Exploring the Variations and Benefits of Rivet Nuts
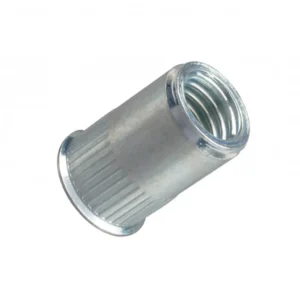
Leading Rivet Nut Manufacturer and Supplier in China
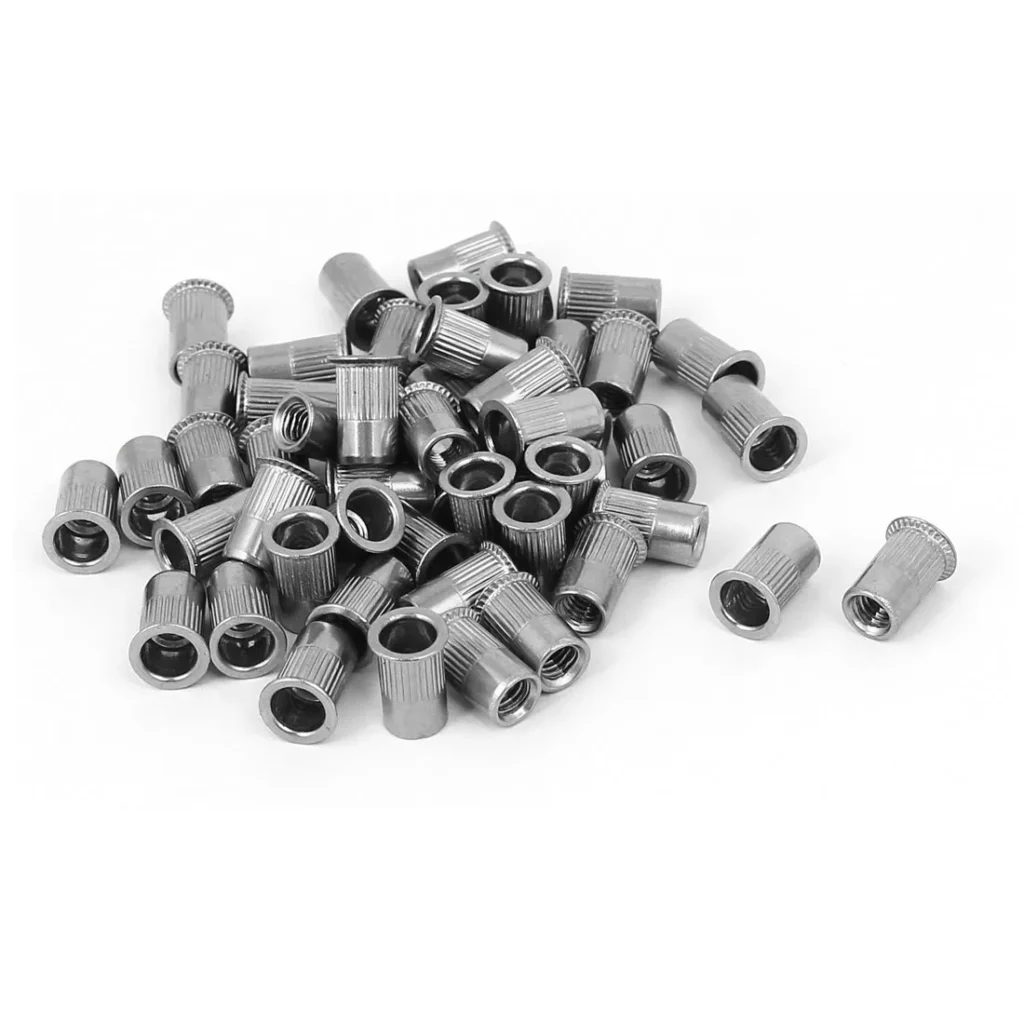
Rivet nuts are essential fasteners used across various industries, offering a reliable and versatile solution for securing materials with ease. Understanding the different variations available, from head styles to body types, can significantly enhance the performance and efficiency of your projects. In this blog, we’ll explore the variations and benefits of rivet nuts, highlighting their advantages in terms of strength, installation ease, and cost-effectiveness. Whether for thin materials or heavy-duty applications, rivet nuts provide a durable fastening solution.
