How Do Jack Nuts Work?
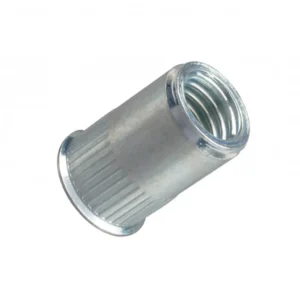
Leading Rivet Nut Manufacturer and Supplier in China
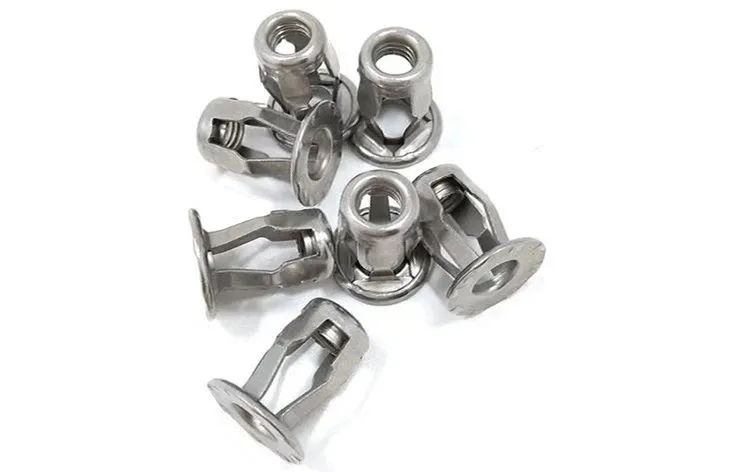
Ever wondered how to fasten thin panels without welding or rivets, using just one-side access? Discover how do Jack nuts work! These ingenious fasteners use mechanical expansion—tightening a bolt drives a cone-shaped core to radially expand the sleeve, creating a vibration-resistant, removable thread. Perfect for automotive, electronics, and furniture!
Table of Contents
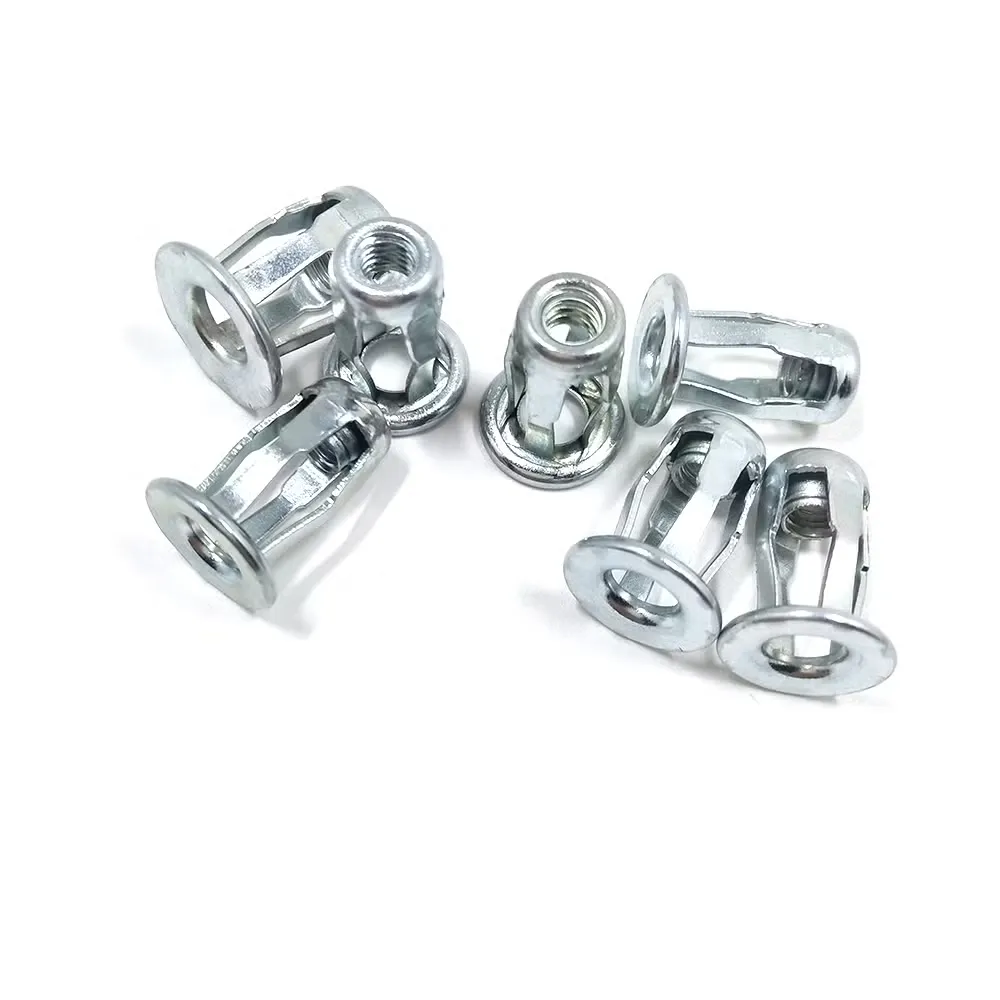
Definition
Jack Nuts are fasteners specifically designed for thin-walled materials, soft substrates, or hollow structures. They provide a secure threaded connection in places where traditional threaded fasteners cannot be used, and are widely used in plastics, fiberglass, thin metal sheets, and other soft or fragile materials.
