The Ultimate Guide to Hex Body Rivet Nuts
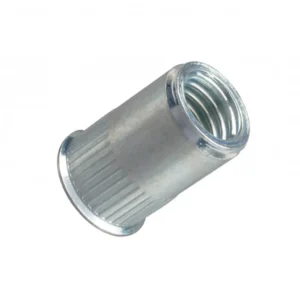
Leading Rivet Nut Manufacturer and Supplier in China
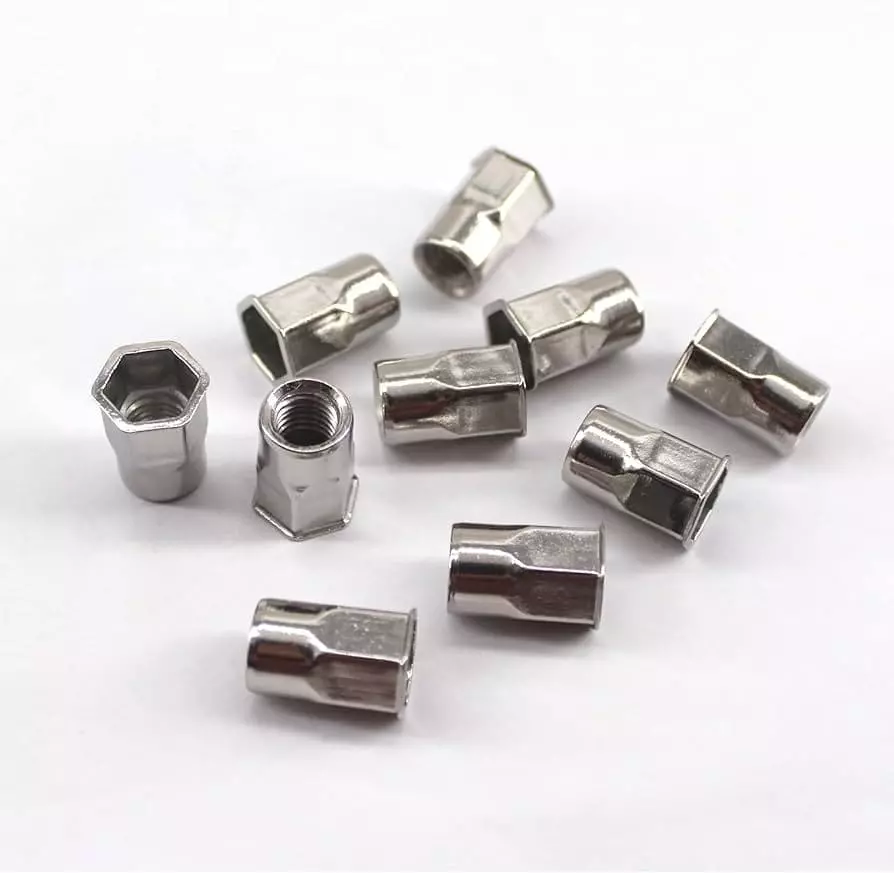
Are you looking for a fastening solution that delivers exceptional torque resistance and long-lasting performance? Hex body rivet nuts are engineered to provide a strong, secure hold—especially in high-vibration or high-torque environments where standard round rivet nuts may fail. In this ultimate guide, we’ll explore everything you need to know about hex body rivet nuts, from how they work and where they excel, to installation techniques, technical specifications, and industry applications. Whether you’re a design engineer or a purchasing manager, this guide will help you understand why hex body rivet nuts are a smart choice for your fastening needs.
Table of Contents
What Are Hex Body Rivet Nuts?
Hex body rivet nuts are rivet nuts with an external hexagonal shape, specifically designed to be installed into pre-punched hexagonal holes. Once installed, they offer excellent resistance to rotation, making them ideal for high-vibration, high-load, and structurally demanding applications.
Difference from Round Body Rivet Nuts:
- Superior Anti-Rotation Performance: The hex shape interlocks with the hex hole to create a mechanical lock, offering significantly higher resistance to spin-out than round body rivet nuts, which rely mainly on friction.
