What Is the Difference Between a Rivet Nut and a Threaded Insert?
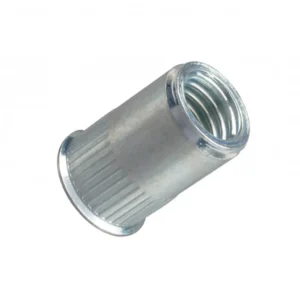
Leading Rivet Nut Manufacturer and Supplier in China
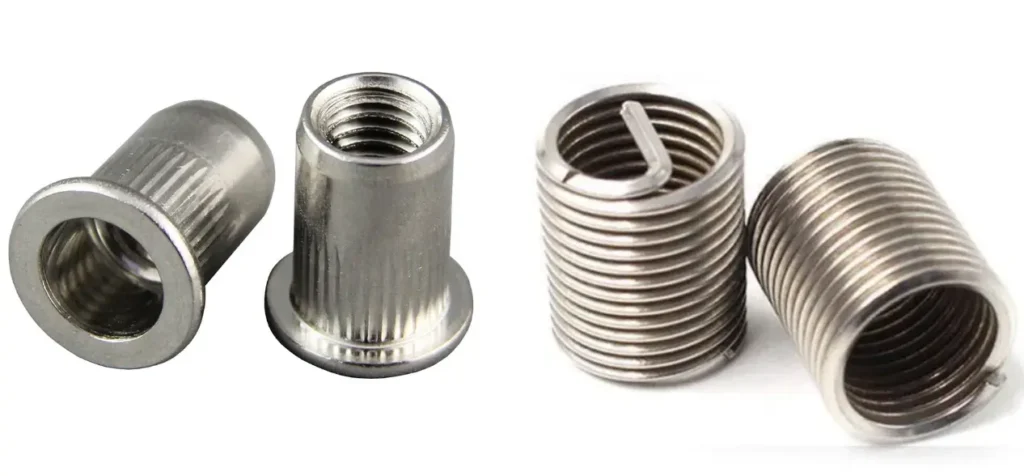
When choosing fastening solutions for different materials and structural requirements, understanding the difference between a rivet nut and a threaded insert is essential. While both provide internal threads for secure fastening, they differ significantly in terms of installation method, suitable base materials, and application scenarios. This guide breaks down the key distinctions to help you select the right option based on your project’s needs—whether you’re working with thin metal sheets, solid plastics, or require repeatable disassembly.
Table of Contents
What Are Rivet Nuts and Threaded Inserts?
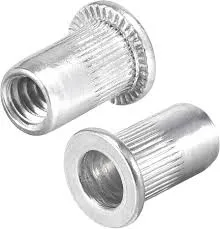
A rivet nut is a special type of fastener primarily used for joining thin sheets or hollow profiles. It typically consists of a hollow cylindrical body with internal threads, whose tail end can be plastically deformed by a specialized tool to tightly clamp inside the hole of the material, thus creating a strong internal threaded connection. This design allows installation from one side of the material without access to the backside, making it ideal for applications where backside access is not possible.
What Are Threaded Inserts?
Threaded inserts are generally used in solid materials such as metal, plastic, or wood. They are installed by pre-drilling a threaded hole in the material, then either screwing in an externally threaded insert or fixing it by bonding, heat staking, or other methods. This reinforces weak or damaged threads, increases thread strength, or repairs worn holes. Installation of threaded inserts usually requires access to both sides of the material or at least to the inner part of the hole.
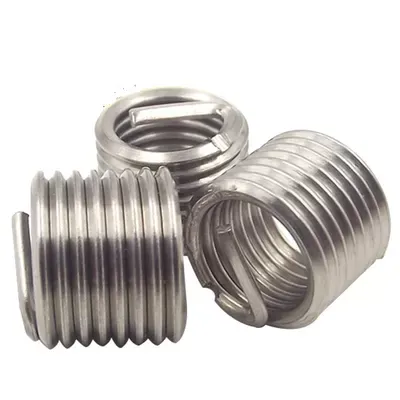
How Do the Installation Methods Differ?
