The Ultimate Guide to Buying Jack Nuts
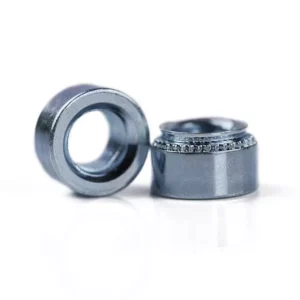
Leading Self-Clinching Fasteners Manufacturer and Supplier in China
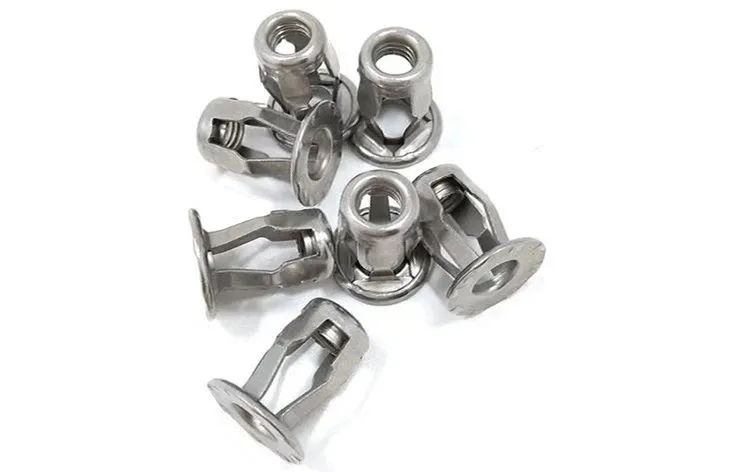
When it comes to securing lightweight panels, electrical enclosures, or composite materials, Jack Nuts (or rivet nuts) offer a unique solution—combining threaded reliability with the convenience of blind-hole fastening. But with endless materials, sizes, and brands available, navigating the guide to buying Jack Nuts can feel overwhelming. How do you balance cost, durability, and application demands without compromising safety or performance?
This ultimate guide breaks down the 7 critical factors you need to know, from decoding material grades (stainless steel vs. aluminum) to avoiding installation pitfalls. Whether you’re a DIY enthusiast tackling home projects or an engineer sourcing industrial fasteners, you’ll discover actionable tips to select the perfect Jack Nut for your project. Let’s dive in!
Table of Contents
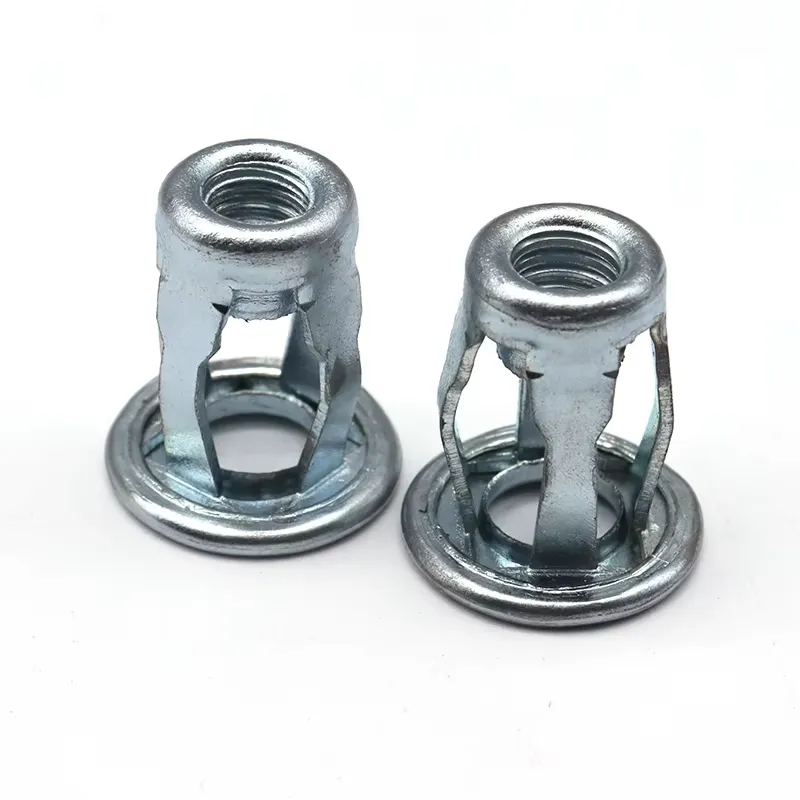
Jack Nuts are rivet-style fasteners designed to create durable, threaded anchor points in thin or brittle materials. They consist of a flanged metal sleeve, a threaded interior insert, and a cone-shaped end. During installation, a specialized tool pulls the insert upward, causing the sleeve to compress and flare outward, forming a secure, vibration-resistant grip. This eliminates the need for access behind the mounting surface, making them ideal for hollow structures.