- Stricter Hole Requirements: While round rivet nuts can be installed in standard drilled holes, hex body rivet nuts require precisely machined or punched hexagonal holes, often needing specialized tools.
- Higher Installation Reliability: Hex body rivet nuts are much less likely to loosen or spin in high-vibration environments, making them more suitable for heavy-duty structural connections.
Common Material Types:
- Carbon Steel: High strength and cost-effective; suitable for general industrial use. Typically comes with zinc plating or Dacromet coating for corrosion resistance.
- Stainless Steel (304/316): Excellent corrosion resistance; ideal for outdoor, humid, or chemically aggressive environments.
- Aluminum Alloy: Lightweight and naturally corrosion-resistant; perfect for lightweight assemblies, electronic enclosures, or aerospace applications.
- Brass: Good conductivity and corrosion resistance; often used in electrical applications or where decorative finishes are needed.
How Do Hex Body Rivet Nuts Work Structurally?
Hex body rivet nuts achieve secure fastening through their unique hexagonal exterior design, which creates a mechanical interlock with the base material. During installation, the tail section undergoes plastic deformation, ensuring a strong and stable connection. Here’s a breakdown of their structural working principles:
1. Anti-Rotation Advantage of the Hex Shape
The hexagonal body is specifically designed to be installed in pre-punched hexagonal holes;
Once installed, the nut mechanically locks into the base material, effectively preventing spinning—even under high torque or vibration;
Compared to traditional round-body rivet nuts, the spin-out resistance can be several times higher, making them ideal for applications with high structural demands.
2. Plastic Deformation During Installation
During the installation process, the tail of the rivet nut is pulled by an installation tool to create axial tension;
The tail section of the nut undergoes controlled plastic deformation, expanding and pressing tightly against the back of the base material;
This process requires access from only one side of the material and does not require welding or backside support, making it suitable for blind applications.
3. Clamping and Locking Mechanism
The head of the rivet nut rests flush against the front surface of the panel, while the expanded tail grips the back;
The base material is securely sandwiched between the two deformed areas, forming a “clamping lock” structure;
This structure allows the rivet nut to withstand both tensile and shear loads, ensuring long-term stability and strength.
4. Clamping Range Flexibility
Hex body rivet nuts are available in different lengths and thread types to accommodate a variety of panel thicknesses. The tail section and deformation amount are precisely engineered to match specific clamping ranges, ensuring stable performance across different material thicknesses.
Below is a typical size chart (using M6 steel hex body rivet nuts as an example):
Specification | Total Nut Length (L) | Recommended Clamping Range (mm) | Hex Hole Size (Flat-to-Flat, mm) |
M6-65 | 15.0 mm | 0.5 – 3.0 mm | 8.9 mm |
M6-90 | 17.5 mm | 3.0 – 6.0 mm | 8.9 mm |
M6-115 | 20.0 mm | 6.0 – 8.5 mm | 8.9 mm |
Notes:
- The clamping range indicates the total panel thickness (including multi-layer structures) that the rivet nut is designed to fasten securely;
- Using a rivet nut with a mismatched clamping range—e.g., installing a 6.0 mm type on 2.0 mm material—may result in failed installation or loose fit;
- It is recommended to confirm the required clamping range during the design phase and leave a tolerance of 0.2–0.3 mm for optimal fit;
- The hex hole must precisely match the nut’s flat-to-flat dimensions to maximize anti-rotation performance.
By selecting the right clamping range, hex body rivet nuts can effectively accommodate applications ranging from ultra-thin sheet metal (0.5 mm) to medium-thick panels (8 mm) with strong, reliable fastening.
What Are the Key Specifications and Standards for Hex Body Rivet Nuts?
a. Common Thread Sizes
Hex body rivet nuts typically cover a wide range of thread sizes, from small M4 to large M12, as well as imperial threads such as UNC 6-32 to 1/2-13, meeting various mechanical and industrial application needs. Different thread sizes determine the load capacity and applicable range of the nut, so proper selection should be based on the load requirements of the joint during design.
b. Definition and Selection of Grip Range
The grip range refers to the material thickness range that a rivet nut can accommodate.
