Choosing the Best Rivet Nut Tool for Your Project
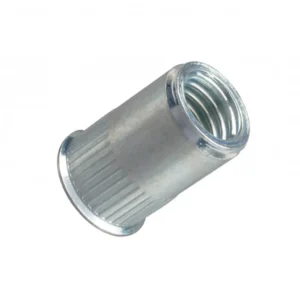
Leading Rivet Nut Manufacturer and Supplier in China
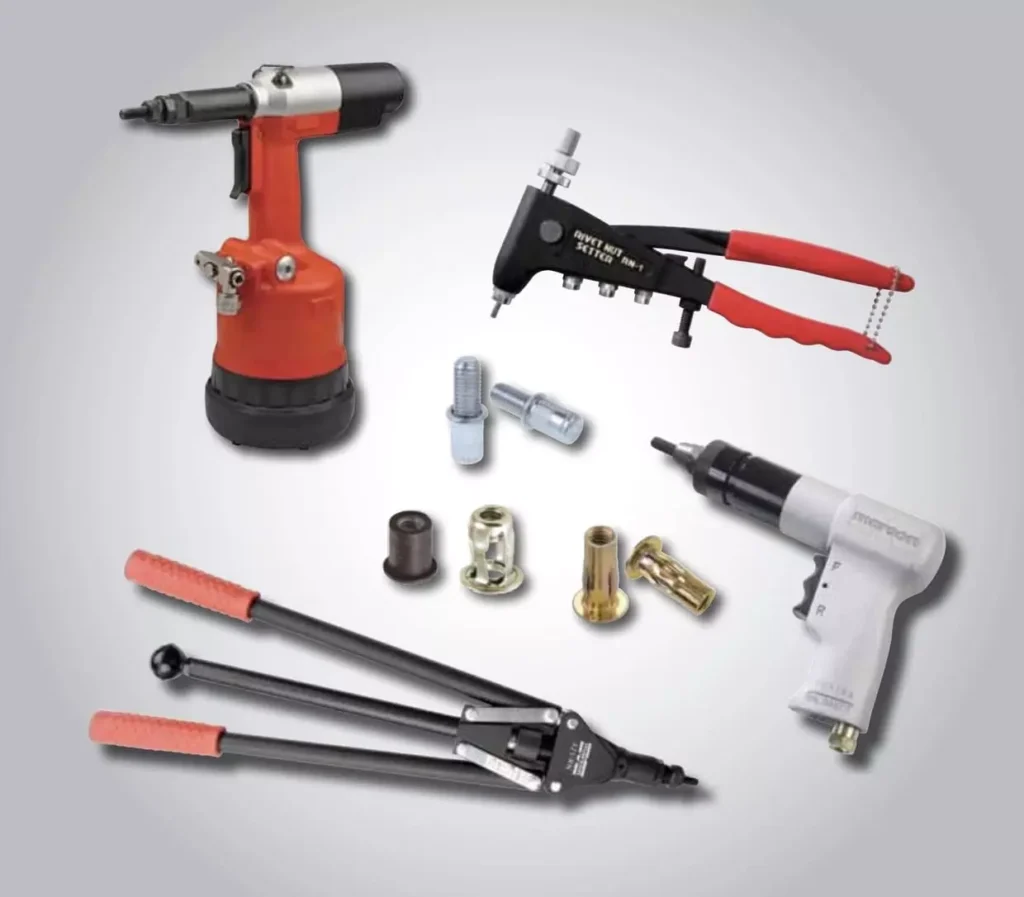
Choosing the best rivet nut tool for your project is essential for ensuring strong and secure installations. With various options like manual, pneumatic, electric, and hydraulic tools, selecting the right one depends on your budget, material, and application needs. In this guide, we’ll explore key factors to consider, from tool performance to maintenance, helping you make the best choice for efficiency and durability.
Table of Contents
What Are the Common Types of Rivet Nut Tools?
Working Principle:
- Manual rivet nut tools typically install rivet nuts through mechanical force. The operator manually pulls the tool’s lever to insert the rivet nut into the pre-drilled hole. The applied force causes the rivet nut to expand and firmly secure within the base material.
- The tool contains a rod or puller, with one end connected to the rivet nut and the other to a tightening mechanism. When the lever is pulled, the rear end of the rivet nut expands, firmly clamping the material.
Usage Scenarios:
- Small Batch Production: Ideal for single or small volume rivet nut installations.