Jack Nuts excel in securing components to soft materials like plastics and composites, where traditional bolts risk damage. Ideal for automotive trims, electronics enclosures, or lightweight panels, they distribute stress evenly, preventing cracks while offering removable, vibration-resistant threaded anchoring.
Key Factors When Buying Jack Nuts
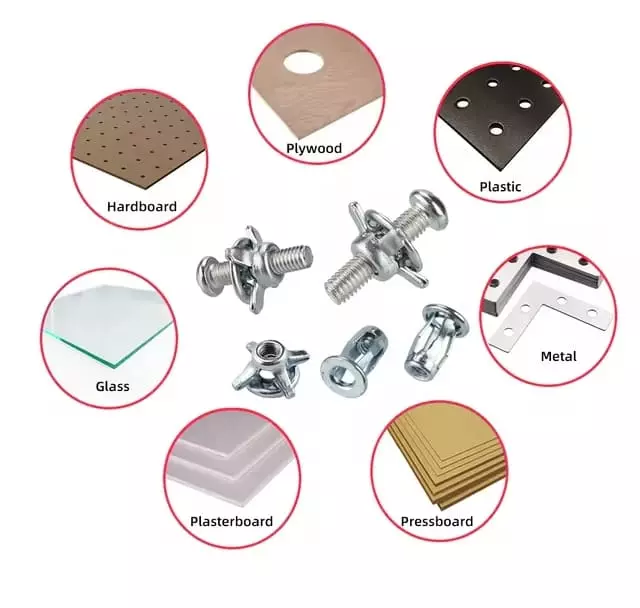
1. Material
Stainless Steel (304/316):
- Exceptional corrosion resistance, ideal for outdoor or humid environments (e.g., marine equipment, outdoor installations).
- Grade 304: Tensile strength ≥505 MPa; salt spray resistance ≥500 hours (ASTM B117 standard), suitable for humid environments (coastal facilities, ship components).
- Grade 316: Incorporates molybdenum for superior acid/alkali resistance. Costs 30-50% higher than 304, recommended for chemical or industrial exposure.
Aluminum (6061-T6):
Lightweight (density 2.7 g/cm³) with moderate tensile strength (≥290 MPa). Designed for non-load-bearing decorative fastening (e.g., automotive interior trim, electronics enclosures). Static load capacity ≤50 kg; avoid high-stress applications.
Zinc-Plated Carbon Steel:
Cost-effective solution for dry indoor applications (furniture assembly, drywall anchoring). Tensile strength ≥800 MPa, but limited corrosion resistance (salt spray resistance ≤100 hours). Avoid moisture-prone or outdoor use.
2. Dimensions and Grip Range
Bolt Diameter:
Standard specifications (e.g., M4–M12) must match the fastener size precisely to ensure thread compatibility and structural integrity.
Bolt Size | Jack Nut Inner Diameter (mm) | Recommended Material Thickness (mm) |
M4 | 4.1-4.3 | 0.8-2.5 |
M6 | 6.1-6.4 | 1.5-4.0 |
M8 | 8.1-8.4 | 2.0-6.0 |
Grip Range:
- Select based on total material stack thickness (e.g., 0.5–3mm for sheet metal vs. 5–10mm for composite laminates).
