Best Rivet Nuts for Plastic
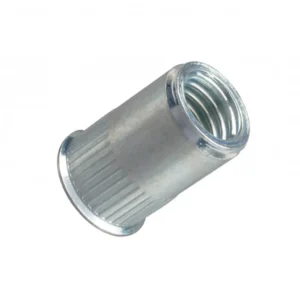
Leading Rivet Nut Manufacturer and Supplier in China
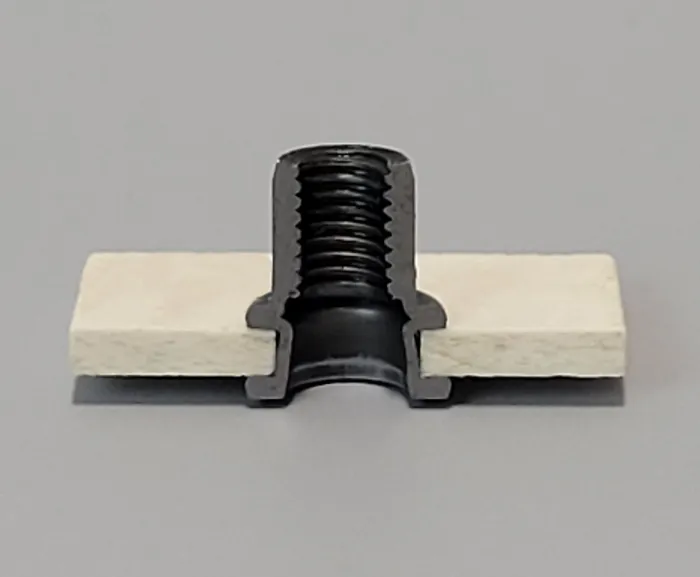
When it comes to securing components on plastic materials, choosing the right rivet nuts for plastic is crucial for strength and durability. In this guide, we’ll explore the best rivet nuts specifically designed for plastic applications, ensuring you achieve reliable and long-lasting connections every time.
Table of Contents
Why Use Rivet Nuts on Plastic?
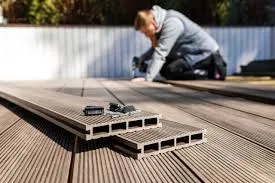
Using rivet nuts on plastic materials is a key solution for enhancing connection strength, improving durability, and optimizing installation efficiency. Plastics are widely used in industries such as automotive, electronics, household appliances, and medical devices due to their lightweight and easy-to-process nature. However, plastics have relatively low mechanical properties, such as strength and thread retention, making it essential to adopt suitable fastening methods to ensure a secure and reliable connection.
1. Provides a Durable Threaded Connection, Preventing Thread Damage
Plastic materials are soft, and direct threading into plastic can result in stripped threads due to repeated assembly, vibrations, or high loads, leading to connection failure. Rivet nuts feature metal threads, significantly enhancing wear resistance and thread lifespan. This is particularly beneficial in applications requiring frequent disassembly, such as electronic enclosures, household appliance panels, and medical equipment components.
2. Ideal for Thin-Walled Plastics, Enhancing Thread Strength
For thin-walled plastic materials (such as ABS, PP, PC, and Nylon), standard screws may not generate sufficient thread engagement to provide stable fastening. Rivet nuts expand the contact area, forming a secure metal thread within thin-walled structures, preventing screws from pulling out under excessive force.
Common applications include:
- Automotive interior components (dashboards, door panels, seat brackets)
- Electronic product enclosures (laptops, server chassis, control panels)
- Plastic piping systems (HVAC ducts, filtration system connectors)
3. Eliminates the Risk of Heat Damage from Welding or Insert Molding
Certain metal nuts can be embedded into plastics using welding, heat staking, or ultrasonic insertion. However, these processes may cause localized melting, deformation, or stress cracking, affecting the structural integrity of the product. Rivet nuts, on the other hand, utilize a cold-forming installation process, eliminating heat-related damage and providing a safer, more stable fastening solution.
4. Enhances Pull-Out and Spin-Out Resistance for Improved Reliability
Standard round rivet nuts may loosen in high-load or vibration-prone environments. However, rivet nuts specifically designed for plastics typically feature knurled or hexagonal designs, significantly improving resistance to rotation and pull-out forces.
