The Ultimate Guide to Jack Nut Sizes
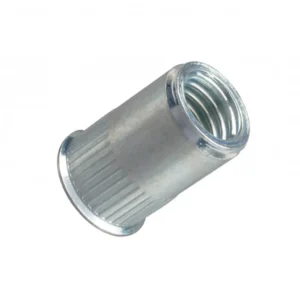
Leading Rivet Nut Manufacturer and Supplier in China
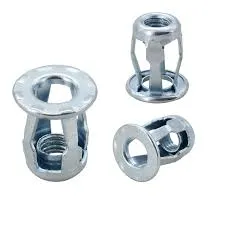
Welcome to The Ultimate Guide to Jack Nut Sizes. Whether you’re working with soft materials or thin sheets, choosing the right jack nut sizes are crucial for a secure and durable installation. In this guide, we’ll explore everything you need to know about selecting the perfect jack nut sizes for your projects.
Table of Contents
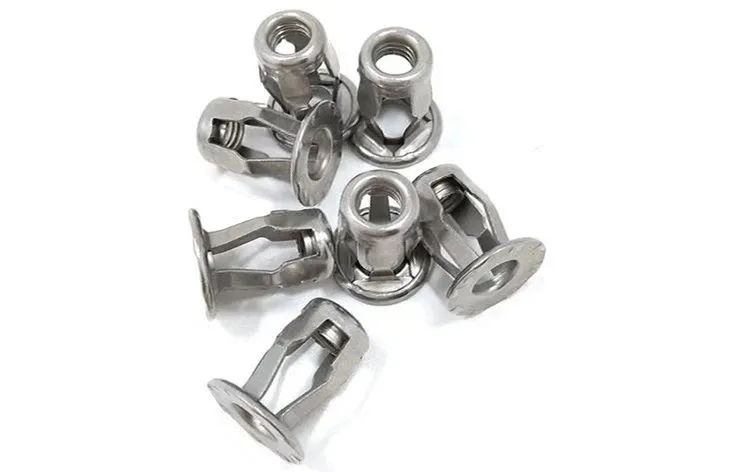
1. Definition of Jack Nut
A Jack Nut is an expansion-type rivet nut designed for use in thin sheets, soft materials, or brittle materials. It consists of a metal sleeve and a four-petal expansion section. During installation, a bolt is tightened, causing the back of the nut to expand, forming a strong gripping structure on the back of the material.
Due to the unique structure of the Jack Nut, it is suitable for materials that cannot support traditional threaded connections, especially thin sheets, plastics, fiberglass, plasterboard, and other low-strength materials. The primary applications include:
- Automotive industry: Used for installing lightweight panels or securing trim pieces.
- Electronics: Provides reliable threaded connections on thin metal or plastic enclosures.
- Furniture manufacturing: Used for joining wood, plywood, or composite materials.
- Construction and decoration: Suitable for fastening soft materials like plasterboard and PVC boards.
1. Applicable Materials
- Jack Nut: Suitable for soft, thin, or brittle materials, such as plastics, fiberglass, plasterboard, and thin metal sheets.
- Standard Rivet Nut: Primarily used for metal, hard materials, such as steel plates, aluminum plates, providing higher pull-out strength and fastening power.
2. Structural Features
- Jack Nut: Composed of a metal sleeve and a four-petal expansion structure. During installation, the tail of the nut expands to create holding force, making it suitable for delicate base materials.
- Standard Rivet Nut: Typically cylindrical or hexagonal, fixed by deformation during installation through riveting, offering higher resistance to pull-out forces.
3. Installation Methods
- Jack Nut: Tightened using a standard bolt, causing the back of the nut to expand and grip the material, no need for a special rivet installation tool.
- Standard Rivet Nut: Requires manual rivet guns, pneumatic rivet guns, or hydraulic rivet guns for installation, where riveting deformation creates the fixing.
4. Load-Bearing Capacity Comparison
- Jack Nut: Primarily relies on material gripping force, with lower pull-out resistance, suitable for light-load connections.
- Standard Rivet Nut: Due to riveting, it forms a strong connection with higher pull-out resistance, suitable for applications requiring high-load fastening.
