Clinch Nut vs Weld Nut: What is the Difference?
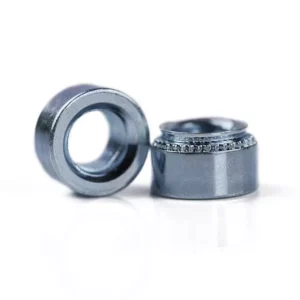
Leading Self-Clinching Fasteners Manufacturer and Supplier in China
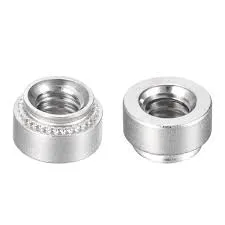
When selecting the right type of fastening solution for your project, understanding the difference between a clinch nut vs weld nut is crucial. Both are commonly used to create strong, secure threaded connections in sheet metal, but they achieve this in different ways. A clinch nut is mechanically pressed into place, providing a reliable, vibration-resistant connection without the need for heat or welding. On the other hand, a weld nut is secured through welding, making it ideal for applications requiring a permanent, high-strength bond. In this article, we’ll explore the key differences between a clinch nut vs weld nut and how to choose the best option for your needs.
Table of Contents
Self-clinching nuts are threaded fasteners that embed permanently into ductile materials like metal sheets. Developed in the mid-20th century for electronics and machinery, they addressed demand for lightweight, vibration-resistant threads in thin panels without welding. Early adoption prioritized aerospace and automotive sectors, later expanding to enclosures and industrial equipment.
Structurally, they feature a knurled or grooved base and a threaded shank. When pressed into a pre-drilled hole, tooling deforms the surrounding material, causing the base to lock into place via displaced metal. This creates a flush, load-bearing thread ideal for high-stress assemblies. Their design eliminates secondary hardware, streamlining production
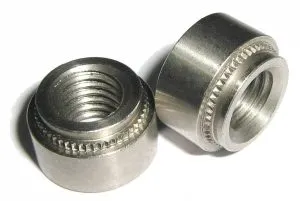
Key Features of Clinch Nuts
1. Press Directly into Thin Sheets – No Welding or Glue Needed
Self-clinching nuts work like “stamping a logo” – you press them directly into pre-drilled holes on thin sheets (metal, plastic, etc.). When pushed in, the sheet material deforms around the nut’s grooves or ridges, creating a secure “lock.” No extra screws, welding, or glue are required, making them ideal for tight spaces (e.g., inside electronics or car doors).
- Installed like a “stamp” – press and lock;
- No heat or tools that damage materials (unlike welding);
- Best for thin sheets (0.5–3mm thick).
2. Built-In Anti-Rotation – No Screw Loosening
These nuts have corners, serrated edges, or textured surfaces that “bite” into the sheet’s hole edges, preventing the nut from spinning when tightening or loosening screws. This is crucial for high-vibration environments (e.g., car engines) or frequent maintenance.
- Works like LEGO blocks – snaps in place and won’t twist;
- Perfect for cars, machinery, or anything that shakes;
- Requires precise hole sizing (too big or small reduces effectiveness).
3. Heavy-Duty Load Capacity – Holds Weight and Force
Despite their small size, self-clinching nuts spread forces across the sheet using wide bases or angled designs. This prevents the sheet from tearing under pulling or twisting forces. Made from stainless steel or hardened steel, they’re built to last.
- Acts like a wide coaster – distributes weight to avoid damage;
- Tough enough for repeated use (e.g., robot arms);
- If overloaded, the sheet might fail first, but the nut stays intact.
4. Thin-Sheet Friendly – Prevents Cracking or Warping
Regular nuts can bend thin sheets, but self-clinching nuts are specially shaped to “nudge” materials gently during installation, avoiding cracks or warping (e.g., smartphone frames). Some models add a support ring for ultra-thin sheets (<1mm).
- Works like kneading dough – spreads pressure evenly;
- Ideal for phone casings, laptop frames, or lightweight shelves;
- Requires clean, pre-drilled holes (no rough edges!).
