How to Choose Jack Nuts for Plastic?
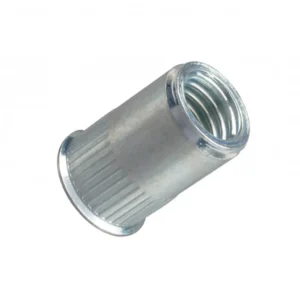
Leading Rivet Nut Manufacturer and Supplier in China
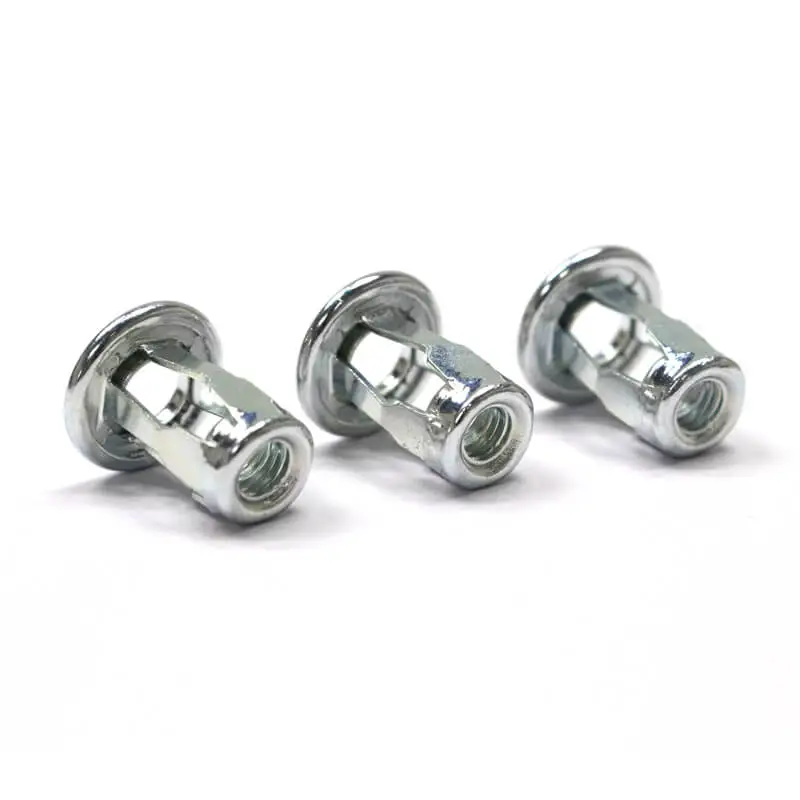
A jack nut for plastic offers a practical solution by providing secure, threaded inserts that prevent the risk of stripping or cracking. However, not all jack nuts are suitable for plastic, so you should choose the correct size, material, and design. In this guide, we’ll explore key factors to consider when choosing jack nuts for plastic to ensure durability and ease of installation in your projects.
Table of Contents
Advantages of Using Jack Nuts for Plastic
Using jack nuts for plastic materials presents several significant advantages, particularly in maintaining the strength and integrity of plastic components.
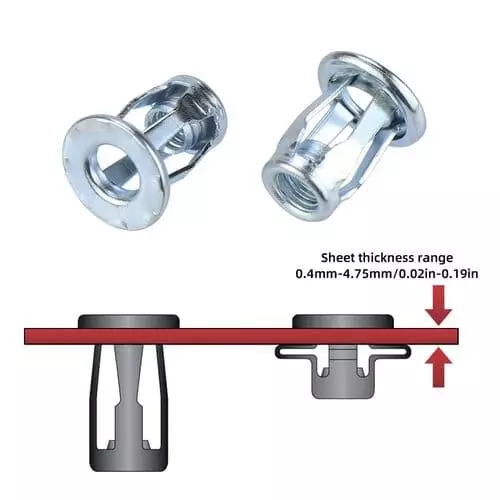
1. Prevents Material Damage
Plastics, especially softer varieties, are highly susceptible to cracking, stripping, or breaking when directly threaded. Jack nuts mitigate these issues by providing a secure, non-destructive method of creating threaded inserts.
