Installation Requirements of Rivet Nuts
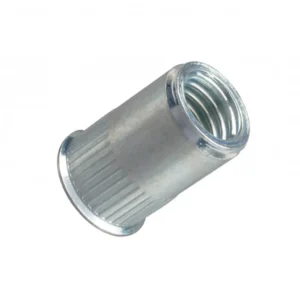
Leading Rivet Nut Manufacturer and Supplier in China
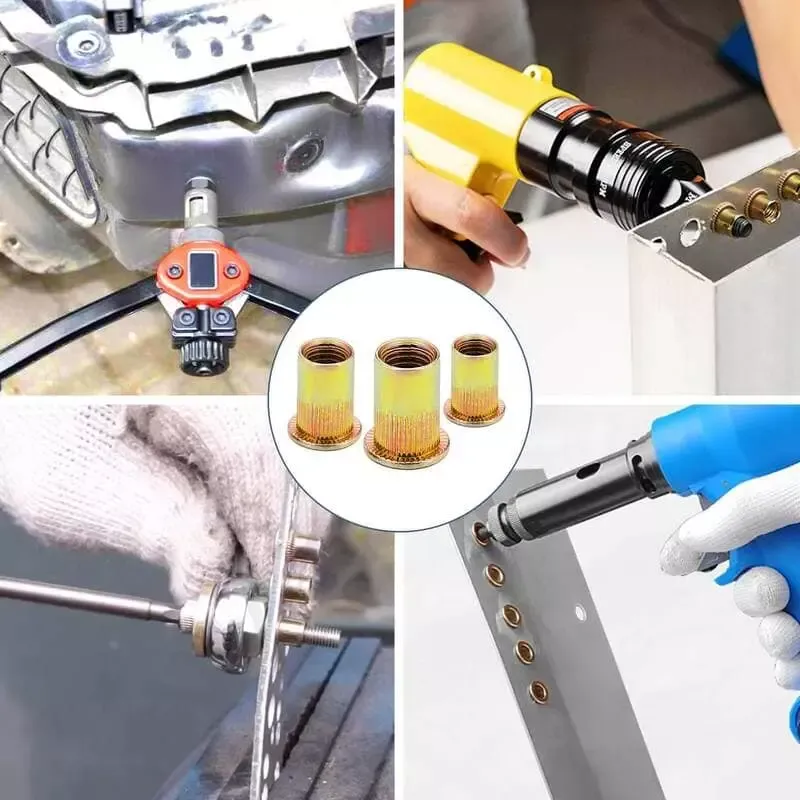
The installation requirements of rivet nuts are crucial to ensuring a secure and durable connection in a variety of applications. Whether you’re working with metals, plastics, or composite materials, understanding the proper installation techniques and specifications can prevent common issues like weak connections, material damage, or failure under load. In this blog, we’ll explore the essential factors to consider, from material selection to installation pressure, that will help achieve optimal results and long-lasting, reliable fixes.
Table of Contents
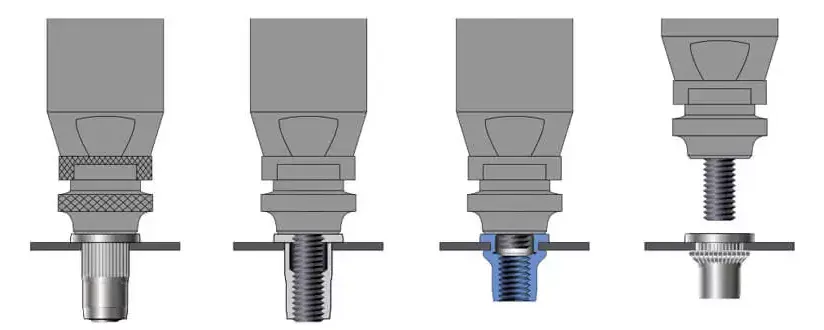
1. Preparation
- Choose the appropriate tool: Depending on the installation environment and requirements, select either a manual tool or a pneumatic tool. Manual tools are suitable for small-scale installations, while pneumatic tools are ideal for large-scale, fast installations.
- Check materials and dimensions: Ensure that the rivet nut is compatible with the thickness and hole size of the material being installed.
- Clean the hole: Remove any debris from the hole to ensure a smooth surface, preventing any jamming or uneven installation.
