Why & How : Using PEM Studs for Aluminum
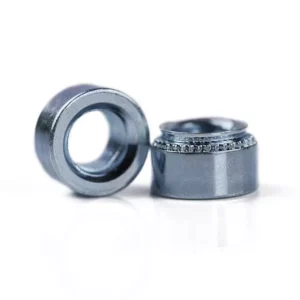
Leading Self-Clinching Fasteners Manufacturer and Supplier in China
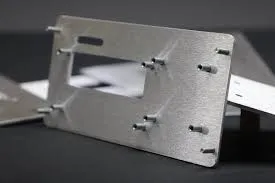
PEM studs for aluminum provide strong, reliable threaded connections in lightweight metal applications. They eliminate the need for welding, reduce assembly time, and ensure a secure fit. This guide explores why PEM studs are ideal for aluminum structures and how to install them correctly to maximize performance and durability.
Table of Contents
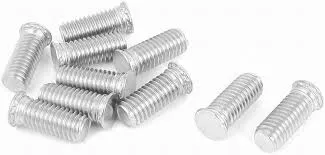
PEM Studs are permanent mechanical fasteners designed specifically for thin sheet materials. They are embedded into materials like aluminum alloy, stainless steel, or coated steel through a precise cold-forming process. The core principle is pressure-triggered plastic deformation.
Made from materials such as steel, stainless steel, or aluminum, PEM Studs resemble small posts (or “studs”), with one end featuring external threads and the other end having a round, flat, or other specific head designs.
Features & Benefits
- Efficient Fastening:
- Installed in a single step (1-3 seconds per unit), increasing efficiency by 70% compared to traditional welding.
- Provides threaded bearing surfaces (e.g., metric threads M3-M12), making them suitable for attaching panels, wiring harnesses, brackets, and other components.
- Mechanical Performance:
- High tensile strength (up to 22kN/m²) and torque resistance (e.g., 6Nm at M6), ensuring stability in vibration-prone environments.
- Aluminum-specific models resist galvanic corrosion (electrolytic corrosion).
- No Backside Operation:
- With its one-sided installation feature, PEM Studs are ideal for closed cavities (such as electronic device enclosures and vehicle body structures).
Applications (Focusing on Aluminum Applications)
Industry | Typical Application | Advantages |
New Energy Vehicles | Battery trays / Electronic control boxes | 15% weight reduction, avoids heat-affected zones (HAZ) from welding |
Consumer Electronics | Aluminum middle frames of phones/laptops | Reliable fastening for aluminum sheets as thin as 0.8mm |
Industrial Equipment | Connecting aluminum heat exchangers and cabinets | Vibration resistance, accommodates thermal expansion and contraction |
Advantages
- Saves Time and Costs: The installation process is simple and fast, reducing the complex steps of traditional thread cutting and welding.
- Suitable for Thin Materials: PEM Studs provide strong fixation for thin sheets without damaging the base material.
- High Strength and Reliability: They offer long-lasting connection strength, ensuring stable operation over time and reducing maintenance needs.
Why: Five Key Reasons to Use PEM Studs for Aluminum
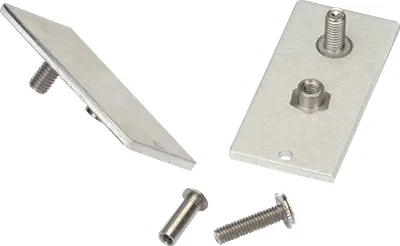
1. Lightweight Design
PEM Studs are about 50% lighter than traditional bolts. In applications where lightweight design is crucial, particularly in industries such as automotive and aerospace, using PEM Studs can significantly reduce overall weight.
2. Corrosion Resistance
When aluminum (anode) comes into contact with ordinary steel fasteners (cathode), galvanic corrosion can occur in humid environments, leading to structural failure. PEM Studs, made from 300 series stainless steel or passivated carbon steel, combined with surface coatings (such as zinc-nickel alloy), offer excellent corrosion resistance, especially in high-humidity and high-salinity environments.