Rather than cutting threads into the plastic, jack nuts expand within the material to create a strong internal thread. This expansion process ensures that the plastic’s surface and structure remain intact, reducing the risk of damage during installation. This is important in delicate applications where material integrity is critical.
2. Strong Threaded Connection
Plastic materials typically do not have the same strength or load-bearing capacity as metals, making it challenging to achieve reliable threaded connections. Jack nuts address this by providing a robust, long-lasting insert that ensures bolts or screws can be securely fastened without causing material deformation.
The expansion of the jack nut inside the plastic material creates a strong grip that prevents loosening.
Jack nuts are relatively easy to install compared to traditional threading methods, especially in plastic materials. The installation process generally involves inserting the jack nut into a pre-drilled hole and then using a specialized tool or hand tool to expand the nut. This allows for quick and efficient installation, minimizing labor and time spent on fastening.
Additionally, the lack of need for expensive or specialized equipment makes jack nuts a cost-effective solution for high-volume production or repair work.
4. Prevents Thread Stripping
Plastic materials are prone to thread stripping due to their softer and more flexible nature compared to metals. When traditional threads are cut directly into plastic, repeated use of fasteners can cause the threads to strip, rendering the connection unreliable.
Jack nuts solve this problem by providing a durable, reusable internal thread that resists stripping. The nut’s design allows for multiple installations and removals of bolts or screws without damaging the insert or the surrounding plastic. This is particularly advantageous in repair and maintenance applications, as it prolongs the lifespan of both the plastic material and the fasteners used.
5. Enhanced Load Distribution
Jack nuts expand and deform at their base, allowing them to distribute the load evenly across the surrounding plastic material. This even distribution prevents localized stress concentrations.
By spreading out the forces exerted on the plastic, jack nuts ensure a more stable and reliable connection, even in applications where the fasteners might experience high levels of tension or shear forces.
Key Tips for Using Jack Nuts with Plastic
Using jack nuts with plastic requires attention to detail to ensure that the installation is successful and that the plastic material remains undamaged. By following these key tips, you can ensure that jack nuts provide a secure, long-lasting connection in plastic materials.
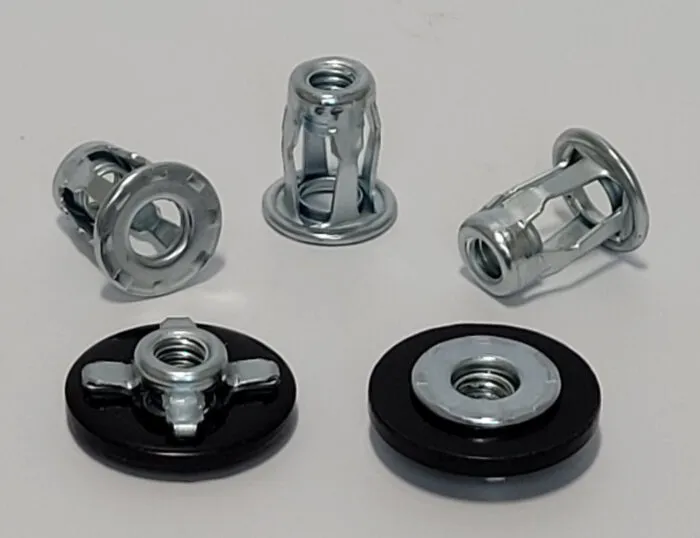
1. Choose the Right Jack Nut
Select a jack nut made from a material that is compatible with the type of plastic you are using.
Stainless steel and aluminum are commonly used for jack nuts because they offer a good balance of strength and corrosion resistance, making them ideal for plastic applications.
Consider the environmental conditions, such as exposure to moisture, chemicals, or high temperatures, to ensure the selected jack nut material is durable enough.
2. Correct Hole Size
It is crucial to drill the right size hole for the jack nut installation. The hole diameter should be slightly larger than the outer diameter of the jack nut to allow it to expand properly during installation.
If the hole is too small, the jack nut may not expand correctly, leading to a weak or unstable connection. Too large a hole could result in a loose fit and compromised performance. Always refer to the manufacturer’s guidelines for hole size recommendations.