Main Applications of Clinch Nuts
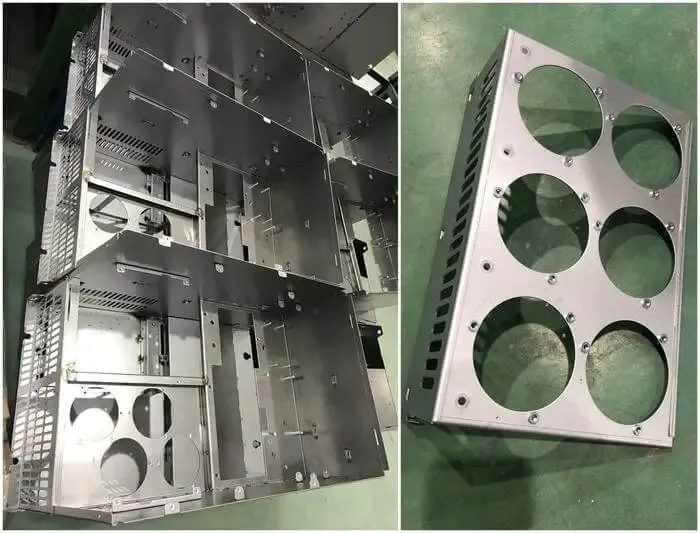
1. Electronics Enclosures and Frame Assembly
Self-clinching nuts are widely used in metal/plastic casings for smartphones, laptops, routers, and other electronics to secure screw threads. Their embedded installation saves space, hides within thin sheets, and supports ultra-slim device designs.
- Typical Use Cases:
- Fixing SIM card slots in smartphone frames;
- Mounting heat sinks in server chassis;
- Connecting display panels to stands.
- Benefits: Avoids heat damage from welding to sensitive components; provides flush and stable threaded interfaces.
2. Automotive Lightweight Components
In automotive manufacturing, self-clinching nuts replace welded nuts in thin sheet metal parts like doors, engine mounts, and control panels, reducing weight and improving assembly efficiency.
- Typical Use Cases:
- Reinforcing threaded points for door hinges;
- Attaching headlight brackets to vehicle bodies;
- Strengthening electric vehicle (EV) battery enclosures.
- Benefits: Vibration-resistant performance prevents loosening under dynamic loads; aligns with lightweight automotive designs.
3. Industrial Machinery and Automation Equipment
Self-clinching nuts are ideal for motors, robots, and production line systems, especially in high-vibration environments or scenarios requiring frequent maintenance.
- Typical Use Cases:
- Securing covers on robotic arm joints;
- Mounting ventilation grilles on motor housings;
- Connecting conveyor belt supports to frames.
- Benefits: Anti-rotation design ensures screw stability; high load capacity suits heavy-duty industrial applications.
4. Sheet Metal Structures for Appliances and Consumer Goods
In appliances (e.g., AC units, refrigerators) and metal shelving, self-clinching nuts simplify assembly and reduce reliance on secondary processes like welding.
- Typical Use Cases:
- Installing protective grilles on AC outdoor units;
- Joining crossbeams in metal storage racks;
- Fastening panels on kitchen appliances.
- Benefits: Single-sided installation saves time and labor; eliminates weld marks or rivet-induced surface flaws.
Core Value Summary of Clinch Nuts
- Space-saving: Ideal for compact designs;
- Vibration resistance and durability: Long-lasting threads in dynamic environments;
- Cost-effective: Reduces welding/riveting complexity;
- Lightweight compatibility: Perfect for modern thin-sheet material requirements.
What Are Weld Nuts?
Weld nuts are specialized threaded fasteners permanently bonded to metal surfaces through welding. They feature a base with a flange or raised projections (for “projection welding”) that concentrate heat during welding, ensuring a secure bond. Typically made from carbon steel, stainless steel, or aluminum, they create durable threaded anchors in sheet metal, frames, or structural components, commonly used in automotive, machinery, and construction.
Unlike removable fasteners, weld nuts provide high strength and vibration resistance, ideal for heavy-load or high-temperature environments. Installation requires welding equipment (e.g., spot or arc welders) and precise alignment to avoid distortion.