Form:Salt Spray Test Performance
Combination | Corrosion Time (ASTM B117) |
---|---|
Aluminum Plate + Ordinary Carbon Steel Bolt | 240 hours |
Aluminum Plate + Coated PEM Studs | 1000 hours |
According to the salt spray test (ASTM B117), PEM Studs made of stainless steel outperform traditional welds and bolts in aluminum applications. Even in marine environments or exposure to chemicals, PEM Studs maintain long-term stability and reduce maintenance costs.
3. No Secondary Processing Required
Compared to traditional thread cutting or welding methods, PEM Studs are installed directly onto aluminum using press-fit technology, eliminating the need for secondary processing such as drilling and tapping. This results in a 40% savings in assembly costs. Here’s a cost comparison between using PEM Studs and traditional threading methods:
Process | Traditional Bolt Solution | PEM Studs Solution |
Drilling | Required (±0.05mm precision) | Not needed |
Tapping/Welding | Required (15 seconds per hole) | Not needed |
Fastener Installation | Manual tightening (20 seconds) | Hydraulic press-fit (3 seconds) |
4. High Strength Load Capacity
PEM Studs offer exceptionally high tensile strength and shear capacity. Compared to traditional welded studs, PEM Studs provide a more secure connection on aluminum and can withstand higher loads. In various experiments, PEM Studs consistently outperform traditional welded studs in tensile and shear strength.
Form:Mechanical Test Data (for 2mm thick 5052 aluminum alloy plates)
Metric | M6 Welded Stud | PEM Studs (FH type) |
Tensile Strength (kN) | 4.2 | 12.8 |
Shear Strength (kN) | 3.1 | 9.5 |
Fatigue Life (cycles at 10Hz) | 50,000 | 200,000+ |
5. Consistency Assurance
Using PEM Studs eliminates human welding errors, improving production line consistency. In drone production, adopting PEM Studs increased the production yield from 78% to 95%. This consistency not only enhances product reliability but also reduces rework and maintenance costs caused by welding errors.
Additionally, PEM Studs reduce quality fluctuations due to equipment aging or operational issues, further enhancing overall production efficiency.
Summary
PEM Studs are not just an “upgrade” to fasteners but a redefinition of the technical-economic balance in aluminum assembly: achieving a breakthrough in lightweight design, corrosion resistance, and cost reduction under the same load, making them especially suitable for electrification, precision, and high-reliability applications.
How: Installation Guide for PEM Studs on Aluminum
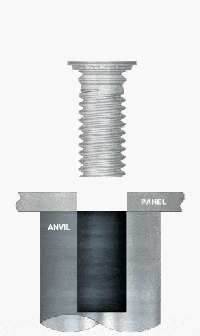
1. Equipment Selection
It is generally recommended to use a 2-4 ton hydraulic press for press-fit installation. The pressure range should be adjusted according to the thickness and hardness of the aluminum material to ensure proper installation. It is advisable to use matching molds to ensure the correct insertion of PEM Studs, preventing material damage. Below are the recommended equipment parameters:
- Pressure Range: 2-4 tons
- Hydraulic Press Type: Adjustable pressure hydraulic press
- Mold Type: PEM Studs-specific mold
- Mold Matching Diagram: Ensure the mold dimensions match the Studs and aluminum to achieve optimal installation results.
2. Step-by-Step Installation Steps
1. Hole Positioning
Ensure that the installation hole on the aluminum is at the specified location, and the hole diameter tolerance should be strictly controlled within ±0.05mm. Accurate hole diameter is crucial for the proper installation of PEM Studs. If the hole is too large or too small, it may result in an insecure connection.
2. Pre-loading the Studs
During installation, first place the PEM Studs into the preset hole and ensure they are in full contact with the hole walls. Check that the PEM Studs are free from defects and that their shape is intact.