5. Rotation Resistance
- Jack Nut: In soft materials, it is prone to rotational failure. It is recommended to pair it with washers or use a larger gripping range.
- Hex Rivet Nut: Fixed by a hexagonal hole, providing better rotation resistance, suitable for high-torque applications.
Summary Comparison Table: Jack Nut vs. Rivet Nut
Comparison | Jack Nut | Rivet Nut |
Applicable Materials | Soft materials, thin sheets, brittle materials | Metals, hard materials |
Installation Method | Tighten bolt, expansion grip | Rivet gun pull, deformation fixing |
Installation Tools | Standard bolt | Manual rivet gun, pneumatic rivet gun, hydraulic rivet gun |
Load-Bearing Capacity | Suitable for light loads | Suitable for high-strength connections |
Pull-out Resistance | Moderate | Strong |
Rotation Resistance | Relies on gripping force, prone to rotation failure | Hex rivet nut offers good rotation resistance |
Suitable for Enclosed Areas | Suitable | Suitable |
The Jack Nut is specifically designed for thin-walled or soft materials, while the standard rivet nut is better suited for metal and high-strength applications. The choice depends on the base material and installation environment to determine the most appropriate type of nut.
What Are the Common Jack Nuts Sizes?
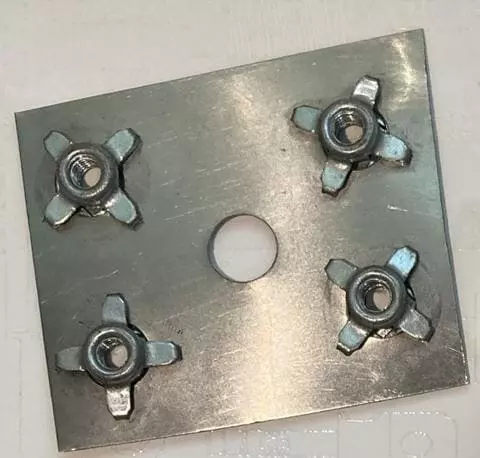
1. Common Specifications and Standard Size Parameters
Specification (Metric) | Installation Hole Size (mm) | Nut Outer Diameter (mm) | Grip Range (mm) | Total Length (mm) |
M3 | 4.8 – 5.0 | 5.8 | 0.3 – 3.0 | 10 – 12 |
M4 | 6.0 – 6.2 | 7.0 | 0.5 – 3.5 | 11 – 13 |
M5 | 7.0 – 7.2 | 8.2 | 0.5 – 4.0 | 13 – 15 |
M6 | 9.0 – 9.2 | 10.2 | 0.5 – 4.5 | 14 – 16 |
M8 | 11.0 – 11.2 | 12.5 | 1.0 – 5.0 | 16 – 18 |
- Installation Hole Size: The required pre-drilled hole diameter for installation, typically slightly larger than the nut’s thread diameter, allowing the Jack Nut to expand and firmly secure after installation.
- Grip Range: Refers to the material thickness range that the nut can effectively grip. The material thickness must fall within the grip range; otherwise, the installation may fail or the gripping force may be insufficient.
- Total Length: The overall length of the Jack Nut, which affects its installation depth and suitability for specific applications.
2. Grip Range and Its Importance
(1) The Role of Grip Range
The grip range refers to the material thickness range that the Jack Nut can effectively fasten. If the material thickness exceeds the grip range, the nut may not fully expand, leading to loosening or an insecure fixation.
(2) Choosing the Right Grip Range
- Thin Materials: If the material is too thin, the nut may deform excessively, resulting in insufficient strength. It is recommended to use models with washers to increase the contact area.
- Thick Materials: If the material exceeds the grip range, the nut may fail to fully expand, resulting in an insecure fix. It is advisable to select a larger specification or an extended-length Jack Nut.
(3) Calculating Grip Range
The grip range is typically selected based on the following formula:
Grip Range = Material Thickness + 0.5mm (Installation Tolerance)
For example, if the material thickness is 2.5mm, a Jack Nut with a grip range of at least 3.0mm should be selected to ensure a secure installation.
