Why Use Rivet Nuts: Strong, Reliable Fastening Solutions
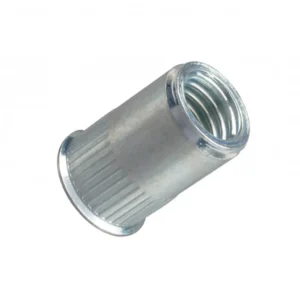
Leading Rivet Nut Manufacturer and Supplier in China
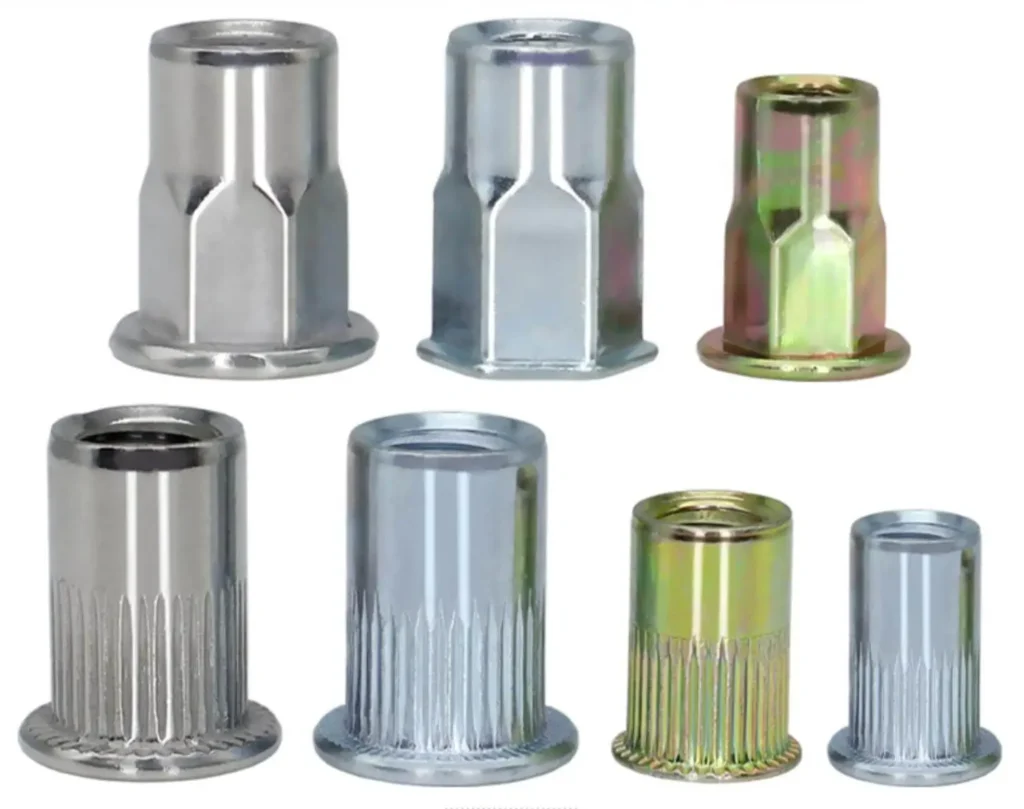
When it comes to creating strong, secure, and reliable connections in materials that are thin or difficult to work with, why use rivet nuts becomes a critical question. These versatile fastening solutions offer a range of benefits over traditional methods, providing superior strength, vibration resistance, and ease of installation. Rivet nuts can transform your assembly process, ensuring durability and long-lasting performance. In this blog, we’ll explore the many reasons why rivet nuts are the go-to solution for a variety of industries, from automotive to electronics and beyond.
Table of Contents
What Are Rivet Nuts and How Do They Work?

Rivet nuts, also known as blind rivet nuts or rivnuts, are specialized fasteners designed to provide strong internal threads in materials where tapping is impractical—such as thin sheets, tubes, or blind holes. A rivet nut typically consists of a hollow, internally threaded metal body. The head can come in different styles such as flat head, countersunk, or flange head, while the shank may be round, hexagonal, or knurled to suit various installation needs.
These fasteners are ideal for “blind” installations, where access is available from only one side. This makes them especially suitable for applications with limited space or enclosed structures.