2. Insert the Rivet Nut
Insert the nut: Place the rivet nut into the pre-drilled hole, ensuring that the outer edge of the nut is flush with the hole opening.
3. Install the Nut
- Use the installation tool: Utilize the selected tool (manual or pneumatic) to compress the rivet nut into the hole. The tool applies pressure to expand the outer shell of the nut, securely fixing it into the material.
- Apply uniform pressure: Ensure that the pressure applied by the tool is even, allowing the rivet nut to fully expand and securely fix within the material.
4. Check the Installation
- Check the fixation: After installation, check that the rivet nut is securely fixed in the material, ensuring no loosening or shifting.
- Torque check: Use a torque tool to check the fastening force of the connection, ensuring that the nut is neither over-tightened nor under-tightened.
Rivet Nut Installation Tools: Types and Suitable Conditions
There are various types of rivet nut installation tools, each suited for different installation needs, scales, and environments. Below are some common types of rivet nut installation tools and their appropriate conditions:
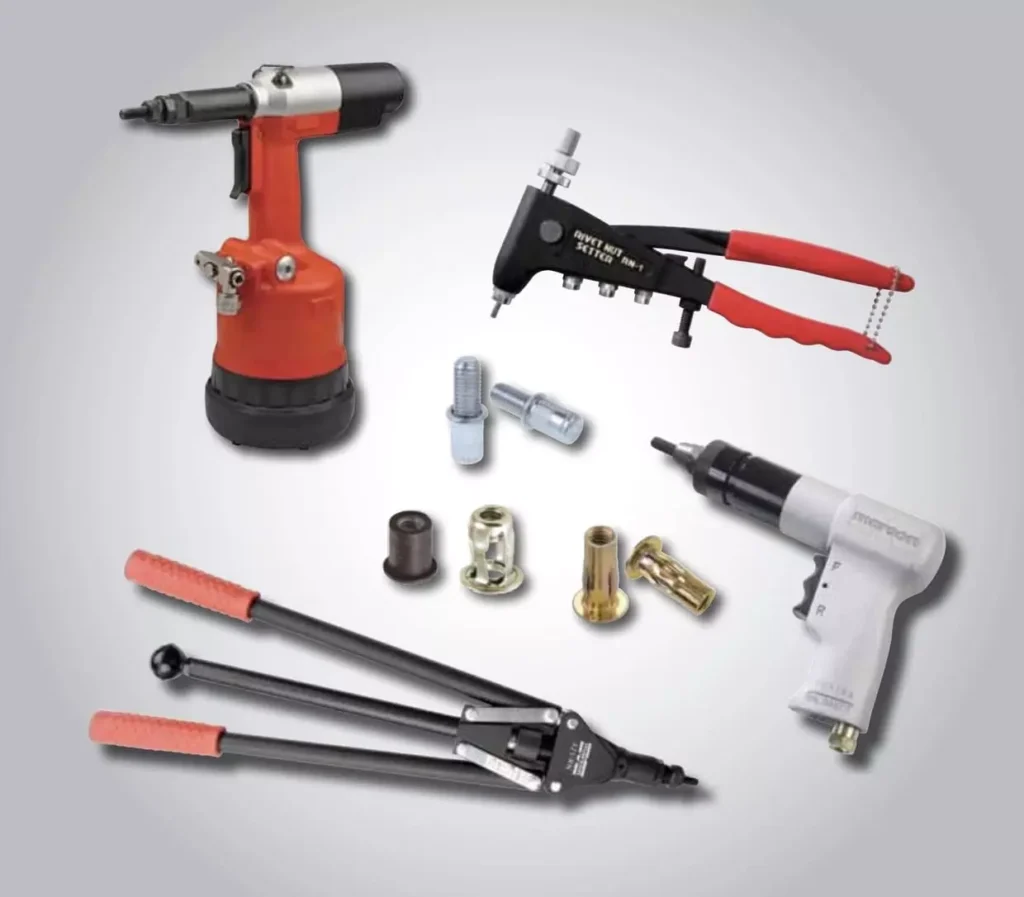
- Type: Manual rivet nut installation tools typically include manual rivet tools and manual rivet nut guns. These tools use hand power to compress and expand the rivet nut, making them suitable for small-scale or precision installations.
- Suitable Conditions:
- Suitable for light-duty and smaller scale jobs.
- Ideal for environments where large-scale or high-frequency operations are not required.