The working principle of Jack Nuts is similar to expansion anchors. During the tightening of the screw, the four ribbed parts of the nut expand outward, creating support on the back side, thus securely fastening the nut within the substrate. This structure allows for reliable fastening in situations where riveting or welding cannot be used.
Key Benefits
1. Suitable for Soft or Thin-Walled Materials
In materials such as plastics, fiberglass, aluminum alloys, and thin steel sheets, traditional threaded fastening methods often encounter the following issues:
- Self-tapping screws may strip or fail due to the softness of the material.
- Welded nuts may not be suitable due to the material being too thin or heat-sensitive.
- Standard rivet nuts require larger holes and precise holding thickness, making installation unstable.
Jack Nuts address these challenges with their unique expansion structure. During screw tightening, the legs expand outward, forming a stable backing support that avoids applying excessive localized stress to the substrate. As a result, they can be securely fastened to soft materials without causing damage.
2. No Need for High-Precision Holes
In many industrial or repair applications, it is difficult to control the precision of the drilled holes. Standard rivet nuts usually require hole tolerances within ±0.1mm; otherwise, installation failure or loosening may occur. In contrast, Jack Nuts are more adaptable to hole dimensions and allow for a wider tolerance range, offering the following advantages:
- Standard drills or punching tools can be used to create holes without requiring high-precision machining equipment.
- Slight errors in hole diameter do not affect the fastening performance of Jack Nuts, making installation more flexible.
- The reduced reliance on hole precision lowers production costs and increases construction efficiency.
3. Suitable for Blind Hole Installations or One-Sided Operations
In some applications, fasteners must be installed from one side, and access to or force application on the opposite side is not possible, such as:
- Hollow profiles (e.g., aluminum alloy frames, steel tubes, etc.)
- Sealed enclosures (e.g., electronic cabinets, car doors, instrument panels, etc.)
- Difficult-to-reach installation areas (e.g., internal connection points of equipment)
Jack Nuts expand their support structure inside the material, allowing for fastening from a single side without the need for additional tools or back-side support. This characteristic makes them highly advantageous for blind hole installations.
4. Easy Installation with No Special Equipment
Compared to welded nuts or rivet nuts, Jack Nuts are much easier to install and do not require specialized equipment:
- Only a screwdriver, wrench, or dedicated installation tool is needed, with no welding, riveting, or other special processes required.
- The installation process does not generate high heat or sparks, making it suitable for heat-sensitive materials (e.g., plastics, composites).
- No special skills are needed, allowing non-professional users to install quickly and reducing construction costs and maintenance complexity.
5. Suitable for Various Materials and Size Requirements
Jack Nuts can be selected in different materials and specifications to meet various environmental and load-bearing requirements.
Moreover, Jack Nuts are available in a range of sizes from M3 to M8, ensuring they can provide reliable fastening effects in different applications.
Structure & Components
Jack Nuts primarily consist of the following parts:
- Threaded Body
- This part provides the internal threads, allowing screws or bolts to be screwed in and form a firm connection.