- Hexagonal Rivet Nuts: Mechanically interlock with the plastic, preventing rotation, making them ideal for high-torque applications.
- Knurled Rivet Nuts: Feature knurled outer surfaces that increase friction, enhancing grip and preventing loosening in plastic materials.
5. Suitable for Mass Production, Improving Assembly Efficiency
Rivet nuts can be quickly installed using manual, electric, or pneumatic tools, making them ideal for high-volume production while reducing labor costs. This advantage makes them widely used in automotive manufacturing, industrial equipment, and consumer electronics.
Installation Methods:
- Manual tools (for small-scale or repair applications)
- Electric tools (for mid-scale applications with faster installation speed)
- Pneumatic/hydraulic tools (for large-scale production and automated assembly lines)
6. Compatible with Various Plastic Materials, Offering Versatile Applications
Rivet nuts can be used with a wide range of plastic materials, including:
- Thermoplastics (ABS, PP, PC, Nylon, PVC)
- Reinforced composites (Glass-fiber reinforced plastics, carbon-fiber composites)
- Engineering plastics (POM, PEEK, PPS)
Regardless of whether the plastic is high-strength (such as glass-fiber reinforced Nylon) or relatively soft (such as PP or PVC), selecting the right rivet nut type and material ensures a strong and reliable connection.
Conclusion: Advantages of Using Rivet Nuts on Plastic
Advantage | Description |
Provides durable threads | Prevents plastic threads from stripping, extending service life |
Ideal for thin-walled plastics | Offers strong fastening in thin materials |
No heat processing required | Avoids deformation or damage from welding or heat staking |
High pull-out and spin-out resistance | Knurled, hexagonal, or flanged designs enhance stability |
Suitable for mass production | Quick installation improves production efficiency |
Compatible with various plastics | Works with different thermoplastics and composite materials |
What Are the Fastening Challenges in Plastic Materials?
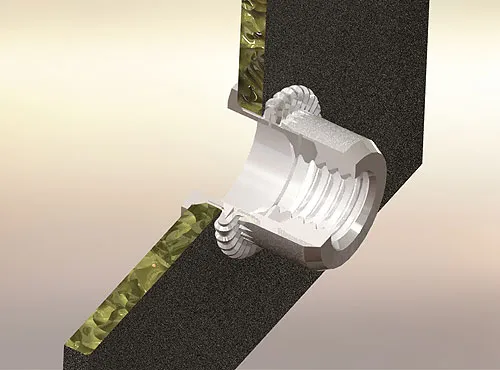
1. Low Strength and Rigidity
- The tensile strength of plastics is generally lower than that of metals. For example, polycarbonate (PC) and polypropylene (PP) have a tensile strength of approximately 60 MPa, whereas steel can reach up to 400 MPa. This makes conventional bolts and nuts prone to connection failure when used in plastic. Rivet nuts effectively distribute pressure, enhancing connection strength.
- According to the ASTM D638 standard, plastics typically have a tensile strength of 20-60 MPa, whereas metals fall within the 200-500 MPa range. Therefore, when fastening plastics, it is essential to use fasteners that can distribute stress effectively.
2. Poor Thread Retention
- The thread holding capability of plastics like polypropylene (PP) and polyethylene (PE) is roughly half that of metals.
- For example, the thread strength of polypropylene is only 6.5-8.5 MPa, whereas steel threads typically have a holding strength of 50-70 MPa. This means that threads in soft plastics are prone to damage, making rivet nuts a better solution for improved fastening and preventing thread stripping.
3. Thermal Expansion Issues
- The coefficient of thermal expansion (CTE) of plastics is significantly higher than that of metals. For example, polyethylene (PE) has a CTE of 100-200 × 10⁻⁶/°C, while steel has a much lower CTE of 10-12 × 10⁻⁶/°C.
- In environments with high temperatures or large temperature fluctuations, plastics expand or contract, leading to unstable bolt connections. Rivet nuts are designed to accommodate these dimensional changes, reducing stress-induced failures.