3. Applicable Installation Hole Size Range
Specification | Recommended Installation Hole Size (mm) | Tolerance Range (mm) |
M3 | 4.8 – 5.0 | ±0.1 |
M4 | 6.0 – 6.2 | ±0.1 |
M5 | 7.0 – 7.2 | ±0.2 |
M6 | 9.0 – 9.2 | ±0.2 |
M8 | 11.0 – 11.2 | ±0.2 |
Importance of Installation Hole Size:
- Hole Too Large: The nut may become loose or rotate after installation, causing failure.
- Hole Too Small: The nut may not install properly or could damage the material.
- Precision Materials (such as stainless steel, aluminum alloys) require high-precision drilling or laser cutting to ensure the hole size meets tolerance requirements.
How to Choose the Right Jack Nut Sizes?
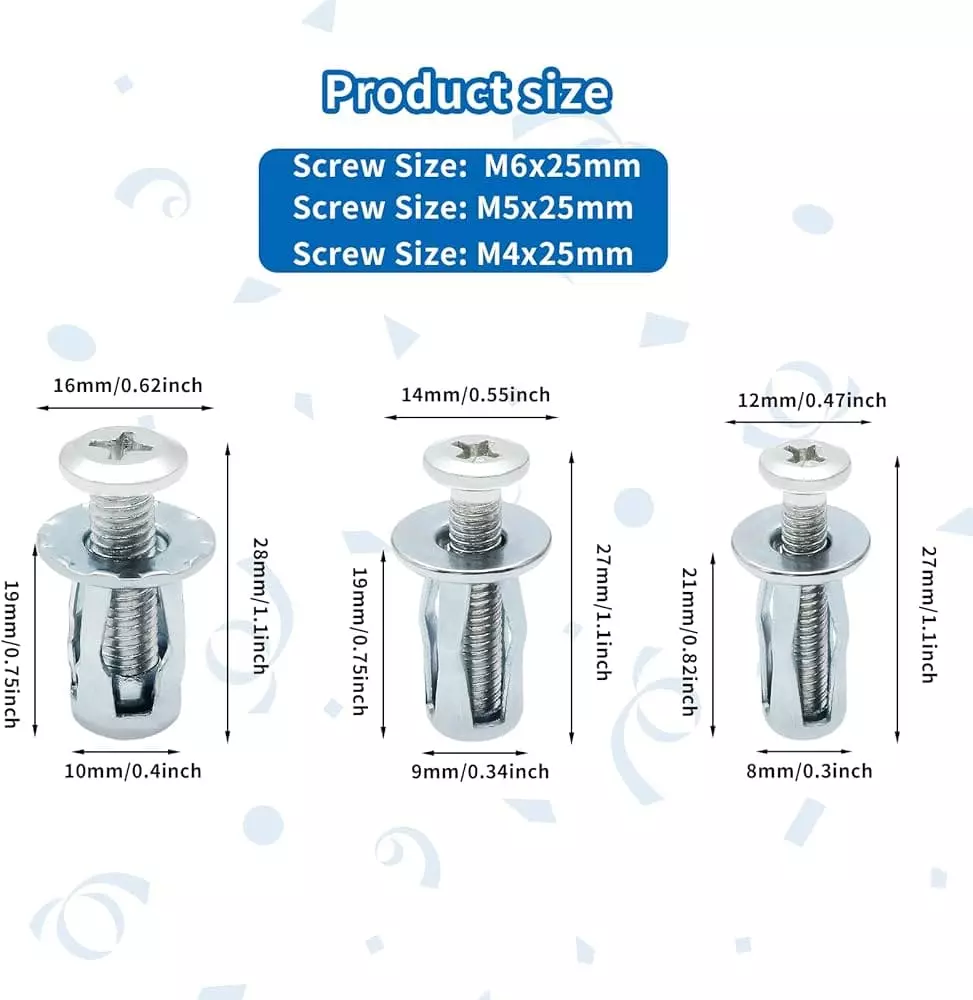
Choosing the correct size of Jack Nut is crucial for installation quality, fastening strength, and service life. Factors such as material thickness, application scenario, and load capacity need to be considered to ensure that the Jack Nut can securely and reliably fasten the target component.