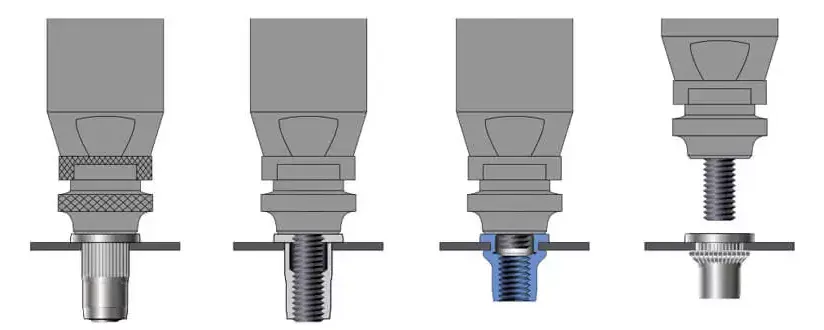
The installation of a rivet nut relies on a specialized tool that plastically deforms the tail end of the rivet nut, securely fastening it inside thin sheets or hollow profiles. The detailed steps and principles are as follows:
① Preparation
Drill a hole in the base material according to the rivet nut’s specified tolerance, ensuring the rivet nut can be inserted smoothly without looseness.
② Insert the Rivet Nut
Align the flange end of the rivet nut with the hole and insert it, allowing the tail end to protrude from the back side of the material.
③ Tool Setup
Attach a mandrel and anvil that match the rivet nut’s thread size to the rivet tool, ensuring a perfect fit between the tool and the rivet nut.
④ Tail Deformation by Pulling
Activate the rivet tool, which pulls the mandrel backward, causing the rivet nut’s tail to expand and bend inward, forming a “umbrella” or “petal”-shaped plastic deformation zone.
⑤ Clamping and Locking
This expansion tightly clamps the base material between the rivet nut’s flange and the deformed tail, creating a strong mechanical lock. The internal threads remain fixed in the material, capable of withstanding bolt torque and tensile loads.
⑥ Single-Sided Installation Advantage
The entire installation is completed from one side of the base material without backside access, making rivet nuts ideal for closed boxes, tubes, or complex structures.
⑦ Post-Installation Stability
Once installed, the rivet nut will neither rotate nor loosen, providing good tensile and shear strength to meet structural connection requirements.
Notes
- The rivet tool must deliver sufficient and even pulling force to ensure full tail deformation;
- Hole diameter and edges must be clean and burr-free to avoid installation defects;
- Different materials and specifications require corresponding force and stroke settings per manufacturer recommendations;
- The rivet nut must be perpendicular to the base material during installation to prevent misalignment and poor locking.
In summary, rivet nut installation relies on plastic deformation of the tail for mechanical locking, allows efficient single-sided installation, and is widely used in thin-sheet structures and enclosed spaces.
Threaded Insert Installation
Threaded inserts are fasteners designed to enhance thread strength or repair threaded holes in solid materials such as metal, plastic, or wood. They have diverse installation methods including screw-in, press-in, and adhesive bonding, detailed as follows:
① Hole Preparation
Drill a hole sized precisely to the threaded insert’s outer diameter and installation requirements to ensure a tight fit without looseness.
② Screw-In Installation
- Used for externally threaded inserts such as steel helicoils or copper thread inserts.
- Installed by screwing the insert into the pre-drilled hole using special tools like installation wrenches or thread insert drivers.
- The external threads engage with the hole threads to achieve mechanical locking.
- Commonly applied in metal substrates, especially for repairing damaged threads.
③ Press-In Installation
Suitable for smooth, non-threaded inserts usually made of copper, aluminum, or plastic.
Installed by pressing or hammering the insert into the hole using a press machine or hammer tools.
Inserts often feature knurls, barbs, or expansion features that create strong friction to prevent rotation or pull-out.
