Rivet Nut Uses and Installation Tips
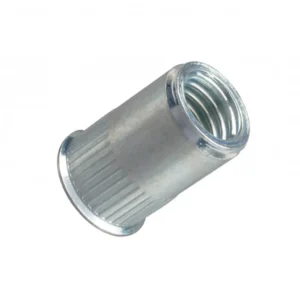
Leading Rivet Nut Manufacturer and Supplier in China
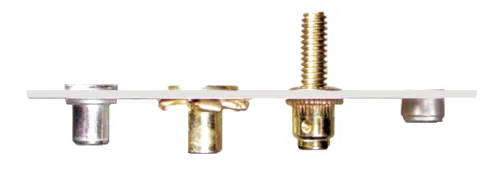
Rivet nuts are essential fasteners for creating strong, reliable threads in thin materials, hollow structures, and hard-to-reach areas. From automotive and aerospace to furniture and electronics, rivet nut uses span various industries, offering secure and vibration-resistant connections. In this guide, we’ll explore common applications of rivet nuts and provide key installation tips to ensure optimal performance in your projects.
Table of Contents
How to Choose the Right Rivet Nuts?
1. Material Selection
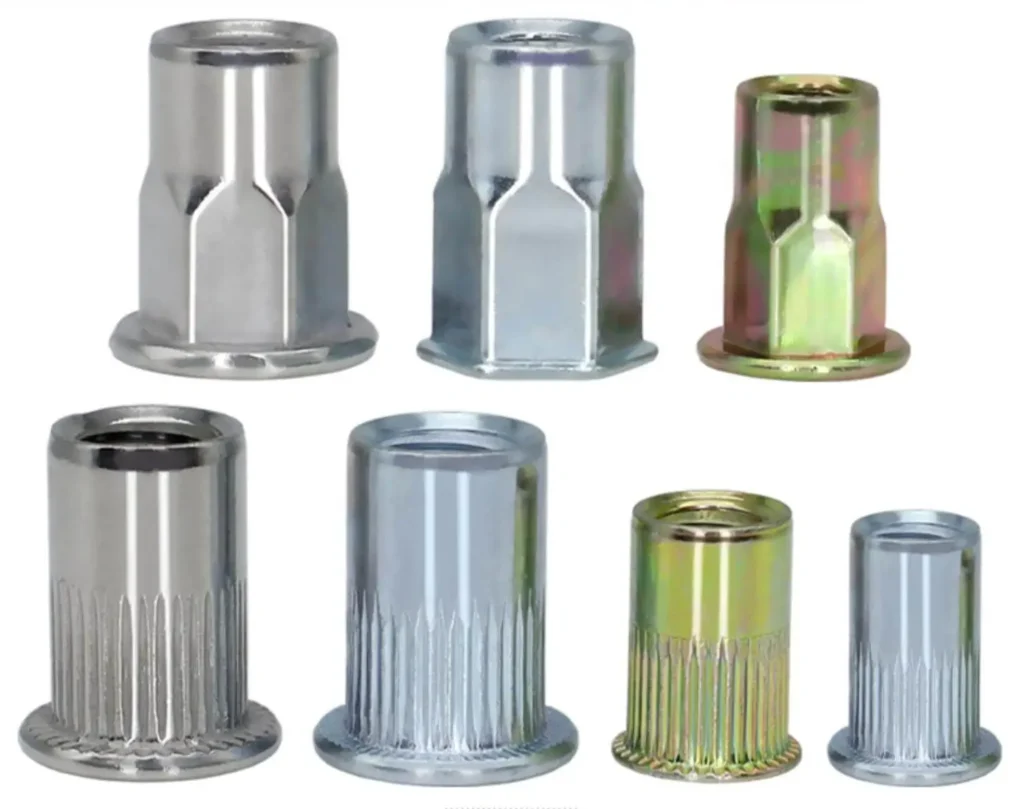
The material of rivet nuts determines their mechanical strength, corrosion resistance, and applicable environments. Different materials are suitable for different applications.