Table of Contents
What Are the Benefits and Applications of Different Rivet Nut Head Types?
Benefits
a. Flush Surface Finish:
Countersunk head rivet nuts are designed to sit flush with the surface of the material, creating a smooth, even finish. This is especially important when aesthetics and functionality must align. The countersunk design allows the rivet nut to integrate seamlessly into the material, ensuring a clean, flat surface.
- A countersunk head typically features an angle between 82° to 90°, matching standard countersunk drill bits to create a flush finish.
- This flush finish is particularly beneficial in applications where aerodynamics or visual appeal is critical, such as in aerospace or automotive industries.
b. Aesthetic Appeal:
The countersunk head provides a sleek, low-profile look, making it ideal for visible or consumer-facing applications. It ensures a more professional and polished appearance, reducing the visual impact of hardware.
- In automotive or furniture design, where visual appeal is crucial, countersunk rivet nuts help reduce protrusion by up to 50% compared to standard head rivet nuts, enhancing the overall design quality.
c. Prevents Snagging:
The countersunk head is recessed, preventing any protrusions that could catch on clothing or other materials, which is particularly important in environments where safety and ergonomics are a concern.
- Studies show that a countersunk head can reduce snagging risks by up to 75% in environments like wearable equipment, sports gear, or medical devices.
d. High Load Distribution:
The countersunk design allows the load to be distributed more evenly over a larger surface area, enhancing the rivet nut’s ability to handle heavy-duty applications. This is particularly beneficial in high-torque or high-load scenarios, where material integrity is critical.
- Countersunk rivet nuts typically have a higher load distribution efficiency (up to 20-30% more evenly distributed) than standard head rivet nuts. This allows them to support higher tensile and shear strength, making them suitable for high-strength steel or aluminum materials used in heavy-duty manufacturing.
Application Scenarios
- Automotive and Aerospace – Used in areas where flush installation is required to improve aerodynamics and prevent air resistance. Common in aircraft fuselages, car body panels, and interior fittings.
- Electronics and Enclosures – Ideal for mounting components inside electronic devices, cabinets, or enclosures where space is limited and a smooth surface is necessary.
- Furniture and Cabinetry – Used in wood and composite materials for a clean, flush look while maintaining a strong fastening point.
Benefits
a. Larger Bearing Surface:
The flat head design of rivet nuts provides a wider contact area with the base material. This increased bearing surface improves the load distribution and helps prevent the material from deforming under stress, particularly in softer materials.
- A flat head rivet nut offers up to 40% more surface area compared to a standard dome-shaped head, resulting in reduced stress concentration on the material.
- For example, in aluminum or plastic applications, the flat head design can significantly reduce the risk of material crushing or deforming under high load or torque.
b. Increased Holding Strength:
The larger bearing surface allows for better holding strength, making flat head rivet nuts suitable for high-torque and high-load applications. The increased surface area helps distribute the force more evenly, resulting in a more secure and durable connection.
- Flat head rivet nuts typically provide up to 25% higher holding strength than standard head rivet nuts, especially in applications involving high-tensile materials or dynamic loads.
- For instance, M10 flat head rivet nuts can withstand shear forces up to 30% greater than comparable standard head rivet nuts in automotive applications where vibration and high torque are prevalent.
c. Versatile Installation:
The flat head design is ideal for a range of installation types, including applications where flush or nearly flush surfaces are needed. This versatility allows the rivet nut to be installed in both thick and thin materials with consistent results.
- Flat head rivet nuts can be installed in materials ranging from 0.8 mm to 10 mm in thickness, depending on the size and application, allowing for flexible use in various industrial and commercial sectors.