- Expansion Legs
- During screw tightening, the expansion legs move outward, creating the backing support that ensures the nut is securely fixed in the substrate.
- Flange
- The flange portion is located on the surface of the substrate and provides additional support and fixation, preventing the nut from loosening or detaching under stress.
- Installation Screw (Optional)
- In some applications, a screw is used to directly tighten the Jack Nuts, aiding in the expansion and fixing process.
How Do Jack Nuts Work?
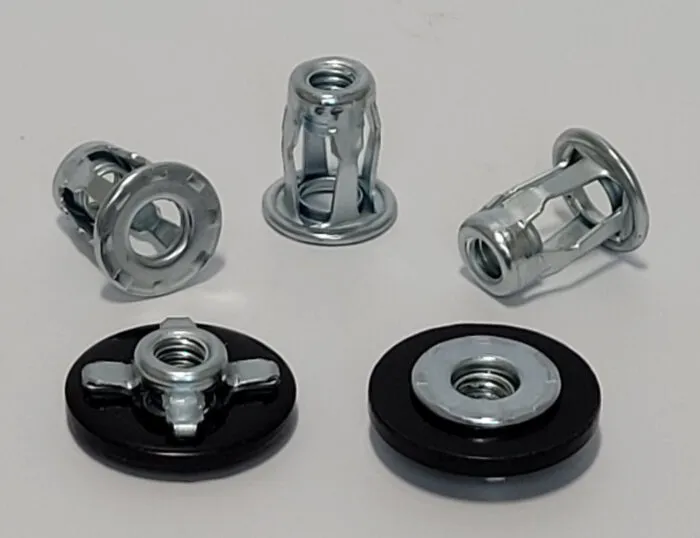
Jack Nuts achieve fixation through mechanical deformation. Their working principle relies primarily on their unique structural design. When the screw is tightened, the expansion legs of the Jack Nut expand outward, forming a solid backing support on the backside of the material, thereby securing the nut firmly in place.
Working Process
1. Insert into the Material Hole
- Select the appropriate size Jack Nut and insert it into the pre-drilled hole, ensuring the flange part is flush against the material surface.
- The threaded sleeve of the Jack Nut passes through the material while the expansion legs remain in a compressed state.
2. Tighten the Screw to Activate Deformation
- As the screw is threaded into the internal threads of the Jack Nut, the axial force from the screw causes the threaded sleeve to move forward.
- Since the expansion legs cannot move forward, they begin to expand outward and bend under the applied force.
3. Expansion Forms Back Support
- As the screw continues to tighten, the expansion legs fully open and press tightly against the backside of the material, forming a stable anchoring point.
- At this point, the Jack Nut is securely fixed in place, creating a stable threaded connection.
4. Installation Complete, Forming Removable Threads
- Once the expansion legs are fully deployed, the Jack Nut functions like a standard nut and can be used to fasten bolts, screws, or other fasteners.
- Since the Jack Nut provides a robust internal thread, users can repeatedly remove and reinstall screws without damaging the substrate.
Key Features
- Suitable for Thin-Walled or Soft Substrates: Relies on mechanical deformation to provide back support without requiring high-strength materials.
- Blind Hole Installation: Can be installed from a single side, making it ideal for applications where access to the backside is not possible, such as hollow tubes or enclosed profiles.
- Easy to Remove and Reuse: Once installed, the internal thread of the Jack Nut can be reused multiple times for fastening, without compromising its anchoring performance.
The deformation-based fixation of Jack Nuts provides reliable threaded connections on materials like plastics, fiberglass, and thin metals, making them an ideal choice for lightweight structures and fragile material fastening.
Do You Have Any Questions?
Let Us Solve Your Problem
How to Install Jack Nuts?
Tool List
- Electric Screwdriver or Manual Wrench – Used to tighten the screw and activate the deformation of the Jack Nut.
- Drill Bit – Choose the appropriate drill bit size according to the Jack Nut specification to ensure the correct hole diameter.
- Deburring Tool (e.g., File or Sandpaper) – Cleans the hole edges to allow smooth insertion of the Jack Nut.
