Used in construction machinery, railway equipment, aerospace, etc.
- High-Strength Structural Installations: Suitable for bridges, ships, large steel structures, and more.
Disadvantages:
- Expensive: Hydraulic tools are the most costly and are generally only suitable for large-scale industrial production.
- Not Portable: Due to the size of the equipment, it is better suited for stationary workstations and is not ideal for mobile construction.
- Complex Maintenance: The hydraulic system requires regular maintenance, as failure to do so may result in pressure loss or oil leakage.
Form:Summary and Selection Advice
Tool Type | Advantages | Disadvantages | Suitable Scenarios |
Hand Rivet Nut Tool | Low cost, portable, suitable for small batch jobs | Requires high force, lower efficiency, not suitable for thick plates | Repairs, DIY, light industry, mobile construction |
Pneumatic/Electric Rivet Nut Tool | Fast installation, high precision, suitable for mass production | Higher cost, dependent on air or power supply | Automotive manufacturing, appliance assembly, electronic devices |
Hydraulic Rivet Nut Tool | High clamping force, suitable for high-strength materials | Expensive, heavy equipment, complex maintenance | Automotive manufacturing, aerospace, heavy machinery |
How to Choose the Right Rivet Nut Tool?
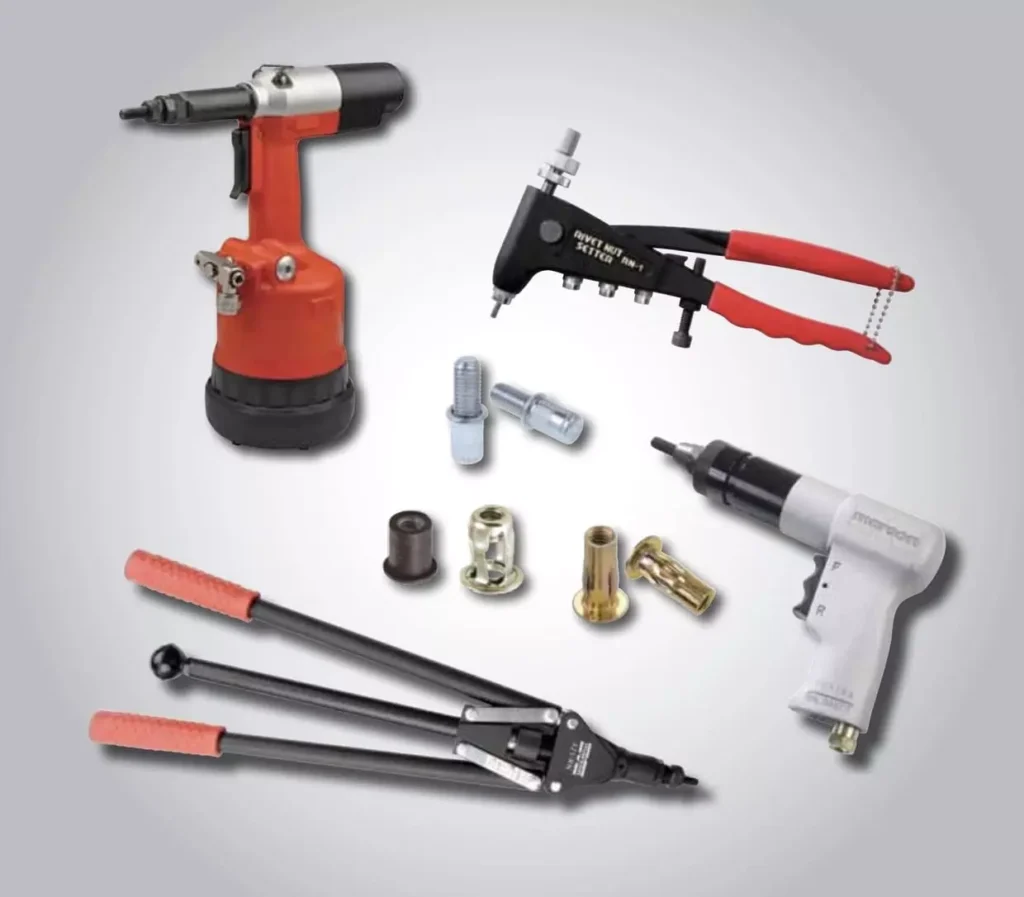
- Small batch installation or repairs → Choose Hand Rivet Nut Tool, which is affordable and portable.