Carbon steel rivet nuts are typically made from low-carbon or medium-carbon steel, offering high mechanical strength and impact resistance. They are ideal for industrial applications that require high load-bearing capacity, such as automotive manufacturing, machinery, and construction. However, carbon steel has poor corrosion resistance, so surface treatments such as zinc plating, Dacromet coating, or phosphating are necessary for use in humid or corrosive environments.
Stainless steel rivet nuts, typically made from 304 or 316 stainless steel, offer excellent corrosion resistance and are ideal for humid, high-temperature, chemical, or marine environments. They maintain good mechanical stability even at high temperatures. However, compared to carbon steel, stainless steel is more expensive and harder, requiring higher installation force during riveting.
Aluminum alloy rivet nuts are lightweight and corrosion-resistant, making them suitable for applications where weight reduction is a priority, such as aerospace, rail transportation, and lightweight automotive manufacturing. However, aluminum has lower mechanical strength than carbon steel and stainless steel, making it unsuitable for high-load or high-vibration environments.
Copper rivet nuts are mainly used in electrical and electronic equipment due to their excellent conductivity. They are also highly resistant to corrosion, especially in marine or chemical environments, where they effectively resist salt spray corrosion. However, copper has lower mechanical strength and limited load-bearing capacity, making it unsuitable for high-strength applications.
2. Size and Specification Selection
Choosing the right rivet nut size depends on the bolt diameter, base material thickness, and installation hole diameter to ensure secure fastening.
(1) Thread Size Selection
Different rivet nut sizes correspond to different bolt diameters. For example, an M3 rivet nut is used with a 3mm diameter bolt, while an M6 rivet nut is used with a 6mm diameter bolt. The rivet nut’s internal thread must match the bolt size to prevent thread damage or loose connections.
(2) Matching with Base Material Thickness
The length of the rivet nut should match the thickness of the base material. If the rivet nut is too short, it may not fully secure after riveting; if it is too long, it could result in uneven riveting or installation failure. Generally, thin-walled rivet nuts are suitable for materials between 0.5mm and 3mm thick, while thick-walled rivet nuts work best for materials over 3mm thick.
(3) Drilling Hole Diameter Selection
When installing rivet nuts, pre-drilled holes in the base material should be slightly larger than the rivet nut’s outer diameter. For example, an M6 rivet nut typically requires a hole diameter of about 9mm to ensure proper insertion and firm fastening after riveting. If the hole is too large, the rivet nut may loosen; if too small, installation may be difficult or damage the base material.
3. Application Environment
The working environment of the rivet nut directly affects its durability and reliability, making it important to select the right material and type based on the application scenario.
(1) Humid or Corrosive Environments
For humid environments or areas exposed to corrosive gases and liquids, such as marine settings, chemical plants, or outdoor equipment, 316 stainless steel rivet nuts are recommended due to their superior corrosion resistance compared to carbon steel and aluminum. For general outdoor applications, zinc-plated carbon steel rivet nuts offer a more economical option but have lower corrosion resistance than stainless steel.
(2) High-Temperature Environments
In high-temperature applications such as engine compartments, boilers, or industrial furnaces, stainless steel rivet nuts are more heat-resistant than carbon steel or aluminum. 316 stainless steel can maintain its mechanical properties in environments up to 800°C.
(3) High-Vibration Environments
For applications involving high vibration, such as automobiles, machinery, and aerospace, hexagonal rivet nuts or flange rivet nuts with anti-rotation teeth are recommended to prevent loosening. Round-body rivet nuts are not suitable for high-vibration environments as they can rotate and loosen over time.
(4) Lightweight Requirements
For weight-sensitive applications such as aerospace, rail transportation, and electric vehicles, aluminum alloy rivet nuts are ideal. They are 30% lighter than carbon steel, stainless steel, and copper, helping reduce overall equipment weight and improve fuel efficiency or battery range.
4. Strength and Load Requirements
The strength and load capacity of rivet nuts depend on their material, thread specifications, and structural design.