3. Use Proper Installation Tools
To achieve the best results, use the right tools to install jack nuts. Hand tools or pneumatic tools can be used to expand the jack nut and secure it in place. If you’re working with plastic, be sure the tool settings (such as pressure) are appropriate for the material. Take your time to ensure the jack nut is properly expanded inside the hole, creating a secure threaded insert.
Jack nuts expand inside the plastic material to create a strong, threaded connection. Always monitor the installation process to ensure the jack nut expands evenly. Incomplete or uneven expansion can lead to loose fasteners or cause the plastic to deform around the nut. Make sure the jack nut is flush with the surface of the material to avoid any protrusions that might cause issues in assembly.
4. Use for Non-Load Bearing Applications When Needed
While jack nuts are durable, they are not always suitable for high-load applications when used with plastic. In situations where a high load-bearing capacity is required, such as in heavy machinery or structural components, jack nuts may not provide the necessary strength. For such applications, consider using metal materials or other stronger fastening solutions.
5. Consider Vibration Resistance
Plastic materials can be more susceptible to vibration than metals, which may cause fasteners to loosen over time. Jack nuts provide a secure threaded connection, but it’s important to consider whether additional locking mechanisms (such as lock washers or thread-locking adhesives) might be necessary, especially in applications where vibration is a concern.
Do You Have Any Questions?
Let Us Solve Your Problem
How to Choose Jack Nuts for Plastic?
Choosing the right jack nuts for plastic requires considering several factors to ensure optimal performance, durability, and compatibility with the plastic material you’re working with.
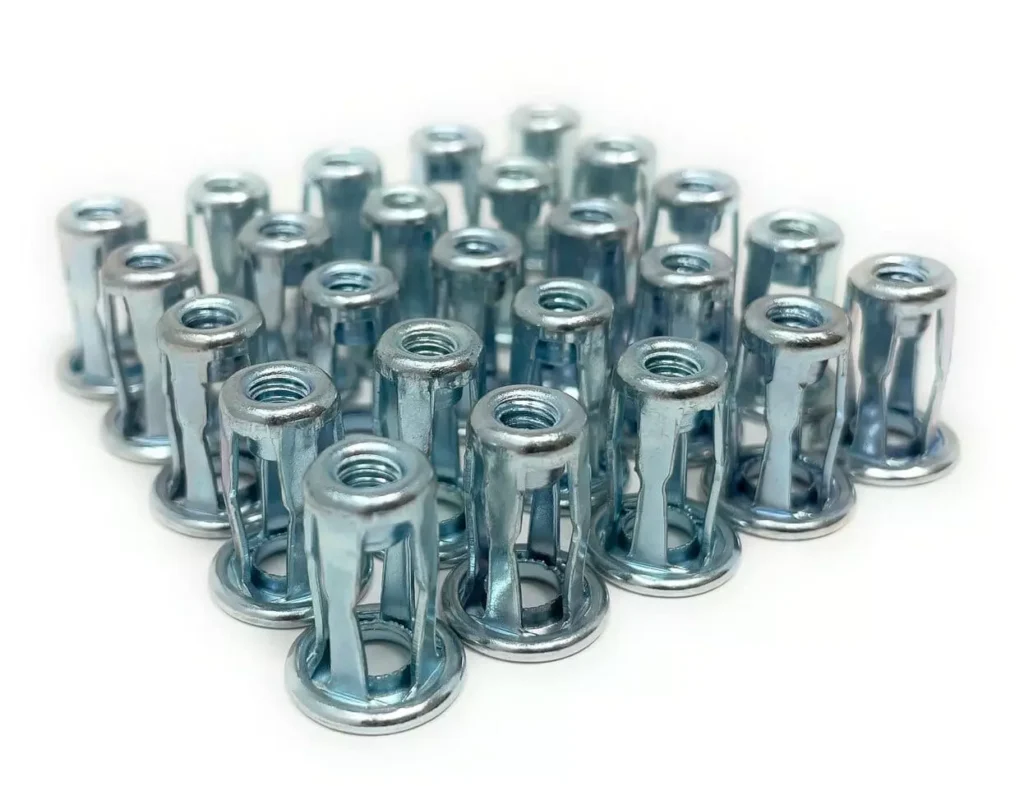
Material Compatibility
Choose jack nuts made from materials that are compatible with plastic and provide adequate strength without damaging the plastic. Stainless steel and aluminum are often preferred due to their good balance of corrosion resistance and strength.