- Medium-scale production or efficiency improvement → Choose Pneumatic/Electric Rivet Nut Tool, which provides fast installation and consistent quality.
- High-strength, high-precision requirements → Choose Hydraulic Rivet Nut Tool, ideal for large-scale industrial production.
By considering the installation requirements, rivet nut size, base material hardness, and budget, you can select the right tool to improve production efficiency and ensure a secure and stable rivet nut installation.
Do You Have Any Questions?
Let Us Solve Your Problem
How to Choose the Right Rivet Nut?
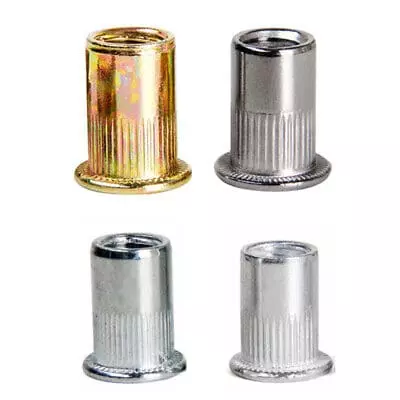
① Choose Based on Material Thickness
Material Thickness | Recommended Rivet Nut Type |
< 1.0mm (Extremely Thin Materials) | Jack Nut, Round Body Rivet Nut |
1.0mm – 3.0mm (Thin Sheet) | Knurled Body Rivet Nut |
> 3.0mm (Medium Thickness) | Hexagonal Rivet Nut, Knurled Body Rivet Nut |
② Choose Based on Load Requirements
Load Level | Recommended Rivet Nut Type | Applicable Materials |
Light Load (< 100N) | Smooth Body Rivet Nut, Jack Nut | Plastic, Aluminum Alloy, Thin Metal Sheets |
Medium Load (100N – 500N) | Knurled Body Rivet Nut | Steel, Composite Materials, Medium-thickness Metals |
Heavy Load (> 500N) | Hexagonal Rivet Nut | Steel Structures, Engineering Machinery, Heavy-duty Applications |
③ Other Considerations
- Do you need anti-rotation ability?
- Yes → Choose Knurled Body Rivet Nut or Hexagonal Rivet Nut.
- No → Choose Smooth Body Rivet Nut.
- Is the base material soft (plastic, thin aluminum)?
- Yes → Choose Jack Nut or Smooth Body Rivet Nut.
- No → Choose Knurled Body Rivet Nut or Hexagonal Rivet Nut.
Conclusion - How to Choose the Right Rivet Nut
- For light loads and soft materials (e.g., plastic, thin aluminum), Round Body Rivet Nut or Jack Nut are recommended.
- For medium loads and metal sheets, Knurled Body Rivet Nut is ideal to enhance anti-rotation ability.
- For heavy loads and heavy-duty applications (e.g., automotive, machinery), Hexagonal Rivet Nut ensures maximum clamping force.
Choosing the right rivet nut type can improve installation stability, extend service life, reduce maintenance costs, and ensure the fastening meets application requirements.
How to Use a Rivet Nut Tool?