Importance of Proper Matching
If the grip range is too narrow, the rivet nut may not fully expand, resulting in insufficient locking force and potential loosening or detachment during use. Conversely, if the grip range is too wide, excessive compressive force during installation may damage or deform the base material, compromising the integrity of the joint.
Design Recommendations
When designing or selecting rivet nuts, accurately measure the total thickness of the materials being joined (including the sum of multiple layers) and choose a rivet nut whose grip range fully covers that thickness. It is also recommended to leave a certain installation tolerance, generally 0.2 to 0.3 mm, to accommodate manufacturing deviations and actual installation conditions.
c. Selection Suggestions for Different Material Thicknesses
For thin sheets (e.g., 0.5 mm to 2 mm), medium thickness plates (2 mm to 6 mm), and thick plates (above 6 mm), appropriate rivet nut models with matching lengths and grip ranges should be used to ensure proper installation and joint strength. When multiple layers are stacked, selection should be based on the total combined thickness.
For more data and information on the clamping Range of rivet nuts of different specifications, refer to our blog Rivet Nut Grip Range Chart.
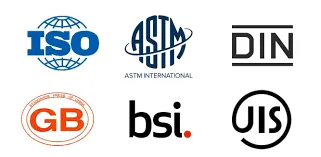
The manufacturing and inspection of hex body rivet nuts generally follow international and national standards such as Rivet Nut ISO Standard and Rivet Nut DIN Standard. These standards specify requirements for dimensional tolerances, thread accuracy, material properties, and surface treatments, ensuring product interchangeability and consistent quality.
e. Surface Treatment Types
To enhance corrosion resistance and appearance, rivet nuts often undergo various surface treatments, including:
Zinc Plating (electroplated or hot-dip), suitable for general industrial environments;
Dacromet Coating, providing excellent salt spray resistance;
Stainless Steel Finish, ideal for highly corrosive environments;
Other Special Coatings, customized based on specific application requirements.
What Are the Advantages and Disadvantages of Hex Body Rivet Nuts?
Advantages Detailed:
a. Strong Anti-Rotation Capability
The hexagonal shape of the rivet nut requires it to fit precisely into a matching hex-shaped hole. This mechanical interlock prevents the nut from rotating or loosening even under high torque or severe vibration. Compared to traditional round rivet nuts, hex body rivet nuts greatly enhance torque resistance, ensuring long-term connection stability and safety, especially in applications such as automotive chassis and machinery where anti-rotation is critical.
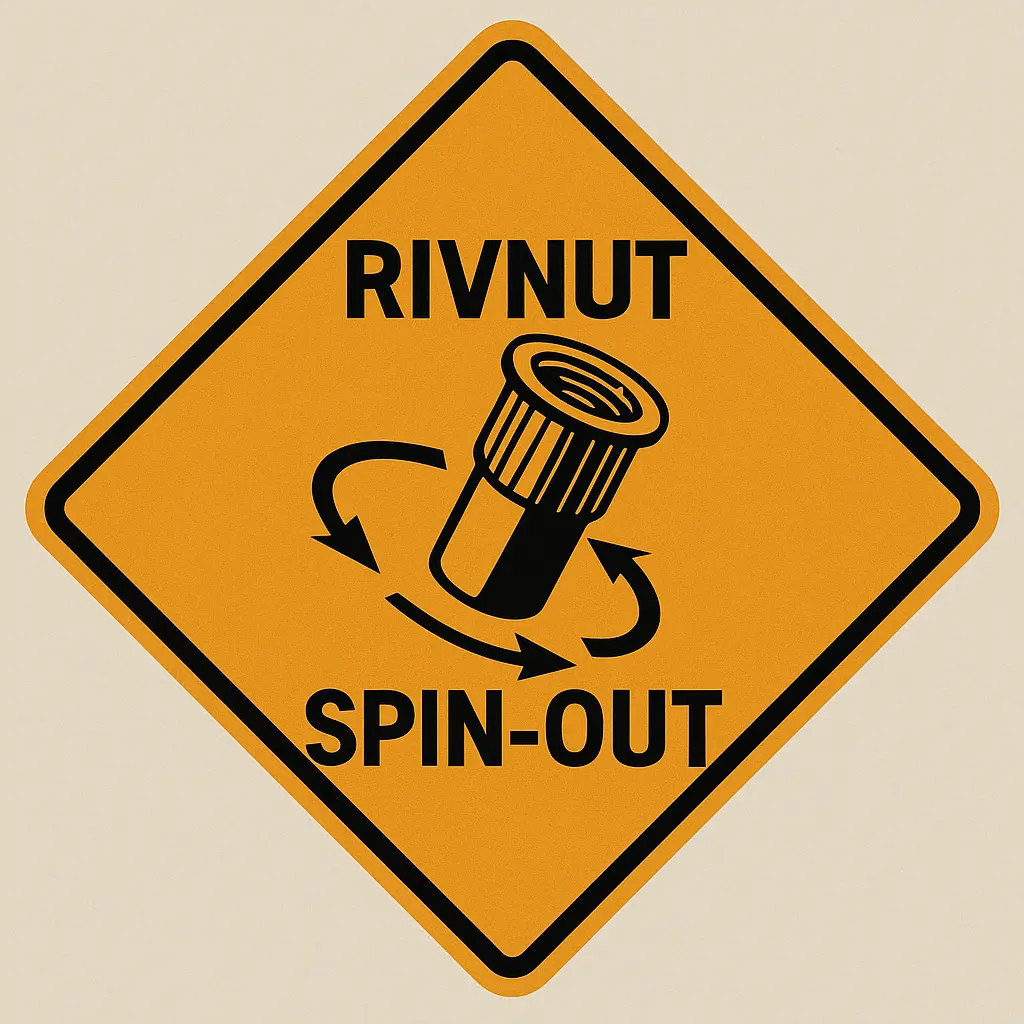
b. Secure Installation Suitable for High Shear or Vibration Environments
