The Ultimate Guide to Buying Rivet Nuts
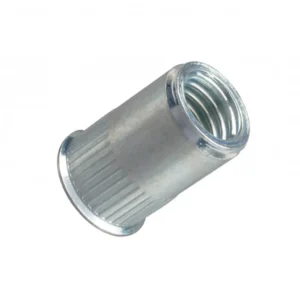
Leading Rivet Nut Manufacturer and Supplier in China
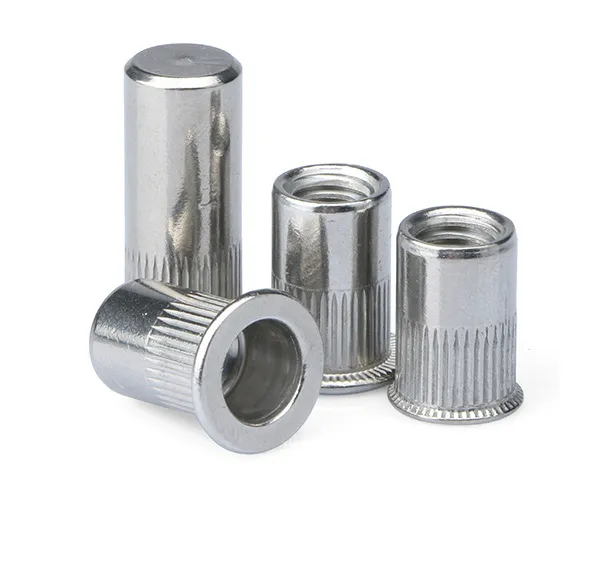
Looking for the perfect rivet nuts for your project? This ultimate guide to buying rivet nuts will help you choose the right type, material, and size for your application. Whether you’re working with thin sheet metal or thick composites, our expert tips will ensure you make the best choice for durability and strength.
Table of Contents
What Are Rivet Nuts?
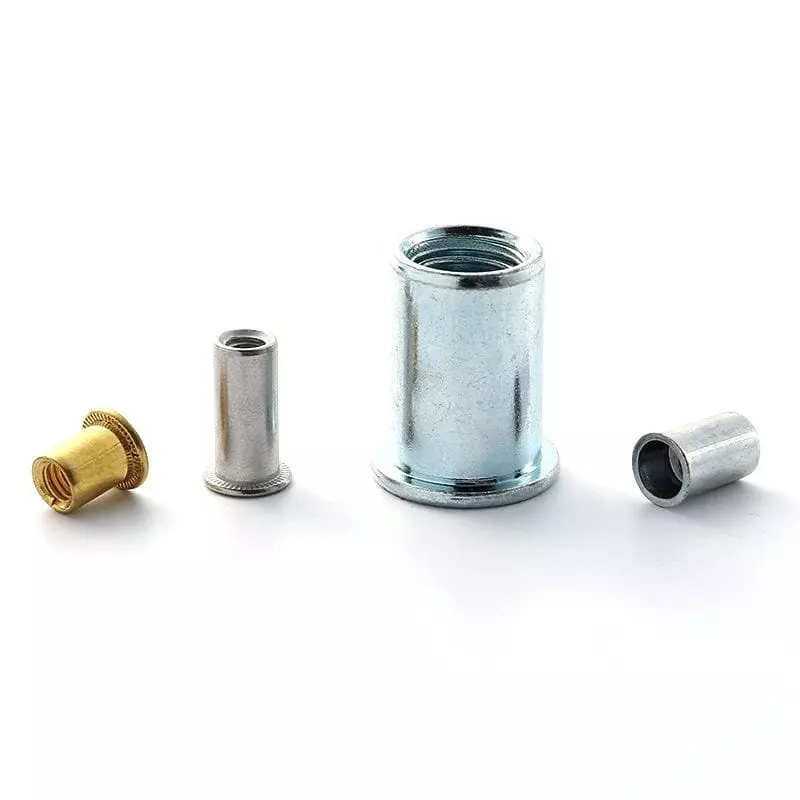
Rivet Nuts are hollow fasteners made of metals (e.g., aluminum, steel, stainless steel) featuring internal threading. Installed using tools like manual or pneumatic rivet guns, they are compressed into pre-drilled holes in thin materials (metal, plastic), where the tail expands to form a permanent connection while providing robust threaded support. Compared to welding or bolting, rivet nuts enable quick, removable threaded interfaces on fragile or thin materials without heat or specialized equipment.
