How to Choose Jack Nuts for Sheet Metal?
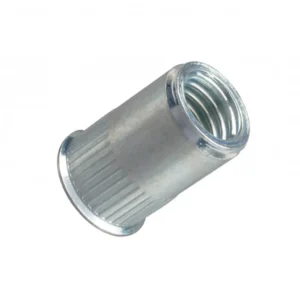
Leading Rivet Nut Manufacturer and Supplier in China
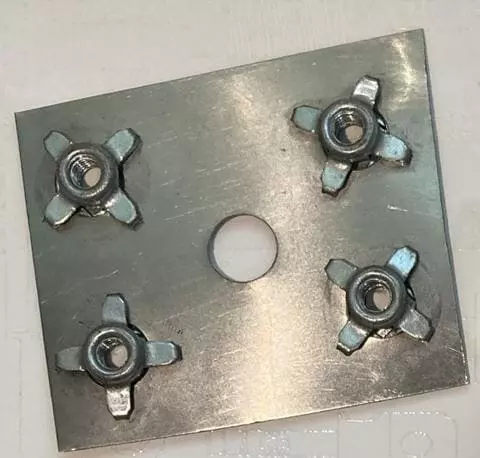
Jack nuts for sheet metal provide versatile, vibration-resistant fastening in blind applications—but choosing the wrong type risks corrosion, loosening, or structural failure. This guide simplifies material compatibility, load ratings, and installation best practices to help you optimize durability and performance for automotive, HVAC, or DIY projects.
Table of Contents
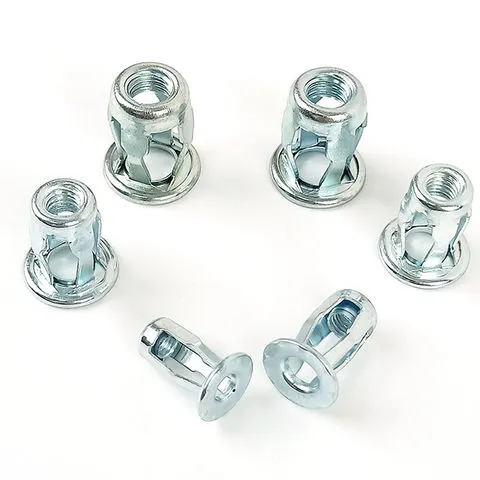
Definition
Jack Nuts are an expandable fastener specifically designed for thin-walled or soft materials such as plastic, fiberglass, and thin metal. Their structure consists of a threaded sleeve and four expansion legs that spread outward when installed, creating a secure anchor point. This design allows them to provide a reliable threaded connection in materials where the backside is inaccessible, making them ideal for blind installation.
Jack Nuts are primarily used in applications that require a threaded connection on thin-walled or soft materials, especially where standard nuts or weld nuts cannot be used.
Common uses include:
- Providing a removable threaded connection, allowing screws to be installed and removed multiple times without damaging the base material.
- Strengthening thin-walled materials by ensuring a secure grip where standard bolts or screws may not provide sufficient clamping force.
- Enabling blind installation, making them suitable for applications where the back side of the material cannot be accessed, such as tubing and enclosed profiles.
- Performing well in vibration-prone environments, as their expansion mechanism offers better resistance to loosening compared to standard nuts.
Key Benefits of Jack Nuts
- Compatible with soft and thin-walled materials, including plastic, fiberglass, aluminum, and thin steel sheets, without compromising structural integrity.
- Supports blind installation, requiring access to only one side of the material, making them ideal for tubing, enclosed profiles, and similar applications.
- Easy to install, using a standard screwdriver or manual tools, eliminating the need for welding or specialized riveting equipment.
- Removable and reusable, allowing screws to be taken out for maintenance or part replacement after the nut is installed.
- Distributes stress effectively, reducing material damage by spreading the load through the expansion legs, preventing localized stress cracks.
Main Applications of Jack Nuts
Jack Nuts are widely used across various industries, including:
- Automotive industry, for securing interior panels, wire brackets, and vehicle body attachments.
- Household appliances, for fastening components in washing machines, refrigerators, ovens, and internal assemblies.