- Exceeding the recommended range can compromise installation integrity. For instance, using an M6 Jack Nut on 1mm-thick material may prevent proper flaring, increasing pull-out risk by 40% or higher due to insufficient sleeve deformation.
3. Load Capacity
Static Load:
- Aluminum Jack Nuts: ≤80 kg vertical load (e.g., lightweight fixtures).
- Stainless Steel Jack Nuts: Up to 200 kg (e.g., wall-mounted TVs or heavy-duty racks).
Dynamic Load (e.g., vibrating machinery):
- Use high-strength stainless steel combined with thread-locking adhesive (e.g., Loctite 243). Tests (SAE Junker) show 60% improvement in vibration resistance.
- Safety Factor ≥3: Critical for automotive engine bay components requiring dynamic load ratings ≥600N (SAE J429 compliance).
4. Application-Specific Design
- Soft Materials (plastics, honeycomb panels):
- Opt for low-compression force models (e.g., nylon-lined variants) to prevent material crushing during installation.
- Brittle Materials (ceramic composites):
- Require Jack Nuts with larger flanges (e.g., 20mm diameter vs. standard 12mm) to distribute pressure and minimize fracture risk.
Common Applications & Industry Examples
Common Applications
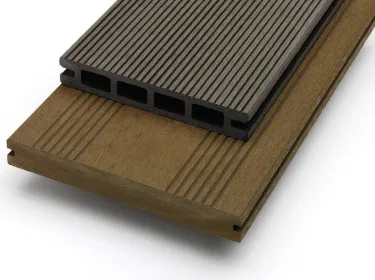
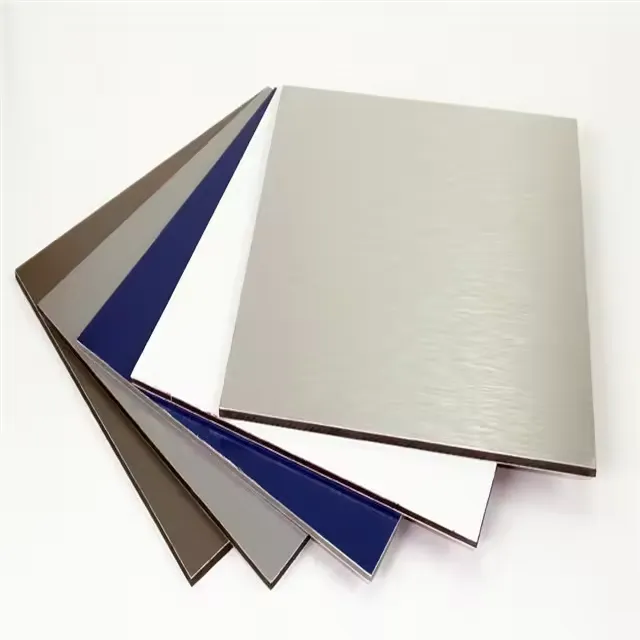
- Thin-Sheet Attachment: Fixing panels, brackets, or fixtures to sheet metal (0.5–3mm) in automotive or HVAC systems.
- Hollow Structures: Securing lightweight frames, wire conduits, or hooks in drywall or hollow-core doors (e.g., hanging TVs, shelves).
- Composite Material Assembly: Anchoring components to carbon fiber, fiberglass, or honeycomb panels (e.g., drone bodies, marine decks).
- Vibration-Prone Environments: Mounting electronics (sensors, control units) in automotive engines or industrial machinery, leveraging anti-vibration flaring.
- Removable Fastening: Temporary fixtures in trade show booths, signage, or theatrical sets where reusability is critical.