Applications: Common types include flat-head, countersunk, and flanged designs, ideal for sheet metal fabrication, automotive assembly, aerospace, and electronics. Key advantages include vibration resistance, corrosion durability, and compatibility with automated installation, making them essential for lightweight material joining in modern industries.
What Types of Rivet Nuts Are Available?
a. Material Types
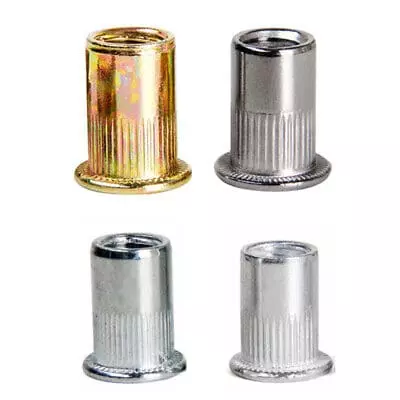
- Features: Steel rivet nuts are made from carbon steel, offering strength and durability. They are often coated with zinc or other protective layers to prevent corrosion. These rivet nuts are commonly used in applications requiring high load-bearing capacity.
- Advantages: Steel rivet nuts provide excellent strength and load-bearing capabilities, making them ideal for structural applications. They are also relatively cost-effective, making them a popular choice for mass-produced projects.
- Disadvantages: While steel is strong, it is more susceptible to corrosion compared to stainless steel or aluminum unless properly coated. Steel rivet nuts are also heavier, which may not be ideal for weight-sensitive applications.
- Features: Stainless steel rivet nuts are highly resistant to corrosion, making them perfect for harsh environments such as marine or chemical industries. Available in grades such as 304 or 316, they offer both strength and rust resistance.
- Advantages: Stainless steel rivet nuts are ideal for outdoor applications or areas exposed to moisture or chemicals. They are highly durable and can withstand high temperatures, ensuring long-term reliability in extreme environments.
- Disadvantages: The primary downside of stainless steel rivet nuts is their cost. They tend to be more expensive than other materials like steel or aluminum. Additionally, they can be more challenging to install due to their hardness.
- Features: Aluminum rivet nuts are lightweight, corrosion-resistant, and easy to install. They are commonly used in industries where weight reduction is crucial, such as aerospace and automotive applications.
- Advantages: Aluminum rivet nuts are lightweight, which reduces the overall weight of the finished product. They also offer good corrosion resistance, making them suitable for outdoor applications where rust might be a concern.
- Disadvantages: Although aluminum rivet nuts are lightweight and corrosion-resistant, they have lower strength than steel or stainless steel. This makes them less ideal for applications that require heavy load-bearing capacity.
- Features: Copper rivet nuts provide excellent electrical conductivity, making them ideal for electrical applications. They are also corrosion-resistant, though they are often used in specific scenarios where conductivity and corrosion resistance are more critical than strength.
- Advantages: Copper rivet nuts are highly conductive, making them perfect for applications like electrical connections or components in sensitive electronics. They are also corrosion-resistant, especially in environments where the metal might be exposed to moisture.
- Disadvantages: Copper rivet nuts are generally softer and less durable than steel or stainless steel, meaning they are not suitable for high-stress applications. They are also more expensive than other materials.
b. Head Types
- Features: Countersunk head rivet nuts have a conical shape that allows the nut to sit flush with the surface of the material. This head type is often used in applications where a smooth, even surface is needed for aesthetic or functional reasons.