- Aerospace and marine industries, for installing cabin panels, lightweight metal frames, and fiberglass structures.
- Furniture and DIY projects, for reinforcing cabinet installations, garage doors, and plastic or metal frame assemblies.
With their unique expansion-based fastening mechanism, Jack Nuts provide an ideal solution for applications requiring blind installation or secure fastening in soft materials.
Why Choose Jack Nuts Over Other Fastening Methods?
Comparative Analysis
When selecting a fastening solution, different options offer distinct advantages and limitations. Below is a comparison of Jack Nuts with other common fastening methods:
- Similarities: Both are designed for blind installations and provide a threaded insert for screws or bolts.
- Differences: Jack Nuts are better suited for soft materials like plastic and fiberglass, whereas rivet nuts primarily work on metal.
Weld Nut vs. Jack Nuts:
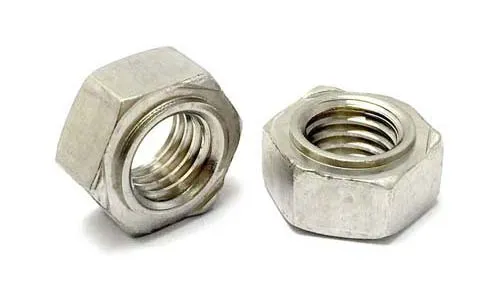
- Similarities: Both create a permanent threaded connection.
- Differences: Weld nuts require welding equipment, making installation more complex and costly. Jack Nuts, on the other hand, require no heat or special tools and can be used on non-metal materials like plastics and composites.
Bolt/Stud & Screw vs. Jack Nuts:
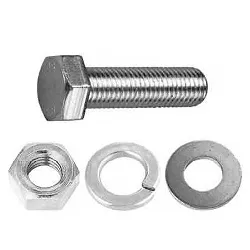
- Similarities: Both provide fastening solutions in various applications.
- Differences: Standard bolts and screws require a material thick enough to support tapped threads or through-hole fastening with a nut. Jack Nuts create secure threads even in thin or soft materials, where direct threading may not work.
- Similarities: Both are used for blind installations and provide vibration resistance.
- Differences: Well nuts, made of rubber with a brass insert, rely on compression to hold the insert in place. While they provide good vibration dampening, they may not offer the same mechanical strength as Jack Nuts, which form a rigid metal anchor on the material’s backside.
Table 1 :Jack Nuts vs. Other Fastening Methods
Feature | Jack Nut | Rivet Nut | Weld Nut | Bolt/Stud & Screw | Well Nut |
Best for | Soft & thin materials | Metal materials | Metal structures | Thick materials | Soft materials |
Blind Installation | Yes | Yes | No | No | Yes |
Special Tools Needed | No | Yes | Yes (Welding) | No | No |
Reusable Thread | Yes | Yes | No | Yes | No |
Material Compatibility | Metal, plastic, fiberglass | Metal only | Metal only | Various (depends on thickness) | Plastic, fiberglass, metal |
Vibration Resistance | Moderate | Moderate | High | Low | High |
Ease of Installation | Easy | Moderate | Difficult | Easy | Easy |
Jack Nuts stand out due to their ease of installation, material versatility, and ability to create strong threads in soft or thin materials. Compared to alternatives, they provide a cost-effective and practical solution for many fastening applications.
Do You Have Any Questions?
Let Us Solve Your Problem
How to Choose Jack Nuts for Sheet Metal?
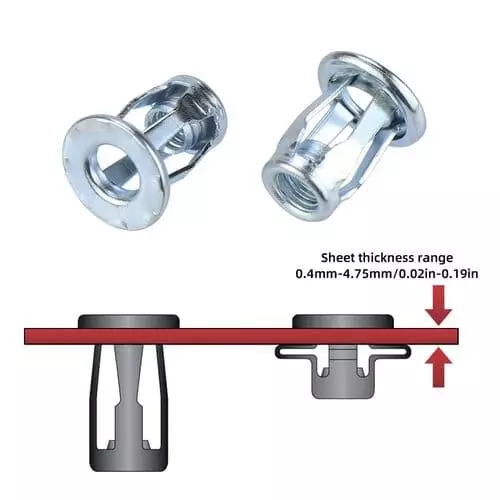
a. Material Selection: What Types of Sheet Metal Are Suitable for Different Jack Nut Materials?