- Jack Nut Installation Tool – A professional tool that helps to uniformly stretch the nut, improving installation accuracy.
Installation Process
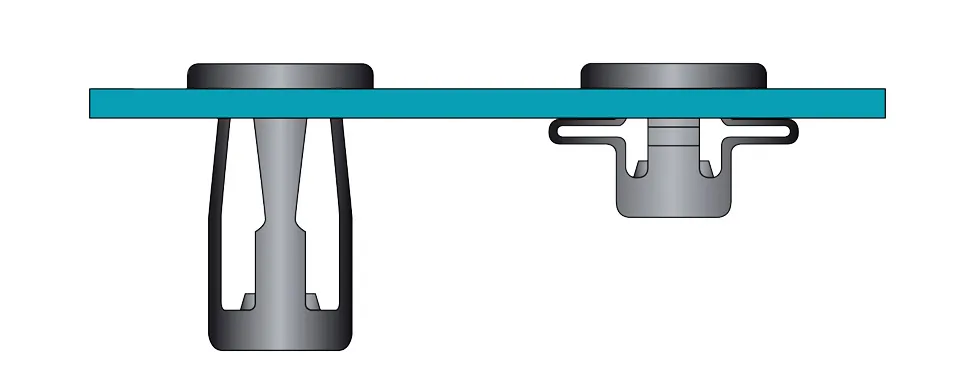
1. Determine Hole Size
- Select the correct drill bit size based on the Jack Nut specification (usually slightly larger than the outer diameter of the threads).
- After drilling, use a deburring tool to clean the hole edges, ensuring the Jack Nut inserts smoothly.
2. Insert the Jack Nut
- Insert the Jack Nut into the hole, ensuring the flange part is flush against the material surface.
- Ensure the nut is positioned correctly and not tilted or loose.
3. Tighten the Screw to Activate Deformation
- Use a screwdriver or wrench to tighten the screw clockwise.
- As the screw tightens, the expansion legs of the Jack Nut will gradually expand and press against the backside of the material.
4. Ensure the Nut is Securely Fixed
- Once the Jack Nut has fully expanded and formed the back support, stop tightening.
- Gently wiggle the screw to ensure the nut is stable and does not loosen or rotate.
5. Complete Installation and Secure the Component
- Now, the Jack Nut provides a stable threaded connection, and you can install bolts or other fasteners.
- The threads remain intact, allowing for multiple removals and reinstallation of screws as needed.
Installation Notes
- Hole Diameter Matching: A hole that is too large may cause the Jack Nut to fail in securing, while a hole that is too small will make installation difficult.
- Moderate Tightening: Over-tightening can damage the substrate or cause the Jack Nut to fail.
- Suitable for Soft or Thin Materials: Ideal for materials like plastics, fiberglass, aluminum alloys, thin steel plates, etc.
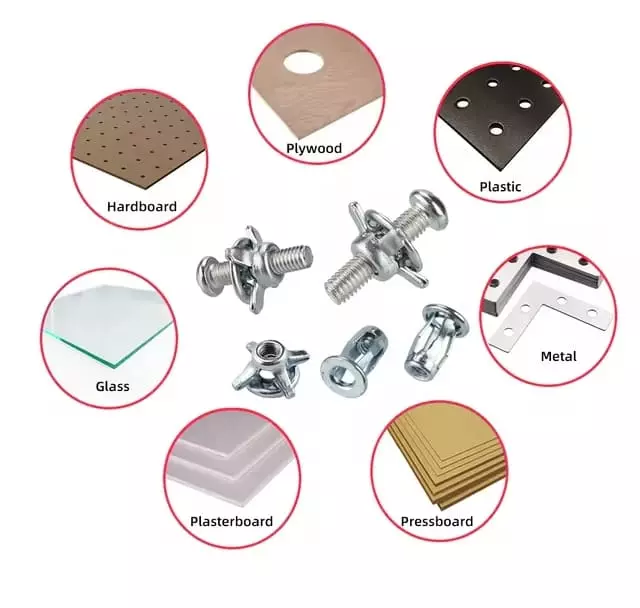
Automotive Industry
Jack Nuts play a vital role in automotive manufacturing and maintenance, especially in areas where standard fasteners cannot provide sufficient grip.