1. Choose the Right Size Based on Material Thickness
The size of the Jack Nut is mainly determined by its Grip Range, which is the thickness of the material it can fasten.
(1) Grip Range Selection
Recommended Grip Range = Material Thickness + 0.5mm (Installation Tolerance)
For example: If the material thickness is 3mm, a Jack Nut with at least a 3.5mm grip range should be selected to ensure stable fastening.
(2) Common Specifications and Grip Range Chart
Jack Nut Sizes | Recommended Grip Range (mm) | Recommended Installation Hole Size (mm) |
M3 | 0.3 – 3.0 | 4.8 – 5.0 |
M4 | 0.5 – 3.5 | 6.0 – 6.2 |
M5 | 0.5 – 4.0 | 7.0 – 7.2 |
M6 | 0.5 – 4.5 | 9.0 – 9.2 |
M8 | 1.0 – 5.0 | 11.0 – 11.2 |
(3) Selecting the Appropriate Grip Range
- Material thickness less than 3mm: Choose M3, M4 specifications.
- Material thickness between 3-5mm: Recommend M5, M6 specifications.
- Material thickness over 5mm: Choose M8 or larger specifications, or consider other fastening solutions for thicker materials (e.g., rivet nuts).
2. Recommended Jack Nut Specifications for Different Applications
Jack Nuts are primarily used for thin sheets and soft materials and are widely used in industries such as automotive, furniture, construction, and electrical appliances. Depending on the application scenario, the requirements for the size and performance of the nuts may vary.
Application Scenario | Recommended Jack Nut Sizes | Applicable Materials | Characteristics |
Automotive Industry | M4 – M6 | Sheet metal, aluminum alloys | Used for interior trims, dashboard fastening, etc. |
Furniture Manufacturing | M3 – M5 | Wood, plastic, composite boards | Used for connecting thin sheets, cabinet fixtures, door handles |
Construction Engineering | M5 – M8 | Steel plates, gypsum boards, PVC | Used for hollow wall installations, light structure bracket fastening |
Electrical Equipment | M4 – M6 | Electronic enclosures, aluminum | Used for electrical panels, heat sinks, casing fixtures |
Industrial Equipment | M6 – M8 | Steel, stainless steel | Used for assembly of mechanical parts in industrial equipment |
Selection Advice
- Light-load applications (≤3mm material): M3, M4 are suitable for furniture, household appliances, and other low-strength scenarios.
- Medium-load applications (3-5mm material): M5, M6 are suitable for the construction and automotive industries with medium-strength fastening requirements.
- Heavy-load applications (≥5mm material): M8 is suitable for industrial equipment, construction projects, and other high-strength scenarios.
3. Load Capacity and Strength Considerations
Different specifications of Jack Nuts have different load capacities. When selecting, consider the tensile strength and torque requirements.
Jack Nut Sizes | Maximum Tensile Strength (N) | Maximum Torque (N·m) |
M3 | 1,500 – 2,500 | 3 – 5 |
M4 | 2,500 – 4,000 | 5 – 7 |
M5 | 4,000 – 6,500 | 7 – 10 |
M6 | 6,500 – 10,000 | 10 – 15 |
M8 | 10,000 – 15,000 | 15 – 20 |
(1) Load Capacity Selection
- Small devices or low-strength applications (1,500-4,000N): M3, M4 are suitable for lightweight materials.
- Medium-strength requirements (4,000-10,000N): M5, M6 are suitable for thicker materials or applications requiring moderate load-bearing capacity.
- High-strength applications (≥10,000N): M8 is suitable for industrial equipment, heavy machinery, and other high-load scenarios.
(2) Factors Affecting Load Capacity
- Material Type: Steel Jack Nuts have higher strength, stainless steel is corrosion-resistant, and aluminum is lighter but has lower strength.
- Installation Method: Using appropriate tools (such as hydraulic nut guns) can ensure higher clamping force and stability.
- Thread Locking: Using locking washers or coatings can improve the nut’s vibration resistance and durability.
4. Key Points for Choosing the Right Jack Nut Sizes
- Determine the material thickness and select the matching grip range.
- Choose the appropriate specification and material based on the application scenario.
- Assess the load capacity to ensure the Jack Nut can handle tensile strength and torque requirements.