Consider the environment in which the plastic part will be used. If the part will be exposed to extreme temperatures, chemicals, UV light, or moisture, choose jack nuts that offer additional protection such as coatings or rust-resistant finishes. For outdoor or marine environments, corrosion-resistant materials and coatings will help maintain the durability of the jack nuts.
Consider the Type of Plastic
Plastic materials generally have lower load-bearing capacity than metals, so it’s essential to match the strength of the jack nut to the application. For heavier-duty applications, you might need jack nuts with higher strength or made from more robust materials. For lighter-duty applications, a standard jack nut will suffice.
- For soft plastics, such as PVC, polystyrene, or acrylic, use jack nuts that are designed for low-strength applications and can expand without causing cracking or material failure.
- For strong plastics like nylon or polycarbonate, you can use jack nuts that provide higher load-bearing capacity.
Choose the Right Thread Size
The thread size must match the fastener or bolt that will be used, and the plastic material must be able to support the threaded connection without damage. Here’s a detailed breakdown of how to choose the right thread size:
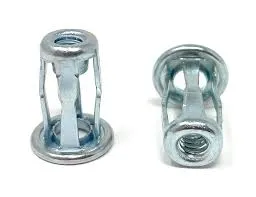
1. Match the Bolt or Screw Size
The jack nut must have the correct internal thread size to match the bolt or screw intended for use in the application. For example, if you are using an M6 bolt (6 mm in diameter), you need to select a jack nut with an M6 internal thread.
- Metric Thread Sizes: Common metric thread sizes for jack nuts include M3, M4, M5, M6, M8, M10, M12, and larger sizes. For example, M6 indicates a bolt or screw with a 6mm diameter. The corresponding jack nut will have an internal thread with the same size, ensuring proper engagement with the bolt.
- Imperial Thread Sizes: In some cases, especially in markets like the United States, imperial thread sizes are used. These sizes may include #6-32, #8-32, ¼”-20, 5/16″-18, and so on. These thread sizes follow different standards (such as Unified Thread Standard) and require corresponding jack nuts.
2. Consider the Thread Pitch
Thread pitch refers to the distance between threads. In the metric system, thread pitch is typically measured in millimeters (mm) between threads. For example, an M6x1.0 thread means that the distance between threads is 1.0 mm.
- Common Thread Pitches: For jack nuts, common thread pitches for metric sizes might include 1.0 mm, 1.25 mm, or 1.5 mm for M6, M8, and M10 sizes. If the wrong pitch is chosen, the bolt may not thread properly into the jack nut, which could lead to a loose connection or thread stripping.
- Imperial Thread Pitch: For imperial threads, pitch is often denoted by the number of threads per inch (TPI). For example, a ¼”-20 bolt has 20 threads per inch. You would need to select a jack nut with the same TPI (20 threads per inch) for a secure fit.
3. Thread Strength and Material Impact
The thread size also plays a role in the strength of the connection. Larger thread sizes can handle higher loads, but they may require stronger materials and larger jack nuts. For plastic applications, a balance must be struck to ensure that the plastic can handle the shear and tensile forces generated by the threaded fastener.
- Load Considerations: For heavier-duty applications, you may need to select a larger thread size (e.g., M8, M10), but this requires ensuring the plastic material can support the load and that the jack nut can expand sufficiently to hold the bolt in place without stripping the threads.
4. Examples of Thread Size Choices for Common Applications:
- Furniture Applications: For lighter-duty connections, such as securing legs on tables or attaching brackets to cabinets, M6 or M8 jack nuts are typically sufficient.
- Appliance Applications: For securing components in appliances like refrigerators, washing machines, or dishwashers, M6 or M8 thread sizes are common, depending on the size of the bolts.
- Automotive or Aerospace Applications: For these heavier-duty applications, thread sizes like M10 or larger might be required. Jack nuts with these sizes ensure that the material remains secure even under stress or vibration.
Select the Correct Jack Nut Design
Jack nuts come in different designs, including open-ended, closed-end, and blind designs.