- Offers high installation precision, making it ideal for more detailed applications.
- Commonly used for maintenance, prototyping, or small-scale on-site installations.
- Type: Pneumatic rivet nut guns use compressed air to quickly and evenly apply pressure to install rivet nuts. These tools are highly effective in high-frequency and large-scale installations.
- Suitable Conditions:
- Suitable for medium to large-scale production environments.
- Ideal for applications that require high-speed installations.
- Particularly effective for continuous production lines that require rapid and efficient rivet nut installations.
- Suitable for applications requiring higher force, such as larger diameter rivet nuts or harder materials.
3. Electric Installation Tools
- Type: Electric rivet nut installation tools combine electric power with mechanical compression, providing stable pressure for medium-scale tasks.
- Suitable Conditions:
- Suitable for applications where continuous operation is needed without manual effort.
- Ideal for environments requiring high-speed installations and consistency.
- Highly effective for most medium to large-scale installation tasks.
Tool Type | Description | Suitable Conditions |
---|---|---|
Manual Tools | Hand-powered rivet tools and guns. | – Small-scale, light-duty jobs – High precision for detailed tasks. |
Pneumatic Tools | Air-powered tools for fast, even pressure application. | – Large-scale production – High-speed, continuous operations. |
Electric Tools | Electric-powered tools for stable pressure. | – Continuous operation – Medium to large-scale tasks with speed. |
Do You Have Any Questions?
Let Us Solve Your Problem
Installation Requirements of Rivet Nuts
1. Suitable Rivet Nut Type
Material Selection
- High Strength: Steel rivet nuts generally have higher tensile and shear strength, allowing them to withstand greater loads, making them suitable for most general industrial environments.
- Cost-Effective: Steel is relatively inexpensive compared to other materials, making steel rivet nuts a more cost-effective choice.
- Applicable Environments: Ideal for use in general industrial, mechanical, and automotive industries, particularly in environments without corrosion risks.
- Excellent Corrosion Resistance: Stainless steel rivet nuts, made from materials like 304 and 316 stainless steel, have outstanding corrosion resistance and can withstand moisture, saltwater, and chemicals, making them ideal for harsh environments.
- High-Temperature Resistance: Stainless steel rivet nuts can withstand higher temperatures, making them suitable for high-temperature or temperature-variable environments.
- Moderate Strength: Stainless steel rivet nuts have slightly lower strength than steel rivet nuts but are the preferred choice in many specialized environments due to their excellent corrosion resistance.
- Lightweight: Aluminum alloy rivet nuts are lighter, making them suitable for weight-sensitive applications where reducing overall equipment weight is a priority.
- Good Corrosion Resistance: Aluminum alloys have moderate corrosion resistance, making them suitable for environments that are not excessively corrosive.
- Medium Strength: Aluminum alloy rivet nuts have lower strength compared to steel and stainless steel rivet nuts but still meet the fastening needs of most applications.
Thread Size Selection
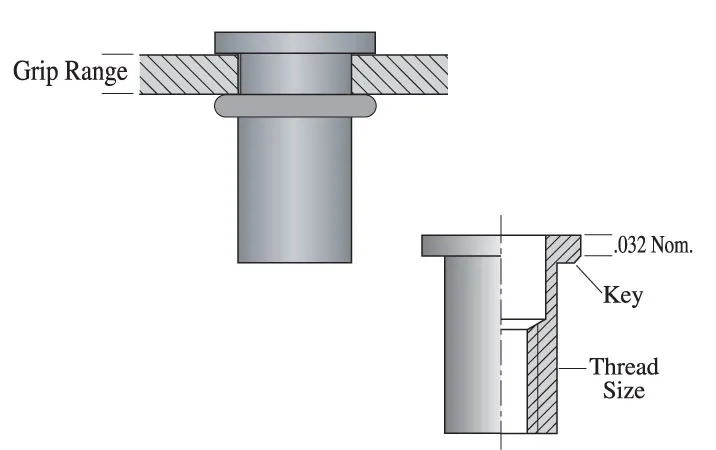
1. Thread Specifications
Thread specifications are typically divided into two main categories: Metric Thread and Imperial Thread, with the choice depending on the region and industry standards.
- Metric Thread: Metric threads are internationally standardized and widely used in most countries and industries. The external diameter is denoted by the letter “M” followed by a number, which represents the size. Common sizes include: M3, M4, M5, M6, M8, M10, M12, etc.