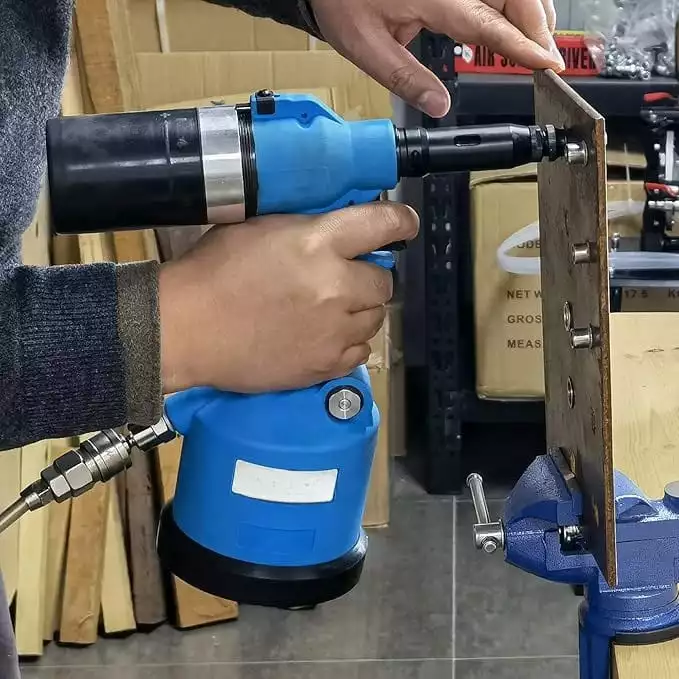
1: Prepare the Tools and Materials
- Choose the appropriate rivet nut tool (manual, pneumatic, electric, or hydraulic).
- Select the right rivet nut based on the material (round, knurled, hexagonal, etc.).
- Use the correct drill bit size to ensure the hole is neither too large nor too small.
- Optional tools: Deburring tool (to remove burrs from the hole edges for improved installation accuracy).
2: Drilling the Hole
- Refer to the rivet nut specification table to ensure the hole diameter is correct. For example:
- 1/4-20 rivet nut → 0.357″–0.362″ (9.07mm–9.19mm)
- M6 rivet nut → 9.0mm–9.2mm
- When drilling metal, use a low-speed drill bit to minimize heat and material deformation.
- For plastic or composite materials, use a step drill to avoid cracks.
- Use a deburring tool or sandpaper to smooth the edges of the hole for better rivet nut fit.
3: Inserting the Rivet Nut
- Insert the rivet nut onto the mandrel or screw of the rivet nut tool.
- Ensure the threads are properly engaged to avoid stripping.
- Insert the rivet nut into the drilled hole, keeping it vertical to prevent misalignment, which could affect the expansion and fixation.
4: Setting the Rivet Nut
- Operate the tool according to its type:
- Manual tool: Grip the handles and tighten with force until the rivet nut fully expands.
- Pneumatic/Electric tool: Set the appropriate torque, press the start button, and the tool will automatically pull the rivet.
- Hydraulic tool: Suitable for large-sized rivet nuts, operate carefully to prevent material deformation.
- Observe whether the rivet nut is completely flush with the surface of the base material without any gaps.
- If the rivet nut doesn’t expand properly during the setting process, you may need to adjust the hole size or switch to a different rivet nut size.
5: Remove the Tool & Check the Installation
- Loosen the rivet nut tool by rotating it counterclockwise and remove it from the rivet nut.
- Visually inspect to ensure the rivet nut is flush with the base material without any tilting or bulging.
- Insert a bolt into the rivet nut to ensure the threads are smooth and not obstructed, indicating a successful installation.
- For high-load applications, apply some pull force to check whether the rivet nut loosens.
Precautions
- Prevent Base Material Damage: When installing on soft materials (like plastic or aluminum), use washers to distribute pressure and prevent damage.
- Batch Installation Optimization: For high-volume rivet nut applications, consider using pneumatic or electric tools to improve efficiency.
- Special Material Considerations:
- Thin metal sheets: Choose knurled rivet nuts to prevent rotation.
- Soft plastics: Choose Jack Nuts to avoid material cracking during installation.