Industry-Specific Examples
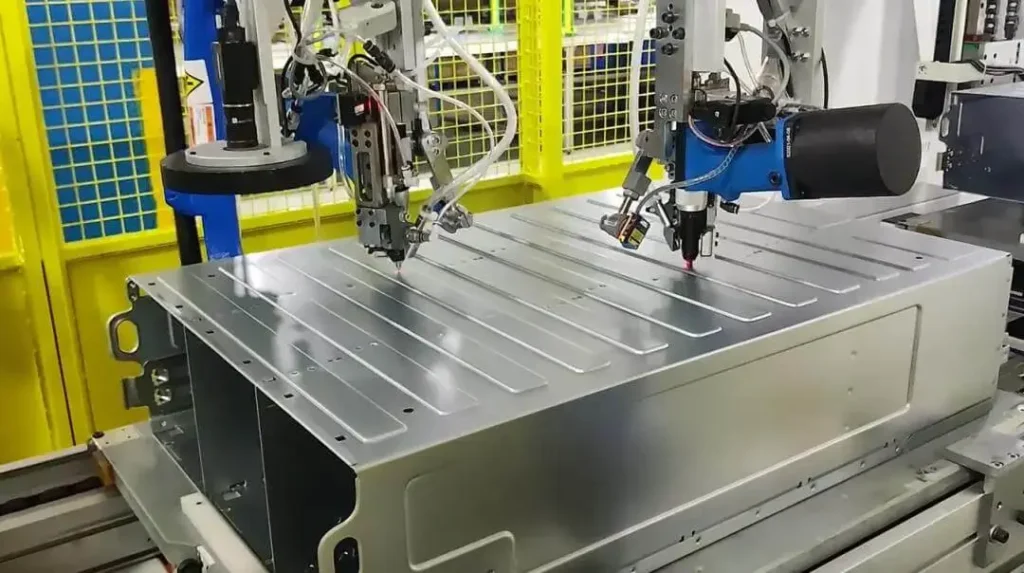
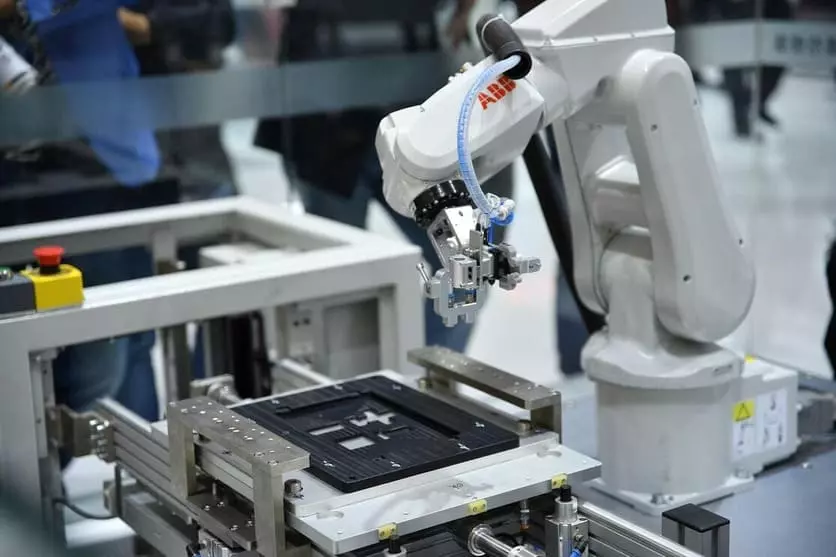
- Automotive: Interior trim assembly, securing dashboard components, or anchoring wiring harnesses to thin body panels.
- Aerospace: Attaching access panels or non-structural covers to aircraft interiors (e.g., overhead bins) without compromising lightweight alloys.
- Electronics & Appliances: Mounting PCBs, heat sinks, or fans inside server racks, printers, or white goods (e.g., washing machine control panels).
- Marine: Fastening corrosion-resistant fittings on boat hulls or decks made of fiberglass-reinforced plastic (FRP).
- Construction: Installing lighting fixtures, handrails, or HVAC ducts onto metal studs or drywall without rear access.
- DIY/Home Improvement: Assembling furniture, garage storage systems, or garden structures (e.g., attaching sheds to composite bases).
How to Install Jack Nuts?