4. Fatigue and Stress Concentration
- Plastics have a lower fatigue limit compared to metals, especially in high-strength plastics such as polycarbonate (PC) and nylon (PA).
- According to the ASTM D3479 standard, the fatigue limit of plastics typically ranges from 15-30 MPa, while steel can exceed 200 MPa. The use of rivet nuts helps mitigate stress concentration, improving the durability of plastic fasteners over time.
5. Corrosion Resistance
- While plastics generally have superior corrosion resistance compared to metals, certain plastics, such as polyethylene (PE) and polypropylene (PP), may degrade when exposed to specific chemicals or extreme environments.
- Zinc-plated steel or stainless steel rivet nuts offer better corrosion resistance. In salt spray tests, treated steel fasteners can withstand over 500 hours of exposure, significantly outperforming untreated plastic surfaces.
6. Installation and Fixation Challenges
- When using conventional bolts or nuts in plastic, especially thin-walled plastics, the material may crack or slip during fastening.
- For example, polyvinyl chloride (PVC) and polyethylene (PE) have relatively low strength and rigidity, making them susceptible to stress concentration, which can ultimately result in loosening or breakage. Rivet nuts provide a more secure fastening solution, preventing material damage and ensuring a firm connection.
7. Long-Term Durability
- Plastics tend to degrade under prolonged UV exposure, particularly in high-temperature or high-humidity conditions.
- Common materials such as polypropylene (PP) and polycarbonate (PC) have UV resistance ratings of only <30 hours and <300 hours, respectively. Rivet nuts contribute to maintaining long-term connection reliability, especially in environments with significant temperature and humidity variations.
Do You Have Any Questions?
Let Us Solve Your Problem
How to Make the Rivet Nut Suitable for Plastic Material?
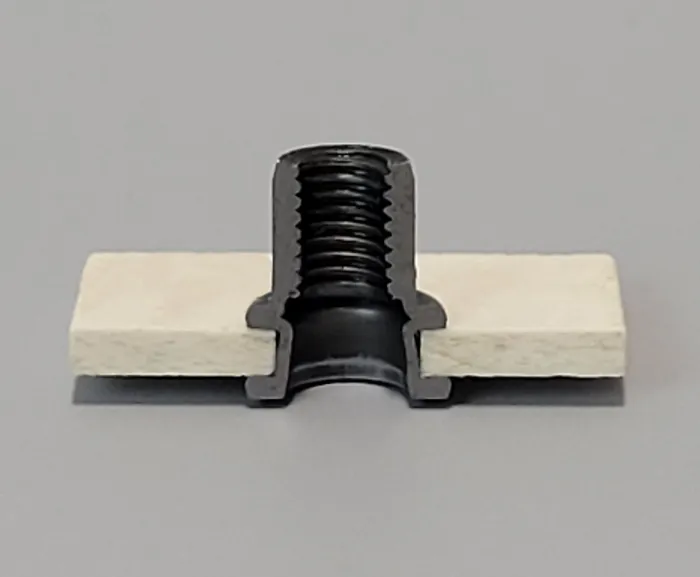
1. Material Selection
Rivet nuts made from aluminum, stainless steel, and brass are commonly used in plastic applications:
- Aluminum rivet nuts are lightweight and ideal for low-load applications in general plastic fastening.
- Stainless steel rivet nuts offer higher strength and superior corrosion resistance, making them suitable for outdoor or high-humidity environments.
- Brass rivet nuts are preferred for applications requiring high conductivity or enhanced corrosion resistance, such as electrical components in plastic housings.
2. Thread Design
To enhance grip and prevent loosening, rivet nuts for plastics often feature reinforced thread designs, such as:
- Knurled threads or self-tapping threads, which ensure a firmer hold on plastic surfaces, reducing the risk of loosening.
- Fine-threaded rivet nuts, which distribute pressure more effectively in softer plastics, preventing material deformation or cracking.
3. Outer Shape Design
The external shape of a rivet nut plays a crucial role in preventing rotation and improving fastening strength:
- Knurled-body rivet nuts enhance friction, preventing the nut from spinning inside the plastic—especially useful for thin-walled plastics.
