How to Choose the Right Rivet Nuts for Plastic and Composites?
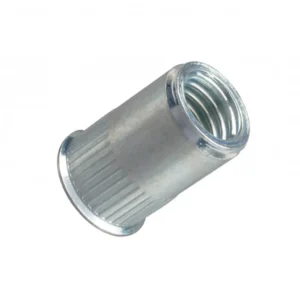
Leading Rivet Nut Manufacturer and Supplier in China
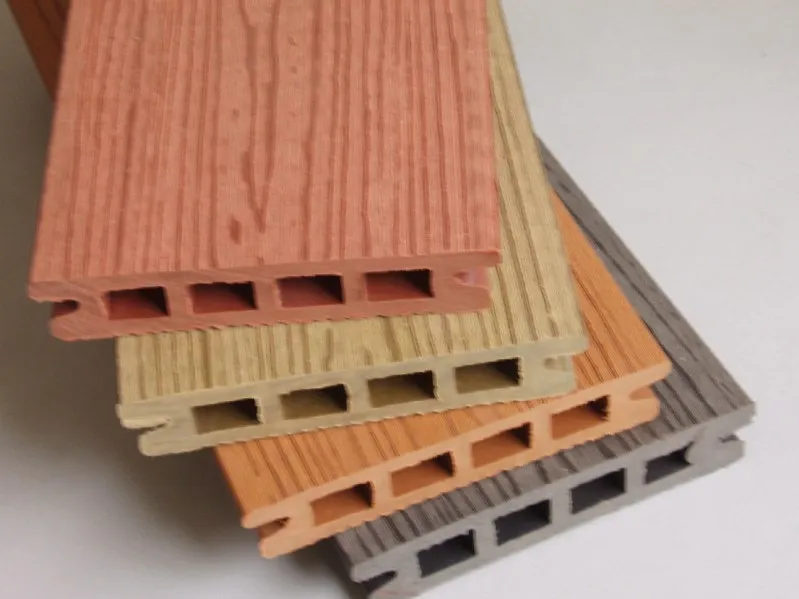
Choosing the right rivet nuts for plastic and composites materials is crucial for ensuring secure and durable connections. In this blog, we will explore key factors to consider when selecting rivet nuts for plastic and composites, from material compatibility to load capacity and installation techniques. By understanding these aspects, you can make informed decisions and ensure the success of your projects.
Table of Contents
Tips of Riveting Plastic and Composites
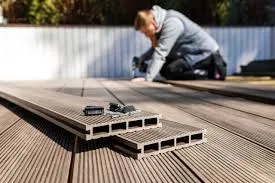
Choose the right rivet nut type
For lightweight or brittle materials like plastic and composites, aluminum rivet nuts are commonly recommended due to their light weight, ease of installation, and relatively gentle expansion force. These rivet nuts create strong and reliable threaded connections without causing damage to fragile materials. Additionally, copper rivet nuts are also a good choice for softer materials as they are softer than steel, providing a secure grip without excessive force that could crack the material.
Furthermore, plastic rivet nuts are specifically designed for use in plastic and composite materials. They are often used in applications where a non-metallic solution is preferred, and they provide excellent resistance to corrosion.