During installation, the rivet nut’s tail expands tightly against the backside of the panel, forming a clamping lock with the front installation surface. This structure can withstand significant shear and axial tensile forces. In high-vibration and high-impact environments like industrial machinery, railway equipment, and heavy vehicles, hex body rivet nuts effectively prevent loosening that could cause connection failure, ensuring equipment safety and stable operation.
c. Ideal for Thin-Walled Materials to Achieve High-Strength Connections
Thanks to the plastic expansion of the rivet nut’s tail during installation, hex body rivet nuts provide firm locking even in thin sheet metal or aluminum profiles, preventing cracking or deformation caused by insufficient base material hardness or thickness. This feature makes them excellent for thin structures such as electronic device enclosures and aerospace lightweight assemblies, balancing connection strength and lightweight design.
d. Supports Single-Side Installation to Improve Production Efficiency
Hex body rivet nuts can be installed from one side without the need for backside support or auxiliary structures. This makes them ideal for complex assemblies or limited-space applications, reducing installation steps and time, and lowering labor costs. They are especially suitable for automated assembly lines and mass production environments.
Disadvantages Detailed:
Requires Precise Hexagonal Hole Preparation with High Machining Accuracy
The hex hole must exactly match the hex shape of the rivet nut, with smooth, burr-free edges to ensure effective mechanical locking. Precision stamping or CNC milling is typically required, which increases machining costs and process complexity. For hard materials or complex geometries, maintaining the necessary accuracy can be challenging, leading to higher installation failure rates.
Not Suitable for Structures Unable to Accurately Punch Hex Holes
Some materials or structural shapes restrict the ability to produce precise hex holes—for example, very thin materials may deform easily, or complex parts may not allow standard hex hole punching. Using hex body rivet nuts in such cases can result in inaccurate hole positions and compromised anti-rotation performance, increasing the risk of connection failure. Alternative rivet nut types or fastening methods should be considered.
Higher Cost Compared to Round Rivet Nuts
The manufacturing of hex body rivet nuts involves more material cutting and complex forming processes, resulting in lower material utilization and more production steps than round rivet nuts. Additionally, the required hole machining equipment and precision add to overall assembly costs. These reasons have caused the differences of rivet nuts price .