- Hexagonal-body rivet nuts provide superior anti-rotation performance and are suitable for high-torque applications.
- Flanged-head rivet nuts help distribute pressure over a larger surface area, reducing stress on softer plastics and preventing damage.
4. Installation Methods
Different types of rivet nuts are designed for various plastic materials and installation techniques:
- Self-tapping rivet nuts: These cut into the plastic during installation, making them ideal for hard plastics such as polycarbonate (PC) and polypropylene (PP).
- Self-expanding rivet nuts: Expand upon installation to form a stronger grip in soft plastics, preventing material damage.
- Pre-installed nuts: Used for thin-walled plastics, these rivet nuts are embedded beforehand to minimize stress during assembly.
Which Type of Rivet Nut is Best for Plastics?
Selecting the right rivet nut for plastic applications is crucial to ensuring high resistance to rotation, strong pull-out force, and long-term stability. Since plastic materials are softer than metals and prone to deformation under stress, specialized rivet nuts are required to prevent loosening, spinning, or damaging the plastic substrate. Below are the best types of rivet nuts for plastics and their characteristics:
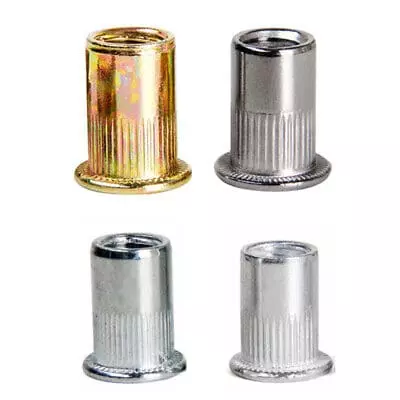
- Designed with a knurled outer surface to increase friction and grip, effectively preventing rotation and pull-out.
- Suitable for soft to medium-hard plastics, such as ABS, PP, and PC.
- Available in round and semi-hexagonal shapes for enhanced anti-rotation performance.
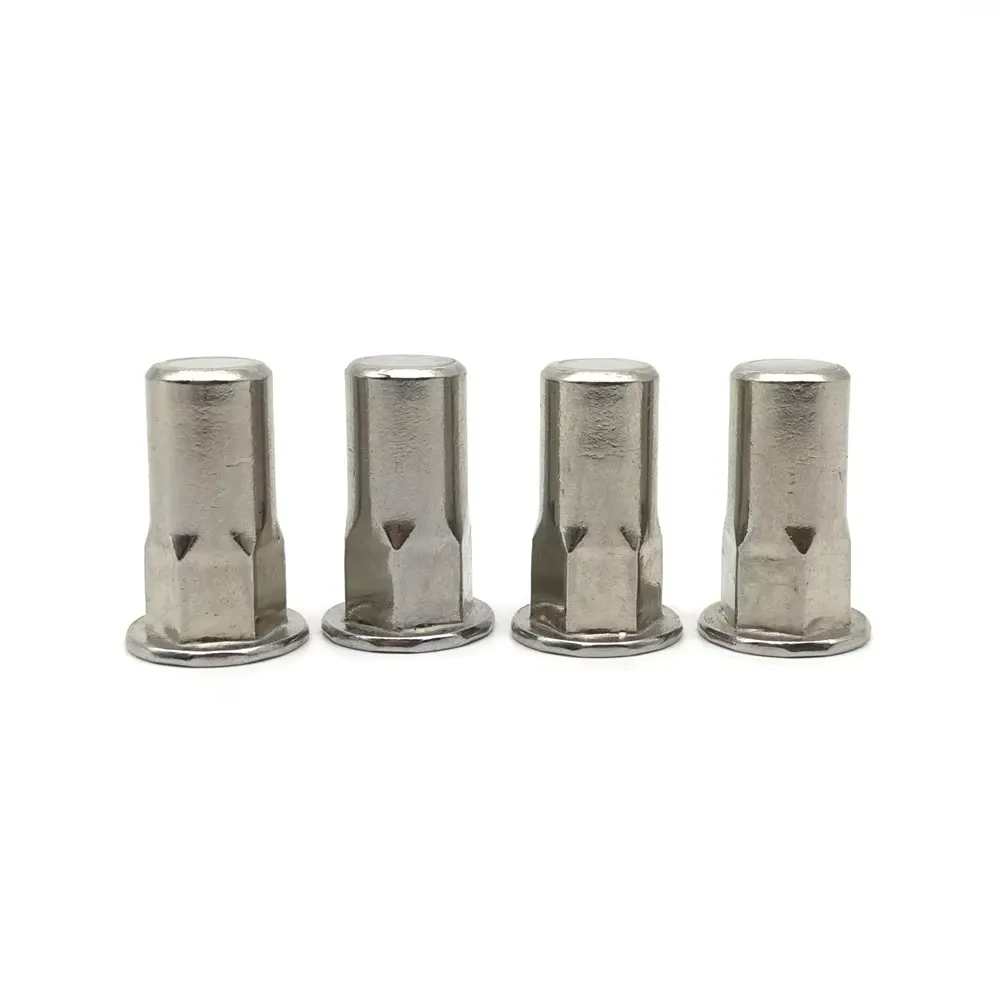
- Hexagonal shape provides a tight fit with the plastic hole, preventing the nut from spinning during installation and use.