Tools Required
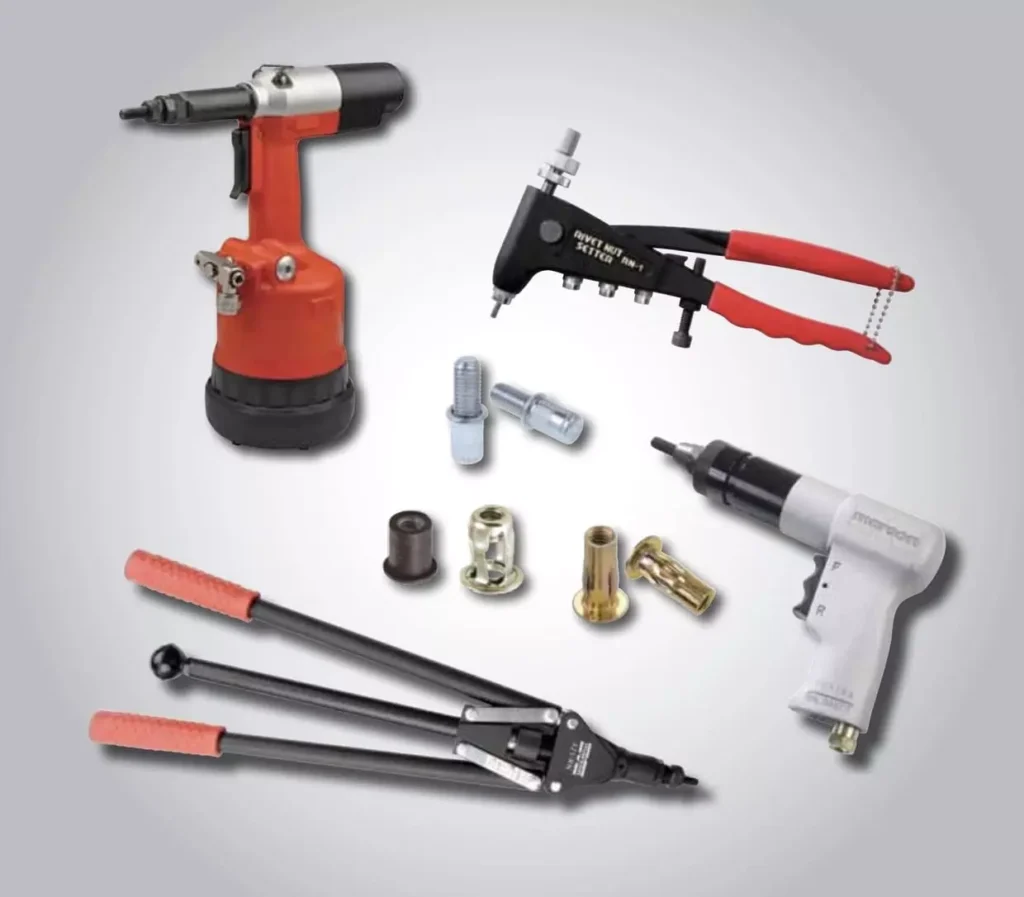
- Essential Tools:
- Jack Nut Installation Tool (manual or pneumatic rivet gun with compatible nosepiece).
- Drill & Drill Bits: Matched to the Jack Nut’s recommended hole size (e.g., 6.5mm for M6).
- Deburring Tool: To clean sharp edges from drilled holes.
- Optional Tools:
- Threaded Bolt or Stud: For alignment during installation.
- Calipers: Verify grip range and hole diameter.
Step-by-Step Installation Guide
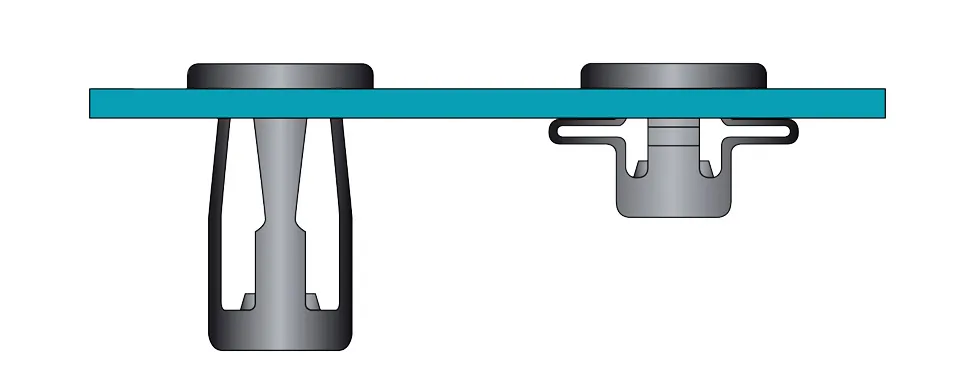
- Prepare the Material:
- Drill a clean, perpendicular hole using the exact diameter specified for the Jack Nut (refer to manufacturer guidelines).