While performance benefits are significant, users must weigh cost versus performance and choose the best option based on application requirements and budget.
Hex body rivet nuts are widely used in industries and applications that demand high structural integrity and connection reliability due to their excellent anti-rotation performance, secure clamping strength, and adaptability to a variety of materials. Below is a detailed explanation of the appropriate use cases and advantages.
Applicable Base Materials
Hex body rivet nuts are compatible with a wide range of materials, especially the following:
Metal sheets: Such as aluminum, carbon steel, and stainless steel—ideal for light to heavy-duty structures.
Composite materials: Including fiberglass and carbon fiber panels—common in aerospace and advanced equipment.
Engineering plastics: Used in specialty plastic parts where enhanced fastening strength is required.
The hexagonal shape engages with pre-punched hex holes to form a mechanical interlock, which effectively prevents the rivet nut from spinning or loosening after installation. This makes it ideal for high-vibration, load-bearing, or long-term connections.
Typical Industry Applications
① Automotive Industry
Used in body panels, chassis structures, seat brackets, battery housings, roof racks, etc.
Ideal for components subjected to vibration and dynamic loads.
The hex interlock structure ensures that the nut remains securely in place under torque or impact.
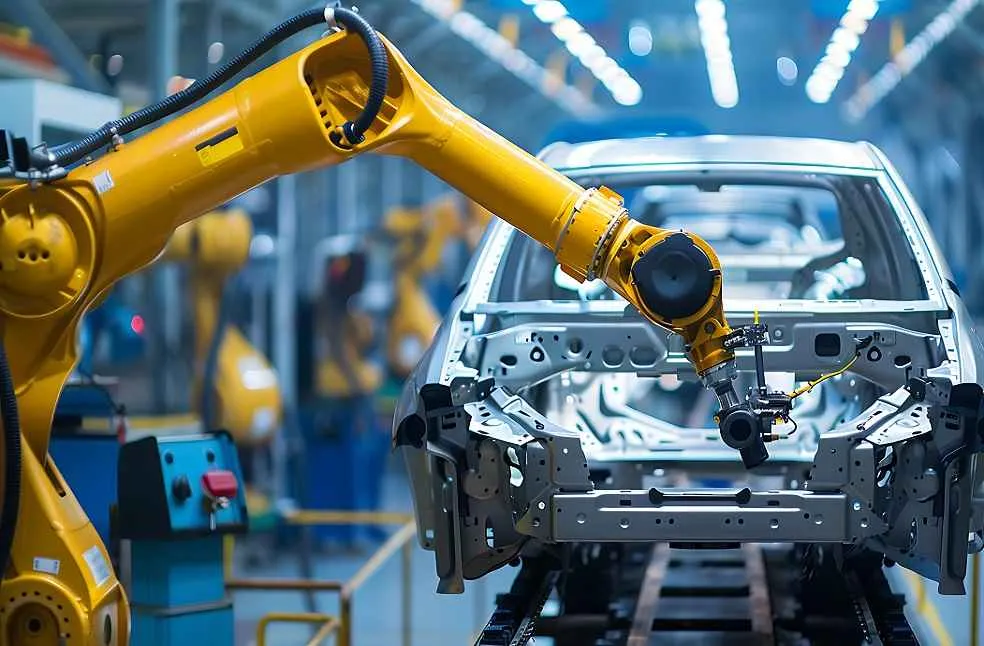
② Rail & Aerospace Industry
Commonly used in train car interiors, structural reinforcements, aircraft panels, and frame joints.
Suitable for lightweight aluminum components requiring strong fastening.
One-sided installation makes it efficient for confined assembly spaces.
③ Electrical & Control Equipment
- Applied in enclosures, control cabinets, instrument panels, and electrical panel assemblies.
- Perfect for mounting cable brackets, DIN rails, and terminal blocks.
- Provides durable threaded connections ideal for long-term use and maintenance.
④ Industrial Equipment Manufacturing
Used in automation equipment frames, robotic arms, and mechanical support structures.
Delivers secure fastening in thin-walled steel or aluminum plates.