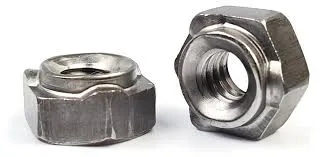
Key Features of Weld Nuts
1. Welding-Specific Structural Design
Weld nuts are optimized for welding through flanges, projections, or circular bumps. For example, projection weld nuts feature raised circular bumps on their base that concentrate electrical current during welding, rapidly melting the metal to form strong fusion bonds with the base material. Flanged weld nuts increase contact area to prevent post-weld misalignment.
- Bump height: 0.5–1.5mm; quantity and arrangement depend on base material thickness (e.g., 3-4 bumps for 2mm steel plates).
- Flange diameter: Typically 1.5–2 times the nut’s outer diameter for stable positioning.
- Compatible with resistance welding (spot/projection) or arc welding processes.
2. Material Versatility and Surface Treatments
Weld nuts are made from low-carbon steel, stainless steel, or aluminum, chosen to match the base material and prevent galvanic corrosion. Surface treatments like zinc plating, nickel coating, or phosphating enhance corrosion resistance. High-end models may use Dacromet coating, which withstands 800+ hours of salt spray testing. Stainless steel nuts (e.g., SUS304/316) are ideal for humid or chemical environments.
- Low-carbon steel hardness: HRB 70–100; cost-effective but requires anti-rust coatings.
- Aluminum nuts: Require specialized equipment (e.g., AC spot welders) for aluminum sheet welding.
- Coating thickness: Typically 5–15μm (e.g., zinc plating ≥8μm).
3. High Strength and Permanent Bonding
Welding creates a metallurgical bond, achieving tensile strength up to 80% of the base material (e.g., ≥400MPa for nuts welded to Q235 steel plates). Weld nuts excel in high-vibration, shock, and thermal environments, outperforming adhesives or mechanical fasteners. Used in automotive chassis, crane structures, and other demanding applications.
- Thread longevity under dynamic loads: 3-5 times higher than self-tapping nuts.
- Compliance with standards: ISO 13918 or AWS D1.1 for weld quality.
- Controlled hardness in the heat-affected zone (HAZ ≤300 HV to prevent brittleness).
4. Process Dependency and Limitations
Weld nuts require specialized equipment and skilled operation. Resistance welding demands precise parameters: current (5-10kA), pressure (200-600N), and duration (0.1–0.5 seconds). Compatible only with weldable metals (steel, stainless steel) and unsuitable for plastics or wood. Minimum base material thickness: ≥1mm (thinner sheets risk burn-through). Pre-weld surface cleaning (oil/oxide removal) is critical.
- Welding defects (e.g., cold welds, overheating) may cause thread failure.
- Pre-coated materials (e.g., pre-painted steel) require post-weld coating repair.
- Irreversible installation; removal requires destructive cutting.
Main Applications of Weld Nuts
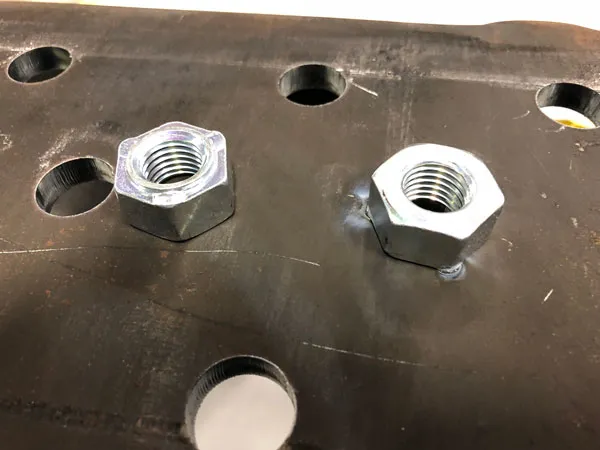
1. Automotive and Transportation
Weld nuts are widely used in vehicle frames, chassis components, and engine mounts:
- Frame rails: Provide high-strength threaded anchors for suspension bolts;
- Exhaust system fastening: High-temperature stainless steel nuts (e.g., SUS310) withstand thermal cycling;
- EV battery enclosure reinforcement: Securely fasten battery packs against vibration.