- Suitable for high-torque applications and stronger plastics, such as fiberglass-reinforced plastic (FRP) and nylon (PA).
- Available in closed-end and open-end designs, depending on application requirements.
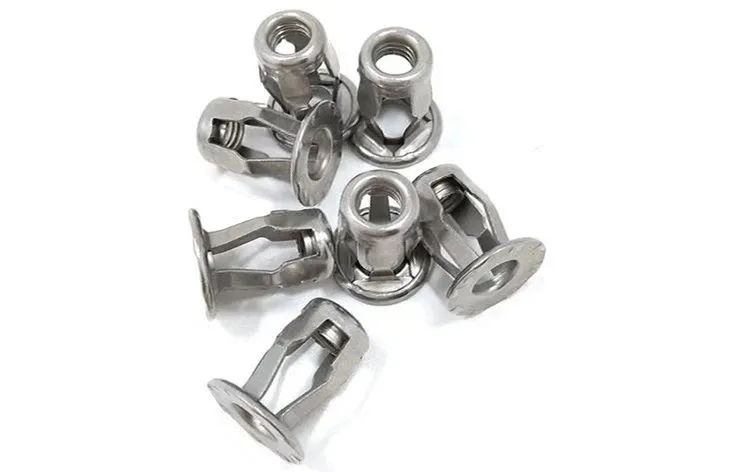
- Unique four-lobe expansion structure, creating a strong “anchor point” within the plastic, ensuring stability even in thin or low-strength plastics.
- Ideal for low-hardness plastics like PP, PE, and PVC, as well as thin plastic panels, without causing excessive stress on the substrate.
- Can be installed manually or with pneumatic tools, offering versatile installation options.
Comparison: Which Rivet Nut is Best for Plastics?
Rivet Nut Type | Main Advantages | Suitable Plastic Materials | Typical Applications |
Knurled Rivet Nuts | Improved grip, prevents slipping | ABS, PC, PP, PA | Electronics, appliances, automotive interiors |
Hexagonal Rivet Nuts | Strong anti-rotation capability, ideal for high-strength plastics | FRP, reinforced nylon (PA+GF) | Automotive, industrial equipment, construction |
Jack Nuts | Best for thin-walled plastics, prevents stress concentration | PP, PE, PVC | Soft plastic panels, home appliances, enclosures |
Conclusion: Are Jack Nuts the Best for Plastic Fastening?
If your application involves thin, soft, or fragile plastic materials, Jack Nuts are the best choice.You can learn about it in this blog what are jack nuts used for.
Their four-lobe expansion design creates a strong internal anchor, ensuring reliable fastening even in low-strength plastics. Additionally, Jack Nuts distribute pressure evenly, preventing surface damage such as cracking or deformation.
However, the best rivet nut choice depends on factors such as plastic material properties, load requirements, and torque resistance. For high-strength plastics, hexagonal rivet nuts might be more suitable, while thin-walled rivet nuts can also be considered for certain applications. Therefore, it’s always recommended to evaluate the specific application environment and material characteristics when selecting the ideal rivet nut.