- Example: For an M6 Jack Nut, drill a 6.5mm hole in 2mm-thick aluminum.
- Deburr the hole edges to prevent sleeve damage.
- Insert the Jack Nut:
- Place the Jack Nut into the hole, ensuring the flange sits flush against the surface.
- Optional: Insert a threaded bolt temporarily to align the nut during installation.
- Secure with Installation Tool:
- Insert the Jack Nut’s mandrel into the tool’s nosepiece.
- Squeeze the tool handles steadily until the mandrel snaps off, indicating full sleeve expansion and flaring.
- Verify Installation:
- Confirm the flange remains tight against the surface without gaps.
- Test pull-out resistance by gently tugging the bolt.
Pro Tips for Success
- Soft Materials (Plastics/Composites):
Use low-force hand tools to avoid crushing; pre-tighten bolts at 2-3 Nm torque. - Overcoming Slippage:
If the Jack Nut spins during installation, apply light pressure to the flange with pliers. - Critical Loads:
Apply thread-locking adhesive (e.g., Loctite 243) to bolts in high-vibration areas. - Avoid Over-Compression:
Excessive flaring can split thin materials—stop when the mandrel breaks naturally. - Reuse Correction:
If installed incorrectly, drill out the Jack Nut and replace it; they are not reusable after full expansion.
Common Mistakes & Fixes:
Issue | Solution |
Loose Fit | Check hole diameter; replace with a Jack Nut for thicker material. |
Sleeve Not Flaring | Ensure tool compatibility; replace worn mandrels. |
Material Cracking | Use wider-flange Jack Nuts or reduce compression force. |
Do You Have Any Questions?
Let Us Solve Your Problem
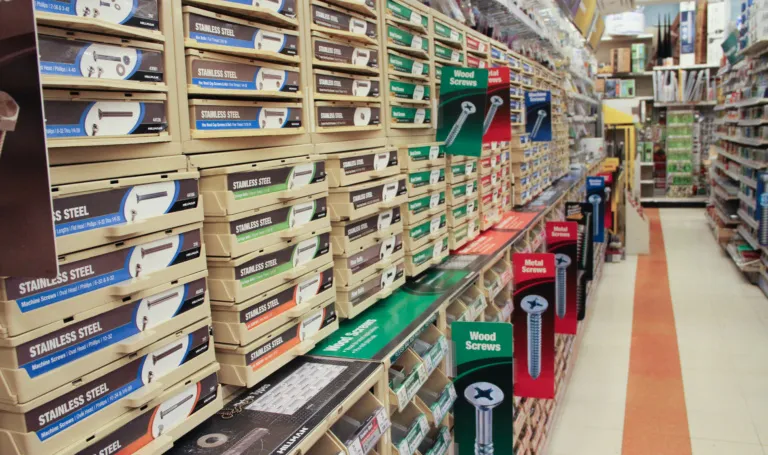
1. Offline Fastener Stores
- Best For: Urgent small-scale purchases or DIYers needing hands-on inspection.
- Pros:
- Immediate availability for common sizes (e.g., M4–M8).
- Expert advice from staff to match materials (e.g., stainless vs. aluminum).
- Cons:
- Limited inventory for specialized types (e.g., large-flange or corrosion-resistant variants).
- Higher per-unit costs compared to bulk online orders.
2. Online Retail Marketplaces
- Best For: Cost-conscious buyers or those needing diverse options.
- Pros:
- Wide range of brands, sizes, and materials (e.g., Amazon, eBay).