- Advantage: 3x higher fatigue resistance than self-tapping nuts, meeting automotive dynamic load standards.
2. Heavy Machinery and Industrial Equipment
Essential for load-bearing joints in excavators, mining rigs, and hydraulic systems:
- Excavator boom joints: Reinforce pivot bolt threads to handle shear forces;
- Pressure vessel flanges: Maintain sealing under extreme heat and pressure;
- Conveyor brackets: Distribute stress through multi-point welding.
- Advantage: Withstand axial pull-out forces ≥600MPa, outperforming rivets or adhesives.
3. Construction and Infrastructure
Replace traditional embedments in steel structures, bridges, and transmission towers:
- Steel beam connectors: Pre-welded nuts accelerate on-site assembly;
- Elevator rail mounts: Flanged nuts simplify vertical alignment;
- Solar panel frames: Aluminum nuts resist corrosion in outdoor setups.
- Advantage: Reduce on-site welding risks, ideal for prefabricated construction.
4. Energy and Shipbuilding
Critical for offshore platforms, ship engines, and nuclear power systems:
- Ship deck fastening: Marine-grade stainless steel (316L) nuts resist saltwater corrosion;
- Reactor support frames: Nuclear-grade welds comply with RCC-M standards;
- Wind turbine towers: Large-flange nuts dissipate tower dynamic stresses.
- Advantage: ISO 5817-certified weld quality ensures 20+ years of service life.
Core Value Summary of Weld Nuts
- Permanent high-strength fixation
- Extreme environment resistance
- Simplified assembly
- Heavy-duty compatibility
Do You Have Any Questions?
Let Us Solve Your Problem
What's the Difference - Clinch Nut vs Weld Nut
Form: Clinch Nut vs. Weld Nut – Comparison
Category | Clinch Nut | Weld Nut |
Installation | Press-fit (cold forming); no heat | Welded (resistance/arc); heat required |
Material | Thin sheets (0.5–3mm; Al, steel, SS) | Thick metals (steel/SS, ≥1mm); excludes plastics |
Strength | Moderate (~300MPa pull-out) | High (matches base metal, up to ~600MPa) |
Process | Simple press tools; no surface prep | Welding equipment/skills; surface prep needed |
Cost | Low per unit, bulk-friendly | High setup/energy costs |
Removability | Destructive (damages sheet) | Destructive (grinding/cutting) |
Corrosion | Requires coating (e.g., zinc) | Material compatibility critical |
Vibration | Good | Excellent (metallurgical bond) |
1. Installation
- Clinch Nut:
Installed via cold-forming press without heat. A hydraulic or pneumatic press forces the nut into a pre-punched hole in the sheet metal. The nut’s serrated base or knurls plastically deforms the surrounding material, creating a mechanical interlock.
Key steps: Punch hole → Align nut → Apply pressure (5–20 tons).
Tools: Clinching press or CNC punch machine. - Weld Nut:
Requires heat-based welding (resistance/arc/MIG). The nut’s projections or flange concentrate heat to fuse it to the base metal.
Key steps: Clean surface → Align nut → Apply current/pressure (e.g., 8kA for 0.3s).
Tools: Spot welder, electrode fixtures.
2. Material Compatibility
Clinch Nut:
Limitations: Brittle materials (e.g., hardened steel) may crack during pressing.
Ideal for: Thin, ductile metals (0.5–3mm) like aluminum, mild steel, or stainless steel.Weld Nut:
Ideal for: Thicker metals (≥1mm steel/stainless steel) with weldability.
Limitations: Non-weldable materials (e.g., magnesium, coated steels) require special techniques.
3. Strength
Clinch Nut:
Pull-out strength: Typically 200–300MPa, limited by sheet metal thickness and ductility.
Shear strength: Moderate, suitable for static loads (e.g., enclosures).Weld Nut:
Pull-out strength: Matches base metal (e.g., 400–600MPa for steel), as welding creates a metallurgical bond.
Shear strength: Excellent for dynamic loads (e.g., vehicle suspension).