- Advantages: Countersunk head rivet nuts provide a clean, flush finish, making them ideal for applications where a smooth surface is required, such as automotive or aerospace industries. They also minimize protrusion, which is important for tight spaces.
- Disadvantages: These rivet nuts require precise installation to ensure proper alignment and depth. If the countersunk hole is not made accurately, the rivet nut may not sit flush, leading to poor installation and weak connections.
- Features: The flat head of a rivet nut features a broad, level surface that provides a larger contact area with the material. This design is commonly used in applications where a wide bearing surface is needed to distribute the load.
- Advantages: Flat head rivet nuts are easier to install compared to countersunk heads and are suitable for applications that require even pressure distribution. They are also more forgiving in terms of alignment, making installation simpler.
- Disadvantages: Flat head rivet nuts may protrude from the surface of the material, which could be an issue in applications requiring a flush finish. Their larger surface area might not be ideal for applications with strict space limitations.
- Features: Reduced head rivet nuts have a smaller diameter head compared to flat-head rivet nuts. They are designed to minimize the protrusion above the surface, making them ideal for applications with limited space.
- Advantages: These rivet nuts are ideal when space is constrained, as the reduced head minimizes protrusion. They are also more aesthetically pleasing for applications where a smaller, less noticeable fastener is desired.
- Disadvantages: While they reduce protrusion, reduced head rivet nuts provide a smaller contact surface area, which may not distribute the load as effectively as a flat head. This makes them less suitable for high-stress applications.
c. Body Types
- Features: The hexagonal body of a rivet nut provides additional grip and resistance to rotation during installation. This design is especially beneficial when the nut needs to withstand high torque or pressure in its final application.
- Advantages: Hex body rivet nuts offer superior torque resistance and prevent rotation during installation, making them ideal for use in high-stress or high-torque applications. They are also suitable for thicker materials where more gripping power is needed.
- Disadvantages: The hex body design requires more space compared to round body rivet nuts, and may be harder to install in thin materials due to its larger footprint. It also may not be as aesthetically pleasing as round body rivet nuts for certain applications.
- Features: Round body rivet nuts have a simple cylindrical shape, making them easy to install and versatile in a wide range of applications. The rounded shape offers a clean, smooth appearance when installed.
- Advantages: Round body rivet nuts are easy to install and require less space than hex body rivet nuts. They are suitable for general-purpose applications where load-bearing requirements are not extremely high.
- Disadvantages: Round body rivet nuts do not offer the same level of torque resistance as hex body rivet nuts. In applications where high torque is a concern, the round body design may allow the nut to rotate during installation or use.
- Features: Knurled body rivet nuts have textured ridges on their surface that enhance their grip in materials, preventing them from rotating during installation. This design is particularly useful when the material is softer or more prone to slippage.
- Advantages: The knurled design improves the grip of the rivet nut, preventing rotation during installation, especially in softer or more flexible materials. This makes them a reliable choice for materials that might otherwise allow the nut to spin.
- Disadvantages: The installation of knurled body rivet nuts requires precise alignment to ensure the ridges properly grip the material. They may not be ideal for use in hard, rigid materials where the knurled surface could be less effective.
How Do Different Types of Rivet Nuts Compare?
1. Material Comparison
Type | Characteristics | Advantages | Ideal Applications |
---|---|---|---|
Steel | High strength, cost-effective | Heavy-duty load capacity | Construction, machinery |
Stainless Steel | Corrosion-resistant, durable | Suits harsh environments (salt, moisture) | Marine, chemical industries |
Aluminum | Lightweight, moderate strength | Weight-sensitive assemblies, non-magnetic | Aerospace, electronics |
Copper | High thermal/electrical conductivity | Conductive interfaces, heat dissipation | Electrical systems, HVAC |
2. Head Type Comparison
Type | Installation & Features | Key Benefits |
---|---|---|
Countersunk Head | Flush finish with pre-drilled chamfered holes | Aerodynamic/smooth surfaces (e.g., aircraft) |
Flat Head | Simple round profile for generic use | Versatile for flat sheet metal (e.g., appliances) |
Reduced Head | Compact design with smaller head diameter | Space-constrained or thin materials (e.g., PCBs) |
3. Body Type Comparison
Type | Structural Features | Performance Advantages |
---|---|---|
Hex Body | Six-sided body resists rotation | High torque resistance (e.g., automotive parts) |
Round Body | Smooth cylindrical design | Easy installation in standard holes |
Knurled Body | Textured surface for enhanced grip | Prevents loosening in soft materials (plastics) |
Key Performance Factors
- Strength vs. Weight: Steel > Stainless Steel > Aluminum > Copper.