- Interior Panel Fixing – Ideal for securing plastic or fiberboard materials without damaging thin-walled components.
- Wiring Harness Bracket Installation – Provides stable mounting points for electrical wire brackets inside the vehicle body.
- Lightweight Metal Component Fixing – Commonly used for detachable connections in aluminum or composite material parts.
Home Appliance Manufacturing
- Washing Machines – Used for fixing control panels and frames without deforming thin sheets.
- Oven and Microwave Shells – Facilitates secure installation of internal brackets and components.
- Refrigerators and HVAC Systems – Provides strong support for internal structural components.
Aerospace and Shipbuilding Industries
- Aircraft Internal Structures – Suitable for cabin panels, cargo holds, and lightweight metal frames.
- Ship Structural Components – Used for securing attachments to fiberglass and aluminum alloy hulls.
- Composite Material Component Connections – Offers stable threaded connections on lightweight materials without compromising material strength.
DIY and Repair Projects
Jack Nuts are popular among DIY enthusiasts and repair professionals for quick and effective fastening solutions.
- Repair Loose Screw Holes – When standard screws can no longer secure tightly, Jack Nuts provide enhanced threaded connections.
- Reinforce Thin Sheet Connections – Ideal for securing garage doors, cabinets, and furniture made of thin materials.
- Custom Metal and Plastic Structures – Easy for individuals or small manufacturers to create detachable metal and plastic component connections.
Conclusion: Why Use Jack Nuts?
- Suitable for Thin-Walled or Soft Materials – Provides strong connections where regular nuts and bolts cannot be used.
- Supports Blind Hole Installation – No need to access the backside of the material for installation.
- High Load-Bearing Capacity – Delivers durable and vibration-resistant fastening performance.
- Easy Installation – No special tools or welding required for simple installation.
Whether in industrial production or home repairs, Jack Nuts provide reliable and efficient fastening solutions for various materials and structures.
Do You Have Any Questions?
Let Us Solve Your Problem
Jack Nuts vs. Other Nuts
When selecting the right fastener, each type of nut has its own advantages. Jack Nuts stand out with their unique expansion fastening mechanism, offering superior performance in certain applications compared to traditional nuts like rivet nuts, weld nuts, and insert nuts. Below is a comparative analysis of these options:
- Similarities: Both can be used for thin-sheet and blind hole installations without requiring support from the backside.
- Differences:
- Jack Nuts are suited for soft materials (e.g., plastics, fiberglass), whereas rivet nuts are primarily used for metal materials.
- Rivet nuts require specialized riveting tools, while Jack Nuts can be installed with a standard screwdriver.
Weld Nuts vs. Jack Nuts
- Similarities: Both provide strong threaded connections.
- Differences:
- Weld nuts require welding equipment, making the installation process more complex, while Jack Nuts can be installed by simply tightening screws.
- Jack Nuts can be used on materials that cannot be welded, such as plastics or composite materials, whereas weld nuts are limited to metal use.
Insert Nuts vs. Jack Nuts
- Similarities: Both can be used for soft materials such as plastics or wood.
- Differences:
- Jack Nuts use expansion for fastening, requiring less precise hole dimensions, whereas insert nuts typically require threaded holes or specialized tools for insertion.
- Jack Nuts support blind hole installation, whereas insert nuts typically require access from both sides for installation.
Jack Nuts vs. Other Nuts Comparison Table
Feature | Jack Nuts | Rivet Nuts | Weld Nuts | Insert Nuts |
Suitable Materials | Soft materials, thin metals | Primarily metal | Metal only | Plastic, wood |
Blind Hole Installation | Yes | Yes | Requires backside contact | Requires dual-side processing |
Installation Method | Screwdriver or riveting tools | Requires specialized riveting tools | Requires welding equipment | Requires hole or compression tools |
Hole Precision Requirement | Low | High | High | Moderate |
Removability | Removable | Difficult to remove | Difficult to remove | Removable |
Installation Complexity | Simple | Moderate | Complex | Moderate |
Cost | Low | Moderate | High | Moderate |
Jack Nuts are ideal for blind hole installation, soft materials, and scenarios requiring low-precision hole processing. Compared to traditional rivet nuts, weld nuts, and insert nuts, they offer a flexible, easy-to-use, and cost-effective fastening solution.