4. Process Requirements
Clinch Nut:
Speed: Fast (1–2 seconds per nut), ideal for high-volume production.
Skill level: Minimal training; no surface cleaning needed.
Cost: Low per-unit cost, but limited to thin sheets.Weld Nut:
Speed: Slower (3–10 seconds per nut due to setup/cooldown).
Skill level: Requires certified welders to avoid defects (e.g., porosity, spatter).
Cost: Higher energy/equipment costs, but versatile for heavy-duty use.
5. Vibration Resistance
- Clinch Nut:
Performance: Relies on mechanical friction; may loosen under prolonged vibration.
Mitigation: Adhesives or thread-locking compounds can enhance retention. - Weld Nut:
Performance: Permanent metallurgical bond prevents loosening, even in extreme vibration (e.g., aircraft engines).
Testing: Often validated via ISO 16156 vibration endurance tests.
Clinch Nut vs Weld Nut : How to Choose the Right Type
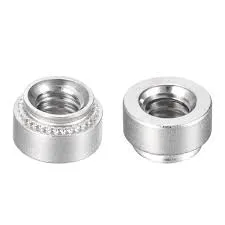
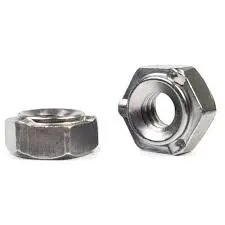
Choose Clinch Nut When:
1. Thin Materials
- Base material thickness: 0.5–3mm (e.g., aluminum sheets, thin stainless steel).
- Avoids heat-induced warping or burn-through.
2. Speed & Cost Efficiency
- High-volume production (e.g., automotive stamping lines, appliances).
- Minimal equipment: Requires only a press, no welding setup.
3. Light to Moderate Loads
- Static applications (e.g., enclosures, brackets, HVAC ducts).
- Pull-out strength ≤300MPa.
4. Non-Harsh Environments
- Indoor or dry conditions (corrosion risk managed via zinc plating).
5. No Post-Processing
- Avoids weld spatter cleanup or surface refinishing.
Choose Weld Nut When:
1. Thick or Heavy-Duty Materials
- Base material thickness: ≥1mm steel/stainless steel.
- Handles high heat input without distortion.
2. Extreme Load & Vibration
- Dynamic applications (e.g., chassis, cranes, shipbuilding).
- Tensile strength matches base metal (e.g., 400–600MPa).
3. Harsh Environments
- Corrosive (marine, chemical) or high-temperature conditions.
- Use stainless steel (316L) or corrosion-matched materials.
4. Permanent, Irreversible Fixation
- Critical structural joints requiring metallurgical bonding.
5. Custom or Low-Volume Production
- Repairs, prototypes, or specialized equipment with welding capabilities.
Do You Have Any Questions?
Let Us Solve Your Problem
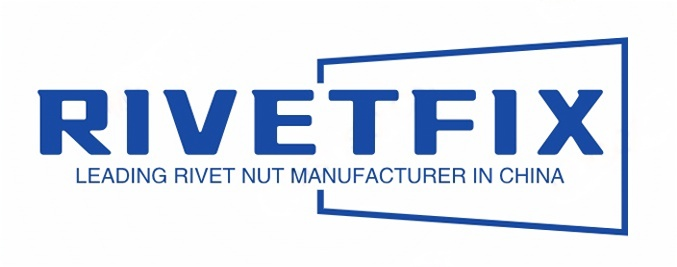
As a leading fastener manufacturer in China with more than 15 years in the industry, Rivetfix are committed to providing first-class quality fasteners and responsive services to the world.
Our wide selection of self clinching series allows you to find the perfect solution for your project. Trust Rivetfix for superior service, high-performance products, and expert advice tailored to your fastening needs. We can select the most suitable fasteners according to your project needs, and provide product customization services.
Contact us for project advice and the latest clinch nut quote!
Get High Quality Clinch Nuts Quote!
1. Thin Materials
Send Your Rivet Nut Request
For more than 20 years, Rivetfix has helped customers solve many rivet nuts sourcing needs and technical challenges.
Have a question? Contact us and we’ll provide you with the perfect solution.