- In automotive and electronic enclosure assemblies, flat head rivet nuts enable quick and precise installation without requiring additional machining or surface preparation, reducing assembly time by up to 30%.
Application Scenarios
- Heavy Machinery and Construction – Frequently used in industrial machinery, frames, and structural components where strong and stable fastenings are required.
- Electrical Panels and Industrial Enclosures – Ensures secure mounting of electrical components, providing reliability and stability in high-vibration environments.
- Agricultural and Transportation Equipment – Common in tractors, trailers, and heavy-duty vehicles where durability is essential, even under harsh environmental conditions.
Benefits
a. Space Efficiency:
The reduced head design of rivet nuts allows for a more compact and space-saving solution. These rivet nuts are ideal for applications where space is limited, or where a low-profile fastener is required.
- Reduced head rivet nuts typically have up to 40% less head height compared to standard head rivet nuts. This reduction in height makes them ideal for installations in tight spaces, such as in aerospace, automotive interiors, or electronic devices.
b. Reduced Weight:
The smaller head size leads to a reduction in overall weight, which is particularly beneficial in industries where weight is a critical factor, such as in aerospace, automotive, or portable equipment.
- A reduced head rivet nut can weigh up to 30% less than a standard rivet nut, depending on the material used (e.g., steel, aluminum), making it a lightweight option without compromising on performance or load-bearing capacity.
- For example, in aircraft manufacturing, reducing the weight of individual components by even small margins can result in significant overall weight savings, contributing to better fuel efficiency.
c. Improved Aesthetics:
The reduced head provides a cleaner, more subtle appearance, making it suitable for applications where appearance matters. The minimal head protrusion reduces the visual impact of the fastener while still providing a strong connection.
- In consumer electronics or high-end appliances, where design and aesthetics are key, the reduced head rivet nuts offer a sleek, less intrusive appearance, blending seamlessly into the product while maintaining secure fastening performance.
d. Suitable for Thin-Walled Materials:
The reduced head design allows for installation in thinner materials without risking damage to the material’s surface. This makes them ideal for applications in sheet metal, plastic, or lightweight materials that need secure fastening without compromising the structural integrity.
- Reduced head rivet nuts are ideal for materials ranging from 0.5 mm to 3 mm thick, which makes them perfect for thin sheet metal applications such as electrical panels, enclosures, or even furniture construction where traditional fasteners might be too bulky.
Application Scenarios
- Automotive Interiors and Exteriors – Commonly used in dashboards, seats, and trim panels, where space constraints and lightweight materials require a discreet but strong fastening solution.
- Thin-Walled Tubing and Frames – Frequently used in bicycle frames, handrails, and metal enclosures where the fastener needs to fit within a limited space.
- Consumer Electronics and Appliances – Ideal for assembling small devices and appliances where traditional fasteners might be too bulky or intrusive.
Summary
Head Type | Advantages | Applications |
---|---|---|
Countersunk Head | Flush finish, prevents snagging, good load distribution | Automotive, aerospace, electronics, furniture |
Flat Head | Large bearing surface, high strength, prevents pull-through | Heavy machinery, electrical panels, transportation |
Reduced Head | Compact for tight spaces, minimizes material deformation, lightweight | Automotive interiors, tubing, consumer electronics |
Do You Have Any Questions?
Let Us Solve Your Problem
What Are the Advantages and Applications of Different Rivet Nut Body Types?
Benefits
a. High Resistance to Rotation:
The hexagonal shape of hex rivet nuts provides superior resistance to rotation, making them ideal for applications where the fastener needs to stay securely in place even under heavy load or vibration. The flat edges of the hex body interlock with the surrounding material, reducing the chance of slippage.
- Hex rivet nuts can offer up to 50% more resistance to rotation compared to round or flat-head rivet nuts, particularly in high-vibration environments like automotive or industrial machinery.
b. Increased Load Distribution:
The hexagonal body distributes the load more evenly across a wider surface area compared to traditional round rivet nuts. This reduces stress concentration on the material and enhances the overall durability of the connection.