- DIY Projects: Simple to use, suitable for home applications.
- Maintenance and Small-Scale Engineering: Perfect for tasks that don’t require high-intensity operations.
Working Principle:
- Pneumatic rivet nut tools use compressed air to drive an internal cylinder for installing the rivet nut. When compressed air flows through the tool’s cylinder, it drives the tool’s puller, applying force to expand the rivet nut and securely fasten it.
- This tool provides uniform pulling force, reducing errors that may occur with manual operation.
Usage Scenarios:
- Large-Scale Production: Suitable for high-efficiency, large-volume rivet nut installation.
- Automated Production Lines: Can be integrated into automated assembly lines.
- High-Efficiency Factory Environments: Ideal for environments requiring fast, continuous operations.
Working Principle:
- Electric rivet nut tools operate by driving an electric motor that powers the internal mechanism, automatically applying force to install the rivet nut. The tool contains a motor that drives the puller or rod, and during installation, the electric tool automatically provides the required force to expand the rivet nut and secure it in the hole.
- Electric tools often come with adjustable torque settings, ensuring consistent pulling force for each installation, improving accuracy.
Usage Scenarios:
- Medium-Scale Production: Suitable for moderate-volume rivet nut installation, offering higher efficiency than manual tools.
- Assembly Lines and Repair Work: Ideal for applications requiring precise control in medium-intensity operations.
- Small-Scale Manufacturing and Maintenance: Suitable for environments that demand higher precision and speed.
4. Hydraulic Rivet Nut Tools
Working Principle:
- Hydraulic rivet nut tools use a hydraulic system to provide strong pulling force for rivet nut installation. Hydraulic oil is pumped to the tool’s hydraulic cylinder, pushing the piston and applying immense force to expand the rivet nut.
- This tool can provide a higher pulling force than others, making it suitable for installing larger or high-strength rivet nuts.
Usage Scenarios:
- Heavy Industrial Applications: Ideal for thick metals, steel plates, and large-scale engineering projects.
- Mechanical Manufacturing and Automotive Industries: Used for installation tasks requiring extreme strength and precision.
- Special Engineering and Construction Applications: Suitable for high-strength, long-lasting fixation requirements.
Advantages and Disadvantages of Different Rivet Nut Tools
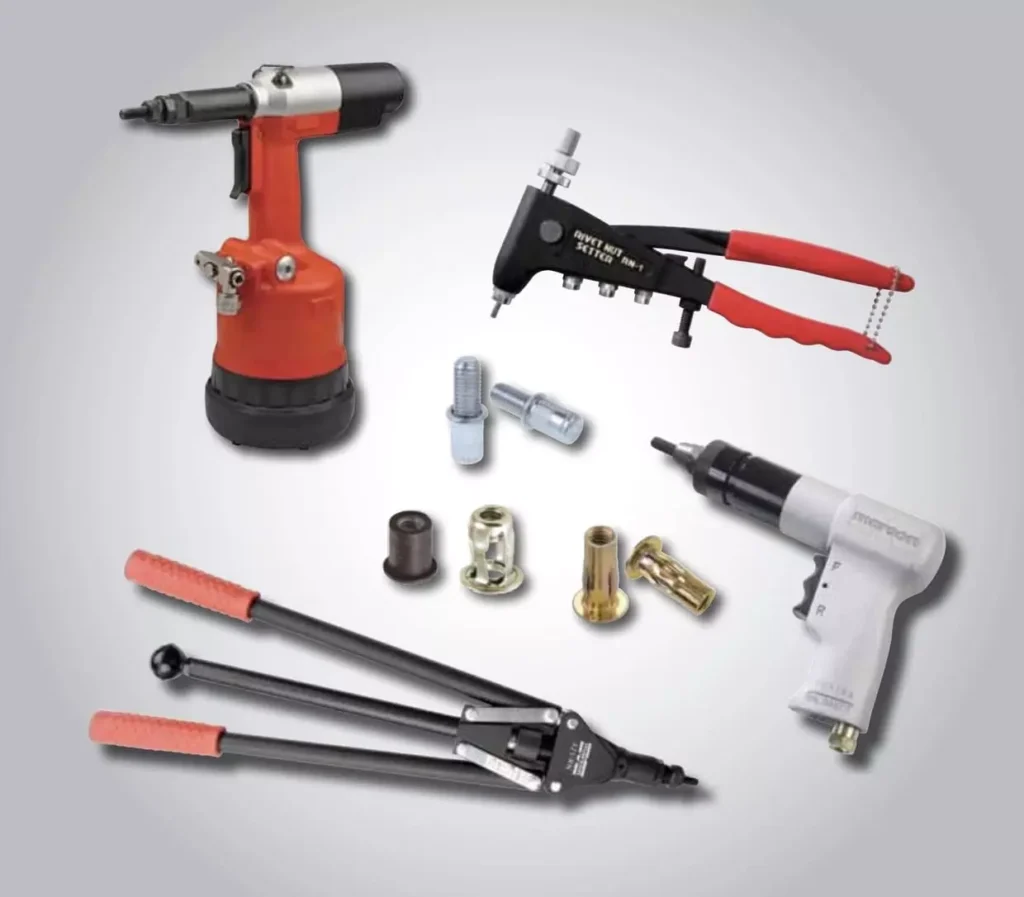
Choosing the right rivet nut tool depends on specific application requirements, including workload, efficiency, base material type, and more. Each type of tool has its advantages and disadvantages. Here is an analysis of the pros and cons of manual, pneumatic, electric, and hydraulic rivet nut tools:
Advantages:
- Low Cost: Manual tools are inexpensive, making them suitable for projects with a limited budget.