The material selection of Jack Nuts must match the sheet metal material, the working environment, and corrosion resistance requirements, while also avoiding electrochemical galvanic corrosion caused by dissimilar metals in contact. Below are the common pairing recommendations:
1. Stainless Steel Jack Nut
Suitable Sheet Metal Materials:
- Stainless Steel Sheet (304/316): 304 stainless steel (general-purpose) is suitable for common corrosive environments, while 316 stainless steel, with its molybdenum content, offers better resistance to chloride corrosion and is ideal for marine or chemical industries.
- Galvanized Steel: The sacrificial anode property of the zinc coating helps delay corrosion of the underlying steel. When paired with stainless steel Jack Nuts, ensure that the contact surface remains dry.
- Aluminum: Caution Required: Direct contact between stainless steel and aluminum accelerates aluminum oxidation due to electrochemical corrosion, especially in humid environments.
Applications:
- Humid, salt-spray environments (e.g., outdoor equipment, marine engineering).
- High-strength and corrosion-resistant applications (e.g., automotive undercarriages, industrial equipment).
Note:
For aluminum alloys, using stainless steel Jack Nuts can lead to corrosion of the aluminum (due to the electrochemical difference), so it’s advisable to use insulating washers or select aluminum Jack Nuts for such applications.
2. Aluminum Jack Nut
Suitable Sheet Metal Materials:
- Aluminum Alloy Sheets: Suitable for common alloys such as 6061-T6 and 5052 (lightweight and good workability).
- Thin Steel Sheets (lightweight applications): Such as 0.8-1.2mm low-carbon steel (requires pairing with aluminum screws for corrosion resistance).
Applications:
- Lightweight structures with low load requirements (e.g., drone frames, electronic heat sink enclosures).
- Applications requiring electrical conductivity (e.g., shielding in electrical devices).
Note:
Due to the lower hardness of aluminum, frequent vibrations may cause thread wear. It should not be used for load-bearing or frequently disassembled applications.
3. Zinc-Plated Steel Jack Nut
Suitable Sheet Metal Materials:
- Cold-Rolled Steel Sheets: SPCC/DC01 steel (low cost, should be coated with paint for rust protection).
- Galvanized Steel: Hot-dip galvanized (Zinc ≥150g/m²) or electro-galvanized (Zinc ≥20g/m²), providing double protection when paired with galvanized Jack Nuts.
- Painted Sheet Metal: Ensure the pre-drilled hole edges are free from paint to prevent the coating from peeling off with the galvanized layer.
Applications:
- Dry indoor environments (e.g., furniture assembly, internal cabinet fixation).
- Low-cost, non-critical connections (e.g., DIY tool racks).
Note:
Galvanized layers can corrode if scratched, so avoid using them in humid or water-exposed environments.
b. Size Matching: How to Determine the Size of Jack Nuts for Sheet Metal?
Key Parameters and Matching Guidelines
1. Sheet Metal Thickness:
- The overall length of the Jack Nut should be slightly greater than the sheet metal thickness (recommended 1-2mm overrun) to ensure proper expansion and engagement with the sheet metal during installation.
- Example: For a 2mm sheet metal, select a Jack Nut with an overall length of 3-4mm.
2. Thread Specifications (Internal Threads):
- The internal thread of the Jack Nut should match the corresponding bolt/screw specification, with common standards being metric (e.g., M4, M5) and imperial (e.g., 1/4″-20).
- Key Point:
- The bolt length should extend through the sheet metal and have sufficient engagement depth (at least 2 times the thread diameter).=
3. Outer Sleeve Diameter and Pre-Drilled Hole Match:
The outer diameter of the Jack Nut determines the required pre-drilled hole size. The hole diameter should generally match the nominal outer diameter of the Jack Nut, with an error margin of ±0.1mm.
4. Practical Example:
Electronic Equipment Enclosure (Aluminum 1.5mm thick): Select an aluminum Jack Nut (overall length 3mm, outer diameter 6.35mm, internal thread M4), paired with an M4×8mm stainless steel screw.
c. Load Capacity: How to Choose Jack Nuts Based on Load Requirements?