- Corrosion Resistance: Stainless Steel > Aluminum > Copper > Steel (uncoated).
- Installation Complexity: Hex body > Knurled body > Round body.
- Cost: Copper > Stainless Steel > Steel > Aluminum.
Do You Have Any Questions?
Let Us Solve Your Problem
How to Determine Compatibility with Your Materials?
1. Understand the Material You Are Working With
- Metal (Aluminum, Steel, Stainless Steel): Rivet nuts are commonly used in metals, especially when you need a secure threaded insert in thin or thick metal sheets. Steel and stainless steel rivet nuts are ideal for high-strength applications, while aluminum rivet nuts are lighter and corrosion-resistant.
- Plastic or Composites: When using rivet nuts for plastics, choose materials that won’t cause damage to the plastic surface during installation. Composite materials, such as fiberglass or carbon fiber, require a careful choice of nut. In fact, for soft and lightweight materials, Jack nuts are the best choice. Because they’re designed for soft materials.
2. Consider the Material Thickness
- Thin Materials(0.5 mm to 3 mm), such as thin aluminum sheets or plastic panels, you’ll need rivet nuts that provide a strong attachment without distorting the material. In this case, low-profile rivet nuts like flat head or reduced head are often the best choices. These types of rivet nuts minimize the chance of deforming the material and offer a smooth finish when installed.
- Thick Materials(thicker than 6 mm) , such as structural steel or thick composite panels, you need a rivet nut that can penetrate deeply enough to provide a secure hold without damaging the material. Hex body rivet nuts are also suitable here, but you may need to use longer rivet nuts to accommodate the increased thickness. Additionally, for very thick materials, knurled body rivet nuts may be necessary for better retention and resistance to rotation under load.
3. Load Requirements and Material Strength
The strength of the material should influence the rivet nut you select. For higher strength requirements:
- Steel Rivet Nuts: They are ideal for applications that will experience high stresses or heavy loads, such as in automotive, structural, or machinery applications.
- Stainless Steel Rivet Nuts: They are perfect for environments exposed to moisture, chemicals, or extreme temperatures, where corrosion resistance and strength are paramount.
- Aluminum Rivet Nuts: Although they are not as strong as steel, aluminum rivet nuts provide sufficient strength for lighter loads while offering significant weight savings in aerospace or automotive applications.
4. Environmental Conditions
- Corrosion Resistance: If your application involves exposure to moisture, chemicals, or outdoor elements, corrosion-resistant materials like stainless steel and aluminum rivet nuts are the best choices.
- Temperature Considerations: High temperatures can affect the performance of certain materials. Stainless steel is more heat-resistant than aluminum or brass, making it the best choice for applications in high-temperature environments.
- Vibration and Shock Resistance: Materials prone to vibration or shock should use rivet nuts designed for such conditions, like hex or knurled body rivet nuts, as they offer better grip and resistance to loosening under stress.
5. Size and Type of Rivet Nut
- Head Types: Ensure the head type of the rivet nut suits the surface you’re working with. For flush, smooth finishes, use countersunk head rivet nuts. For general-purpose applications, flat-head rivet nuts work well, while reduced head rivet nuts are ideal for tight spaces.
- Body Types: For materials that require extra grip, knurled body rivet nuts are ideal as they prevent rotation during installation. For standard applications, round body rivet nuts offer a clean and simple solution.