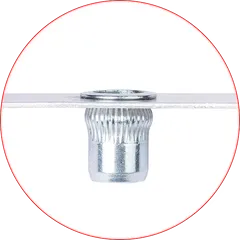
The working principle of a rivet nut relies on controlled deformation during installation. First, a hole (either round or hexagonal) is pre-drilled in the base material. The rivet nut is then inserted into the hole. Using a special installation tool—such as a rivet nut gun—the internal mandrel is pulled, causing the rear portion of the rivet nut to expand and deform plastically, creating a bulge that firmly grips the base material.
Once the riveting process is complete, the rivet nut becomes permanently fixed to the base material, forming a durable, threaded anchor point. Screws or bolts can then be threaded into the rivet nut, providing a reliable connection with excellent tensile strength and resistance to rotation—ideal for various structural and load-bearing applications.
Why Use Rivet Nuts Instead of Traditional Fasteners?
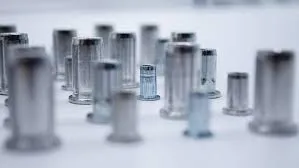
1. Reliable Internal Threading in Thin-Wall Materials
In many lightweight structural designs—such as sheet metal, hollow tubes, or composite assemblies—traditional threading methods (like tapping or welding nuts) are often impractical due to limited material thickness or complex geometry. Rivet nuts overcome this limitation by using a deformation-based installation method that allows secure thread formation in materials as thin as 0.5mm or less. This eliminates the need for extra machining, tapping, or backside welding, simplifying the assembly process and reducing labor and equipment costs—especially beneficial for high-volume, efficiency-driven manufacturing.
2. Ideal for Blind-Side Installation
One of the greatest advantages of rivet nuts is their ability to be installed from only one accessible side, also known as blind installation. This is critical in structures where the backside is inaccessible—such as the closed end of hollow profiles, the inside of electrical enclosures, or within confined equipment compartments. Rivet nuts enable workers to complete fastening from a single side, significantly simplifying workflows, increasing installation flexibility, and improving both efficiency and safety in tight spaces.
3. Material Flexibility for Various Environmental Demands
Rivet nuts are available in a variety of materials to meet the physical and chemical demands of different environments. This versatility allows them to maintain excellent performance in extreme temperatures, outdoor applications, clean rooms, and corrosive conditions.
- Carbon Steel: High strength and cost-effective, suitable for indoor or general industrial use where corrosion resistance is not a concern.
- Stainless Steel (304 / 316): Outstanding rust and corrosion resistance, ideal for damp, marine, or chemically aggressive environments, such as power generation or petrochemical industries.
- Aluminum Alloy: Lightweight with good corrosion resistance, commonly used where weight or electrical conductivity is a concern, such as in electronics, aerospace parts, and instrumentation.
4. High Structural Strength and Vibration Resistance
Compared to conventional screw or bolt fastening, rivet nuts form a mechanically locked structure by deforming behind the base material during installation. This creates a strong clamping force with excellent tensile, shear, and anti-rotation performance. Even under high loads or long-term vibrations, the connection remains stable. Rivet nuts are widely used in automotive chassis, railway vehicles, elevator tracks, and heavy-duty equipment, where high-strength, vibration-resistant fastening is essential.
5. Reusability and Easy Maintenance
Once installed, rivet nuts provide a permanent threaded anchor point that allows for repeated screw-in and removal without damaging the base material or threads. Compared to welded nuts, which require re-welding if damaged or misaligned, rivet nuts offer faster replacement and easier maintenance—making them ideal for serviceable applications such as control panels, removable covers, and access doors.
6. Wide Range of Applications
Rivet nuts are highly adaptable and work with a wide range of materials, including metals, plastics, fiberglass, and composites. Their application spans across nearly all sectors of manufacturing and assembly, including but not limited to:
- Mechanical Assemblies: For connecting frames, brackets, bases, control panels, and more.
- Household Appliance Enclosures: Used in internal structures of washing machines, ovens, air conditioners, and microwaves.
- Industrial Automation Equipment: Including PLC cabinets, electrical component panels, and cabinet doors.
- Sheet Metal Chassis and Control Cabinets: Essential for IT enclosures, power systems, and telecom housing.
- Railway and Automotive Manufacturing: Applied to body attachments, seat tracks, and maintenance hatches.