The load capacity of a Jack Nut is determined by the material strength, thread size, and installation quality. Key evaluations should focus on two types of loads:
1. Static Loads
- Axial tension or pressure perpendicular to the sheet metal (e.g., hanging heavy objects).
- Selection Criteria:
- Stainless Steel Jack Nuts: Provide the highest static load capacity (e.g., M6 stainless steel Jack Nut can withstand 200-300kg of tension).
- Aluminum Jack Nuts: Suitable for light loads (under 100kg).
- Zinc-Plated Steel Jack Nuts: Medium strength (150-200kg), but vulnerable to environmental factors.
2. Dynamic Loads
- Vibration, impact, or cyclical loads (e.g., automotive components, sports equipment).
- Selection Criteria:
- Prioritize Jack Nuts with self-locking threads (e.g., Nylock insert threads).
- Materials must have high fatigue resistance: Stainless Steel > Carbon Steel > Aluminum.
- Example: For electrical brackets in the engine compartment, select 316 stainless steel Jack Nuts (resistant to vibration and high temperature).
3. Safety Factor and Testing
- Manufacturer-rated load capacities are typically based on ideal conditions. In actual applications, it’s advisable to apply a safety factor (recommended 1.5-2 times).
- Example: If the actual load is 50kg, select a Jack Nut rated for ≥75kg.
- Safety Recommendations:
- Critical connections should undergo physical load testing (e.g., using a torque wrench and pressure sensors for verification).
- Avoid single-point load-bearing; distribute loads across multiple Jack Nuts.
Summary: Selection Flowchart
- Determine Sheet Metal Material and Thickness → 2. Match Jack Nut Material and Size → 3. Calculate Load Requirements and Select Strength Level → 4. Verify Pre-Drilled Hole Dimensions → 5. Test Samples Before Mass Use.
How to Buy Jack Nuts?
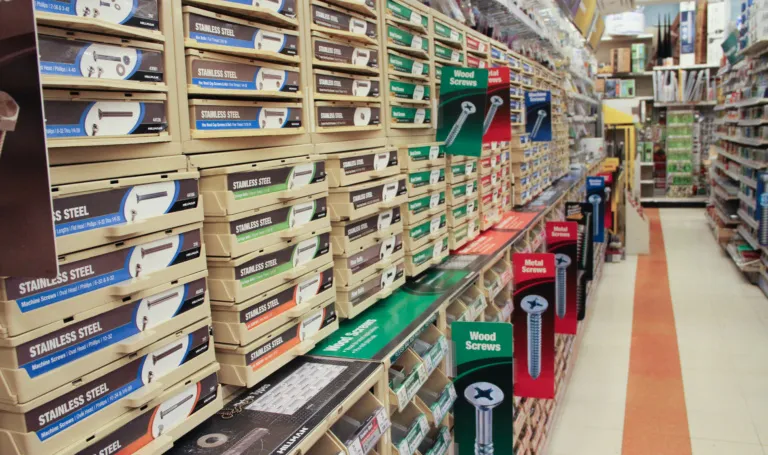
Directly Contact Manufacturers:
- Advantages: Allows for customized services where you can select materials, sizes, thread specifications, etc., based on your specific needs.
- Ideal for long-term or bulk purchases, establishing a stable supply relationship with the manufacturer.
Through Distributors or Agents:
- Advantages: Usually has ready stock and shorter delivery times, suitable for small batch purchases or emergency needs.
- Ideal for retailers, wholesalers, or projects requiring fast supply.
Online Platforms or E-commerce Websites:
- Advantages: Convenient, transparent pricing, and allows for multi-party comparison and direct ordering.
- Suitable for one-time small batch purchases or projects sensitive to quality and price.
Local Hardware Stores or Fastener Shops:
- Advantages: Allows on-site product inspection and quality confirmation, ideal for urgent needs.
- Suitable for small businesses or individual DIY projects.
2. Key Factors for Choosing a Jack Nut Supplier
1. Quality Certifications:
- Prefer suppliers certified with ISO 9001 (Quality Management System), ISO 14001 (Environmental Management), or DIN (German Standards).