- Imperial Thread: Imperial threads are primarily used in the US, UK, and some other countries. They are measured in inches, with numbers indicating the thread density or the number of threads per inch. Common sizes include: 1/4″-20, 3/8″-16, 1/2″-13, etc.
2. Thread Diameter (Outer Diameter)
The thread diameter refers to the external diameter of the thread, also called the outer diameter. The correct thread diameter must match the diameter of the bolt or screw used to ensure a stable threaded connection.
- For example, an M6 thread has a 6mm outer diameter, which should match the diameter of the corresponding bolt. When selecting, consider the match between the outer diameter and the hole diameter to ensure the rivet nut can be smoothly installed.
3. Thread Pitch
Thread pitch refers to the axial distance between individual threads. Different thread pitches are suitable for different application needs, and common types include:
- Coarse Thread: Features a larger pitch and is ideal for softer or thicker materials, providing stronger tensile strength and self-locking performance. Commonly used in applications requiring higher loads and strength.
- Fine Thread: Features a smaller pitch and is suitable for precise assemblies and high-strength connections, typically used in thin-walled materials and applications where a uniform tightening force is required.
2. Suitable Hole Requirements
Hole Diameter
The hole size should be chosen according to the rivet nut’s outer diameter and thread specifications. Too small a hole will lead to installation difficulty or prevent the rivet nut from expanding correctly, while too large a hole will affect the nut’s holding force.
Generally, the hole diameter should be 0.1mm-0.2mm larger than the rivet nut’s outer diameter, allowing it to insert and expand smoothly.
Hole Wall Smoothness
The inner wall of the hole should be kept as smooth as possible to prevent debris, burrs, and irregularities, ensuring that the rivet nut can expand smoothly and provide a firm threaded connection. Burrs inside the hole can affect the rivet nut’s holding effect, potentially causing loosening.
Hole Spacing
If holes are too close together, it may affect the nut’s expansion and stability. Ensure sufficient distance between holes based on the installation environment and design requirements, so each rivet nut can be installed and expand fully.
3. Suitable Installation Tools
Torque Requirements
The torque applied during installation needs to be precisely controlled. Too high or too low torque will affect the installation outcome.
- Excessive Torque: Can lead to excessive compression or damage to the rivet nut, and even cause the base material to puncture or deform, resulting in unreliable connections.
- Insufficient Torque: Will prevent the rivet nut from fully expanding, which can lead to loose installations and potential loosening during use.
Tool Selection
Based on the rivet nut size, material, and installation environment, choose the appropriate installation tool (such as manual tools, pneumatic tools, electric tools, or hydraulic tools). Ensure the tool’s pressure range meets the requirements of the selected rivet nut to avoid tool damage or poor installations.
Do You Have Any Questions?
Let Us Solve Your Problem
Potential Issues from Incorrect Installation of Rivet Nuts and Solutions
Incorrect installation of rivet nuts can lead to a range of problems that not only affect the strength and safety of the connection but may also damage the materials or equipment in use. Below are some common issues that may arise and their solutions:
Problem① : Rivet Nut Fails to Expand or Secure Properly
A common issue during the installation of rivet nuts is that the nut fails to expand or secure properly. This is typically caused by uneven pressure, improper installation tools, or mismatched hole sizes. To resolve this issue, it’s essential to ensure all installation steps are in accordance with the specifications.