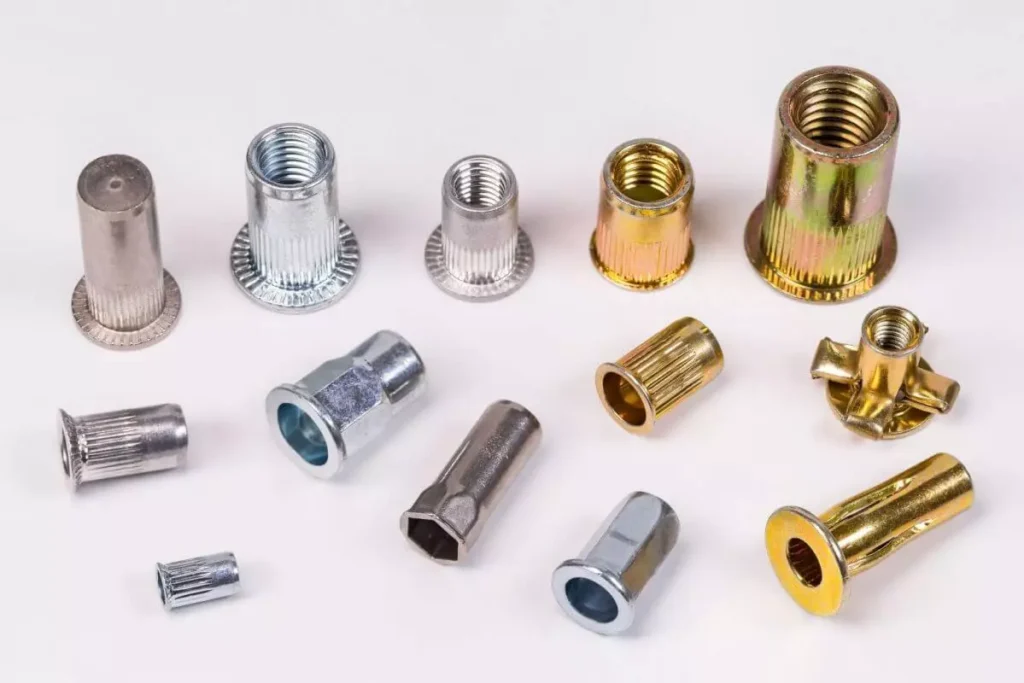
Ensure the correct hole size
Ensuring the correct hole size is crucial when installing rivet nuts in plastic or composite materials to avoid material damage and ensure a secure fit. If the hole is too large, the rivet nut may not expand properly, leading to a loose or ineffective connection. On the other hand, if the hole is too small, excessive force is required to install the rivet nut, which can cause the material to crack or deform.
Recommended Hole Sizes for Different Rivet Nuts:
- M3 Rivet Nut: Hole diameter should be 5.2 – 5.5 mm
- M4 Rivet Nut: Hole diameter should be 6.4 – 6.8 mm
- M5 Rivet Nut: Hole diameter should be 7.3 – 7.7 mm
- M6 Rivet Nut: Hole diameter should be 8.3 – 8.7 mm
- M8 Rivet Nut: Hole diameter should be 10.3 – 10.7 mm
Apply controlled expansion force
When installing rivet nuts in plastic or composite materials, applying controlled expansion force is essential to prevent cracking or deformation.
Recommended Expansion Force Guidelines for Rivet Nuts:
- Aluminum Rivet Nuts:
- Expansion force range: 500 – 1,000 N (Newtons)
- Ideal for softer materials like plastic or composites.
- Steel Rivet Nuts:
- Expansion force range: 1,000 – 2,000 N
- Better suited for harder composites or thicker plastics, offering more strength.
- Stainless Steel Rivet Nuts:
- Expansion force range: 1,500 – 3,000 N
- Excellent for high-stress environments or materials with higher tensile strength, such as certain reinforced plastics.