3. Press-fit Pressure Monitoring
During the press-fit process, avoid applying excessive pressure that could deform the aluminum material. It is recommended to use pressure monitoring equipment to track the pressure in real-time, ensuring it remains within the recommended range. Overpressure may cause aluminum deformation or incomplete insertion of the PEM Studs.
3. Inspection Standards
To ensure the reliability of PEM Stud installation quality, necessary quality checks must be performed.
- Visual Inspection: After installation, first perform a visual check to ensure that the base of the PEM Studs is tightly fitted against the aluminum surface, with no gaps.
- Tensile Testing: It is recommended to sample 5% of the PEM Studs for tensile testing per batch. Use standard tensile testing equipment to verify the connection strength, ensuring that each PEM Stud can withstand the expected load. For example, M5 Studs ≥ 2.5kN, M8 ≥ 6.8kN.
4. Failure Case Analysis
In the actual installation process, several common failure cases may occur. Understanding these issues and applying corrective measures can improve installation success rates.
- Hole Position Deviation Leading to Loosening: If hole position deviation prevents proper installation of PEM Studs, it may cause loosening. Solution: Use an expansion sleeve to fix the problem by enlarging the hole by +0.1mm and adding the sleeve to ensure that PEM Studs are securely held in place.
Do You Have Any Questions?
Let Us Solve Your Problem
Benefits of Using PEM Studs for Aluminum
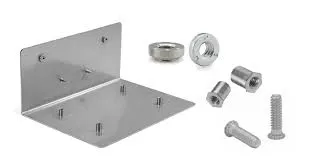
Increased Production Efficiency:
- Using PEM Studs eliminates complex machining steps such as thread cutting or welding.
- It has a shorter installation cycle, making it suitable for mass production.
Enhanced Connection Reliability:
Provides high-strength connections, avoiding the structural weaknesses associated with welding and threaded connections.
Form:Mechanical Performance Comparison (based on tests with 6061-T6 aluminum alloy plate):
Property | Welded Studs | Self-Tapping Screws | PEM Studs |
Tensile Strength | 4.5kN (prone to breakage) | 3.8kN (stripping) | 12.8kN |
Shear Strength | 3.2kN | 2.6kN | 9.5kN |
Vibration Test | Cracks after 50,000 cycles | Loosens after 30,000 cycles | No failure after 200,000 cycles |
Test Conditions: SAE J1455 Standard, 10Hz Frequency, ±1.5mm Amplitude |
Cost Efficiency:
Reduces machining and installation costs, making it ideal for projects that require strict production efficiency and cost control.
Maintenance Cost Savings: The corrosion resistance of PEM Studs extends the product lifespan (e.g., offshore equipment maintenance cycle extended from 2 years to 5 years).
Decision-Making Tool: When to Choose PEM Studs?
- Recommended Scenarios: Aluminum plate thickness: 0.5-6mm; Required for high-frequency or high-vibration loads; Aiming for lightweight design and cost balance.
- Not Recommended Scenarios: Very thick aluminum (≥8mm, custom stepped studs required); Extreme high-temperature environments (>200°C, welding is preferred).
Common Challenges When Using PEM Studs with Aluminum
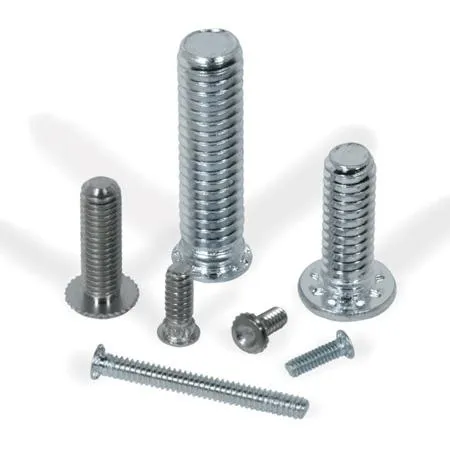
Material Selection and Compatibility Issues:
When using PEM Studs with aluminum, material compatibility can be an issue, especially when dealing with different surface treatments (such as anodizing) or varying hardness levels. Aluminum alloys and coatings can sometimes interfere with proper embedding, leading to weak or unreliable connections. Ensuring the right type of aluminum and surface finish is crucial for optimal performance.