(1) Tensile Strength
Tensile strength indicates the maximum axial force a rivet nut can withstand. For example, an M6 carbon steel rivet nut has a tensile strength of approximately 25kN, while an M6 stainless steel rivet nut can reach 30kN. For high-strength applications, thick-walled carbon steel or stainless steel rivet nuts should be used.
(2) Torque Resistance
Torque resistance determines whether the rivet nut will loosen due to rotational forces. Hexagonal rivet nuts provide better stability in high-torque environments due to their anti-rotation structure. In contrast, round-body rivet nuts may loosen under high torque and are not suitable for frequent tightening or disassembly.
(3) Anti-Loosening Design
For applications exposed to high vibration and impact, rivet nuts with serrated flanges, locking structures, or anti-rotation features should be used to increase friction and prevent loosening. Flange-type rivet nuts, for instance, have a larger support surface, reducing deformation and preventing loosening over time.
Rivet Nuts Uses in Various Materials
Rivet nuts are widely used in metal, plastic, composite materials, fiberglass, and wood due to their easy installation, high strength, and broad applicability. Each material has different requirements for rivet nuts, and choosing the right type and installation method ensures a secure and durable connection.
1. Applications in Metal Materials
(1) Thin Metal Sheets (Sheet Metal)
Thin metal sheets are commonly used in automobile manufacturing, machinery, home appliances, cabinets, and electrical equipment. Direct tapping can easily damage the material, and welded nuts may cause deformation. Rivet nuts provide a reliable threaded connection for 0.5mm to 5mm thin metal sheets, without causing heat damage to the base material while withstanding high tensile and torque forces.
- Recommended Rivet Nuts: Thin-wall rivet nuts, flange rivet nuts, hex rivet nuts
- Applicable Industries: Automotive, home appliances, communication equipment, sheet metal processing
(2) Thick Metal Sheets
For metal sheets thicker than 5mm, direct tapping is usually possible. However, when high-strength connections or replaceable threads are required, thick-wall rivet nuts are preferred, especially in machinery, large steel structures, and shipbuilding.
- Recommended Rivet Nuts: Thick-wall rivet nuts, hex rivet nuts
- Applicable Industries: Heavy machinery, shipbuilding, rail transit, heavy equipment
(3) Aluminum and Stainless Steel Materials
Aluminum and stainless steel are widely used for lightweight and corrosion-resistant applications. These materials are either too soft or too hard, making traditional tapping unreliable. Rivet nuts solve this issue by providing a strong threaded connection, making them common in aerospace, lightweight automotive, and medical equipment.
- Recommended Rivet Nuts: Aluminum rivet nuts, stainless steel rivet nuts
- Applicable Industries: Aerospace, new energy vehicles, medical equipment
2. Applications in Plastic Materials
Plastics are widely used in electronics, electrical appliances, and automotive interiors due to their lightweight, insulation, and corrosion resistance. However, plastics have low thread strength, making direct tapping prone to stripping. Rivet nuts provide a metal thread within plastic materials, strengthening the connection and improving reusability.
(1) Soft Plastics (ABS, PP, PE)
Soft plastics are commonly used in appliance housings, automotive trim, and electronic products. Large flange rivet nuts are recommended to increase the contact area and prevent surface damage. Jack nuts, designed for soft materials, are also a suitable choice.
- Recommended Rivet Nuts: Flange rivet nuts, aluminum rivet nuts, jack nuts
- Applicable Industries: Home appliances, electronics, automotive interiors
(2) Hard Plastics (PC, PA, POM)
Hard plastics are used in industrial equipment, medical devices, and instrument housings. Knurled or toothed rivet nuts are ideal, as they have anti-rotation features that enhance connection stability.
- Recommended Rivet Nuts: Knurled rivet nuts, hex rivet nuts
- Applicable Industries: Medical equipment, industrial instruments, power tools
3. Applications in Composite Materials
Composite materials, such as carbon fiber, fiberglass, and engineered composites, are known for their high strength and lightweight properties, making them essential in aerospace, racing, and wind power industries. Since these materials are difficult to tap and prone to delamination or cracking, rivet nuts provide the best solution.