Mostly used in plastic or soft metals and suitable for mass production.
④ Tool Usage
Screw-in inserts require specialized drivers, power tools, or wrenches for smooth and accurate insertion.
Press-in inserts require pressing equipment or punches to apply uniform force.
Adhesive inserts require glue applicators or heating devices.
⑤ Post-Installation Performance
Threaded inserts significantly increase the thread strength of the base material and prevent wear or damage.
Some types include locking or vibration-resistant features suitable for repeated assembly and disassembly.
Notes
Hole diameter and installation depth must be tightly controlled to avoid loosening or misalignment;
Avoid over-tightening or impact during installation to prevent insert deformation or substrate damage;
Different materials and insert types require specific installation processes as per manufacturer instructions;
The installation environment should be clean to prevent contamination affecting insert bonding and fixation.
What Materials and Applications Are Rivet Nuts and Threaded Inserts Suitable For?
Suitable Base Materials: Primarily used in sheet metal and thin-walled tubing, which are typically thin and hollow structures.
Typical Applications: Widely used in automotive manufacturing, aerospace, electrical enclosures, and sheet metal assemblies—especially in enclosed or hollow structures where access to the backside is not possible.
Minimum Installation Thickness: Rivet nuts can be installed in very thin materials, down to 0.5 mm, making them ideal for lightweight structural fastening.
What Are Threaded Inserts Used For:
- Suitable Base Materials: Ideal for solid materials such as metal (aluminum, steel), plastic, and wood.
- Typical Applications: Commonly used in plastic housings, aluminum structural parts, and mold repair—especially in scenarios where thread reinforcement or damaged thread repair is needed.
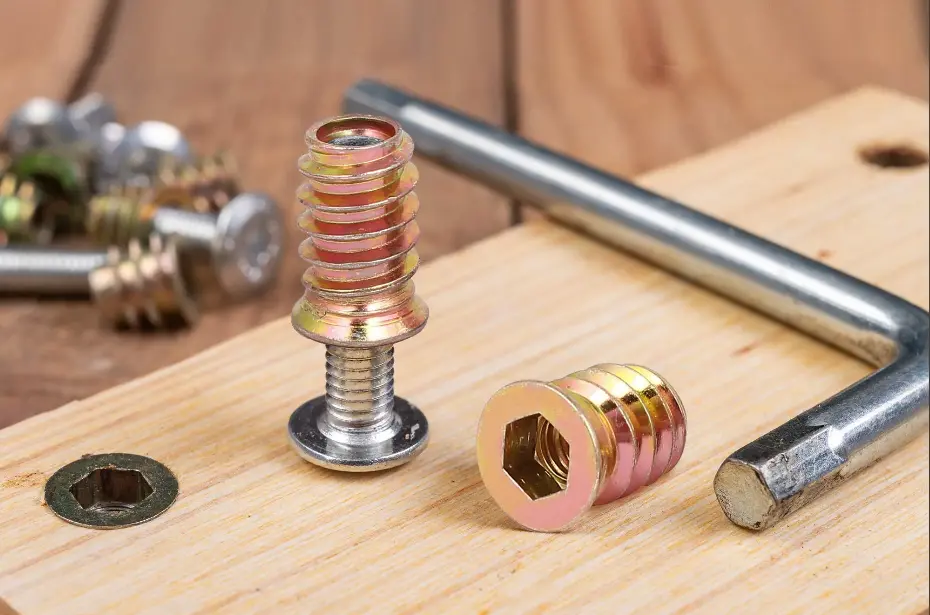
- Minimum Installation Thickness: Requires enough depth for secure anchoring, typically needing a material thickness at least equal to the outer diameter of the insert.