- Renewable Energy and Solar Mounting Systems: Providing reliable threaded connections in wind and solar energy structures.
Summary: Why Use Rivet Nuts
Advantage | Rivet Nuts | Traditional Fasteners (Welded Nuts / Tapping) |
Material Thickness Compatibility | Suitable for thin sheets/tubes | Requires thick material |
Installation Method | Blind-side, single-side installation | Often requires access to both sides |
Processing Requirements | No welding or tapping needed | Complex processing, heat-affected zones |
Connection Strength | High tensile and anti-rotation performance | Prone to loosening under vibration |
Maintenance and Removal | Reusable and easy to service | Difficult to remove or replace |
Application Versatility | Widely applicable across industries | More limitations |
Do You Have Any Questions?
Let Us Solve Your Problem
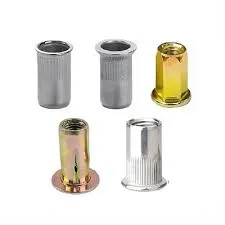
In practical applications, one type of rivet nut does not fit all. Different structural designs, base materials, and usage environments require variations in rivet nut types, head styles, and thread sizes. Below is a detailed breakdown of the key selection factors to help you choose the right model—ensuring optimal connection strength and installation efficiency.
1. Round, Knurled, or Hex Body: Which Offers Better Anti-Rotation Performance?
Body Type | Characteristics | Anti-Rotation Performance | Typical Applications |
Round Body | Smooth exterior, general-purpose | ★☆☆☆☆ | Standard loads, non-vibrating assemblies |
Knurled Body | Textured surface for increased friction | ★★★☆☆ | Softer materials, light to medium loads |
Hex Body | Hexagonal shape fits into hex hole | ★★★★★ | High-torque applications, anti-loosening required |
2. Flange Head Types
Flange Type | Features | Recommended Applications |
Flat Head | Slightly protrudes after installation; standard type | Where surface flushness isn’t critical; general mechanical structures |
Reduced Head | Compact head profile | Lightweight applications; space-constrained environments |
Countersunk Head | Sits flush within material | Aesthetic or decorative components with high surface requirements |
Thread Size | Recommended Applications |
M4 | Small electronics enclosures, instruments, appliance panels |
M5 | General electronics, lightweight structural components |
M6 | Appliance mounting, light-to-medium mechanical structures |
M8 | Medium-load industrial components, equipment brackets |
M10–M12 | Heavy machinery, automotive chassis, high-torque assemblies |
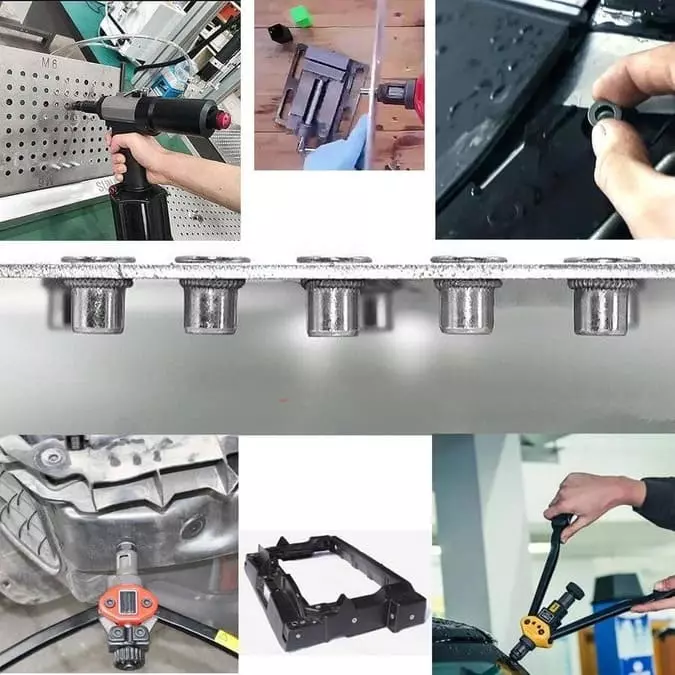
1. Automotive Manufacturing
In modern automotive production, rivet nuts are widely used for internal threading in lightweight structures such as aluminum and thin steel sheets. Compared to traditional welding, rivet nuts enable faster installation without compromising the base material—making them ideal for blind holes and post-assembly installations.