- Competitive pricing, especially for bulk purchases.
- Cons:
- Risk of counterfeit/low-quality products (check seller ratings and reviews).
- Longer lead times and potential shipping errors.
3. Specialized Jack Nut Suppliers
- Best For: Industrial users, aerospace/automotive industries, or custom requirements.
- Pros:
- Access to high-performance or custom-engineered Jack Nuts (e.g., titanium for aerospace).
- Technical support, certifications (ISO, AS9100), and volume discounts.
- Cons:
- Higher minimum order quantities (MOQs) and longer lead times.
- Pricing less transparent for small orders.
Comparative Overview
Criteria | Offline Stores | Online Marketplaces | Specialized Suppliers |
Cost Efficiency | Moderate | High (for bulk) | High (volume discounts) |
Product Range | Limited | Extensive | Custom/High-Performance |
Technical Support | Basic | Varies by seller | Dedicated engineering teams |
Lead Time | Immediate | 2–7 days | 1–6 weeks (custom orders) |
Certification | Rarely | Select sellers | Industry-compliant |
What Are Some Common Brands of Jack Nuts to Consider?
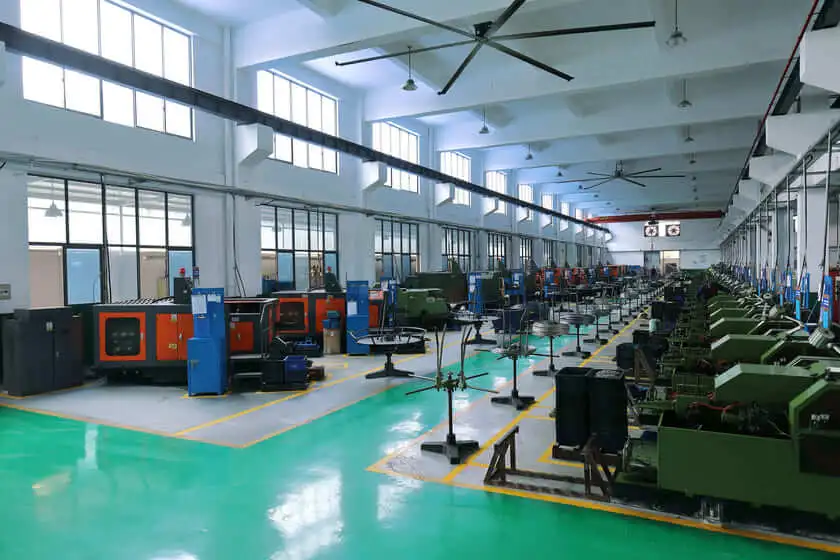
PEM® is a registered trademark of PennEngineering.
- Strengths: High-precision Jack Nuts compliant with ISO 16582 and AS9100 (aerospace).
- Features: Stainless steel, aluminum, and specialty materials (e.g., titanium for heat resistance).
- Best For: Aerospace, medical devices, and mission-critical industrial applications.
- Strengths: Automotive-compliant designs (e.g., FMVSS 216 crash-test certified).
- Features: Proprietary Trilobe® thread profiles for vibration resistance.
- Best For: Automotive assembly lines, heavy machinery.
- Strengths: Wide grip range (0.5–10mm), including low-profile models for tight spaces.
- Features: Corrosion-resistant coatings (e.g., Geomet®).
- Best For: Marine, renewable energy (solar/wind turbine panels).
4. Rivetfix 🌟 (Your Brand Highlight)
- Focus: Innovator in fast installation and multi-scenario adaptability.
- Benefits:
- Tailored solutions (anti-corrosion coatings, specialized head designs).
- Competitive pricing with support for small-batch custom orders.
- Fast technical support and tool compatibility guidance.
Key Recommendation: For projects prioritizing cost-efficiency, flexibility, and localized support, Rivetfix balances quality and efficiency seamlessly.
Guide to Buying Jack Nuts- FAQs
Q1: How do I choose the right material for my Jack Nut?
- Stainless Steel: Use in humid/outdoor environments (boats, coastal areas). Check for 304/316 grade labels.