(1) Carbon Fiber Composites
Carbon fiber has high strength and low weight but is prone to cracking. Large flange rivet nuts help distribute stress, reduce material damage, and provide a strong threaded connection.
- Recommended Rivet Nuts: Large flange rivet nuts, stainless steel rivet nuts
- Applicable Industries: Aerospace, racing, drones
(2) Fiberglass Composites
Fiberglass is widely used for electrical insulation and corrosion-resistant equipment. Aluminum or stainless steel rivet nuts ensure durable connections with excellent corrosion resistance.
- Recommended Rivet Nuts: Aluminum rivet nuts, stainless steel rivet nuts
- Applicable Industries: Wind power, marine equipment, electrical equipment
4. Applications in Wood Materials
Wood and wood-based materials are commonly used in furniture, construction, and musical instruments. Traditional wood screws tend to loosen over time, especially after repeated assembly and disassembly. Rivet nuts provide a stable metal thread, improving durability and increasing the load capacity of wood materials.
(1) Solid Wood
For load-bearing structures or applications requiring high pull-out strength, knurled or large flange rivet nuts increase friction and prevent loosening.
- Recommended Rivet Nuts: Knurled rivet nuts, large flange rivet nuts
- Applicable Industries: Furniture manufacturing, architectural decoration, musical instruments
(2) Plywood and Engineered Wood (MDF, Particle Board)
For plywood and MDF, toothed rivet nuts provide better grip, preventing loosening over time.
- Recommended Rivet Nuts: Toothed rivet nuts, knurled rivet nuts
- Applicable Industries: Office furniture, cabinetry, exhibition displays
Summary: Rivet Nuts Uses in Various Materials
Rivet nuts are widely applicable to metal, plastic, composite materials, and wood, providing secure threaded connections, increased structural strength, and easier installation.
- Metal Materials → Suitable for automotive, machinery, rail transit; use carbon steel, stainless steel, aluminum rivet nuts.
- Plastic Materials → Suitable for appliances, electronics; use flange or knurled rivet nuts.
- Composite Materials → Suitable for aerospace, wind power; use large flange rivet nuts.
- Wood Materials → Suitable for furniture, construction; use toothed or knurled rivet nuts.
Do You Have Any Questions?
Let Us Solve Your Problem
Why Rivet Nuts Are More Practical Than Other Fasteners?
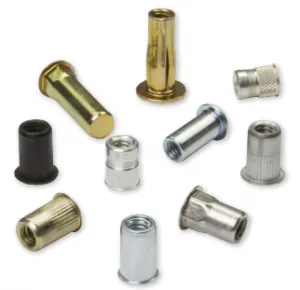
In various industrial manufacturing and assembly processes, rivet nuts offer easy installation, wide applicability, high strength, and no need for welding, making them superior to traditional nuts, screws, weld nuts, and rivets. Whether for metal, plastic, composite materials, or wood, rivet nuts provide secure threaded connections and are ideal for thin sheets, hollow structures, and hard-to-reach workpieces.
1. Suitable for Thin Sheets and Hollow Structures – Solving Tapping Issues
In traditional fastening methods, materials need a certain thickness for threading bolts directly. If the base material is too thin (e.g., 0.5mm-3mm sheet metal), standard threading cannot ensure sufficient strength, leading to thread stripping or failure. Rivet nuts, however, provide a reliable threaded connection on thin-walled materials, ensuring a strong hold.
Additionally, hollow structures (such as tubes) cannot be tapped or welded easily. Rivet nuts enable high-strength internal threads in such materials, making them ideal for bicycle frames, automotive exhaust systems, and steel frame structures.
Comparison:
- Traditional tapping: Requires sufficient material thickness; otherwise, threads may strip.
- Rivet nuts: Work on sheets as thin as 0.5mm, providing strong and durable threads.
