How to Choose PEM Nuts / Self-Clinching Nuts for Sheet Metal?
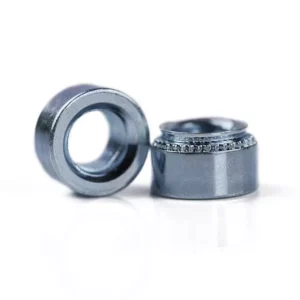
Leading Self-Clinching Fasteners Manufacturer and Supplier in China
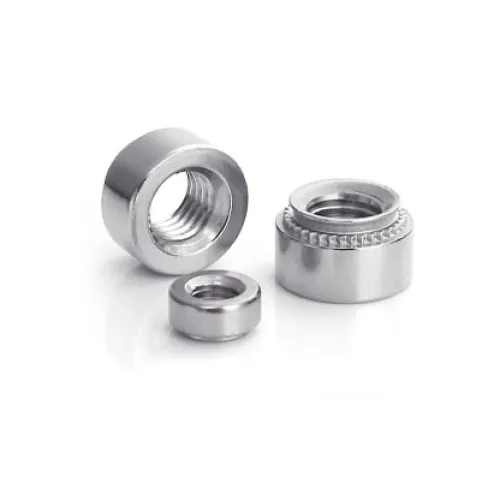
Traditional welding or riveting can warp materials and demand costly labor. Use pem nuts for sheet metal—engineered for fast, tool-free installation via cold-pressing. These self-clinching nuts eliminate secondary processes, enhance structural integrity, and excel in lightweight designs (0.5–6mm thickness). In this guide, discover how to choose the right PEM nut by balancing material compatibility, load demands, and environmental factors—ensuring reliable, cost-effective fastening.
Table of Contents
What Do I Need to Know About Self Clinching Nuts?
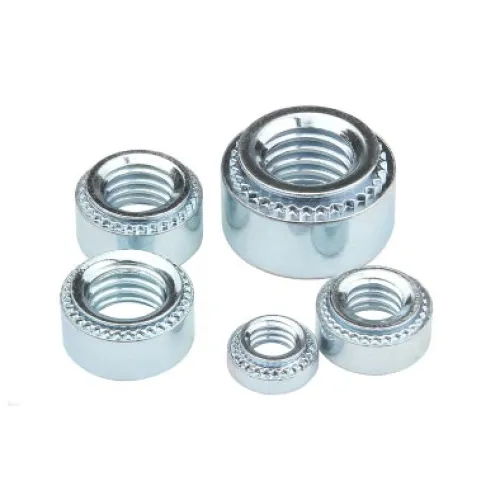
Definition and Working Principle
PEM Nuts (Self-Clinching Nuts) are fasteners that are directly embedded into sheet metal using cold pressing technology. The core principle is:
- Installation Process: The nut is pressed vertically into a pre-punched hole in the sheet metal. The barbs, serrations, or annular grooves at the base of the nut cause plastic deformation in the material, creating a mechanical interlock for secure attachment.
- Locking Mechanism: The material of the sheet metal is “pressed” into the locking structure of the nut, providing a tensile strength that is typically greater than the yield strength of the sheet metal itself.
Common Types and Characteristics
- Locking Mechanism: All types rely on cold-press insertion into sheet metal, using serrations/barbs and the plastic deformation of the sheet material to achieve the interlock.
- General Limitations: Thin sheets (<0.5mm) may result in poor engagement, while thicker sheets (>6mm) require high-load variants.
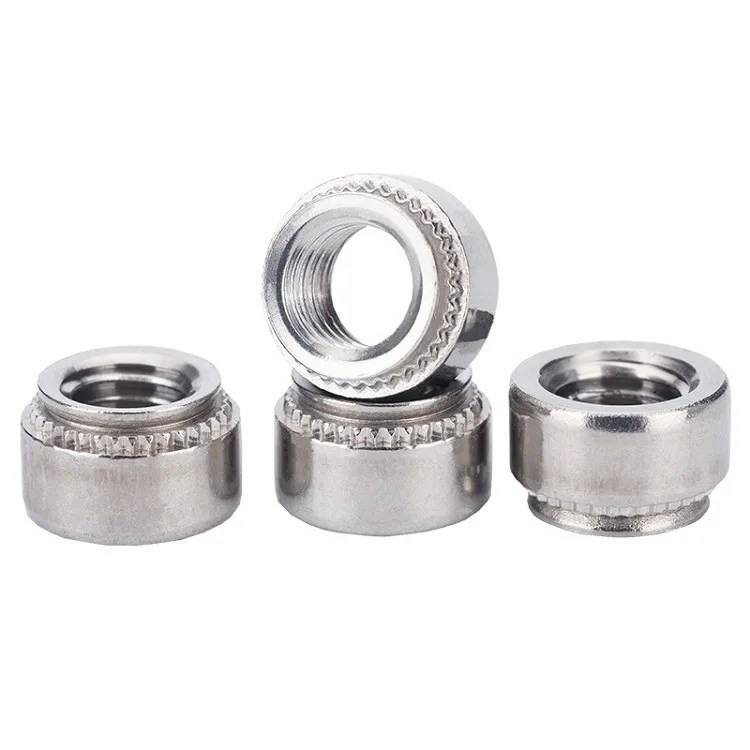
- Design Features: Nuts with internal threads and locking serrations or grooves at the base.