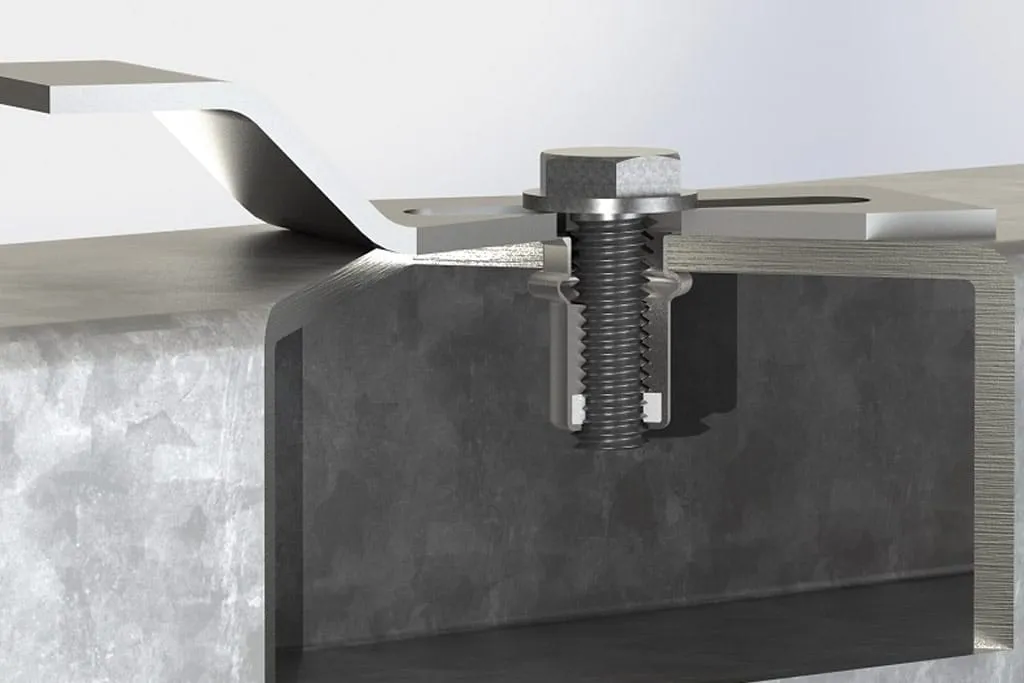
Possible Causes:
1. Insufficient or Excessive Pressure from the Installation Tool:
- Insufficient Pressure: If the installation tool does not provide enough pressure, the rivet nut will not expand fully, causing it to fail to secure properly.
- Excessive Pressure: If the pressure is too high, the rivet nut may be over-compressed or deformed, making it unable to expand properly.
Data Reference:
The ideal pressure range during installation should be between 7000N to 15000N, depending on the size and material of the nut.
For an M6 stainless steel rivet nut, the best installation pressure is typically around 10000N.
For larger sizes, such as M12, higher pressure is required, usually around 15000N.
2. Mismatched Hole Size:
- If the hole is too small, the rivet nut will not enter smoothly, leading to incomplete expansion.
- If the hole is too large, the rivet nut will not make proper contact with the material, failing to provide sufficient holding strength.
Data Reference:
For an M6 stainless steel rivet nut, the recommended hole size range is 6.2mm – 6.5mm. If the hole size is smaller than this range (e.g., less than 6.2mm), the nut will not fit, and expansion will be impossible.
For an M12 rivet nut, the recommended hole size range is 12.2mm – 12.5mm. If the hole is too large, the nut will not properly secure the material.
3. Mismatch between Nut Type and Base Material:
- If the nut type is unsuitable for the base material (e.g., using a steel rivet nut on a softer material), the nut may damage the material upon expansion, leading to an unstable connection.
Data Reference:
Steel rivet nuts are suitable for 2mm – 6mm steel plates and harder materials.
For softer materials, such as plastics or aluminum, it’s recommended to use aluminum alloy rivet nuts or those with softer expansion characteristics.
Solutions:
1. Ensure Proper Pressure from Installation Tools:
Use tools with pressure control to ensure that the pressure is neither too high nor too low. The pressure should be evenly distributed during installation to ensure the rivet nut expands and secures properly.
Recommended Pressure:
- For M6 rivet nuts, the installation pressure should be around 10000N to ensure full expansion and secure fixing.
- For M12 rivet nuts, the installation pressure should be around 15000N to achieve proper expansion at larger sizes.
2. Check Hole Size and Smoothness of Hole Walls:
Ensure the hole size conforms to the standard and the hole walls are free from burrs or irregularities. The hole size should be 0.2mm – 0.5mm larger than the nut’s outer diameter to allow for smooth installation.
Recommended Hole Size:
- For M6 rivet nuts, the hole size should be between 6.2mm and 6.5mm.
- For M12 rivet nuts, the hole size should be between 12.2mm and 12.5mm.
3. Choose the Appropriate Nut Type for the Base Material:
Select the correct rivet nut based on the material type and usage environment to ensure the nut expands properly and provides a strong connection.
Recommended Materials:
- Steel rivet nuts are suitable for 2mm – 6mm steel plates.
- Stainless steel or aluminum alloy rivet nuts are better for softer materials or environments with high corrosion risks.