- Simple Operation: No additional power source is required, making them easy to use and ideal for DIY tasks.
- Portable: Compact and easy to carry and store, making them suitable for small workspaces.
Disadvantages:
- Slow Speed: Manual operation is slower, with lower efficiency, making it unsuitable for large-scale production.
- Dependent on Manual Force: Requires significant manual effort, which can lead to fatigue during long operations and affect installation quality if the force is inconsistent.
- Not Suitable for Thick Materials: For thicker metals or hard materials, manual tools may lack the necessary force and expansion effect to provide the required strength.
2. Pneumatic and Electric Rivet Nut Tools
Advantages:
- High Efficiency: Pneumatic and electric tools are suitable for medium to large-scale production and offer higher efficiency.
- Uniform Pulling Force: Provides stable and consistent pulling force, ensuring the rivet nut expands fully and is securely installed.
- Adaptable to Various Materials: These tools can handle various base materials, especially metals and plastics, and are versatile for different work environments.
Disadvantages:
- Maintenance Requirements: Pneumatic tools need regular checks on the air pressure system, while electric tools require recharging or battery replacement, increasing maintenance costs and time.
- Higher Cost: Pneumatic and electric tools have higher initial investment costs, making them less suitable for small-scale or budget-constrained projects.
- Dependency on Air or Power Supply: Requires a stable air or power supply, making them unsuitable for environments without these resources.
3. Hydraulic Rivet Nut Tools
Advantages:
- Powerful Pulling Force: Hydraulic tools provide extremely high pulling force, making them suitable for large-sized rivet nuts and thick materials, ensuring a strong and secure fix.
- Wide Range of Applications: Can handle materials of various thicknesses and hardness, including hard metals like steel.
- Efficient and Durable: Hydraulic tools can perform continuous large-scale rivet nut installations, making them ideal for industrial and heavy-duty applications.
Disadvantages:
- High Cost: Hydraulic tools are expensive and require additional hydraulic oil and equipment maintenance, making them suitable for heavy industry and large-scale production.
- Complex Operation: Hydraulic tools are more complex and require specific training and experience to use. Non-professionals may encounter safety hazards during operation.
- Large Size: Hydraulic tools are typically bulky and require dedicated space for operation, making them unsuitable for tight workspaces.
Summary
- Manual tools are ideal for small-scale, DIY, or budget-conscious projects, offering low cost and easy operation, but they are slower and less efficient.
- Pneumatic and electric tools are more suitable for large-scale production, providing efficient and stable performance but requiring more maintenance and higher investment.
- Hydraulic tools provide powerful pulling force and a wide range of applications, ideal for heavy industrial use, but their high cost and complex operation limit their suitable environments.
Do You Have Any Questions?
Let Us Solve Your Problem
How to Choose the Best Rivet Nut Tool for Your Project?