- Applications: One-sided installation on sheet metal (e.g., electronic device enclosures, chassis), where no access is available from the back side.
- Advantages: Easy installation, low cost, and stable internal threads.
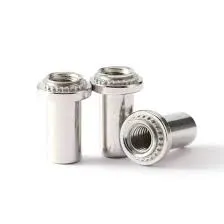
- Design Features: Internal threads with a sealed head, locking serrations or grooves at the base.
- Applications: Outdoor equipment, medical devices, vehicle parts, or other applications requiring liquid penetration resistance.
- Advantages: Sealed head forms a waterproof barrier without requiring additional sealing.
Material Selection and Performance Comparison
The material of the PEM nut directly influences both performance and cost:
Material | Advantages | Disadvantages | Typical Applications |
Carbon Steel | – Low cost, high strength (Tensile ≥ 800MPa) | – Prone to rust (requires zinc/nickel coating) | Indoor equipment, non-corrosive environments (server cabinets, furniture) |
Stainless Steel | – Strong corrosion resistance (A2/A4 grade) | – 2-3 times the cost, high hardness (may wear out molds) | Outdoor equipment (5G base stations, maritime equipment), chemical, medical |
Aluminum | – Lightweight (1/3 the density of carbon steel) | – Lower strength (Tensile ≈ 400MPa) | Aerospace, portable devices (drones, camera mounts) |
Selection Guidelines:
- Corrosion Resistance Priority: Choose stainless steel for humid/acidic environments.
- Lightweight Priority: Use aluminum alloy with anodized treatment.
- Cost Priority: Carbon steel with coating for general industrial environments.
Considerations:
- Hardness Matching: The nut material’s hardness should be greater than that of the sheet metal (e.g., stainless steel nuts for aluminum sheets).
- Installation Tool Limitations: Stainless steel requires higher pressing force (20%–30% more than carbon steel); a high-tonnage press is recommended.
- Anti-counterfeiting Check: Poor-quality carbon steel nuts with thin coatings may corrode. Ensure material reports (e.g., RoHS certification) are verified during procurement.
How to Choose PEM Nuts / Self-Clinching Nuts for Sheet Metal?
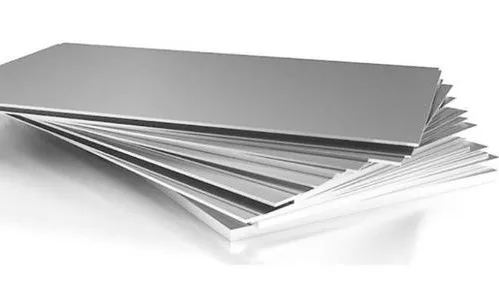
a. Material Compatibility
- Key Rule: The nut material must be harder than the sheet metal to prevent deformation during installation.
- Example: For aluminum sheets, use stainless steel nuts instead of aluminum nuts (stainless steel hardness: ~200 HV vs. aluminum: ~25 HV).
- Material Pairing Guide:
- Carbon Steel Nuts: Ideal for mild steel or galvanized sheets (cost-effective for indoor/non-corrosive environments).
- Stainless Steel Nuts: Best for aluminum sheets or corrosive environments (e.g., marine, chemical industries).
- Aluminum Nuts: Reserved for ultra-lightweight applications but require compatibility with softer alloys (e.g., electronics enclosures).
b. Sheet Metal Parameters
1. Thickness Requirements
- Standard Range: 0.5 mm – 6 mm (thickness tolerance ±10%).
- Special Cases:
- For sheets < 0.5 mm: Use low-profile or micro PEM nuts (e.g., PEM® SMT series).