Item | Rivet Nut | Threaded Insert |
---|---|---|
Suitable Base Materials | Sheet metal, thin-walled tubing | Solid metal, plastic, wood |
Typical Applications | Automotive, aerospace, enclosures | Plastic housings, aluminum parts, mold repair |
Minimum Installation Thickness | As thin as 0.5 mm | ≥ Outer thread diameter thickness |
How Do Rivet Nuts and Threaded Inserts Compare in Strength and Stability?
a. Rivet Nut
Tensile Strength: Mainly depends on the degree of plastic deformation at the rivet nut’s tail during installation, as well as the thickness and material of the clamped base. The thicker or stronger the base material, the higher the overall pull-out strength. When used in thinner materials, the tensile resistance decreases accordingly.
Anti-Rotation Performance: To prevent spinning when a bolt is threaded in, rivet nuts require anti-rotation features such as hexagonal bodies (fitted into hex holes) or knurled exteriors (to enhance friction in round holes). Rivet nuts without such features may slip under high torque.
Reusability: Since the installation process causes irreversible deformation, removing a rivet nut typically damages the tail structure, rendering it unusable. Therefore, rivet nuts are generally single-use fasteners and are not suitable for applications requiring frequent disassembly.
b. Threaded Insert
Thread Strength Enhancement: Designed to provide stronger and more wear-resistant threads in soft materials like plastic or aluminum. Ideal for applications involving repeated assembly or vibration where connection strength and service life are critical.
Tensile/Shear Resistance: Some inserts feature barbs, external threads, or self-tapping designs that create a secure mechanical bond. When installed in solid metal, they offer excellent tensile and shear strength with high stability.
Reusability: Many types (e.g., metal inserts, wire thread inserts) are reusable. Even after repeated bolt installations and removals, the internal threads remain intact, making them perfect for maintenance-heavy or service-access areas.
Vibration and Loosening Resistance: Some inserts (like self-locking or key-locking types) offer excellent resistance to loosening under vibration, widely used in aerospace, military, and precision machinery applications where connection security is critical.
How Do Rivet Nuts and Threaded Inserts Compare in Tensile and Shear Strength?
1. Tensile and Shear Strength of Rivet Nuts
The tensile strength of a rivet nut largely depends on:
The material of the rivet nut itself (e.g., carbon steel, stainless steel, aluminum);
The thickness and hardness of the base material;
Whether the deformation during installation is sufficient.
For example, an M6 carbon steel rivet nut installed in 1.5 mm thick steel typically has a pull-out strength of around 4.5 to 6.5 kN.
Shear Strength:
Shear resistance is primarily supported by the flange surface friction against the base material. Since the rivet nut relies on deformation for locking, the shear strength is usually lower than its tensile strength, often around 3.0 to 5.0 kN for M6 in 1.5 mm steel.
Weakness:
Because its locking strength relies on the deformation of thin sheet material, rivet nuts are not ideal for continuous heavy shear loads or cyclic stress applications.
2. Tensile and Shear Strength of Threaded Inserts
Tensile Strength:
Threaded inserts achieve secure fastening through external threads, key locks, or knurled surfaces. Their tensile strength is significantly higher when installed in solid substrates. For example, an M6 stainless steel insert in aluminum can achieve a pull-out strength of 8.0 to 12.0 kN, much higher than a rivet nut of the same size.
Shear Strength:
Thanks to a large surface area and solid mechanical interlock with the base material, threaded inserts offer excellent resistance to lateral loads. An M6 steel insert in aluminum typically provides shear strength of 7.0 to 10.0 kN.
Advantages:
Threaded inserts are ideal for soft materials or applications requiring frequent disassembly. They offer strong and stable connections with high tensile and shear capacities, and most can be reused multiple times with bolts.
Comparison Table: Tensile / Shear Strength Overview
Category | Rivet Nut | Threaded Insert |
---|---|---|
Tensile Strength (M6) | 4.5–6.5 kN (in steel) | 8.0–12.0 kN (in aluminum) |
Shear Strength (M6) | 3.0–5.0 kN | 7.0–10.0 kN |
Suitable Materials | Thin sheet, hollow sections | Solid metals, plastics, etc. |
Locking Mechanism | Tail-end deformation | Thread engagement / mechanical lock |
Reusability | Single-use | Mostly reusable |
Summary Recommendation
For thin-wall structures, single-side installation, and cost-sensitive applications, rivet nuts are the more convenient choice.