- Open-ended designs are ideal for applications where you need to access the inside of the plastic part for installation or maintenance.
- Closed-end or blind jack nuts are better when you need a sealed, moisture-resistant installation, and these are often used in applications where environmental conditions, such as exposure to water, may affect the plastic material.
Hole Size and Installation Fit
The hole size you drill for the jack nut must match the outer diameter of the jack nut, ensuring a proper fit without excessive gap. For example, if you are using an M6 jack nut, the hole size should typically range between 6.5 mm and 7.0 mm (depending on the jack nut design) to allow for proper expansion and ensure a secure connection in the plastic material.
Recommended Hole Sizes (for reference):
- M6 Jack Nut: 6.5 mm to 7.0 mm
- M8 Jack Nut: 8.5 mm to 9.0 mm
- M10 Jack Nut: 10.5 mm to 11.0 mm
Choosing a hole size too large or too small will prevent the jack nut from expanding correctly or may cause damage to the surrounding plastic.
Why Wholesale Jack Nuts from China
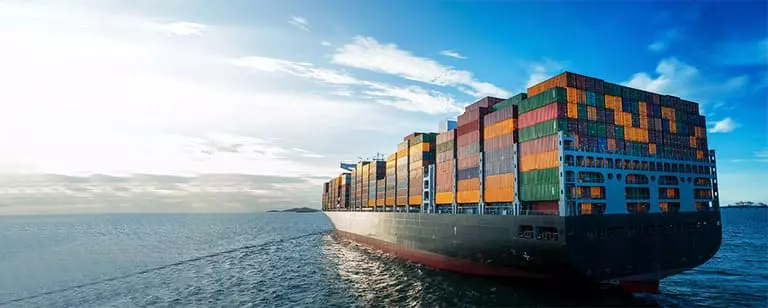
- Cost-Effective: Lower production costs lead to competitive pricing, ideal for bulk purchases.
- High Quality: Many suppliers meet international standards like ISO, DIN, and JIS.
- Variety: Access to a wide range of sizes, materials, and custom options.
- Bulk Orders: Efficient production and reliable shipping for large-scale orders.
- Customization: Tailor products to specific requirements, such as thread size or coating.
- Strong Export Infrastructure: Well-established shipping and logistics networks ensure timely delivery.
Do You Have Any Questions?
Let Us Solve Your Problem
Rivetfix - Leading Jack Nuts Supplier in China
Rivetfix is a leading China manufacturer of jack nuts based in China, offering high-quality, cost-effective solutions for a wide range of industries. We specialize in providing custom jack nuts tailored to meet specific customer requirements, ensuring reliable and durable threaded connections. With a commitment to quality and efficient service, Rivetfix guarantees fast delivery and competitive pricing, making us the trusted choice for businesses worldwide.
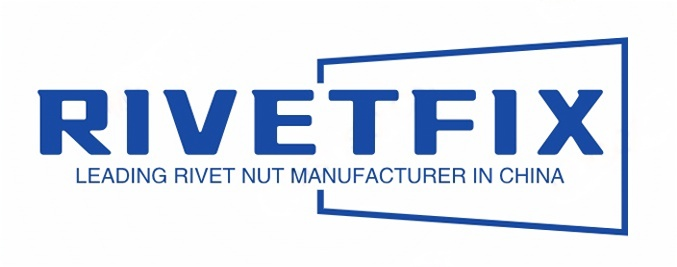
Select Rivetfix for Your Next Project Endeavor
As a leading fastener manufacturer in China with more than 15 years in the industry, we are committed to providing first-class quality fasteners and responsive services to the world.
Our factory manufactures 400 million pieces of structural rivets and automobile blind rivets, 1 billion standard blind rivets annually now. We can select the most suitable fasteners according to your project needs, and provide product customization services. Choose Rivetfix for your next project and experience the difference that superior rivet nut solutions can make.
Contact us for project advice and the latest rivet nut quote!
Get High Quality Rivet Nuts Quote!
Send Your Rivet Nut Request
For more than 20 years, Rivetfix has helped customers solve many rivet nuts sourcing needs and technical challenges.
Have a question? Contact us and we’ll provide you with the perfect solution.