Do You Have Any Questions?
Let Us Solve Your Problem
What Are the Considerations When Installing Rivet Nuts on Plastic Materials?
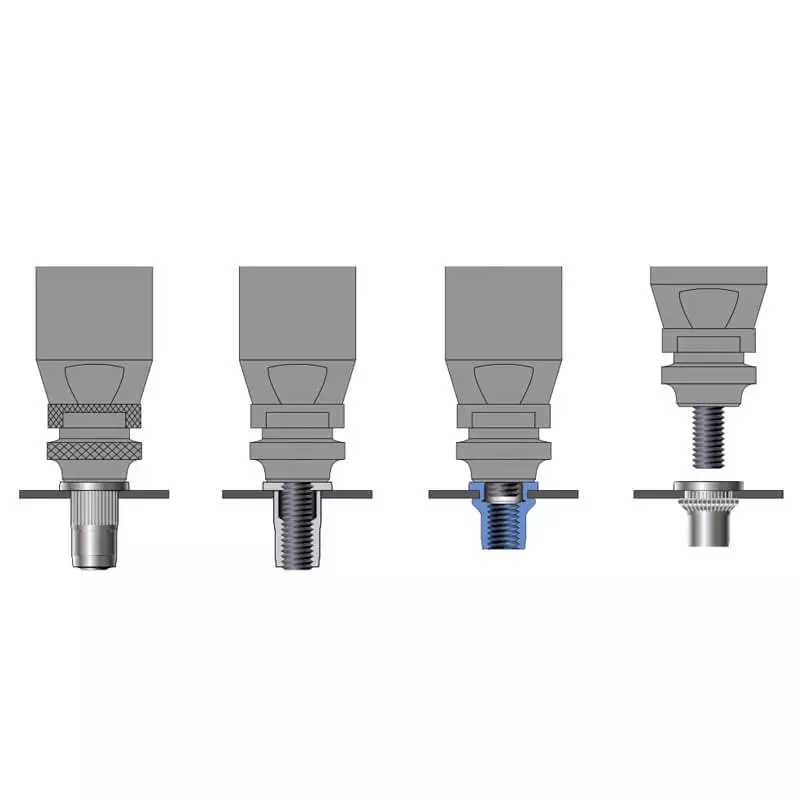
Precise Matching of Drilled Hole Size
- Hole Too Large: The rivet nut may not secure firmly, potentially causing rotation or loosening.
- Hole Too Small: Installation may damage the plastic substrate or prevent the rivet nut from expanding and securing properly.
- Recommended Hole Size Calculation: Use the standard drilled hole sizes provided for rivet nuts according to their specifications, ensuring that the outer diameter of the rivet nut and hole tolerance are within ±0.1mm.
Control Installation Pressure to Avoid Damage to Plastic Material
Use Appropriate Riveting Tools:
- Manual Tools: Suitable for small-batch installations, ensuring that excessive pressure is not applied to the plastic.
- Pneumatic/Electric Rivet Nut Guns: Suitable for high-volume installations, but pressure must be adjusted to prevent deformation or cracking of the plastic.
- Low Torque Settings: To avoid over-compressing the plastic substrate.
Pressure Control During Installation:
- Excessive Pressure ➝ May cause cracking on the plastic surface or rivet nut failure.
- Insufficient Pressure ➝ May result in the rivet nut not fully deforming, leading to loosening after installation.
- Recommendation: Use torque-adjustable installation tools and conduct installation tests to optimize the pressure settings.
What Are the Recommended Rivet Nut Brands and Suppliers?