- For sheets > 6 mm: Select high-load variants with deeper knurls (e.g., PEM® CLS nuts).
2. Hole Specifications
- Critical Tolerance: Follow supplier guidelines (e.g., PennEngineering recommends ±0.05 mm for M3 nuts).
- Common Errors:
- Oversized holes → Reduced pull-out strength (e.g., 3.2 mm hole for M3 nut instead of 2.9 mm causes 30% strength loss).
- Misaligned holes → Uneven pressure distribution during installation.
- Best Practice: Use CNC drilling or precision jigs for consistency.
c. Load & Environmental Requirements
1. Static Load Capacity
- Prioritize tensile strength ratings:
- M3 nuts: ≥1,500 N (e.g., PEM® FH-632).
- M6 nuts: ≥6,000 N (e.g., PEM® FH-365).
- Formula Check:(Typical safety factor = 1.5–2 for industrial use.)
2. Dynamic/Vibration Resistance
- Opt for nuts with anti-rotation features:
- Asymmetric Knurls (e.g., PEM® SP nuts for uneven load).
- Ring Lock Design (e.g., PEM® CLS nuts for high-vibration automotive use).
3. Corrosive Environments
- Stainless Steel (A2/A4):
- A2 (304 SS): Saltwater resistance (marine applications).
- A4 (316 SS): Acid/alkali resistance (chemical processing).
- Coating Options:
- Zinc-Nickel Plating: For moderate corrosion resistance (automotive underhood).
- Passivation: Enhances stainless steel’s oxide layer (medical devices).
Do You Have Any Questions?
Let Us Solve Your Problem
How to Install Clinch Nuts on Sheet Metal?
1. Tool Selection
- High-Volume Production: Hydraulic presses (e.g., 5–20 tons, adjustable for nut size).
- Low-Volume/Prototyping:
- Manual arbor presses (for M3-M6 nuts).
- Hand-held installation tools (PEM® PGK series for fieldwork).
- Critical Tip: Match press force to PEM specifications (±10% tolerance).
- Example: M4 stainless steel nut requires ~4.5 kN vs. 3.2 kN for carbon steel.
2. 6-Step Installation Process
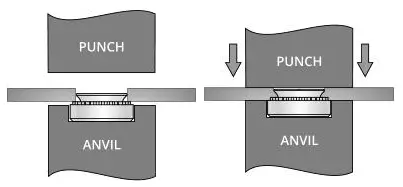
1: Clean the Sheet Surface
- Use isopropyl alcohol or a degreaser to remove oil, dust, or oxides.
- Why? Contaminants reduce knurl grip strength by up to 30%.
2: Drill Precision Holes
- Follow supplier hole size charts (e.g., for M3 PEM nut: 2.9 mm ±0.05 mm).
- Tool Recommendation: Carbide-coated drill bits (extends tool life in stainless steel).
3: Align the Nut
- Use alignment fixtures or self-centering press tooling (prevents skewed installation).
- Visual Check: Ensure nut knurls fully contact the hole circumference.
4: Press Vertically
- Apply force perpendicular to the sheet.
- Force Settings:
- Carbon steel nuts: 3–15 kN (varies with size).
- Stainless steel nuts: 20–30% higher force.
- Audible/Visual Cue: A crisp “click” indicates full seating.
5: Inspect Flatness
- Use a straightedge or dial gauge.
- Acceptable Tolerance: <0.1 mm protrusion above the sheet surface.
6: Rotational Test
- Use a torque wrench to verify resistance:
- M3 nut: 0.5–1.2 N·m (typical).
- Reject nuts that spin freely (indicating poor knurl engagement).
3. Common Installation Errors & Fixes
Error | Root Cause | Solution |
Oversized Holes | Drill bit wear/miscalibration | – Re-drill with calibrated bit.<br>- Use PEM® oversize nut variants. |
Angled Pressing | Misaligned tooling | – Use guided press tooling.<br>- Add alignment pins. |
Ignoring Lubrication | Friction damages threads | – Apply light oil on threads (e.g., WD-40).<br>- Avoid lubricating knurls. |
4. PEM Nut Installation Failures Handing
1: Nuts Pull Out
- Causes:
- Sheet thickness below minimum (e.g., 0.3 mm for M3 nut → requires ≥0.5 mm).
- Hole diameter exceeds tolerance (e.g., 3.1 mm for 2.9 mm requirement).
- Fix:
- Replace with PEM® thin-sheet nuts (e.g., SMT series).
- Install reinforcement plates for load redistribution.
