Buy Stainless Steel Self Clinching Nuts in Bulk
-Bulk stainless steel self clinching nuts supply
Upgrade your assembly with 304/316 stainless steel self-clinching nuts, ideal for marine, medical, and chemical environments. Featuring a mechanical lock for vibration resistance, these nuts install effortlessly into sheets (0.8–3mm) with no welding. Available in M2–M12 sizes, IATF 16949:2016 and ISO Certification. Enjoy bulk discounts for orders over 10,000 units, custom coatings (passivated/electropolished), and fast global delivery. Request a free sample today!
Home » 4-40 m4 m6 Stainless Steel Self Clinching Nuts Wholesale
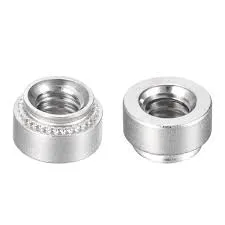
Technical Specifications
- Material & Standards:
- Grade 304 (1.4301) / 316 (1.4401) stainless steel (medical-grade 316L available upon customization).
- IATF 16949:2016 and ISO Certification.
- Dimensions & Compatibility:
- Metric: M2–M12 | Imperial: #2-56 – 1/2-20.
- Compatible sheet thickness: 0.8–3 mm (stainless steel or aluminum sheets).
- Surface Finishing:
- Passivated – Enhanced corrosion resistance;
- Electropolished – Ideal for medical/food industries, easy to clean.
Key Benefits
- Extreme Environment Suitability: Resistant to seawater, chloride ions, and high temperatures (continuous operating temperature ≤400°C).
- Hygiene Compliance: Non-porous surface meets FDA/EU 1935/2004 food contact standards.
- Mechanical Performance: Tensile strength ≥500 MPa (Grade 316), significantly exceeding ordinary stainless steel nuts on the market.
- Sustainability: 100% recyclable material, reducing welding-related pollution.
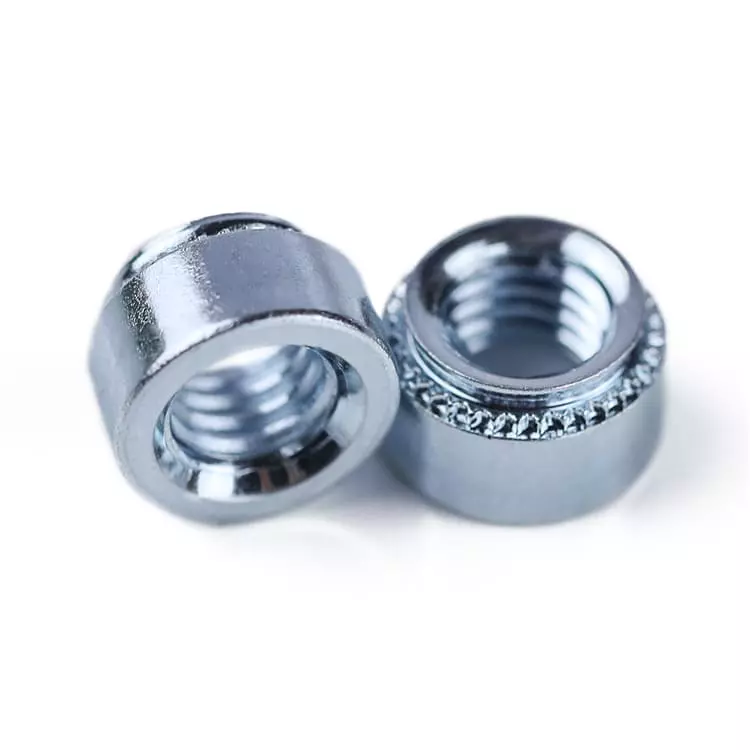

Custom Stainless Steel Self Clinching Nuts for Medical Equipment
Ideal for surgical tools and diagnostic devices due to medical-grade 316L compatibility, corrosion resistance, and easy sterilization for hygienic environments.

Custom Stainless Steel Self Clinching Nuts for Food Processing Machinery
Used in conveyor systems and mixers; electropolished surfaces meet FDA/EU food safety standards and resist bacterial growth.

Custom Stainless Steel Self Clinching Nuts for Marine and Offshore Systems
Withstands corrosive seawater and chloride-rich environments, ensuring longevity in shipbuilding, offshore platforms, and coastal infrastructure.

Custom Stainless Steel Self Clinching Nuts for Electronics and Enclosures
Secures components in thin aluminum/stainless steel enclosures (e.g., servers, control panels) without welding, maintaining structural integrity.
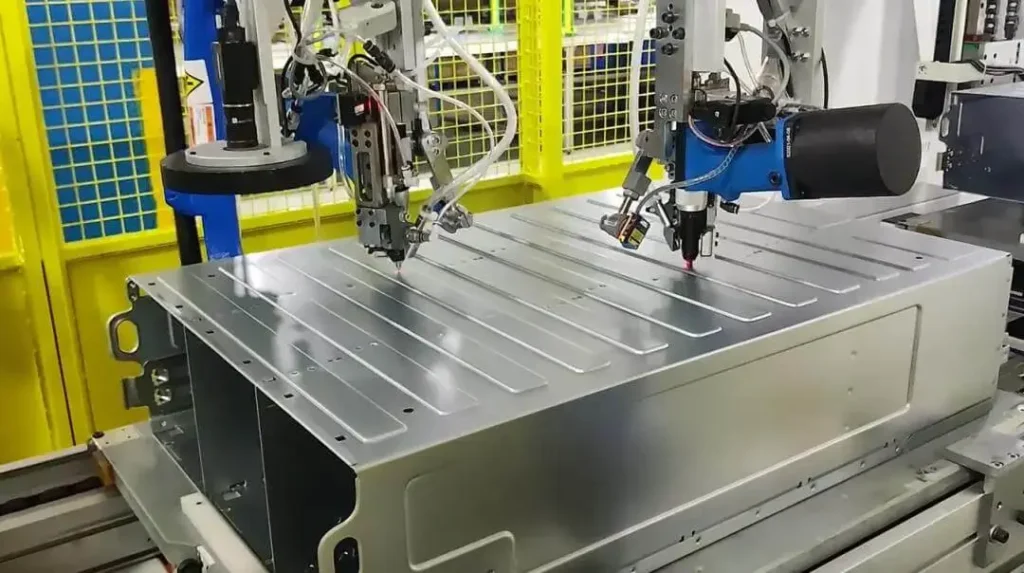
Custom Stainless Steel Self Clinching Nuts for Automotive Manufacturing
Integrates with lightweight aluminum body panels in EVs or fuel systems, offering high tensile strength and heat resistance (≤400°C).