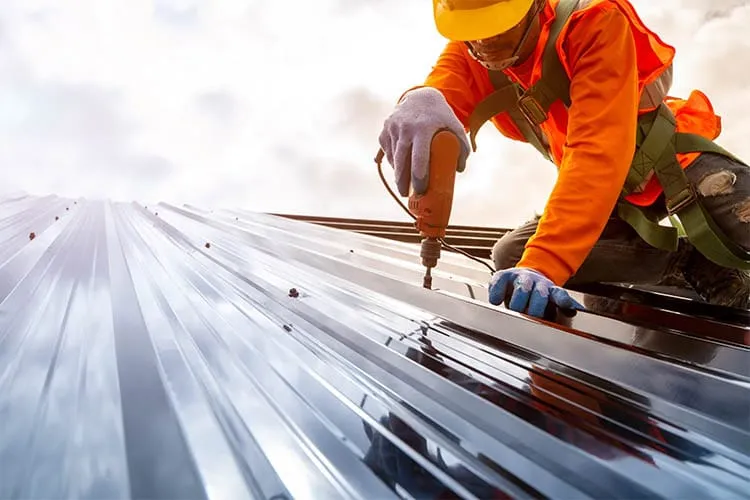
Selecting the right rivet nut tool is essential to ensuring installation quality and work efficiency. Different tools are suited for different project requirements, so when choosing a rivet nut tool, consider the following key factors:
1. Choose the Right Tool Based on Project Size
Small Batch Production or DIY Projects:
- For small batch production or DIY tasks, a manual rivet nut tool is a cost-effective option. Manual tools are suitable for installing rivet nuts one at a time or in small quantities. While they require more manual effort, they are simple, easy to operate, and affordable.
- Example: If you only need to install a few rivet nuts on furniture, cars, or lightweight equipment, a manual tool will meet the requirements.
Large-Scale Production:
- For high-efficiency, large-volume rivet nut installation, pneumatic rivet nut tools or electric rivet nut tools are better choices. These tools can complete large quantities of installations in a short time, providing consistent pulling force and expansion results.
- Example: The automotive manufacturing and home appliance industries often use pneumatic tools to improve production efficiency and ensure assembly precision.
Medium-Scale Production:
- Electric rivet nut tools are ideal for medium-scale installation needs, especially when precision and efficiency are required. Electric tools often feature adjustable pulling force to ensure consistency in each installation.
2. Choose the Tool Based on Base Material and Rivet Nut Specifications
Metal Base Materials:
- If your project involves thick metal sheets, hydraulic rivet nut tools are the best choice. These tools provide greater pulling force, suitable for installing large rivet nuts and handling high-strength work environments.
- Example: In the construction industry, using hydraulic tools to install rivet nuts in thick steel plates ensures secure installation.
Plastic or Lightweight Metals:
- For softer materials such as plastic or aluminum alloys, manual or electric tools can effectively complete the installation. These tools provide enough pulling force without damaging the material, ensuring secure rivet nut fixation.
- Example: When installing rivet nuts on plastic housings, an electric tool ensures consistency and precision.
Rivet Nut Specifications:
- Different sizes of rivet nuts require corresponding tools for installation. For example, larger rivet nuts (such as M10 or M12) may need hydraulic tools, while smaller rivet nuts (such as M4 or M5) can be installed with manual or electric tools.
- Data: For M4 rivet nuts, a manual tool provides enough pulling force; however, for M12 rivet nuts, hydraulic tools (with a maximum pulling force of up to 10 tons) are required for correct installation.
3. Consider the Tool’s Pulling Force Adjustment, Ease of Use, and Durability
Pulling Force Adjustment:
- For projects requiring precise control, it is important to choose tools with adjustable pulling force. This allows you to adjust the force applied depending on rivet nut size and base material thickness, avoiding over-expansion or insecure fixation.
- Example: Electric rivet nut tools typically have adjustable pulling force to ensure each rivet nut expands evenly, resulting in higher installation quality.
Ease of Use:
- When selecting a tool, consider its ease of use, especially if the tool will be used for extended periods. Features such as handle design, button placement, and weight distribution impact the comfort during use.
- Data: According to a user survey, over 60% of workers reported that pneumatic tools are favored in large-scale production due to their lighter weight and ease of operation.
Durability:
- When choosing a tool, assess its durability, especially for projects requiring long-term, heavy use. High-quality rivet nut tools ensure longer service life and stable performance under high-intensity conditions.
- Example: Hydraulic and pneumatic tools generally have higher durability, making them ideal for industrial-grade applications, while manual tools are better suited for occasional use.
Summary: How to Choose the Best Rivet Nut Tool?
- Small Batch or DIY Projects: Manual tools.