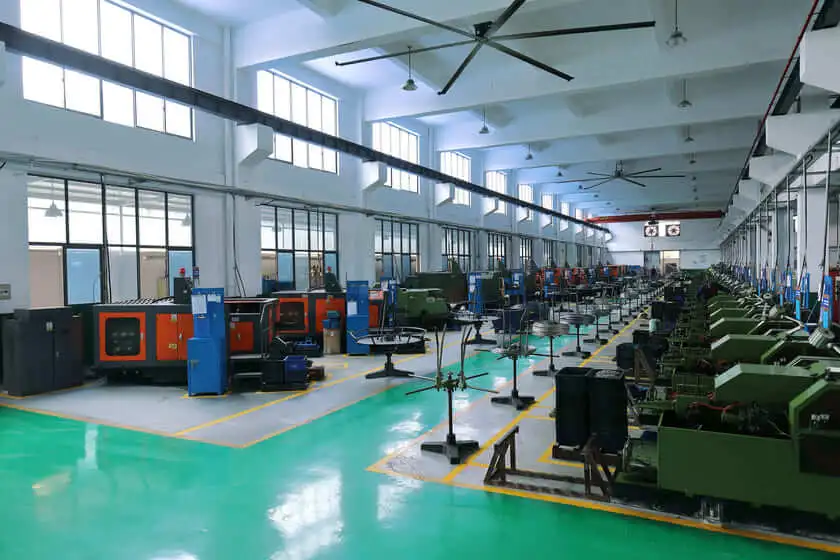
1. Trusted Rivet Nut Brands
Rivetfix – Specializes in high-strength rivet nuts, offering knurled and hexagonal rivet nuts suitable for plastic materials, widely used in industrial and automotive applications.
Bollhoff – A well-known German fastener brand, its RIVKLE® rivet nuts are of excellent quality, designed for lightweight structures and plastic substrates.
Gesipa – Known for precision manufacturing and high durability, ideal for fastening applications in the automotive, electronics, and aerospace industries.
POP Avdel (Stanley Engineered Fastening) – Offers a variety of rivet nut types, including low-torque installation models suitable for plastic materials.
Southco – Primarily focused on fastening solutions for electronics, appliances, and the automotive industry, offering a range of high-performance rivet nuts.
2. Bulk Procurement Recommendations for Industrial Manufacturing and Automotive Sectors
Purchase Directly from Manufacturers: For large procurement volumes, consider contacting manufacturers directly (e.g., Rivetfix, Bollhoff) to obtain bulk discounts and technical support.
Choose Reliable Distributors: Distributors such as McMaster-Carr, Fastenal, RS Components, or Amazon Industrial offer a variety of rivet nut brands and support international shipping.
OEM/ODM Procurement: For custom requirements, reach out to specialized suppliers offering OEM production or ODM design services to meet the specific needs of certain industries.
Focus on Inventory and Lead Times: For large-scale purchases, select suppliers with stable inventory levels and short lead times to ensure the production line is not delayed due to stockouts.
Certification Requirements: For high-standard industries such as automotive and aerospace, it’s advisable to choose suppliers with certifications like ISO 9001 or IATF 16949 to ensure product quality and consistency.
Why Choose Rivetfix
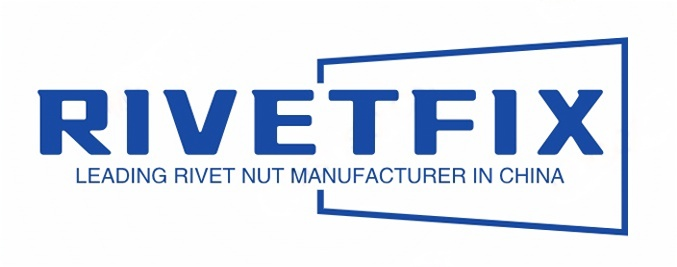
As a leading fastener manufacturer in China with more than 15 years in the industry, Rivetfix are committed to providing first-class quality fasteners and responsive services to the world.
Rivetfix offers a wide range of rivet nuts designed to meet the unique demands of your projects. With options like countersunk, flat, and hex heads, as well as knurled and round body types, Rivetfix ensures you have the right solution for every application. Choose Rivetfix for versatile, cost-effective, and durable fastening solutions tailored to your specific needs. In addition, we can also provide customized rivet nuts service according to your requirements.
Contact us for project advice and the latest rivet nut quote!
Get High Quality Rivet Nuts Quote!
Send Your Rivet Nut Request
For more than 20 years, Rivetfix has helped customers solve many rivet nuts sourcing needs and technical challenges.
Have a question? Contact us and we’ll provide you with the perfect solution.