Problem② : Material Mismatch or Incorrect Selection
When the material of the rivet nut is not suitable for the base material, it may cause installation issues, weak connections, material cracking, or deformation. This is typically caused by choosing a rivet nut material that does not match the base material or by selecting the wrong specifications (e.g., strength, size) for the application.
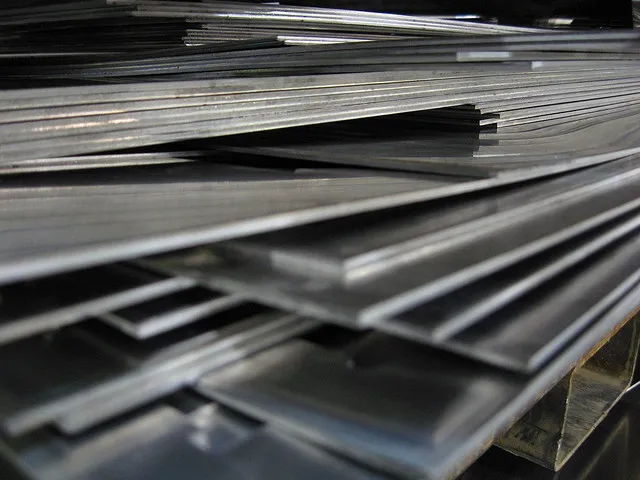
Possible Causes:
- Material Mismatch: Using a rivet nut that is unsuitable for the base material can affect its load-bearing capacity and installation performance. For example, using a steel rivet nut on softer base materials like aluminum alloys or plastics may result in material deformation or an inability to create a secure threaded connection.
- Incorrect Rivet Nut Type Selection: For high-corrosion environments, such as marine or chemical settings, choosing a regular steel rivet nut instead of a stainless steel one may lead to rusting, reducing the connection strength and durability.
- Mismatch in Load-Bearing Capacity: If the selected rivet nut has insufficient strength to meet the load requirements of the base material (e.g., using a softer rivet nut in a high-load application), the rivet nut may fail to provide the required holding force after installation.
Solutions:
- Ensure Proper Material Matching Between Rivet Nut and Base Material:
- Steel Rivet Nuts: Suitable for general industrial environments, ideal for use in hard metal materials such as steel.
- Stainless Steel Rivet Nuts: Ideal for applications with high corrosion resistance requirements, such as marine, chemical, or high-humidity environments. These are well-suited for outdoor or chemical facility installations.
- Aluminum Alloy Rivet Nuts: Best for lightweight, lower-load applications or when corrosion resistance is not a primary concern. These are appropriate for use with aluminum alloys or plastics.
- Select the Appropriate Rivet Nut Type and Size:
- Ensure the selected rivet nut’s size, specifications, and load-bearing capacity meet the installation requirements. For high-load applications, choose rivet nuts with high tensile and shear strength, such as alloy steel rivet nuts.
- Select the correct thread size and grip range to ensure the rivet nut can be securely installed and provide sufficient holding power.
Rivetfix- Ready to Provide You With Rivet Nut Selection Advice and Solutions
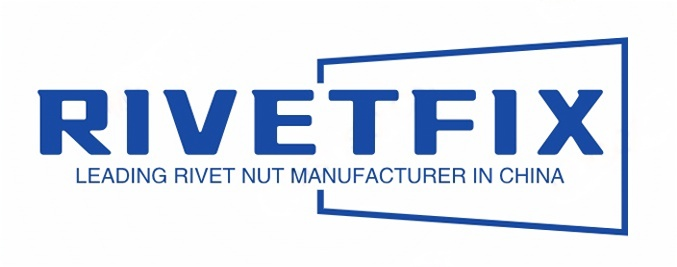
Rivetfix is here to offer expert advice and tailored solutions for all your rivet nut needs. Whether you’re unsure about the right size, material, or installation process, our team is ready to guide you through every step of the selection process.
With a wide range of high-quality rivet nuts and deep industry knowledge, Rivetfix ensures you make the best choice for your application. We offer custom rivet nuts service and various technical support.
Contact us for project advice and the latest rivet nut quote!
Get High Quality Rivet Nuts Quote!
Send Your Rivet Nut Request
For more than 20 years, Rivetfix has helped customers solve many rivet nuts sourcing needs and technical challenges.
Have a question? Contact us and we’ll provide you with the perfect solution.