Advantages of Rivet Nuts for Plastic and Composites
1. No Need for Thread Tapping
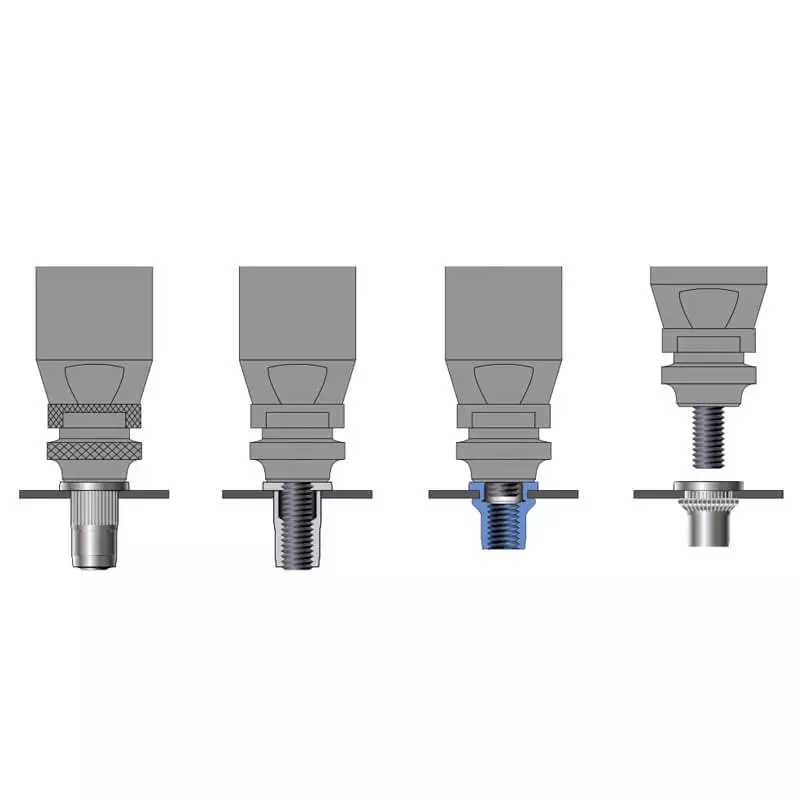
Rivet nuts eliminate the need for tapping threads directly into plastic or composites, which are often too brittle to hold traditional threads. This makes installation easier and faster.
Saves Time and Labor:
With rivet nuts, there’s no need for the time-consuming process of manually tapping threads into materials, which can be particularly challenging in materials like fiberglass or soft metals. The rivet nut installation process is quick and easy, saving valuable time and reducing labor costs.
Prevents Material Weakening:
Tapping threads directly into thin or brittle materials like plastic, composites, or soft metals can cause the material to weaken. Rivet nuts, on the other hand, create a secure internal thread without cutting into the base material, preserving its integrity and strength.
2. Strong and Secure Connections
Rivet nuts create a robust and reliable threaded connection, even in lightweight or brittle materials, ensuring that fasteners such as screws or bolts remain securely attached.
High Rivet Nut Strength:
Rivet nuts, particularly those made from steel or stainless steel, are capable of withstanding high tensile strength and shear forces. This makes them ideal for applications that require strong, durable connections, such as in automotive, aerospace, and industrial machinery.
Resistant to Vibration and Impact:
Rivet nuts provide excellent resistance to vibration and impact forces. Once installed, their expansion inside the base material ensures they are securely locked in place, preventing loosening or shifting, even under continuous movement or stress.
3. Even Load Distribution
Rivet nuts expand inside the material, distributing the load evenly across the surface. It reducing the risk of stress fractures or cracks that could occur with point loads.
Even load distribution reduces the risk of material deformation or damage, especially in softer materials like plastic or thin metals. By spreading the load, rivet nuts prevent indentation or weakening of the material around the fastener.
4. Easy Installation
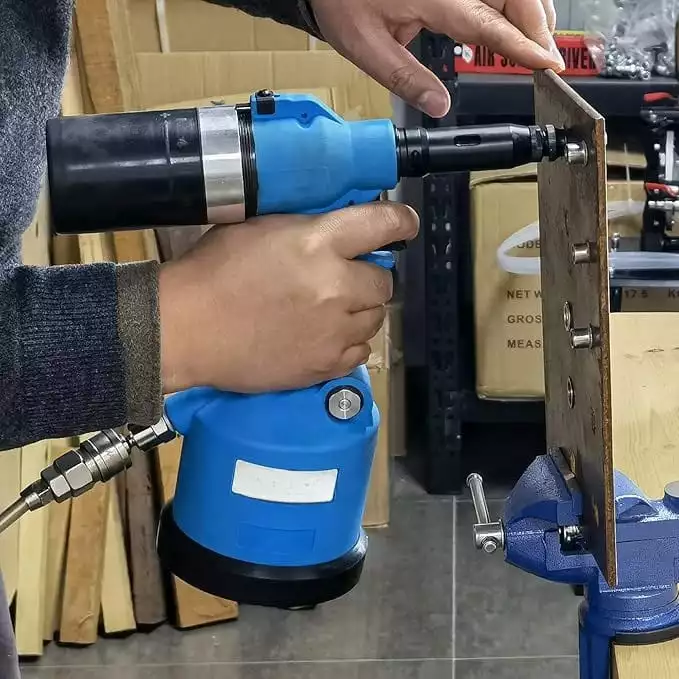
Single-Sided Installation:
Rivet nuts can be installed from one side of the material, eliminating the need to access both sides of the workpiece. This makes them ideal for applications in hard-to-reach areas or situations where one side is inaccessible.