- Ensure the installation hole size meets the recommended values to avoid loosening or damaging materials during installation.
How to Install Jack Nuts?
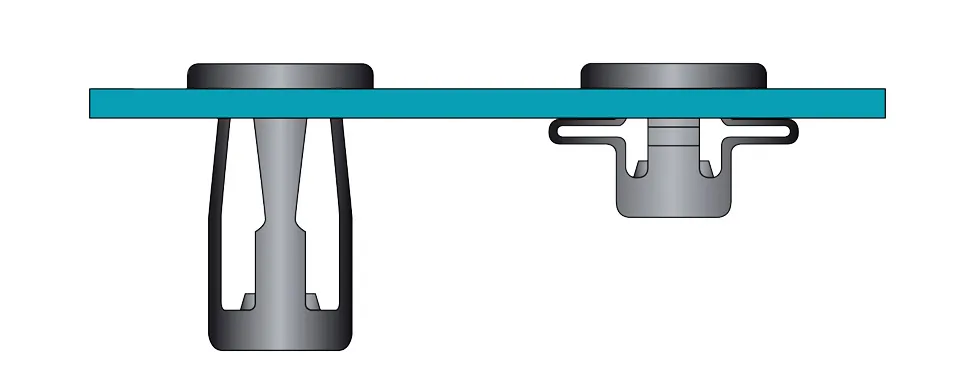
1. Installation Tools Overview (Manual Tools vs. Pneumatic Tools)
Installing Jack Nuts requires specialized rivet tools to expand the nut inside the material, forming a fastening force. The choice of tool depends on the installation volume, nut specification, and application scenario.
(1) Manual Tools
- Applicable Range: Small-batch installations, low-strength applications (such as furniture, household appliances).
- Advantages: Simple to operate, low cost, suitable for M3-M6 specifications.
- Disadvantages: Requires significant manual force, not suitable for high-strength fastening.
- Common Tools: Manual rivet nut gun, manual wrench set.
(2) Pneumatic Tools
- Applicable Range: Medium to large batch production, industrial applications (such as automotive, construction).
- Advantages: Fast installation speed, stable rivet force, suitable for M4-M10 specifications.
- Disadvantages: Requires compressed air equipment, higher tool cost.
- Common Tools: Pneumatic rivet nut gun, hydraulic rivet nut gun.
- Selection Recommendation:
Small-batch installation (DIY, repairs): Recommended manual tools.
Mass production (factory, industrial installations): Recommended pneumatic tools for improved efficiency and consistency.
2. Standard Installation Steps and Precautions
1: Prepare the Installation Hole
- Use the appropriate drill bit to drill a hole in the material.
- Ensure the hole size matches the recommended values (refer to the Jack Nuts specification chart).
- Clean the hole interior to avoid debris affecting the installation.
2: Insert the Jack Nut
- Fully insert the Jack Nut into the drilled hole, ensuring it sits flat against the material surface.
3: Use the Tool to Pull Rivet
- Connect the Jack Nut installation tool (manual/pneumatic).
- Pull the nut with appropriate force to expand it inside the material and form a fastening force.
- Ensure the Jack Nut fully expands and tightly conforms to the material inside.
4: Inspect Installation Quality
- Ensure the nut does not loosen or rotate.
- Perform a torque test (e.g., for M6, it should reach 10-12 N·m).
- Visually inspect whether the Jack Nut is fully expanded, with no deformation or tilting.