2. No Welding Required – Improved Production Efficiency
Traditional weld nuts must be welded to the base material, requiring specialized equipment and potentially causing deformation, stress concentration, and corrosion risks. Moreover, welded nuts are not removable, making maintenance and replacement difficult. In contrast, rivet nuts do not require welding and can be installed quickly using manual, pneumatic, or electric tools, without affecting the base material.
Comparison:
- Weld nuts: Require high temperatures, risk deforming the base material, and are difficult to replace.
- Rivet nuts: Cold-installed, avoiding material damage and allowing quick replacement.
Application Examples: In automotive manufacturing, electronic enclosures, and shipbuilding, rivet nuts replace weld nuts to improve efficiency and reduce production costs.
3. One-Side Installation – Ideal for Hard-to-Reach Areas
Some applications involve restricted access to the back side, such as closed structures, tubular components, or confined spaces (e.g., automobile A-pillars, cabinet frames, and sealed containers). Weld nuts and traditional nuts require access from both sides, whereas rivet nuts can be installed from only one side, solving fastening challenges in enclosed or tight spaces.
Comparison:
- Traditional nuts/weld nuts: Require access from both sides, limiting their usability.
- Rivet nuts: Allow single-sided installation, making them ideal for confined spaces.
Application Examples: In automotive chassis, home appliances, and cabinet assembly, rivet nuts provide a convenient one-sided fastening solution.
4. Reusable and Easy to Maintain
Unlike rivets, which are permanent, rivet nuts provide a reusable threaded connection, allowing bolts and screws to be tightened and removed multiple times. Weld nuts and rivets, once installed, cannot be removed or reused easily, leading to higher maintenance costs. If a weld nut is damaged, replacement is difficult and costly, whereas a rivet nut can be quickly replaced with a new one.
Comparison:
- Rivets: Permanent fastening; cannot be reused once removed.
- Weld nuts: Difficult and costly to replace.
- Rivet nuts: Reusable and easy to replace, reducing maintenance costs.
Application Examples: In rail transportation, machinery, and aerospace, rivet nuts lower long-term maintenance costs and improve serviceability.
5. Wide Applicability – Compatible with Various Materials
Unlike weld nuts and traditional tapping, which are mostly limited to metal materials, rivet nuts work well with metal, plastic, composites, and wood. For plastic housings, fiberglass panels, and carbon fiber structures, where welding or tapping is impractical, rivet nuts provide the best fastening solution.
Comparison:
- Weld nuts: Limited to metal; cannot be used on plastic or composites.
- Rivet nuts: Suitable for metal, plastic, composite materials, and wood.
Application Examples: In electric vehicles, consumer electronics, and smart devices, rivet nuts enable secure fastening between plastic and metal components.
6. High-Strength Connection with Superior Vibration Resistance
Rivet nuts mechanically lock into place through deformation, creating a stable threaded connection that withstands high axial and torque loads. Some rivet nuts, such as hexagonal and knurled rivet nuts, have anti-rotation designs, ensuring strong fastening even in high-vibration environments (e.g., automotive engines, railway equipment, and industrial machinery). In contrast, standard nuts tend to loosen, and weld nuts may crack over time due to fatigue.
Comparison:
- Standard nuts: Prone to loosening under vibration.
- Weld nuts: May experience fatigue failure over time.
- Rivet nuts: Mechanically locked, vibration-resistant, and long-lasting.
Application Examples: In engine compartments, railway tracks, and wind turbines, rivet nuts offer long-term reliability in high-vibration environments.