6. Installation Process and Tools
Choosing the right rivet nut based on the material also involves considering the tools needed for installation. Ensure that your installation tools, such as hand tools, pneumatic tools, or hydraulic presses, are compatible with the rivet nut you plan to use. For softer materials like plastic, you might require a lower installation force and specific tools designed for delicate surfaces.
How to Maintain Your Rivet Nuts?
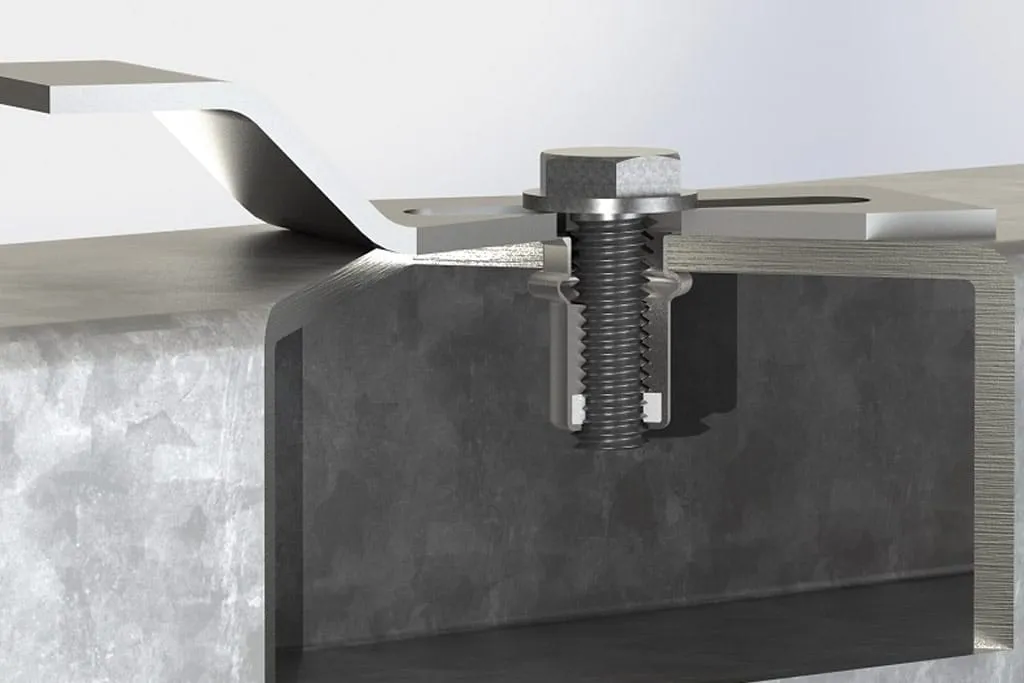
Proper maintenance ensures rivet nuts retain their functionality and longevity. Below are essential steps and tips:
1. Regular Inspection
- Periodically inspect rivet nuts for signs of wear, corrosion, or loosening. Look for any signs of rust or damage, especially in environments where moisture or chemicals are present. Inspect the surrounding material for any deformations or cracks around the rivet nut.
2. Proper Tightening
- Ensure rivet nuts are tightened correctly, as over-tightening or under-tightening can affect their performance. Over-tightening can damage the surrounding material or strip the threads, while under-tightening may cause the rivet nut to loosen over time.
3. Avoid Overloading
- Never exceed the recommended load limits of the rivet nuts. Overloading can cause the rivet nut to fail or loosen, compromising the integrity of the fastening.
4. Corrosion Prevention
- For rivet nuts used in harsh environments (e.g., outdoor or marine settings), consider using corrosion-resistant materials like stainless steel or applying a protective coating to prevent rust or corrosion.
5. Cleanliness
- Keep the area around the rivet nuts clean. Dirt, debris, and contaminants can interfere with the proper functioning and threading of the nut. Use a soft cloth and mild detergent to clean the area without damaging the material or threads.