No Need for Thread Cutting:
Unlike traditional tapping, rivet nuts do not require the material to be threaded. This simplifies the process, reduces setup time, and eliminates the risk of damaging the material during threading.
Variety of Installation Tools:
Rivet nuts can be installed with manual, pneumatic, or hydraulic tools, providing flexibility depending on the required force and the material thickness.
Consistent and Reliable Results:
Once installed, rivet nuts provide a secure and durable threaded insert, ensuring reliable connections every time. Many rivet nut gun tools provide you with mounting solutions.
5. Aesthetic Appeal
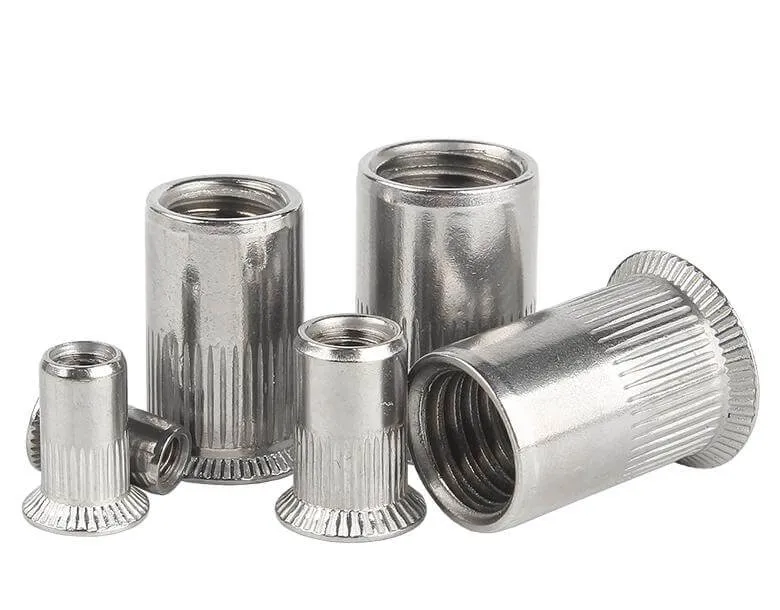
Countersunk rivet nuts have many aesthetic advantages due to their unique design, especially for applications requiring a flat, smooth surface.
This type of rivet nuts are designed not only to meet the functional requirements, but also to enhance the overall beauty of the product. Countersunk rivet nuts have a tapered head that, when installed, is completely flush with the surface of the material, providing a smooth, protruding appearance.
This makes them particularly suitable for industries that require a high level of appearance, such as automotive interiors, electronic casings, and high-end furniture. Its conical head can also be combined with smooth surface treatments, such as anodizing, chrome plating, etc., to enhance the modern feel and sophistication of the product.
Do You Have Any Questions?
Let Us Solve Your Problem
Rivet Nuts Work on Plastic Materials
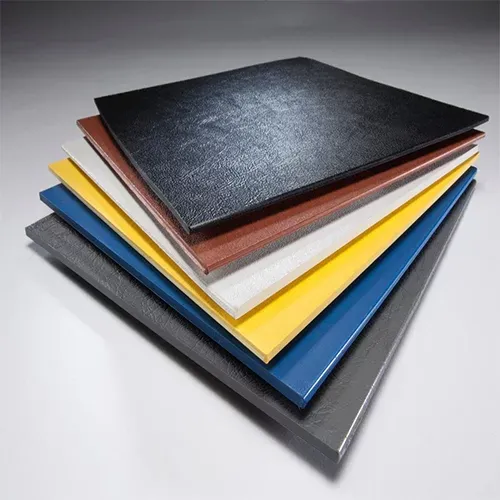
1. Load Capacity
Rivet nuts in plastic materials typically have a lower load-bearing capacity compared to metals, but the strength can vary based on the type of plastic.