- The larger surface area of the hex body can result in 20-30% better load distribution than round-bodied rivet nuts, improving their performance in applications with high shear and tensile stresses, such as in automotive chassis or structural supports.
c. Strong and Secure Fastening:
Hex rivet nuts provide a high level of mechanical strength, offering a more secure fastening solution in demanding applications. Their strong grip and increased resistance to loosening make them a top choice for high-stress and high-torque environments.
- Hex rivet nuts are known to provide up to 40% stronger fastening compared to round rivet nuts, particularly in environments where the connection will face repeated loading or torque, such as in heavy machinery or construction equipment.
d. Compatible with Pre-Punched Hexagonal Holes:
Hex rivet nuts are specifically designed to fit pre-punched hexagonal holes, simplifying the installation process and ensuring a more secure and precise fit. This compatibility allows for more efficient assembly, reducing time and material costs.
- Pre-punched hexagonal holes improve the installation efficiency by up to 25% compared to round holes, as there is less material deformation during insertion, making hex rivet nuts ideal for high-volume manufacturing applications in industries like automotive or electronics assembly.
Application Scenarios
- Automotive and Aerospace – Used in vehicle frames, aircraft panels, and structural components where strong, vibration-resistant fastening is required.
- Heavy Machinery and Equipment – Common in industrial applications where high torque and load-bearing capacity are necessary.
- Structural Steel and Metal Fabrication – Provides secure installation in thick and high-strength steel materials, preventing rotation during assembly.
Benefits
a. Easy Installation:
The simple cylindrical design of round rivet nuts makes them straightforward to install, requiring minimal effort for insertion into pre-drilled holes. This ease of use reduces installation time and increases efficiency.
- Round rivet nuts are known to reduce installation time by up to 30% compared to more complex designs, making them a favored choice in industries such as electronics assembly and consumer product manufacturing, where rapid assembly is essential.
b. Versatile Application:
Round rivet nuts can be used in a variety of materials, including metals (steel, aluminum), plastics, and composites. This versatility makes them suitable for a broad range of industries, from automotive to electronics to general manufacturing.
- Round rivet nuts are compatible with materials ranging from 0.5 mm to 12 mm thickness, providing flexibility for both lightweight and heavy-duty applications.
c. Cost-Effective Solution:
Due to their simple design and manufacturing process, round rivet nuts are typically more affordable than other types of rivet nuts, making them a cost-effective solution for many applications.
- Round rivet nuts can be up to 20-30% cheaper than more complex or specialized designs, making them the go-to option for high-volume, low-cost manufacturing in industries such as consumer electronics and appliance assembly.
Application Scenarios
- Consumer Electronics and Appliances – Commonly used in assembling devices where ease of installation is crucial.
- Sheet Metal Fabrication – Frequently used in light-duty applications such as electrical enclosures, ventilation systems, and HVAC units.
- General Manufacturing and Assembly – Ideal for non-critical connections in furniture, household items, and lightweight structures.
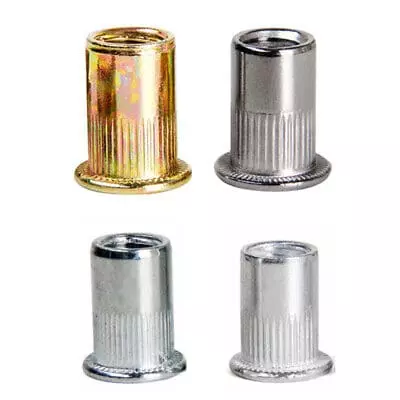
Benefits
a. Enhanced Grip and Anti-Rotation:
The knurled surface of these rivet nuts creates additional friction against the base material, significantly reducing the risk of the nut spinning inside the hole. This feature ensures a stronger and more secure connection.