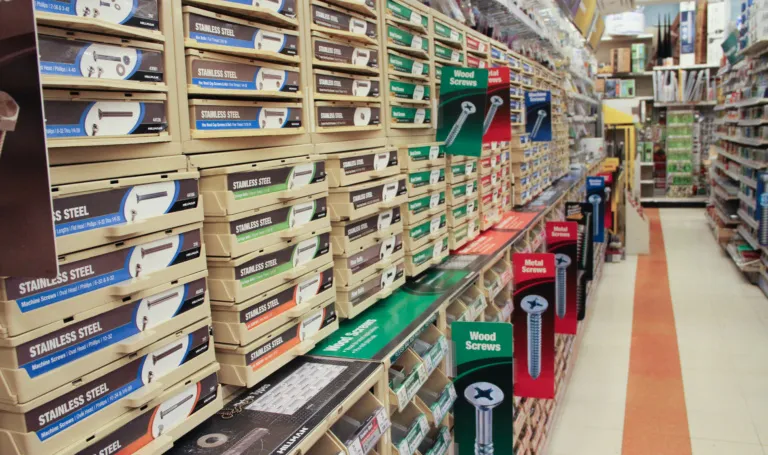
1. Offline Fastener Stores
- Pros: Immediate purchase, expert advice, hands-on inspection.
- Ideal For: Urgent replacements or small quantities (e.g., hardware stores like Fastenal).
2. Online Retail Marketplaces
- Pros: Wide selection, price comparison, bulk discounts (e.g., Amazon, Alibaba).
- Ideal For: Standard sizes, cost-sensitive buyers.
3. Specialized Rivet Nut Suppliers
- Pros: Customization, technical support, high-quality brands (e.g., Böllhoff, Rivetfix).
- Ideal For: Industrial needs, tailored solutions, or unique materials.
What Are Some Common Brands of Rivet Nuts to Consider?
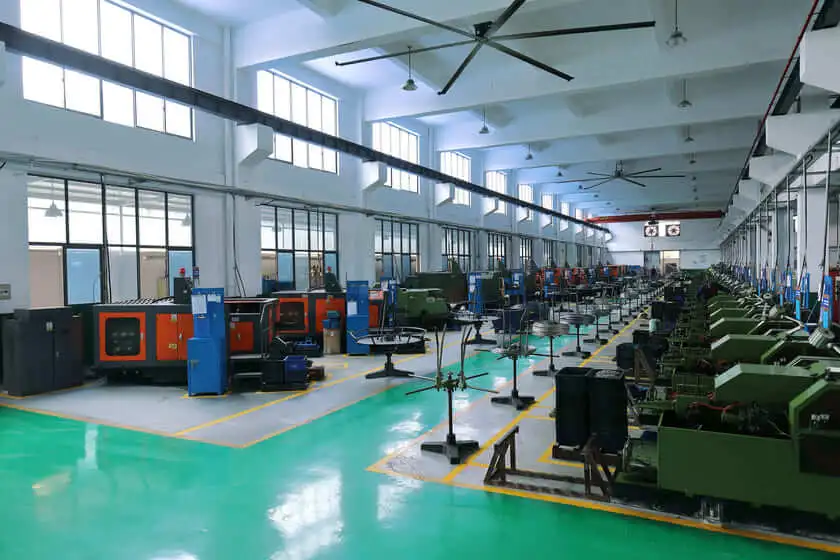
- Focus: Global leader in engineered fastening solutions.
- Benefits: Comprehensive product range (steel, stainless steel, aluminum) for industrial heavy-duty applications.
PEM® is a registered trademark of PennEngineering.
- Focus: Benchmark in sheet metal fastening technology.
- Benefits: Expertise in micro-sized rivet nuts (e.g., below M3) for precision electronics assembly.
- Focus: Top choice for aerospace and automotive industries.
- Benefits: Lightweight designs and resistance to extreme environments (heat/vibration).
4. Marson
- Focus: Cost-effective tools and consumables.
- Benefits: Compatibility with manual/pneumatic tools; ideal for small-to-medium workshops.