Do You Have Any Questions?
Let Us Solve Your Problem
FAQs
Rivet Nut Rotation or Loosening: Possible Causes and Fixes?
- Hole Diameter Too Large: The hole diameter for rivet nuts should be selected based on the specifications. For example, the standard hole diameter for a 1/4-20 rivet nut is 0.357″–0.362″ (9.07mm–9.19mm). If the hole is too large, the rivet nut will not provide sufficient friction to secure it. It is recommended to use the appropriate drill bit to ensure the hole diameter matches the rivet nut specifications.
- Insufficient Clamping Force: If the rivet nut is not securely fixed, it may be due to insufficient pressure from the tool. For pneumatic or electric tools, the torque typically needs to be adjusted to 30-40 N·m to ensure the rivet nut fully expands and secures.
Rivet Nut Not Fully Fixed: Possible Tool Pressure Issues and Adjustments?
- Check the Tool Type: For small-batch installations, it is recommended to use a manual rivet nut tool. If using pneumatic or electric tools, ensure that the pressure settings are appropriate. Pneumatic tools usually require a pressure range of 6-8 bar to provide consistent and sufficient pulling force.
- Adjust the Pressure Settings: Pneumatic and electric tools often have pressure adjustment mechanisms. Setting the proper pressure range is key to ensuring that the rivet nut fully expands. For a 1/4-20 rivet nut, the pulling force of the tool should typically reach 1000-1500 N.
- Use the Correct Tool Model: Ensure that the tool you are using matches the size of the rivet nut. Using a tool that is too large or too small can result in insecure installation.
Base Material Damage or Cracking: Likely Drilling Issues and How to Avoid?
- Choose the Right Drilling Tools and Speed: When drilling hard metals (such as stainless steel or aluminum alloys), use a slower drilling speed (around 200-300 rpm) and high-quality drill bits to reduce friction. For soft plastics (such as ABS or PVC), use a specialized step drill to avoid excessive heat or pressure.
- Control Drilling Pressure: Excessive drilling pressure can cause base material deformation or cracking. It is generally recommended to use a drilling torque of 5-8 N·m, especially on thinner base materials (like plastics).
- Deburring Process: After drilling, burrs should be removed depending on the material. Use a deburring tool to clean the hole edges. Burrs increase friction during installation and can affect the rivet nut’s fixation. It is recommended to ensure the hole edges are smooth within a tolerance of ≤0.1mm.
Why Choose Rivetfix
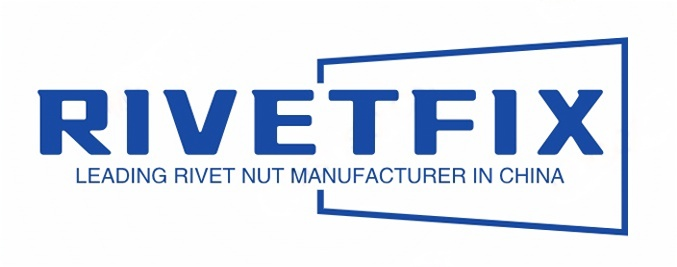
As a leading fastener manufacturer in China with more than 15 years in the industry, Rivetfix are committed to providing first-class quality fasteners and responsive services to the world.
Rivetfix offers a wide range of rivet nuts designed to meet the unique demands of your projects. With options like countersunk, flat, and hex heads, as well as knurled and round body types, Rivetfix ensures you have the right solution for every application. Choose Rivetfix for versatile, cost-effective, and durable fastening solutions tailored to your specific needs. In addition, we can also provide customized rivet nuts service according to your requirements.
Contact us for project advice and the latest rivet nut quote!
Get High Quality Rivet Nuts Quote!
Send Your Rivet Nut Request
For more than 20 years, Rivetfix has helped customers solve many rivet nuts sourcing needs and technical challenges.
Have a question? Contact us and we’ll provide you with the perfect solution.