- Large-Scale Production: Pneumatic or electric rivet nut tools.
- Base Material: Hydraulic tools for metal materials; manual or electric tools for plastic or lightweight metals.
- Pulling Force Adjustment and Ease of Use: Choose a powerful tool that meets your work requirements, ensuring comfort and work efficiency.
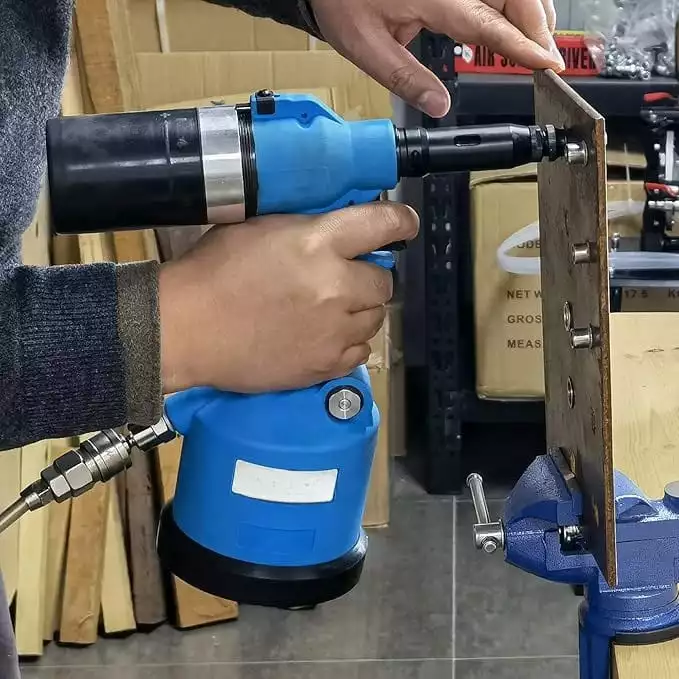
Proper use of rivet nut tools not only improves work efficiency but also ensures the quality of rivet nut installation. The operating methods and precautions vary depending on the tool type. Below is a discussion of how to use manual, pneumatic, electric, and hydraulic rivet nut tools correctly, along with tips for avoiding common issues and using the tools on different materials.
1. How to Correctly Use Manual Rivet Nut Tools
Operating Steps:
- Choose the Correct Rivet Nut and Tool: Ensure the size of the rivet nut matches the tool.
- Align the Rivet Nut: Place the rivet nut into the tool’s mandrel, ensuring it aligns with the insertion hole.
- Insert the Rivet Nut: Position the tool over the drilled hole, keeping it perpendicular to the base material to avoid tilting.
- Apply Force: Grasp the tool handle firmly and apply even force until the rivet nut expands and securely fixes in place.
Avoid Common Problems:
- Rivet Nut Loosening: Use knurled or hexagonal rivet nuts to increase friction and prevent loosening.
- Incomplete Expansion: Ensure enough pressure is applied, and avoid a loose grip on the handle. If the tool is too light, consider switching to an electric or pneumatic tool.
Precautions:
- Since manual tools require significant force, maintain stability during operation to prevent uneven application, which could lead to insecure rivet nut installation.
2. How to Correctly Use Pneumatic Rivet Nut Tools
Operating Steps:
- Adjust Pressure Settings: Before using the pneumatic tool, ensure the air pressure regulator is set within the appropriate range (usually 6-8 bar).
- Choose the Appropriate Rivet Nut: Select the correct rivet nut and tool for the base material thickness and rivet nut specifications.
- Align the Tool with the Hole: Insert the rivet nut into the tool and align it with the drilled hole, ensuring the tool is perpendicular to the material.
- Activate the Pneumatic Tool: Press the tool switch to activate the tool, using air pressure to pull the tool’s mandrel and expand the rivet nut.
Avoid Common Problems:
- Rivet Nut Rotation: If the tool’s pulling force is insufficient, check the air pressure and ensure that the pneumatic tool’s force range matches the rivet nut specifications.
- Uneven Expansion: Ensure even pressure distribution during operation to avoid over-expansion that could damage the rivet nut.
Precautions:
- Regularly check the pneumatic tool’s air pressure system to avoid air leaks that could affect the tool’s performance.
3. How to Correctly Use Electric Rivet Nut Tools
Operating Steps:
- Adjust Pulling Force: Set the electric tool’s pulling force based on the rivet nut’s specifications and material thickness. Ensure the force is appropriate to fully expand the rivet nut without damaging the material.