Installation Challenges:
Improper installation can lead to several issues, such as PEM Studs loosening, thread stripping, or failure to properly embed into the aluminum material. This can be caused by inconsistent pressure, incorrect hole size, or lack of alignment. These issues might compromise the mechanical properties and stability of the final assembly.
How to Avoid These Issues:
To prevent these challenges, it’s essential to use the right tools and follow the proper installation procedure. Ensuring accurate hole size tolerance and aligning the PEM Studs correctly during installation is critical. Moreover, controlling installation pressure and following the manufacturer’s recommended settings will help avoid deforming the aluminum or causing other installation failures. Regularly testing the installed studs for stability and strength can also minimize potential issues.
PEM Studs vs. Other Fastening Methods for Aluminum
Welding
- Advantages: Welding creates permanent and strong connections, especially in thick materials.
- Disadvantages: Welding on aluminum requires high temperatures, which can distort the material and compromise its strength. It also introduces heat-affected zones (HAZ) that can weaken the material. Furthermore, welding is a time-consuming process and requires skilled labor.
Thread Cutting
- Advantages: Thread cutting provides a secure connection and is commonly used for assembling metal parts.
- Disadvantages: This method is more labor-intensive and often slower than PEM Studs. It also requires precise threading and can weaken thin aluminum parts, leading to stripping or thread failure. Additionally, the need for additional tapping tools increases the overall cost.
Riveting
- Advantages: Riveting is a fast and reliable method for joining aluminum, especially in applications where no threading is needed.
- Disadvantages: Rivets can be bulky and require access to both sides of the material. They may also not offer the same strong, vibration-resistant connections as PEM Studs and are not as flexible in providing a threaded surface for further assembly.
FAQs - Using PEM Studs for Aluminum
What thickness of aluminum is suitable for PEM Studs?
The optimal range is 0.5-3mm. For thicker plates, custom stepped PEM Studs may be required to ensure proper installation and performance.
How can I avoid aluminum cracking during installation?
Control the installation speed (keep it under 5mm/s) and apply a lubricant or anti-seize coating on the aluminum surface to reduce friction and prevent cracking.
Can PEM Studs be removed and reused?
PEM Studs are designed for irreversible installation. If maintenance or future removal is needed, it’s recommended to use removable models, such as the PEM® S series, which allows for disassembly and reuse.
Do You Have Any Questions?
Let Us Solve Your Problem
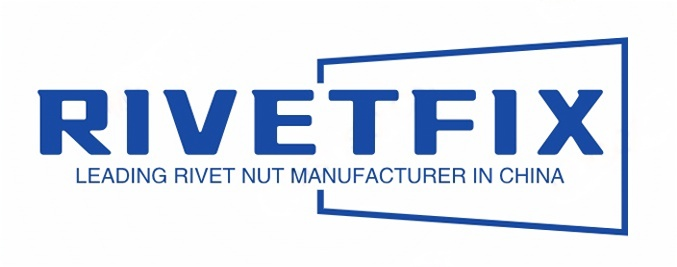
With over 15 years of expertise in fastener manufacturing, Rivetfix has become a trusted global supplier. Our team of 200+ skilled workers and 40+ sales professionals ensures reliable service and consistent supply.
Partnering with Rivetfix means access to top-quality fasteners, cost-saving solutions, and custom designs. We focus on boosting your efficiency, enhancing product durability, and providing on-time delivery. Count on our expert support and continuous innovation for your fastening needs. Choose Rivetfix for premium PEM fasteners and more!
Get High Quality Rivet Nuts Quote!
Send Your Rivet Nut Request
For more than 20 years, Rivetfix has helped customers solve many rivet nuts sourcing needs and technical challenges.
Have a question? Contact us and we’ll provide you with the perfect solution.