Advantages: Quick installation, reliable anti-rotation, no impact on surface treatments (e.g., painting).
- Dashboard bracket mounting
- Seat rail and reinforcement plate connections
- Fastening of bumper brackets, tailgate motors, and other accessories
2. Electrical Cabinets and Control Panels
In electrical cabinets, power distribution units, and industrial control systems, rivet nuts provide reliable threaded connections on sheet metal panels. They allow screws to be removed and reinstalled repeatedly, ensuring convenient maintenance.
Advantages: Blind-side installation, efficient assembly, easy for future servicing.
- Mounting holes for control panels
- Terminal block fixation
- Screws for distribution box covers
3. Appliance Housings
Rivet nuts are particularly suitable for the metal housings and frame structures of appliances such as air conditioners, washing machines, and refrigerators. They enable high-speed, high-efficiency installation on production lines.
Advantages: Suitable for thin sheets, mass production, no thermal effect on materials.
- Wall-mounted AC bracket connections
- Washing machine housing and support frame attachment
- Mounting control boards or door hinges in refrigerators
4. Rail Transit and Elevators
For high-vibration and high-strength structural applications—such as trains, subways, and elevators—rivet nuts provide durable and stable internal threads, able to withstand frequent operation and mechanical stress.
Advantages: Vibration resistance, secure fastening, compatible with steel or aluminum profiles.
- Elevator rail connection components
- Carriage door frames and trim panel fastening
- Signal box and electrical module bracket installation
5. Industrial Equipment Assembly
In the manufacturing of industrial automation equipment, machinery structures, robotics, and electrical enclosures, rivet nuts offer fast and strong fastening across various base materials, including stainless steel, coated steel, and composite plastic panels.
Advantages: Supports diverse base materials, corrosion resistance, durability, customizable solutions.
- Mounting holes for automation production lines
- Sheet metal housings for industrial robots
- Electrical cabinet and mechanical bracket assemblies
Do You Have Any Questions?
Let Us Solve Your Problem
Contact Us for High-Quality Rivet Nut Solutions
If you’re looking for reliable and durable rivet nuts suitable for a wide range of working conditions, we offer professional selection guidance and customization services. Whether your focus is on thread specifications, material performance, corrosion resistance, installation efficiency, or cost control, we can recommend the most suitable product models and installation solutions based on your project requirements.
We are committed to providing high-quality fastening solutions across various industries, including machinery manufacturing, automotive, electronics, rail transit, sheet metal fabrication, and new energy systems. Our technical team can assist you with:
- Fast model selection and product specification confirmation
- Sample support for testing
- Bulk purchasing, OEM customization, and logistics coordination
- Assistance with installation and product-related inquiries
Buy Rivet Nuts from Rivetfix
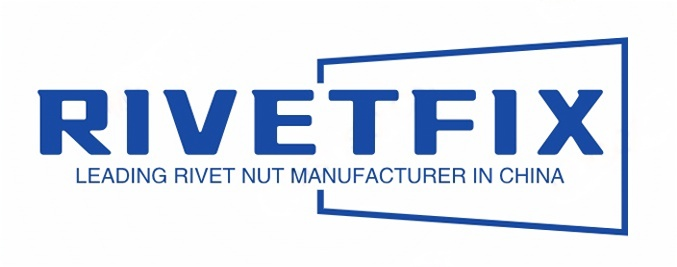
As a leading fastener manufacturer in China with more than 15 years in the industry, Rivetfix are committed to providing first-class quality fasteners and responsive services to the world. We offers a wide range of rivet nuts and clinch nuts designed to meet the unique demands of your projects. Rivetfix ensures you have the right solution for every application. Choose Rivetfix for versatile, cost-effective, and durable fastening solutions tailored to your specific needs. In addition, we can also provide customized rivet nuts service and clinch nuts according to your requirements.
Contact us now for more information and customization options on Rivet Nuts!
Get High Quality Rivet Nuts Quote!
Send Your Rivet Nut Request
For more than 20 years, Rivetfix has helped customers solve many rivet nuts sourcing needs and technical challenges.
Have a question? Contact us and we’ll provide you with the perfect solution.