- Choose the Correct Tool Head and Rivet Nut: Select the correct tool head according to the rivet nut specifications.
- Align the Tool with the Hole: Position the rivet nut tool over the hole and keep the tool perpendicular to the material.
- Activate the Electric Tool: Start the tool and apply pulling force, ensuring the rivet nut expands fully and fixes securely.
Avoid Common Problems:
- Incomplete Expansion: If the rivet nut does not fully expand, check the pulling force settings to ensure sufficient force is applied.
- Thread Damage: Choose a tool head that matches the rivet nut specifications and ensure it does not slip during use to prevent damaging the rivet nut threads.
Precautions:
- Electric tools are ideal for medium-scale installations. Ensure the tool’s battery is charged to avoid loss of power during use.
4. How to Correctly Use Hydraulic Rivet Nut Tools
Operating Steps:
- Check the Hydraulic System: Ensure the hydraulic tool’s oil pressure is within the specified range, typically 6-10 tons.
- Select the Appropriate Rivet Nut and Tool Head: Hydraulic tools are best for larger rivet nuts (e.g., M10 and above). Select the matching tool head.
- Align the Tool with the Hole: Position the hydraulic tool over the drilled hole, ensuring it is perpendicular.
- Apply Pressure: Start the hydraulic system, applying oil pressure to push the tool’s mandrel and expand the rivet nut.
Avoid Common Problems:
- Base Material Cracking or Damage: Hydraulic tools generate a lot of force, so ensure the material can withstand the pressure to avoid breaking the base material.
- Uneven Expansion: Operate smoothly to avoid applying too much pressure suddenly, which can lead to uneven expansion.
Precautions:
- Hydraulic tools are suitable for heavy industrial and large-scale production. Ensure the tool’s oil pressure remains stable to prevent sudden changes that could affect installation quality.
How to Use Rivet Nut Tools on Different Materials
- Metal Materials: When using rivet nut tools on metal sheets, ensure the tool and rivet nut are suitable for the metal thickness. For harder metals, use hydraulic or pneumatic tools to provide greater pulling force for secure rivet nut installation.
- Plastic and Thin Materials: For plastics or thin aluminum alloys, select an appropriate pulling force to avoid excessive pressure that could crack the material. Manual or electric tools are sufficient for these materials, as too much force may damage the surface.
- Soft Metals: For soft metals (such as aluminum), use moderate pressure and electric tools to prevent over-expansion that could damage the base material.
Summary: Tips for Correctly Using Rivet Nut Tools
- Choose the Right Tool: Select a tool based on project scale, material type, and rivet nut specifications.
- Check Tool Settings: Ensure the tool’s pressure, pulling force settings, and tool head match the rivet nut.
- Maintain Steady Operation: Whether using manual, pneumatic, or hydraulic tools, ensure smooth, steady force application to avoid excessive fluctuations.
- Regularly Inspect and Maintain Tools: Periodically check the tool’s condition and perform maintenance to ensure its longevity and installation quality.
Do You Have Any Questions?
Let Us Solve Your Problem
Other Factors to Consider When Choosing a Rivet Nut Tool
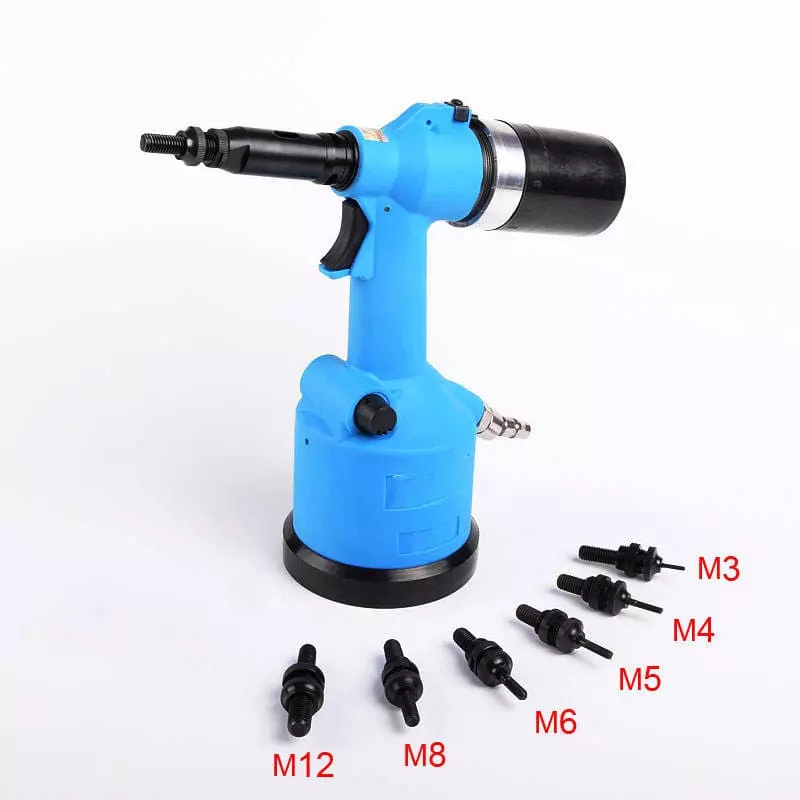
1. Budget
The price of tools varies depending on the type, features, and brand. To ensure cost control and maximize cost-effectiveness, consider the following points when selecting a tool:
- Manual Tools: Generally more affordable, suitable for small-scale projects or DIY work with a limited budget.