For example, plastic materials like ABS or Nylon can handle load capacities of 200 to 500 N (Newtons), while tougher materials like Polycarbonate or Polyethylene may support higher loads, up to 700 N.
2. Insertion Force
Rivet nuts expand by applying radial force. In plastics, it’s crucial to use the correct insertion force to avoid cracking.
The ideal insertion force for rivet nuts in plastic is typically between 300 to 500 N, depending on the type of plastic and the rivet nut size.
3. Hole Size
The hole diameter should match the rivet nut size. For example, if you’re using a M6 rivet nut, the hole diameter should be approximately 6.2-6.3 mm for optimal performance in plastic.
4. Material Thickness
For materials like acrylic or PVC, the plastic thickness should generally be between 2 mm to 6 mm to ensure proper installation of rivet nuts without causing cracking or deformation.
5. Expansion Efficiency
Plastics, especially fiberglass or composite materials, can have lower tensile strength. Rivet nuts work best when the plastic is thick enough to allow for proper expansion.
A thickness of 3 mm to 5 mm is usually recommended for secure rivet nut installation.
Rivet Nuts Work on Composite Materials
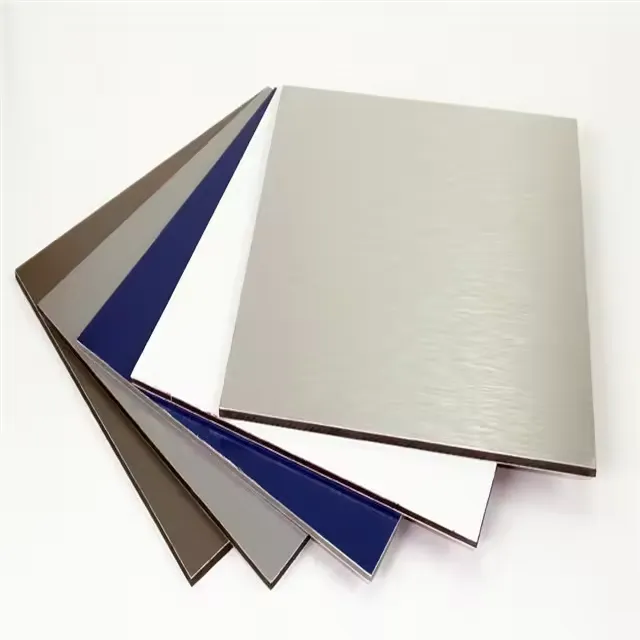
1. Load Capacity
The load capacity of rivet nuts in composite materials is crucial due to their lower tensile strength compared to metals. Composite materials like carbon fiber or fiberglass typically require rivet nuts with a load capacity ranging from 500–1,500 N. This ensures the rivet nut can support the expected loads without causing material failure or excessive stress concentrations.
2. Insertion Force
The insertion force for rivet nuts in composites must be controlled to prevent damage such as cracking or delamination. The typical insertion force required for composite materials ranges between 0.8–1.5 tons (800–1,500 kg), depending on the size of the rivet nut. Using tools that provide adjustable force helps ensure that excessive force is not applied, which could compromise the integrity of the composite material.
3. Hole Size
To ensure proper expansion without damaging the material, the hole size for rivet nuts must be precise. A typical hole tolerance for composite materials should be within ±0.1 mm.
The recommended hole size depends on the rivet nut’s size, usually ranging from M3 to M12, with slight adjustments to accommodate smooth and controlled expansion.
4. Material Thickness
The thickness of the composite material impacts the effectiveness of the rivet nut. Generally, composite materials with a thickness between 3–8 mm are ideal for rivet nuts. If the material is too thin, it may not hold the rivet nut securely, while excessive thickness could require additional force or a larger rivet nut to achieve a reliable connection.