FAQs - How Do Jack Nuts Work
1. What Materials Are Jack Nuts Best Suited For?
Jack nuts are ideal for soft or thin-walled materials, such as plastics, fiberglass, and thin metal sheets. Their unique expansion mechanism ensures a secure hold without damaging the base material.
2. Can Jack Nuts Be Installed Without Special Equipment?
Yes, jack nuts can be installed using standard hand tools like a wrench or a manual installation tool, making them easier to use compared to other fasteners that require special equipment or welding.
3. How Do Jack Nuts Work to Secure Fasteners?
Jack nuts expand upon installation, forming a strong grip within the material. When pressure is applied, the nut’s internal threads expand against the walls of the hole, creating a solid connection without the need for welding or other mechanical processes.
4. Are Jack Nuts Reusable?
Generally, jack nuts are not designed for reuse. Once installed, they are permanently fixed, and attempting to remove and reinstall them can damage both the jack nut and the surrounding material.
5. Can Jack Nuts Be Used in Blind Holes?
Yes, jack nuts are perfect for blind hole applications, as they do not require access to the opposite side of the material. This makes them especially useful for installations in confined spaces or hollow materials.
Do You Have Any Questions?
Let Us Solve Your Problem
Rivetfix - Leading Jack Nut Supplier in China
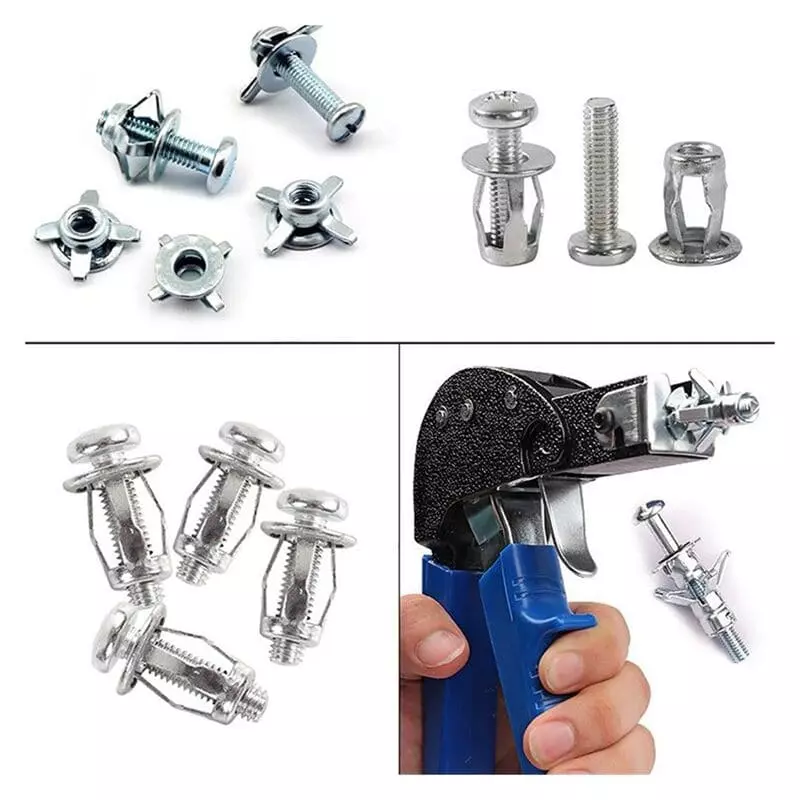
Rivetfix, as a leading jack nut supplier in China, offers high-quality products designed to meet various industrial and commercial needs. With competitive pricing, reliable delivery, and a range of customizable options, Rivetfix is committed to providing efficient solutions for clients worldwide.
We are committed to providing first-class quality fasteners and responsive services to the world. We can select the most suitable fasteners according to your project needs, and provide product customization services.
Contact us for project advice and the latest jack nut quote!
Get High Quality Rivet Nuts Quote!
Send Your Rivet Nut Request
For more than 20 years, Rivetfix has helped customers solve many rivet nuts sourcing needs and technical challenges.
Have a question? Contact us and we’ll provide you with the perfect solution.