5. Rivetfix 🌟 (Your Brand Highlight)
- Focus: Innovator in fast installation and multi-scenario adaptability.
- Benefits:
- Tailored solutions (anti-corrosion coatings, specialized head designs).
- Competitive pricing with support for small-batch custom orders.
- Fast technical support and tool compatibility guidance.
Key Recommendation: For projects prioritizing cost-efficiency, flexibility, and localized support, Rivetfix balances quality and efficiency seamlessly.
If you want to know more about rivet nut manufacturers, you can refer to the following blogs:
Guide to Buying Rivet Nuts- FAQs
Q1: Can I reuse rivet nuts?
Permanent Deformation:
- During installation, the rivet nut’s tail expands and deforms to lock into the material. This process is irreversible.
- Attempting removal damages the nut’s structure, threads, and host material.
Exceptions:
- Non-Deformed Designs: Some specialty rivet nuts (e.g., screw-in types) allow limited reuse, but standard variants do not.
Replacement Protocol:
- Drill out the damaged nut and install a new one in a slightly offset hole (avoid overlapping weakened material).
Q2: Difference between rivet nuts and weld nuts?
Aspect | Rivet Nuts | Weld Nuts |
---|---|---|
Installation | Mechanical expansion (no heat) | Welding (heat required) |
Material Limits | Thin metals, plastics, composites | Thicker metals (≥2mm) |
Strength | Moderate (dependent on grip range) | Very high (fusion with base) |
Appearance | Smooth finish (flush heads) | Possible weld marks/discoloration |
Removability | Non-removable (single-use) | Permanent (grinding required) |
Q3: How to prevent loosening?
- Thread Locking Methods
- Adhesives:
- Low-strength (e.g., Loctite 222): For occasional disassembly.
- High-strength (e.g., Loctite 271): Permanent bonding.
- Mechanical Locking:
- Nylon-insert nuts or spring washers (e.g., Nord-Lock).
- Adhesives:
- Design Features
- Hex Body Nuts: Resist rotation under vibration (ideal for automotive engines).
- Knurled Body: Bites into soft materials (plastics, fiberglass).
- In-Process Control
- Use a calibrated torque wrench to ensure proper preload.
- Follow manufacturer’s torque specs to avoid under/over-tightening.
Have More Questions?
Let Us Solve Your Problem
Why Choose Rivetfix
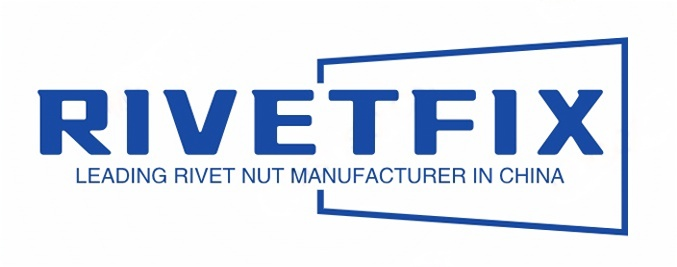
As a leading fastener manufacturer in China with more than 15 years in the industry, Rivetfix are committed to providing first-class quality fasteners and responsive services to the world.
Rivetfix offers a wide range of rivet nuts designed to meet the unique demands of your projects. With options like countersunk, flat, and hex heads, as well as knurled and round body types, Rivetfix ensures you have the right solution for every application. Choose Rivetfix for versatile, cost-effective, and durable fastening solutions tailored to your specific needs. In addition, we can also provide customized rivet nuts service according to your requirements.
Contact us for project advice and the latest rivet nut quote!
Get High Quality Rivet Nuts Quote!
- Characteristics: High strength, wear resistance, and cost-effective.
- Advantages: Ideal for heavy-duty applications (e.g., machinery, construction).
- Limitations: Prone to corrosion; requires protective coatings (e.g., galvanization).
Send Your Rivet Nut Request
For more than 20 years, Rivetfix has helped customers solve many rivet nuts sourcing needs and technical challenges.
Have a question? Contact us and we’ll provide you with the perfect solution.