5. Expansion Efficiency
Expansion efficiency is critical for ensuring that the rivet nut forms a secure connection without damaging the composite. The ideal expansion efficiency for rivet nuts in composite materials should be between 90–95%, which ensures uniform expansion across the entire rivet nut. Proper expansion helps distribute the load evenly and prevents excessive stress on the surrounding material, reducing the risk of cracking or delamination.
Understanding the Distinctions: Rivet Nuts in Plastic vs. Composite Materials
Comparison Item | Plastic Materials | Composite Materials |
Material Properties | Softer, prone to deformation, and more susceptible to cracking under stress. | Harder, higher strength, but more brittle and prone to local stress impact. |
Expansion Force Requirement | Low expansion force, typically ≤0.5 tons, to avoid material cracking. | Higher expansion force, typically ≤1.5 tons, ensuring even pressure distribution. |
Installation Method | Requires controlled expansion force, using low-expansion-force tools (e.g., jack nuts). | Can use standard rivet nuts, but precise force control is necessary to avoid excess pressure. |
Material Preparation | Proper hole size is essential, avoiding excessive heat or friction. | Special attention is needed for hole preparation and layer integrity. |
Installation Tools | Manual or pneumatic tools (with precise force control) | High-precision tools to ensure even expansion force and avoid cracks. |
Summary:
- Plastic Materials: Rivet nuts need to have an expansion force controlled to below 0.5 tons and use low-expansion-force tools like jack nuts to avoid cracking or deformation of the plastic.
Composite Materials: Although the expansion force can be slightly higher, typically ≤1.5 tons, careful attention must be paid to ensure even pressure distribution to prevent cracks or delamination.
What is the Best Rivet Nut for Plastic and Composites?
When choosing Rivet Nuts for plastics, Jack Nuts are usually more suitable than ordinary rivet nuts. Here’s how the two compare:
1. Structural design differences
Rivet nuts: Usually have a large outside diameter and a thick edge to provide a strong grip in metal materials. In plastics, due to the softness and brittleness of plastics, the shape of standard rivet nuts may cause the material to crack or fail, especially in high load or vibration environments.
Jack nuts : Usually have thin edges in design, with special compression structure. Their expansion force is more controllable and suitable for use in fragile materials such as plastics. Jack rivet nuts provide strong fixation without damaging the plastic.
2. Applicability
Rivet Nuts: Suitable for thicker metal materials but not ideal for materials that are prone to cracking or deformation, such as plastics. Standard rivet nuts require a higher expansion force, which could damage thinner or more fragile plastics.
Jack Nuts: Specifically designed for soft materials like plastic and composites. They work well with lower expansion forces, minimizing material damage. Additionally, their design allows for secure connections when installed from one side, making them perfect for plastic applications.
3. Installation Process
Rivet Nuts: Typically require a higher installation force, which might be too intense for plastic materials, potentially causing cracks or deformation.
Jack Nuts: With controlled expansion force, they are better suited for plastic, avoiding excessive stress concentration. Therefore, they are ideal for applications where strong connections need to be formed on plastic.
4. Application Scenarios
- Rivet Nuts: Primarily used in metal sheet materials, steel, and other hard materials, and are not suitable for plastics.
- Jack Nuts: Widely used in applications like electronics, automotive interiors, furniture, and other fields where strong, long-lasting fastening is needed on plastic.