Summary: Rivet Nuts vs. Other Fasteners
- Work on thin sheets and hollow materials, eliminating tapping limitations
- No welding required – faster installation, no material deformation
- One-sided installation – perfect for confined spaces
- Reusable – easy maintenance and cost-effective repairs
- Compatible with metal, plastic, composites, and wood
- Provide high-strength, vibration-resistant connections
Rivet Nut Uses for Your Project
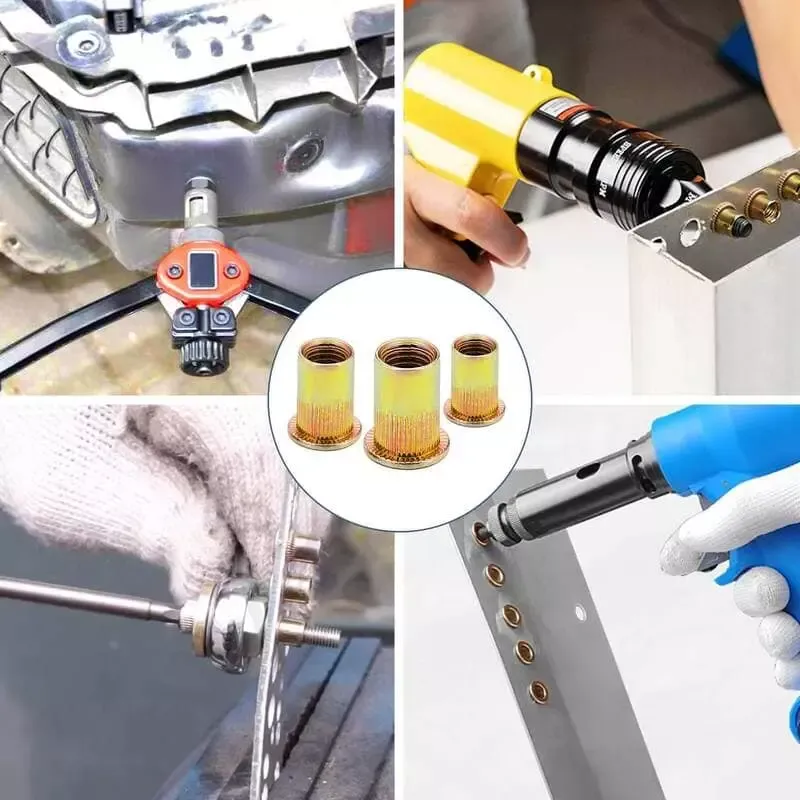
1. Automotive Manufacturing
- Body panels, chassis structures, seat installation, bumper fastening
- Suitable for high-vibration environments, ensuring secure fastening
2. Aerospace Industry
- Aircraft frames, interior fastening, avionics installation
- Uses lightweight aluminum or stainless steel rivet nuts to enhance strength and reduce weight
3. Rail Transportation
- Fastening components inside high-speed trains and subway cars
- Designed for high-strength and corrosion-resistant applications
4. Machinery & Equipment
- Sheet metal enclosures, motor mounts, bracket fastening
- Provides high-load threaded connections, preventing welding deformation
5. Electronics & Cabinets
- Server cabinets, electrical control boxes, instrumentation equipment
- Ideal for metal-to-plastic connections, improving assembly efficiency
6. Home Appliances & Furniture
- Refrigerators, washing machines, kitchen appliances, metal furniture
- One-sided installation, suitable for thin sheets and composite materials
Use the Right Rivet Nut Tool for Installing Rivet Nuts
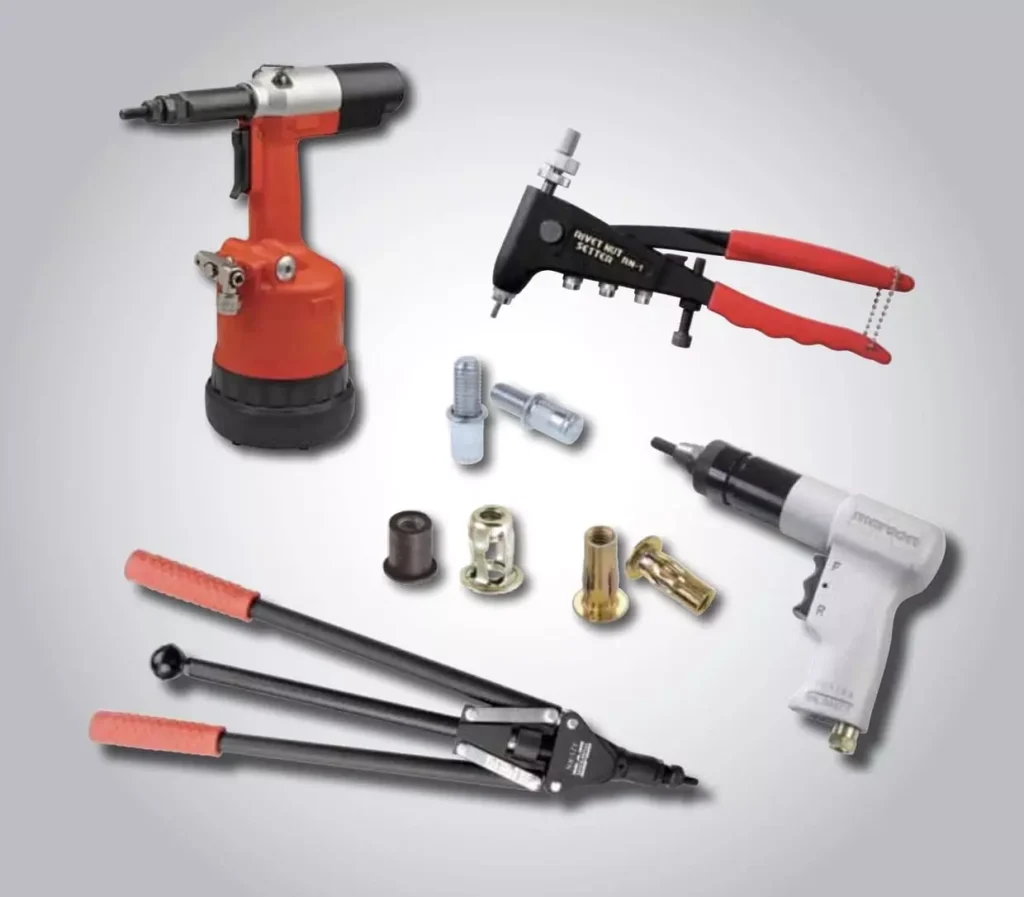
Different types of rivet nut tools are suitable for various applications. When choosing the right tool, consider rivet nut size, workload, installation environment, and cost.