Withstands shear and vibration in demanding operational environments.
⑤ Architectural Hardware & Solar Mounting Systems
- Applied in curtain wall systems, reinforced window and door connections, solar racking systems, etc.
- Designed for outdoor use in high-humidity, high-wind, and temperature-fluctuating environments.
- Stainless steel variants offer superior corrosion resistance and longevity.
Summary: Why Use Hex Body Rivet Nuts?
Superior anti-rotation capability: The hex body prevents spinning under torque.
Higher connection strength: Especially in load-bearing or high-vibration conditions.
Broad material compatibility: Works with metal, plastic, and composite structures.
Blind-side installation: Enables easy installation in limited-access areas.
Ideal for high-standard industries: Automotive, rail, aerospace, electrical, solar, and more.
How to Install Hex Body Rivet Nuts Properly?
1. Hex Hole Processing Methods
Hex body rivet nuts must be installed in pre-formed hexagonal holes to achieve mechanical anti-rotation locking. Common processing methods include:
Laser Cutting: Ideal for thin materials like aluminum or stainless steel; offers high precision and is suitable for batch production.
Punching Die: Best for sheet metal batch processing; highly efficient but requires custom tooling.
CNC Machining: Suitable for thick plates or structural components; ideal for precision assembly with strong dimensional accuracy.
EDM (Electrical Discharge Machining): Used for hard-to-machine materials or intricate areas, though relatively low in efficiency.
Hole tolerance must be strictly controlled within technical requirements. We recommend a flat-to-flat tolerance (AF) ≤ ±0.1mm to ensure proper anti-rotation performance.
2. Tool Selection for Installation
Depending on your application scenario, the following installation tools are recommended:
- Manual Rivet Nut Guns: Suitable for small batch installation, maintenance, or on-site repairs. Simple and cost-effective.
Electric Rivet Nut Guns: Ideal for medium-volume assembly; offers higher efficiency and more consistent pull force.
Pneumatic Rivet Nut Guns/Hydraulic Riveting Systems: Designed for automated production lines and high-volume operations, especially common in machinery and automotive manufacturing.
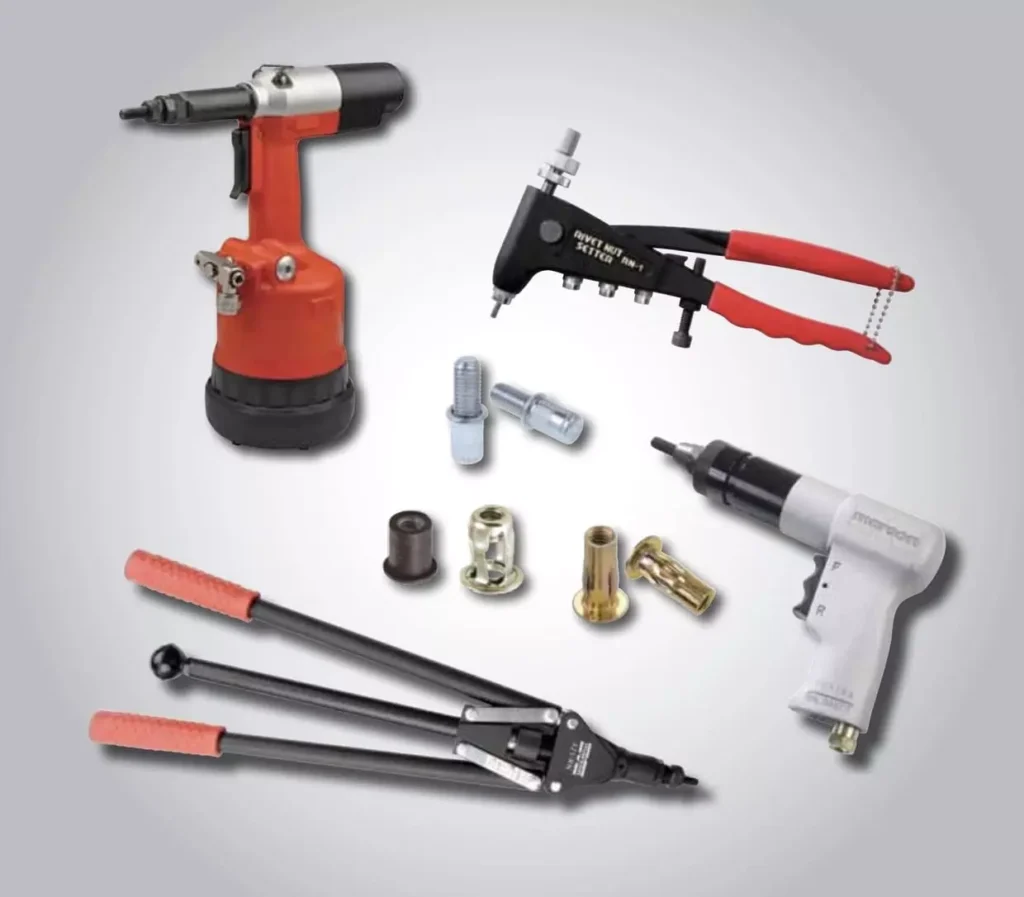
Tools should be equipped with the correct mandrel and anvil to match the rivet nut specification and ensure stable, consistent setting.