Conclusion
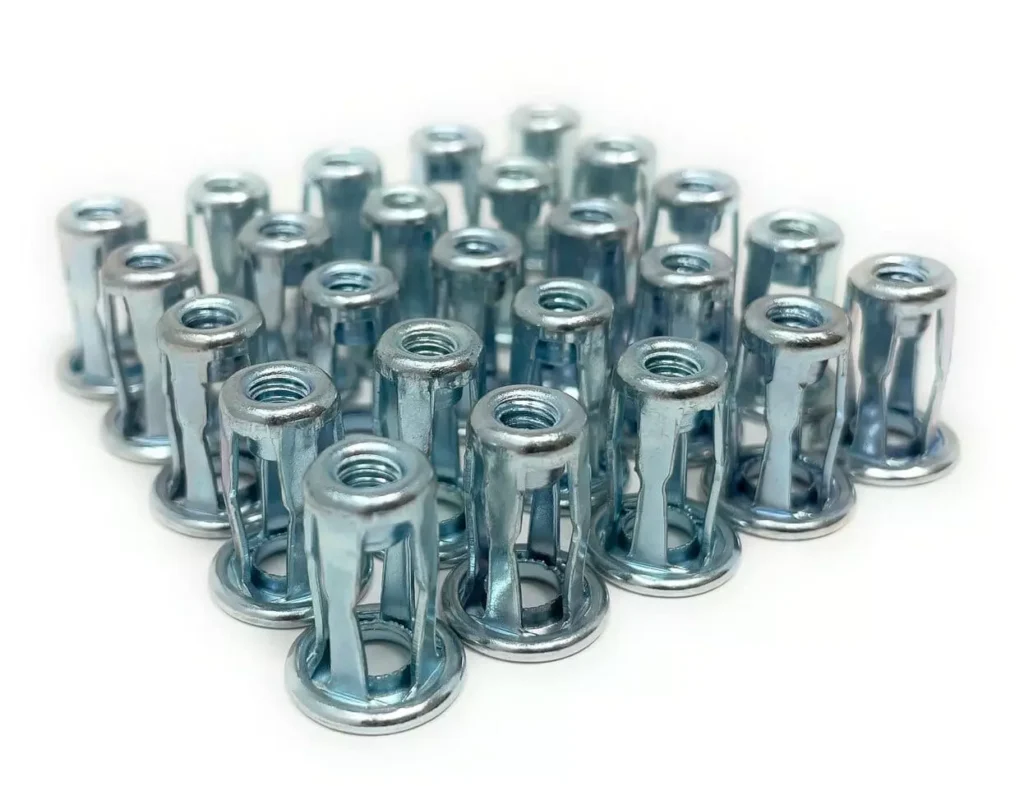
For plastic materials, buying jack nuts are undoubtedly the better choice.
The advantage of this type of rivet nut lies in its ability to function with lower expansion forces, which helps prevent the damage that traditional rivet nuts might cause to fragile plastics during installation. By controlling the expansion force, jack nuts achieve uniform pressure distribution, thus reducing the risk of cracks or deformation in the plastic due to excessive localized stress.
Moreover, jack nuts require minimal processing of the plastic during installation, which reduces the potential for material damage and ensures a strong, durable connection. This makes them an ideal solution for applications where both strength and the integrity of the plastic material must be maintained.
Do You Have Any Questions?
Let Us Solve Your Problem
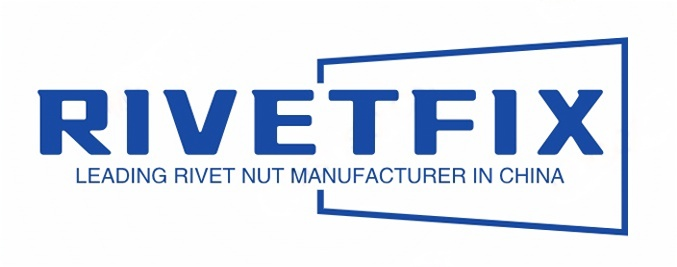
Rivetfix is your trusted partner for premium rivet nut solutions, offering a wide range of high-quality fasteners designed to elevate your projects. Whether you’re working with sheet metal, plastic, or other materials, our rivet nuts provide durable, reliable, and easy-to-install threaded connections.
We offer a comprehensive range of fasteners tailored to meet the unique requirements of your projects. With our customization services, we can design and deliver the ideal solution to suit your specific fastening needs. Committed to quality and customer satisfaction, we ensure that every product we provide enhances the security, efficiency, and durability of your projects, making them built to last.
Contact us for project advice and the latest rivet nut quote!
Get High Quality Rivet Nuts Quote!
Send Your Rivet Nut Request
For more than 20 years, Rivetfix has helped customers solve many rivet nuts sourcing needs and technical challenges.
Have a question? Contact us and we’ll provide you with the perfect solution.