- Suitable for M3-M8 small-sized rivet nuts
- Ideal for small-batch production or repair work
- Low cost but requires significant manual force, making it less efficient
Best for: DIY repairs, occasional use, small metal plate installations
- Suitable for M3-M12 rivet nuts
- Powered by compressed air, with a fast setting speed (30-60 rivets per minute)
- Ideal for high-volume industrial production but requires an air source
Best for: Automotive manufacturing, machining, assembly lines
- Suitable for M3-M12 rivet nuts
- Available in corded or cordless models, providing high portability for on-site work
- Moderate speed (20-50 rivets per minute) but more expensive
Best for: On-site installation, maintenance, mobile operations
Selection Recommendations
- M3-M6 (small-sized nuts) → Choose manual or electric rivet nut gun
- M6-M12 (medium-sized nuts) → Choose pneumatic or electric rivet nut gun
- M12-M20 (large-sized nuts) → Choose hydraulic rivet nut gun
- High-volume production (>1000 pcs/day) → Choose pneumatic or hydraulic rivet nut gun
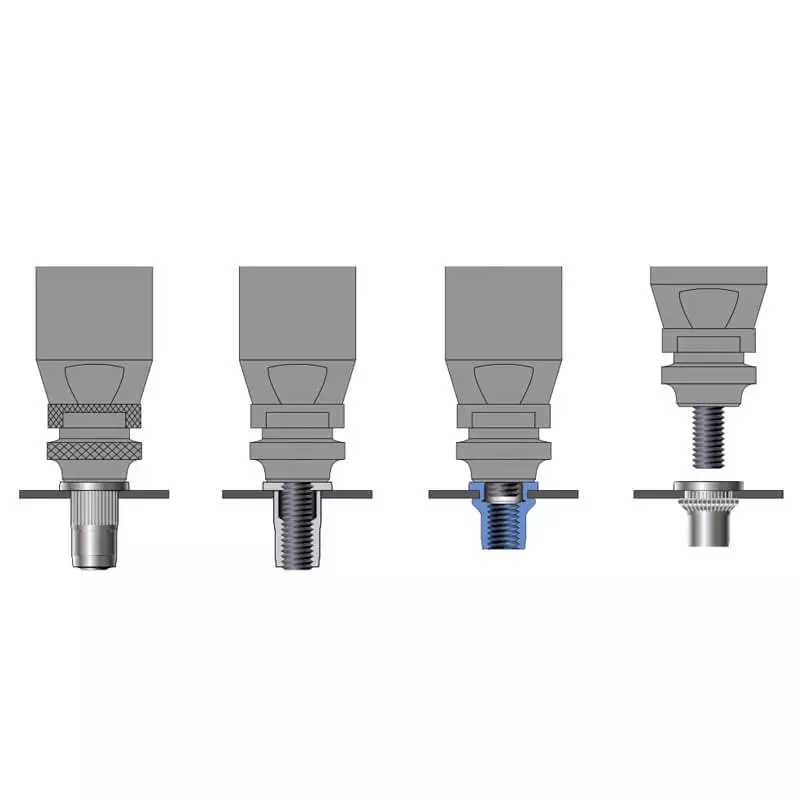
The rivet nut installation process consists of four main steps: preparation, inserting the rivet nut, setting the rivet nut, and quality inspection.
(1) Preparation
- Drilling the Hole: Choose the correct rivet nut hole size based on the rivet nut specifications. For example, an M6 rivet nut typically requires a 9.0mm hole diameter.
- Cleaning the Hole: Remove burrs and debris to ensure the rivet nut fits smoothly.
(2) Inserting the Rivet Nut
- Align the rivet nut with the drilled hole and ensure its flange sits flush against the material surface.