3. Installation Precautions
Hex Hole Size Accuracy
Ensure that the pre-formed hexagonal hole dimensions strictly match the rivet nut specifications. In particular, the across flats (AF) measurement should fall within ±0.1 mm; deviation can lead to failure in anti-rotation or make insertion impossible.
Pull Force and Stroke Control
Axial pull force during setting must fall within a stable, safe range to avoid over-setting or under-setting.
Size | Recommended Pull Force (kN) | Recommended Stroke (mm) |
M4 | 4.0 – 6.0 kN | 4.5 – 5.0 mm |
M5 | 5.0 – 7.5 kN | 5.0 – 6.0 mm |
M6 | 6.5 – 9.0 kN | 6.0 – 7.0 mm |
M8 | 9.0 – 12.0 kN | 7.0 – 8.5 mm |
Tip: For pneumatic or electric tools, enable torque-limiting mode and calibrate the output periodically.
Surface Cleaning and Pre-Treatment
- Burr Control: Burrs inside the hole should not exceed 0.1 mm to ensure even seating and prevent post-installation loosening.
- Oil and Debris Removal: Clean the hole with alcohol or non-corrosive agents to eliminate contaminants that could affect clamping strength.
- Chamfering: A 45° × 0.2–0.5 mm chamfer at the hole entrance is recommended to ease insertion and prevent edge scratching.
Post-Installation Testing
a. Anti-Rotation Test
- Gently rotate the rivet nut clockwise and counterclockwise by hand or using a low-speed driver. No movement indicates a good lock.
- Use a torque wrench for precise testing. For M6 rivet nuts:
Thread Size | Minimum Anti-Rotation Torque (Nm) |
M4 | ≥ 2.0 Nm |
M5 | ≥ 3.0 Nm |
M6 | ≥ 4.5 Nm |
M8 | ≥ 6.5 Nm |
b. Pull-Out Strength Test
- Use a tensile tester to confirm the rivet nut is firmly set into the base material.
- For M6, a minimum pull-out strength of 4.5 kN is recommended.
c. Clamping Effectiveness
- After setting, check clamping force by inserting a feeler gauge between fastened parts. Deformation should not exceed 0.2 mm.
- For mass production, set a 2–5% random inspection rate post-installation to ensure batch consistency.
FAQs
1. Can Hex Body Rivet Nuts Be Installed If the Hole Has Slight Roundness Deviation?
Hex body rivet nuts rely heavily on precise hexagonal holes for their anti-rotation performance, as they achieve mechanical interlocking with the hex-shaped hole.
If the hole has slight roundness deviation (e.g., due to punch misalignment or mold wear), it may compromise torque resistance.
In low-load or low-torque applications, minor deviations can sometimes be compensated with thread-locking adhesives.
However, in medium to high-strength connections, it’s recommended to reprocess the hole to maintain across-flats tolerance within ±0.1 mm to ensure anti-rotation effectiveness.