2: Thread Damage
- Causes:
- Side load during installation (e.g., angled pressing).
- Bolt thread mismatch (metric vs. imperial).
- Fix:
- Use anti-rotation jigs (e.g., PEM® AFJ-CLS holder).
- Replace damaged nuts and verify bolt compatibility.
3: Corrosion Failure
- Causes:
- Carbon steel nuts in humid/salt environments.
- Coating defects (e.g., uneven zinc plating).
- Fix:
- Replace with A4 stainless steel nuts.
- Apply post-installation sealant (e.g., Loctite® 567).
What Are the Recommended Clinch Nuts Suppliers?
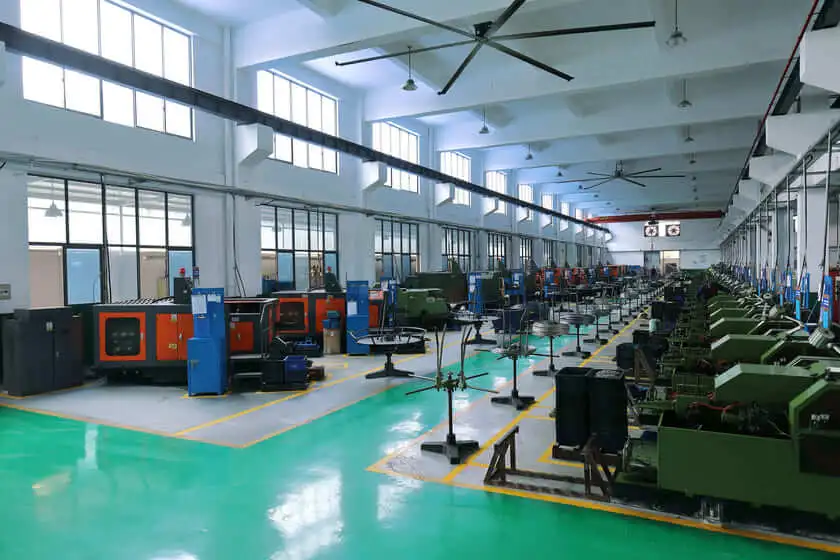
1. Recommended Suppliers and Brand Positioning
Brand | Core Advantage | Applicable Scenarios | Price Positioning |
PennEngineering® | Industry benchmark, full patent technology (e.g., CLS anti-vibration series), highly customizable. | Aerospace, medical devices, precision instruments | High-end (premium 10%-30%) |
Bossard | Global supply chain, quick response via online quotation system, offers JIT delivery solutions. | Automotive, industrial automation, energy equipment | Mid-high end (competitive pricing) |
STANLEY® Engineered Fastening | Leading technology in heavy-duty fields (20% higher tensile strength than industry standards) | Wind power, rail transport, construction machinery | High-end (custom quote required) |
Rivetfix | Cost-performance leader in China, large stock inventory, supports non-standard customization. | Consumer electronics, home appliances, small and medium-sized machinery | Economic (30%-50% lower price than imports) |
2. Cost Control Strategies
1. Small-Volume Purchases (<100 units)
- Objective: Reduce inventory risk + minimize initial cost
- Recommended Channels:
- Digi-Key: Global stock platform (suitable for European and American market orders), but shipping costs are high.
- Alibaba 1688: Select “verified suppliers” and request material certification reports (preferably choose ISO 9001 certified suppliers).
- Tip: Opt for standard models (e.g., PEM® FH series compatible versions) to gain price advantages.
2. Bulk Purchases (>10,000 units)
- Objective: Optimize unit price + ensure long-term supply stability
- Steps:
- Direct Contact with Manufacturers: Obtain sales representative contact information via the manufacturer’s website or exhibitions (e.g., Shanghai Fastener Exhibition).
- Core Negotiation Points:
- Tiered Pricing: For example, 10k units at ¥0.5, 50k units at ¥0.45, 100k units at ¥0.4.
- Payment Terms: Negotiate for 30% advance payment + 70% payment upon delivery, instead of full upfront payment.
- Additional Services: Free warehousing (VMI) or scheduled delivery plans.