(3) Setting the Rivet Nut with a Rivet Nut Gun
- Manual Rivet Nut Gun: Apply force on the handles to compress and secure the rivet nut.
- Pneumatic/Electric Rivet Nut Gun: Press the trigger, and the tool will automatically complete the setting process.
(4) Quality Inspection
- Visual Inspection: Check if the rivet nut is flush with the material and if the threads are intact.
- Pull-out Test: Use a torque wrench to verify the fastening strength.
- Bolt Insertion Test: Ensure the threads are smooth, with no stripping or loosening issues.
Do You Have Any Questions?
Let Us Solve Your Problem
Rivetfix - Leading Rivet Nuts Supplier in China
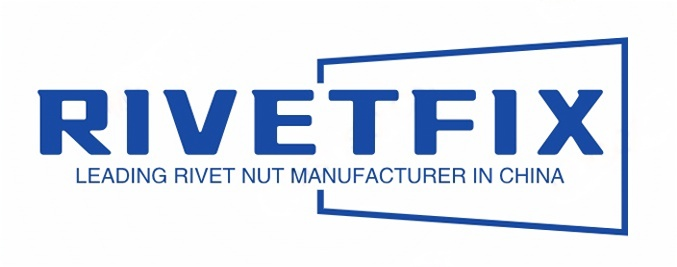
As a leading fastener manufacturer in China with more than 15 years in the industry, Rivetfix are committed to providing first-class quality fasteners and responsive services to the world.
Rivetfix offers a wide range of rivet nuts designed to meet the unique demands of your projects. With options like countersunk, flat, and hex heads, as well as knurled and round body types, Rivetfix ensures you have the right solution for every application. Choose Rivetfix for versatile, cost-effective, and durable fastening solutions tailored to your specific needs. In addition, we can also provide customized rivet nuts service according to your requirements.
Contact us for project advice and the latest rivet nut quote!
Get High Quality Rivet Nuts Quote!
Send Your Rivet Nut Request
For more than 20 years, Rivetfix has helped customers solve many rivet nuts sourcing needs and technical challenges.
Have a question? Contact us and we’ll provide you with the perfect solution.