2. How to Determine If the Installation Is Qualified?
Installation quality can be evaluated by the following criteria:
Visual Inspection: The flange sits flush against the surface with no visible tilting or deformation.
Rotation Test: Try turning the rivet nut manually or with a tool—there should be no movement or loosening.
Clamping Force Test: After tightening a bolt, ensure the assembly does not shake. Use a feeler gauge to check that deformation is within 0.2 mm.
Torque Test: Use a torque wrench to test anti-rotation strength (e.g., for M6, minimum 4.5 Nm is recommended).
Pull-Out Test: Use a pull tester to ensure the axial pull-out force meets the requirement (e.g., ≥4.5 kN for M6).
3. Can Hex Body Rivet Nuts Be Reused After Installation?
No, they are not reusable after installation. Hex rivet nuts are installed by irreversible plastic deformation of their rear section:
While the internal thread can be reused for screw assembly,
The rivet nut body cannot be repositioned or reinstalled once deformed.
If replacement is needed, the existing rivet nut must be drilled out and a new one installed in a freshly prepared hole.
4. What Should Be Noted When Installing into Plastic Materials?
Plastics have lower strength and rigidity compared to metals, so extra care is needed:
Choose Appropriate Rivet Nut Types: Use large-flange hex rivet nuts to distribute load and prevent cracking.
Match the Grip Range Properly: Avoid oversize grip ranges that apply excessive pressure, which can crush the plastic.
Reinforce the Mounting Area: Add metal inserts or ribs on the backside to improve pull-out resistance.
Use Controlled Force Tools: Avoid sudden high-force riveting. Use torque-controlled electric rivet nut guns.
Choose Strong Engineering Plastics: Use materials like glass fiber–reinforced nylon (PA6+GF) for better structural integrity.
Do You Have Any Questions?
Let Us Solve Your Problem
Using Hex Body Rivet Nuts Today
Hexagon rivet nuts are suitable for a wide range of base materials such as metal sheets and composites, and can achieve strong, secure installation in single-sided access, vibration-prone, and thin-wall structures. Whether it’s in automotive manufacturing, rail transit, electrical enclosures, or industrial equipment, Hex rivet nuts offer superior stability and safety. Start using Hex Body Rivet Nuts today and take your fastening to a more professional and durable level.
Buy Hex Body Rivet Nuts from Rivetfix
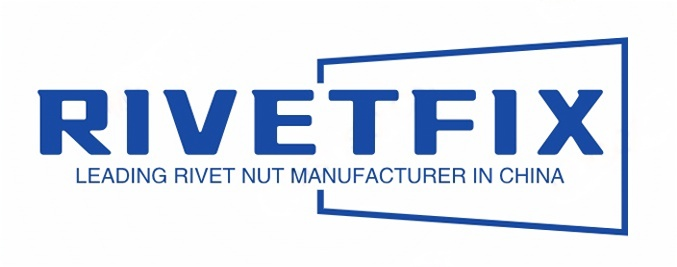
As a leading fastener manufacturer in China with more than 15 years in the industry, Rivetfix are committed to providing first-class quality fasteners and responsive services to the world. We offers a wide range of rivet nuts and clinch nuts designed to meet the unique demands of your projects. Rivetfix ensures you have the right solution for every application. Choose Rivetfix for versatile, cost-effective, and durable fastening solutions tailored to your specific needs. In addition, we can also provide customized rivet nuts service and clinch nuts according to your requirements.
If you’re looking for a high-strength, reliable, and anti-rotation fastening solution, choose our premium Hex Body Rivet Nuts today. Rivetfix offers customized hexagon rivet nuts services for your project. By selecting the right Hex Body Rivet Nut, you can optimize your production process, enhance connection quality, and ensure long-term stability of your products.
Contact us now for more information and customization options on Hex Body Rivet Nuts!
Get High Quality Rivet Nuts Quote!
Send Your Rivet Nut Request
For more than 20 years, Rivetfix has helped customers solve many rivet nuts sourcing needs and technical challenges.
Have a question? Contact us and we’ll provide you with the perfect solution.