- Require material reports (e.g., SGS testing) and salt spray test data (e.g., galvanized products should meet 500 hours of neutral salt spray with no red rust).
2. Product Variety:
- Includes different materials (stainless steel, aluminum, carbon steel), sizes (M3-M12), and surface treatments (galvanized, Dacromet, passivation).
- Check if the supplier can offer customized services to meet specific project needs.
3. Technical Support:
Suppliers should provide selection guides, installation manuals, or on-site engineering consultations (e.g., Rivetfix’s free technical support services).
4. Delivery and Supply Chain Stability:
- Ensure the supplier has stable production capabilities and a record of on-time deliveries. Choose a supplier with short and reliable delivery cycles to avoid project delays.
- Confirm stock lead times in advance (e.g., standard products within 7 days, custom products 15-30 days), and assess their ability to handle sudden demand.
- For long-term projects, evaluate the supplier’s inventory management and logistics capabilities.
5. Price and Cost:
- Compare prices from different suppliers to ensure the selected supplier’s prices are reasonable and in line with market standards.
- Balance quality and price, avoiding sacrificing product quality for lower prices.
- Compare unit prices, minimum order quantities (MOQ), and tiered pricing, while being cautious of hidden costs (e.g., tariffs or extra shipping fees).
3. Recommended Jack Nut Suppliers
1. Rivetfix (China):
Rivetfix is a leading Jack Nut supplier in China, offering a wide range of Jack Nuts with strong production capabilities and custom services. Their products are used in industries such as automotive, home appliances, and furniture, with high-quality inspection reports and certificates.
2. Bollhoff (Germany):
Bollhoff is a globally renowned fastener solutions provider, offering high-quality Jack Nuts and other fastening products, with extensive experience and technical support. Their products are widely used in automotive, aerospace, and electronics industries.
3. Gesipa (Germany):
Gesipa provides high-quality Jack Nuts and has strong global supply capabilities. Gesipa’s products are widely used in mechanical manufacturing, automotive, electronics, and industrial equipment.
4. SWG (Switzerland):
SWG is a specialized supplier of high-quality fasteners with years of experience. Their products offer excellent corrosion resistance and load-bearing capacity, suitable for a variety of industries.
5. Tox Pressotechnik (Germany):
Tox Pressotechnik is known for its innovative fastening technology and high-quality products, earning a good reputation in the industry. Their Jack Nut products are widely used in automated production lines, automotive manufacturing, and heavy industry.
Do You Have Any Questions?
Let Us Solve Your Problem
FAQs - How to Choose Jack Nuts for Sheet Metal
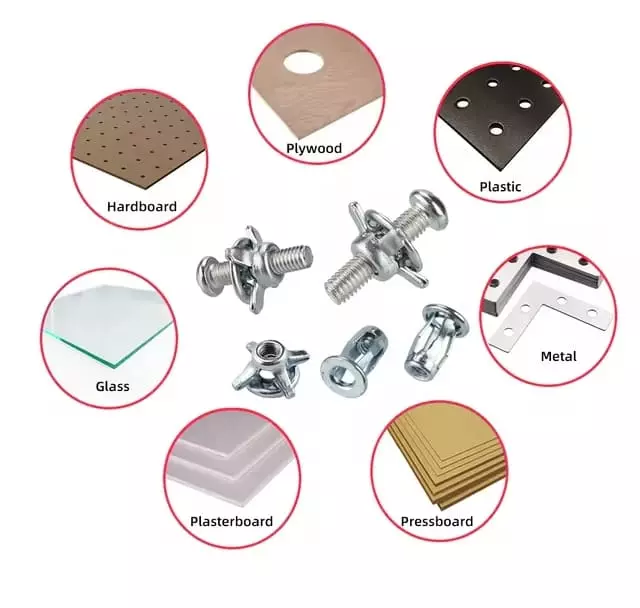
1. What types of sheet metal are Jack Nuts suitable for?
Jack Nuts are suitable for thin-walled or soft materials such as aluminum alloy, cold-rolled steel, galvanized steel, plastic, and fiberglass. Their design allows them to provide strong threaded connections on these materials.