- Pneumatic and Electric Tools: Higher in price but offer greater efficiency, making them suitable for medium-scale production. Depending on the needs, both entry-level and high-end options are available.
- Hydraulic Tools: High-end tools with a higher cost, primarily used for large-scale or industrial applications that require a significant budget.
When choosing a tool, it is important to balance performance and cost, selecting one within an appropriate price range to avoid overspending or choosing an unsuitable low-cost tool.
2. Maintenance and Care
Proper maintenance and care can significantly extend the lifespan of rivet nut tools, reduce malfunctions, and lower long-term operating costs. Key aspects of maintenance include:
- Regular Inspection and Cleaning: Frequently check and clean the tool, especially pneumatic and electric tools. Ensure that dust, oil, and debris do not clog air vents or electrical connections.
- Lubrication and Maintenance: Regularly add lubricant or hydraulic oil to pneumatic and hydraulic tools to prevent excessive friction and wear.
- Replacement of Consumables: Periodically check and replace worn-out parts such as rubber gaskets, seals, and drill bits to maintain tool performance.
- Avoid Overuse: Prevent prolonged high-load operation. Follow the tool’s manual and recommended usage guidelines to reduce wear and tear.
3. Brand and Quality
Choosing a reputable brand and high-quality tool ensures stability and safety during installation while improving overall project efficiency. Consider the following factors:
- Brand Reputation: Well-known brands typically have better quality control and after-sales service. Investing in high-quality tools reduces the risk of project delays and additional costs due to tool failures.
- Certifications and Standards: Select tools that comply with international or industry certifications, as they undergo strict testing and quality control to ensure reliable performance.
- Customer Reviews and Case Studies: Before purchasing a tool, check customer reviews and case studies to understand its real-world performance. Positive feedback from other users can provide valuable insights.
Why Choose Rivetfix
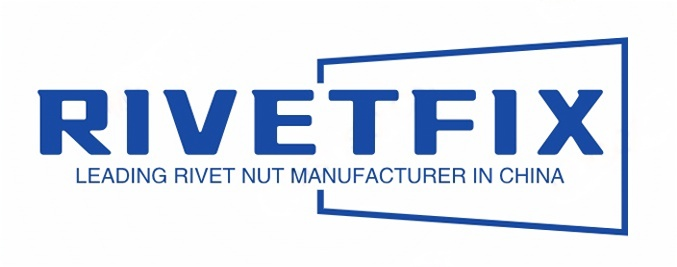
As a leading fastener manufacturer in China with more than 15 years in the industry, Rivetfix are committed to providing first-class quality fasteners and responsive services to the world.
Rivetfix offers a wide range of rivet nuts designed to meet the unique demands of your projects. With options like countersunk, flat, and hex heads, as well as knurled and round body types, Rivetfix ensures you have the right solution for every application. Choose Rivetfix for versatile, cost-effective, and durable fastening solutions tailored to your specific needs. In addition, we can also provide customized rivet nuts service according to your requirements.
Contact us for project advice and the latest rivet nut quote!
Get High Quality Rivet Nuts Quote!
Send Your Rivet Nut Request
For more than 20 years, Rivetfix has helped customers solve many rivet nuts sourcing needs and technical challenges.
Have a question? Contact us and we’ll provide you with the perfect solution.