For heavy-load bearing, repetitive assembly, or use in soft materials, threaded inserts provide higher strength and more stable long-term performance.
Can Rivet Nuts and Threaded Inserts Be Reused or Replaced Easily?
The installation of a rivet nut relies on plastic deformation of its tail section, which creates an irreversible mechanical lock with the base material once installed.
If removal is required, the rivet nut usually must be forcibly destroyed or drilled out, which damages the nut itself and may also compromise the hole in the base material. Therefore, rivet nuts are generally not reusable, and after removal, a new rivet nut must be installed—often requiring hole repair or enlargement.
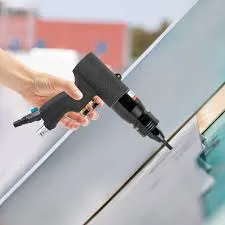
Can You Reuse Threaded Inserts?
Threaded inserts come in various installation types, such as screw-in, press-fit, or bonded. Many models—especially threaded sleeves or locking types—are specifically designed to allow easy removal and reinsertion, making them ideal for applications that require frequent assembly, maintenance, or part replacement. Additionally, threaded inserts are better suited for softer materials like plastic or aluminum, as they minimize damage to the base material during reuse.
Summary:
If your application does not require disassembly and prioritizes fast, permanent installation, a rivet nut is the better option.
If your project requires repeated assembly or ongoing maintenance, a threaded insert offers better reusability and long-term cost efficiency.
Rivet Nuts vs. Threaded Inserts:Which One Is More Cost-Effective to Install?
How Do Rivet Nuts and Threaded Inserts Compare in Installation Cost?
Tool Cost:
Rivet Nut: Installation requires specialized rivet nut tools—manual, electric, or pneumatic—making equipment investment relatively high, especially for industrial-scale operations.
Threaded Insert: Most can be installed using standard tools such as wrenches, drills, or screwdrivers. Some types (like thread repair kits) come with simple installation tools, resulting in lower overall tool cost.
Unit Cost:
- Rivet Nut: Typically made of metal with higher manufacturing precision, rivet nuts have a moderate per-piece cost.
- Threaded Insert: Available in a wide range of materials—from metal to plastic. Plastic inserts are particularly cost-effective for high-volume applications.
Installation Efficiency:
Rivet Nut: Installed in a single action without the need for thread tapping. Ideal for production lines and one-sided access; very fast installation.
Threaded Insert: Often requires pre-tapped holes or heat-press installation. The process is more complex and generally slower than rivet nuts, especially in batch production.
Rivet Nuts vs. Threaded Inserts: Installation Cost Comparison Table
Item | Rivet Nut | Threaded Insert |
---|---|---|
Tool Cost | Medium to High (requires rivet nut tools) | Low to Medium (standard tools) |
Unit Cost | Moderate | Low (especially plastic types) |
Installation Efficiency | High (ideal for production lines) | Moderate (requires pre-drilled or tapped holes) |
When Should You Choose a Rivet Nut vs. a Threaded Insert?
a. When to Choose a Rivet Nut:
One-Sided Access Only: When the assembly environment limits access to only one side of the workpiece, rivet nuts are ideal. Their single-side installation capability makes them perfect for closed structures like enclosures, tubes, and box sections.
Thin-Walled or Hollow Structures That Cannot Be Tapped: For thin or hollow materials where tapping threads is not feasible due to limited wall thickness, rivet nuts provide a strong internal thread by deforming and clamping onto the material.
High-Efficiency Assembly: Rivet nuts can be installed quickly and are well-suited for assembly line production and large-scale manufacturing, improving efficiency and reducing labor costs.
b. When to Choose a Threaded Insert:
Soft Materials or Damaged Threads: In materials like plastic or soft metals where threads can easily strip or wear out, threaded inserts reinforce the thread strength and extend the lifespan of the connection. They’re also effective for thread repair.