2. How to choose the right size of Jack Nuts?
When selecting Jack Nuts, the first step is to determine the sheet metal thickness. The total length of the Jack Nut should be slightly larger than the sheet metal thickness, usually 1-2mm longer. Additionally, the outer diameter should match the size of the pre-drilled hole to ensure proper installation.
3. How to choose the material for Jack Nuts?
The material for Jack Nuts should be chosen based on the sheet metal material, the environment, and corrosion requirements. For example, 304 stainless steel is suitable for general environments, 316 stainless steel is ideal for humid and marine environments, and aluminum Jack Nuts are best for lightweight structures and weight reduction needs.
4. How are Jack Nuts installed?
The installation of Jack Nuts is relatively simple. You only need to use hand tools or a screwdriver to install them into pre-drilled holes. During installation, the expansion legs of the Jack Nut will spread outward, securing it firmly to the material and creating a stable threaded connection.
5. What is the load capacity of Jack Nuts?
The load capacity of Jack Nuts is influenced by the material type, thread size, and installation quality. Generally, stainless steel Jack Nuts have higher load-bearing capacities and are suitable for high-load environments, while aluminum Jack Nuts are designed for lighter loads. When choosing, it’s important to select based on the specific load requirements.
Buy Jack Nuts from Rivetfix
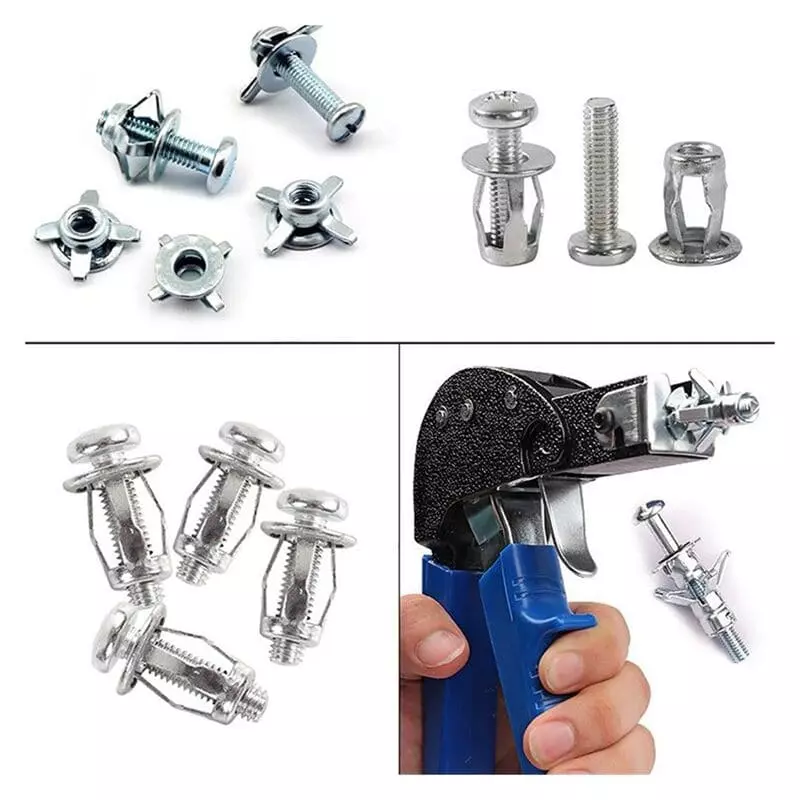
Rivetfix, as a leading jack nut supplier in China, offers high-quality products designed to meet various industrial and commercial needs. With competitive pricing, reliable delivery, and a range of customizable options, Rivetfix is committed to providing efficient solutions for clients worldwide.
We are committed to providing first-class quality fasteners and responsive services to the world. We can select the most suitable fasteners according to your project needs, and provide product customization services.
Contact us for project advice and the latest jack nut quote!
Get High Quality Rivet Nuts Quote!
Send Your Rivet Nut Request
For more than 20 years, Rivetfix has helped customers solve many rivet nuts sourcing needs and technical challenges.
Have a question? Contact us and we’ll provide you with the perfect solution.