- Aluminum: Lightweight fixes (electronics, automotive interiors). Avoid saltwater exposure.
- Carbon Steel: Dry indoor applications (furniture, drywall). Always confirm zinc-plated coatings.
Q2: What size Jack Nut do I need?
- Match the bolt diameter (e.g., M6 bolt → M6 Jack Nut).
- Measure your material thickness (e.g., 2mm sheet metal → select a 0.5–3mm grip range).
- Example: For 1.5mm plastic panels, use an M4 Jack Nut with a 0.8–2.5mm grip range.
Q3: Can Jack Nuts handle heavy loads?
- Static loads (e.g., shelves): Stainless steel handles up to 200kg.
- Dynamic loads (e.g., car engines): Use high-strength stainless steel with a safety factor ≥3 (e.g., 600N dynamic rating).
If a nut with a high load is required, it is recommended to choose a rivet nut. Jack Nuts move to soft material design, such as composites and plastics.
Q4: Are Jack Nuts reusable?
No. Once installed (mandrel broken), Jack Nuts cannot be reused. Drilling out is required for replacements.
Q5: What tools are essential for installation?
- Mandatory: Jack Nut installation tool (manual/pneumatic), drill, deburring tool.
- Optional: Torque wrench for critical loads (e.g., aerospace).
Q6: Why does the Jack Nut spin during installation?
- Common causes: Oversized hole (replace with thicker-grip Jack Nut) or improper tool alignment.
- Fix: Hold the flange with pliers while tightening.
Q7: How do I avoid cracking brittle materials like plastic or ceramic?
- Use low-compression models (nylon-lined) or wider-flange Jack Nuts to distribute pressure.
- Drill holes slightly larger (0.1–0.2mm) to reduce stress.
Q8: Are bargain Jack Nuts safe for critical projects?
No. Cheap variants often lack precise thread tolerances or use subpar materials. Prioritize certified brands for safety.
Q9: How to verify supplier reliability?
- Request material certifications (e.g., ASTM, ISO 9001) and samples for testing.
- Check reviews for consistent complaints (e.g., rusting after 3 months).
Q10: What if the Jack Nut won’t flare properly?
- Check: Mandrel compatibility, grip range, hole diameter.
- Solutions: Use a compatible installation tool or switch to a larger flange design.
Have More Questions?
Let Us Solve Your Problem
Why Choose Rivetfix
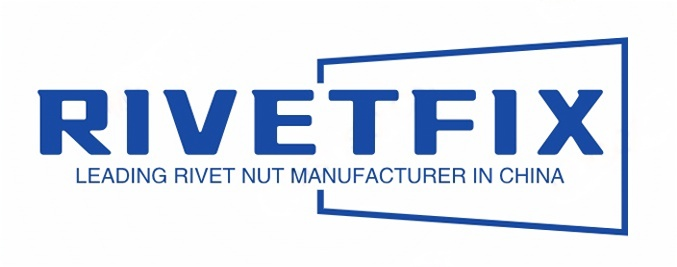
As a leading fastener manufacturer in China with more than 15 years in the industry, Rivetfix are committed to providing first-class quality fasteners and responsive services to the world.
Rivetfix offers a wide range of jack nuts and rivet nuts designed to meet the unique demands of your projects. With options like countersunk, flat, and hex heads, as well as knurled and round body types, Rivetfix ensures you have the right solution for every application. Choose Rivetfix for versatile, cost-effective, and durable fastening solutions tailored to your specific needs. In addition, we can also provide customized jack nuts service according to your requirements.
Contact us for project advice and the latest jack nut quote!
Get High Quality Rivet Nuts Quote!
- Characteristics: High strength, wear resistance, and cost-effective.
- Advantages: Ideal for heavy-duty applications (e.g., machinery, construction).
- Limitations: Prone to corrosion; requires protective coatings (e.g., galvanization).
Send Your Rivet Nut Request
For more than 20 years, Rivetfix has helped customers solve many rivet nuts sourcing needs and technical challenges.
Have a question? Contact us and we’ll provide you with the perfect solution.