Need for Repeated Assembly and Disassembly: Some types of threaded inserts are designed for frequent use, allowing bolts to be removed and reinstalled multiple times without damaging the insert or the base material.
Two-Sided Access Is Available: If the workpiece allows access from both sides, threaded inserts such as press-in or screw-in types can be installed more easily and offer a wider range of tooling options.
Conclusion
Rivet nuts and threaded inserts are two commonly used internal thread fastening solutions, each with distinct characteristics and suitable applications.
Rivet nuts are ideal for thin-walled or hollow structures, especially in situations where only one side of the workpiece is accessible. They achieve a secure hold by plastically deforming their tail section during installation. Rivet nuts offer quick installation and are well-suited for high-volume, assembly-line production. However, they are typically non-reusable after installation and require specialized tools.
Threaded inserts, on the other hand, are more commonly used in solid materials—particularly in plastics or soft metals—to reinforce thread strength or repair damaged threads. They come in various installation types, and some models support repeated assembly and disassembly, making them suitable for applications that require maintenance or frequent part replacement.
Do You Have Any Questions?
Let Us Solve Your Problem
Rivetfix - Leading Fasteners Manufacturer And Supplier In China
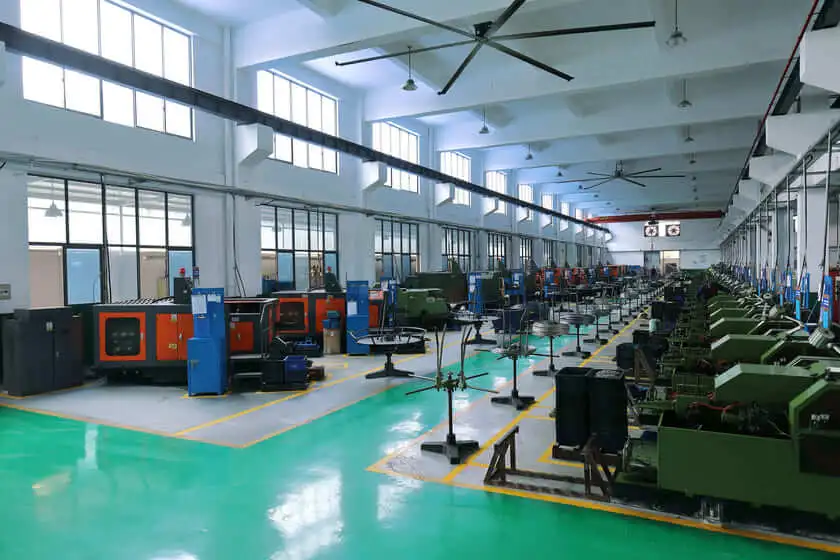
As a leading fastener manufacturer in China with more than 15 years in the industry, Rivetfix are committed to providing first-class quality fasteners and responsive services to the world.
We supply a wide range of threaded inserts and rivet nuts designed to meet the unique demands of your projects. Rivetfix ensures you have the right solution for every application. Choose Rivetfix for versatile, cost-effective, and durable fastening solutions tailored to your specific needs. In addition, we can also provide customized service according to your requirements.
Looking for a reliable way to strengthen your threaded connections or repair damaged threads? Wire thread inserts are the perfect solution. Whether you’re working in aerospace, automotive, electronics, or general manufacturing, these inserts offer exceptional durability, anti-vibration performance, and long-term reliability. Don’t compromise on thread strength—upgrade your fastening systems today with high-quality wire thread inserts.
Contact us now to find the ideal solution for your project!
Get High Quality Rivet Nuts Quote!
Send Your Rivet Nut Request
For more than 20 years, Rivetfix has helped customers solve many rivet nuts sourcing needs and technical challenges.
Have a question? Contact us and we’ll provide you with the perfect solution.