3. Common Installation Errors and Solutions
Problem | Possible Cause | Solution |
Jack Nut spins or slips | Hole diameter too large, insufficient installation pressure | Ensure the hole size is correct and apply more installation force |
Nut not fully expanded | Insufficient pulling force or incorrect grip range | Increase the pulling force and choose the correct nut size |
Material deformation | Excessive installation pressure or thin material | Reduce installation force or add washers on the backside of the material |
Thread damage | Over-pulling or excessive tightening of bolts | Use torque control tools to avoid overloading |
FAQs - Guide to Jack Nut Sizes
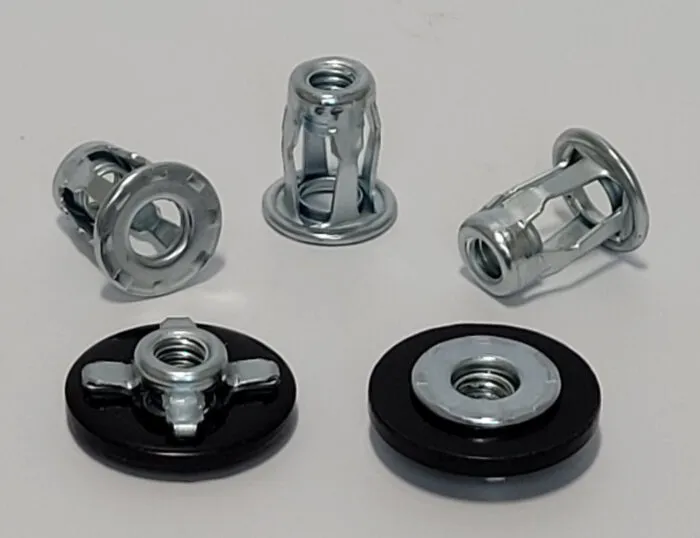
1. What is the difference between manual tools and pneumatic tools?
Manual tools are suitable for small-batch installations and low-strength applications, while pneumatic tools are ideal for medium to large-scale production environments, offering higher installation speed and stability. Pneumatic tools are better suited for larger Jack Nut sizes and high-load applications.
2. How to ensure a secure installation of Jack Nuts?
To ensure a secure installation of Jack Nuts, it is essential to select the correct hole size and installation tool and apply the proper installation force. After installation, check whether the nut is fully expanded, and verify the installation quality through torque testing and visual inspection.
3. What hole size requirements should be considered before installing Jack Nuts?
When installing Jack Nuts, the hole size should be precisely selected according to the nut’s outer diameter. Typically, the hole needs to be 0.1mm to 0.2mm larger than the nut’s outer diameter to ensure the nut can be tightly installed and expand effectively. Holes that are too large or too small may lead to installation failure or nut rotation.
4. What are the common materials and surface treatments for Jack Nuts?
Common materials for Jack Nuts include carbon steel, stainless steel, and aluminum alloys. For applications requiring corrosion resistance, galvanized or stainless steel materials are recommended. Surface treatments include galvanizing, nickel plating, and anti-corrosion coatings, which enhance durability and resistance to corrosion.
5. How is the load capacity of Jack Nuts evaluated?
The load capacity of Jack Nuts depends on the material, size, and installation quality. Common evaluation criteria include the axial tensile strength and radial shear strength the nut can withstand. Based on load requirements, select the appropriate material and size of Jack Nut to ensure it will not loosen or break during use.
Do You Have Any Questions?
Let Us Solve Your Problem
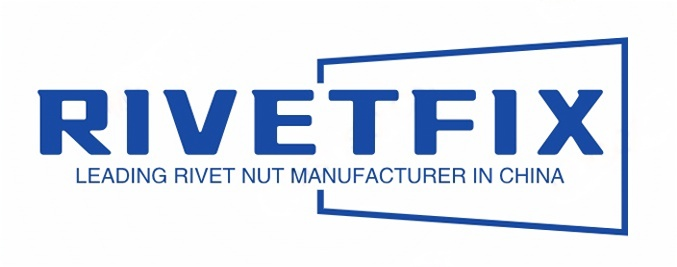
As a leading fastener manufacturer in China with more than 15 years in the industry, Rivetfix are committed to providing first-class quality fasteners and responsive services to the world.
Rivetfix offers a wide range of rivet nuts and jack nuts designed to meet the unique demands of your projects. With different jack nut sizes, Rivetfix ensures you have the right solution for every application. Choose Rivetfix for versatile, cost-effective, and durable fastening solutions tailored to your specific needs. In addition, we can also provide customized rivet nuts service according to your requirements.
Contact us for project advice and the latest rivet nut quote!
Get High Quality Rivet Nuts Quote!
Send Your Rivet Nut Request
For more than 20 years, Rivetfix has helped customers solve many rivet nuts sourcing needs and technical challenges.
Have a question? Contact us and we’ll provide you with the perfect solution.