3. Key Industry Certification Requirements
Industry | Mandatory Certifications | Test Standards (Examples) | Document Requirements |
Automotive | – IATF 16949 (Quality Management System) – PPAP (Production Part Approval Process) | – Salt spray test (ASTM B117, 500h+) – Vibration test (SAE J2380) | – Material Certificate (EN 10204 3.1) – RoHS Report |
Aerospace | – AS9100 (Aerospace Quality Management System) – NADCAP (Special Process Certification, e.g., heat treatment/surface treatment) | – High-temperature strength test (500°C sustained load) – Nondestructive testing (UT/RT) | – Batch traceability documents – MIL-SPEC Certification |
Medical Devices | – ISO 13485 – FDA 21 CFR Part 820 (for the U.S. market) | – Biocompatibility (ISO 10993) – Sterilization validation | – Cleanroom production records – Biocompatibility statement |
Industrial Equipment | – ISO 9001 – CE Certification (for the EU market) | – Static load testing (DIN 9021) – Anti-loosening test | – Third-party test report (e.g., SGS/TÜV) |
Do You Have Any Questions?
Let Us Solve Your Problem
PEM Nuts vs. Other Fastening Solutions
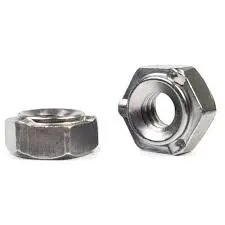
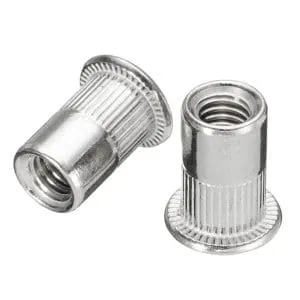
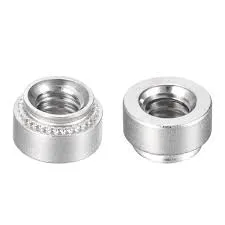
Feature | Weld Nuts | Rivet Nuts | Clinch Nuts |
Strength (Tensile/Shear) | High (depends on welding quality) | Moderate (relies on rivet process) | High (mechanical interlock, stable consistency) |
Cost | Low (material) / High (welding equipment, labor, energy) | Low (simple materials) | Moderate (higher unit cost, but saves post-processing) |
Ease of Installation | Complex (requires welding expertise, potential post-processing) | Moderate (needs rivet gun/dual-side access) | Exceptional (cold-pressed in one step, no post-processing) |
Applicable Sheet Thickness | Thick sheets (>3mm) | Moderate (1–5mm) | Thin sheets (recommended 0.5–6mm) |
Risk of Thermal Deformation | High (due to welding heat) | None | None (cold-pressing process) |
Vibration Resistance | Low (welded points fatigue-prone) | Moderate | High (anti-loosening mechanical interlock) |
Typical Applications | Industrial machinery, heavy-duty frames | Household appliances, light frameworks | Precision electronics, automotive, aerospace, outdoor equipment |
Key Advantages
- PEM Nuts: “King of Thin Sheets”—Balances strength and convenience, ideal for high-precision and vibration-resistant applications.
- Welded Nuts: Cost-effective for thick sheets in rugged environments.
- Rivet Nuts: Suitable for lightweight assembly or small-scale repairs but requires dual-side access.
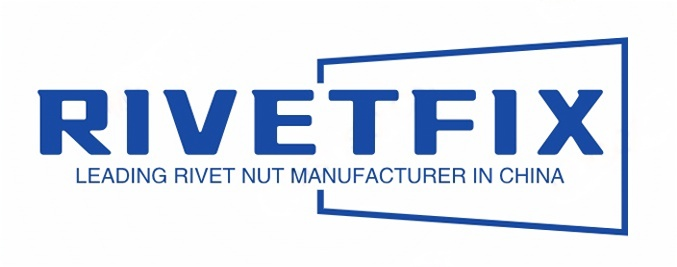
With 15+ years of experience in fastener manufacturing, Rivetfix has grown into a trusted global supplier. Today, we have a dedicated team of 200+ skilled production workers and 40+ professional sales representatives, ensuring seamless service and reliable supply.
Our vision is simple yet powerful: to provide the highest-quality fasteners at competitive prices to customers worldwide. In doing so, we combine precision manufacturing, efficient operations, and exceptional customer support. As a result, we are committed to helping businesses build stronger, more cost-effective solutions. Through this approach, we aim to consistently exceed customer expectations and foster long-term partnerships.
Partnering with Rivetfix means stable supply, top-quality fasteners, and custom solutions. We help you cut costs, boost efficiency, and enhance durability. Expect on-time delivery, expert support, and innovation. Buy PEM fasteners now!
Get High Quality Rivet Nuts Quote!
Send Your Rivet Nut Request
For more than 20 years, Rivetfix has helped customers solve many rivet nuts sourcing needs and technical challenges.
Have a question? Contact us and we’ll provide you with the perfect solution.