- Knurled rivet nuts can provide up to 50% more anti-rotation resistance compared to smooth-surfaced rivet nuts, making them ideal for high-vibration or high-torque applications, such as in automotive assemblies and machinery maintenance.
b. Better Performance in Soft or Thin Materials:
The knurling provides extra gripping power, making these rivet nuts perfect for softer or thinner materials like aluminum, plastic, or composite materials, which might not hold traditional rivet nuts securely.
- Knurled rivet nuts are ideal for materials with thicknesses from 0.8 mm to 5 mm, providing superior grip compared to smooth round rivet nuts, which may not provide enough anchoring strength in these softer or thinner substrates.
c. Improved Torque Resistance Compared to Smooth Round Nuts:
Due to the increased friction from the knurled surface, knurled rivet nuts offer superior resistance to torque, making them better suited for applications exposed to movement, vibration, or dynamic loads.
- In dynamic environments, knurled rivet nuts offer up to 40% better torque resistance compared to smooth round rivet nuts, reducing the likelihood of loosening in applications like machinery housings or vehicle components.
d. Available in Various Head Styles:
Knurled rivet nuts come in multiple head styles, such as flush-mount and extended grip designs, allowing for customization based on the specific needs of the application, whether it’s a low-profile or high-grip requirement.
- The adaptability of knurled rivet nuts in head design means they can be used for applications where flush-mounting is essential (such as in aerospace and electronics), or when extended grip is required for additional holding power, like in automotive chassis or structural assemblies.
Application Scenarios
- Automotive Interior and Exterior Components – Used in dashboards, panels, and lightweight structures requiring secure fastening.
- Thin-Walled Tubing and Frames – Provides a strong, non-rotating connection in bicycle frames, metal furniture, and railings.
- Electrical and Mechanical Assemblies – Common in electronic enclosures and machine housings where enhanced grip is necessary to prevent loosening.
Summary
Body Type | Advantages | Applications |
---|---|---|
Hex Rivet Nuts | High resistance to rotation and even load distribution. | Automotive, aerospace, heavy machinery, and structural applications where high torque and vibration resistance are needed. |
Round Rivet Nuts | Easy installation, versatile, and cost-effective. | Consumer electronics, sheet metal fabrication, and general manufacturing for light-duty applications. |
Knurled Rivet Nuts | Enhanced grip, anti-rotation, and improved torque resistance. | Automotive components, thin-walled frames, and electrical assemblies requiring secure fastening. |
Do You Have Any Questions?
Let Us Solve Your Problem
Rivetfix: Varied Rivet Nuts Designed to Meet Your Project Needs
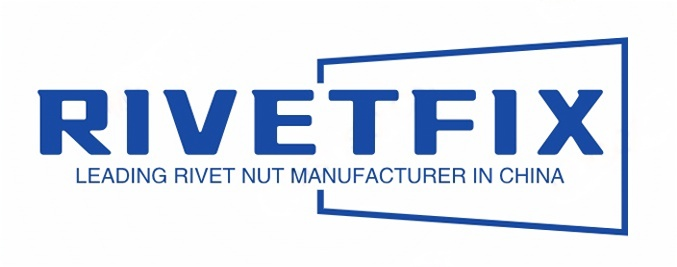
As a leading fastener manufacturer in China with more than 15 years in the industry, Rivetfix are committed to providing first-class quality fasteners and responsive services to the world.
Rivetfix offers a wide range of rivet nuts designed to meet the unique demands of your projects. With options like countersunk, flat, and hex heads, as well as knurled and round body types, Rivetfix ensures you have the right solution for every application. Choose Rivetfix for versatile, cost-effective, and durable fastening solutions tailored to your specific needs. In addition, we can also provide customized rivet nuts service according to your requirements.
Contact us for project advice and the latest rivet nut quote!
Get High Quality Rivet Nuts Quote!
Send Your Rivet Nut Request
For more than 20 years, Rivetfix has helped customers solve many rivet nuts sourcing needs and technical challenges.
Have a question? Contact us and we’ll provide you with the perfect solution.