Custom Stainless Steel Self Clinching Nuts for Renewable Energy Installations
Deployed in solar panel frames or wind turbine housings due to 100% recyclability, durability in extreme weather, and reduced environmental footprint.
How to Install Stainless Steel Self Clinching Nuts
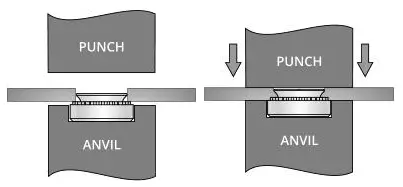
Installation Steps
1. Tool Preparation
- Use a hydraulic press, arbor press, or specialized clinching tool with a custom die matched to the nut size and thickness of the sheet material.
- Verify tool alignment and cleanliness to avoid debris interference.
2. Sheet Preparation
- Drill or punch a hole in the sheet material according to the nut’s specified diameter (refer to manufacturer’s hole size chart).
- Deburr the hole to remove sharp edges and ensure smooth contact with the nut.
3. Nut Positioning
- Insert the nut into the pre-drilled hole, ensuring the knurled ring or serrations align flush with the sheet surface.
- Hold the nut in place using alignment fixtures if necessary.
4. Apply Pressure
- Position the sheet and nut under the press. Apply uniform downward force to drive the nut into the sheet.
- The knurled base will deform the sheet metal, creating a permanent mechanical interlock.
5. Post-Installation Inspection
- Check for flush seating of the nut. The top surface should be even with the sheet without gaps or tilting.
- Perform a pull-out or torque test to validate holding strength (e.g., ≥500 MPa for Grade 316).
Key Precautions
1. Material Compatibility
Avoid mixing stainless steel nuts with aluminum sheets unless corrosion-resistant coatings are applied (electrolytic reactions may occur).
2. Pressure Control
Do not exceed the recommended force (typically 1–5 kN, depending on nut size). Over-pressing may crack the sheet or damage threads.
3. Sheet Thickness Limits
Strictly adhere to the compatible thickness range (0.8–3 mm). Thinner sheets may tear; thicker sheets may prevent proper clinching.
4. Surface Protection
For high-corrosion environments (e.g., marine, chemical), ensure post-installation passivation* or electropolishing of exposed areas.
5. Thread Integrity
Avoid thread contamination during installation. Use soft jaws or protective sleeves on tools to prevent scratches.
6. Hygiene-Critical Applications
For medical or food equipment, clean nuts and tools with alcohol or non-residue solvents before installation to meet FDA/EU hygiene standards.
Environments and Scenarios Requiring Passivation*
1. Marine and Coastal Environments
- Applications: Ship decks, offshore platforms, coastal bridges.
- Rationale: Chloride ions (Cl⁻) in seawater can degrade the passive layer, leading to pitting and crevice corrosion. Passivation significantly extends service life.
2. Chemical Industry Environments
- Applications: Chemical reactors, pipelines, and storage tanks in chemical plants.
- Rationale: Exposure to acidic (e.g., sulfuric acid, hydrochloric acid) or alkaline substances necessitates enhanced chemical resistance to prevent intergranular corrosion.
3. High-Humidity or Tropical Environments
- Applications: Outdoor equipment in tropical regions, steam zones in food processing.
- Rationale: Prolonged moisture exposure accelerates oxidation; passivation suppresses rust formation and corrosion spread.
4. Contact with Dissimilar Metals
- Applications: Aluminum body panels paired with stainless steel nuts (e.g., in electric vehicles), copper alloy heat exchangers.
- Rationale: Electrolytes (e.g., rainwater) may trigger galvanic corrosion. Passivation reduces the electrochemical activity of stainless steel as the anode.
5. Post-Welding or Machining
- Applications: Equipment frames post-welding, machined sheet metal components.
- Rationale: Heat-affected zones or surface contamination from fabrication weaken corrosion resistance, requiring re-passivation to restore the oxide layer.
6. Industries with Strict Compliance Standards
- Applications: Nuclear facilities, oil/gas pipelines (per ASTM A967 or AMS 2700).
- Rationale: Industry mandates require passivation to ensure long-term safety and reliability.
Exceptions: Environments Not Requiring Passivation
- Dry, Clean Indoor Applications: Electronics cabinets, office equipment.
- Electropolished, Low-Risk Environments: Internal cavities of medical devices with no corrosive exposure.
Key Takeaway: Passivation is not a “cure-all” but is essential in environments with chloride ions, chemicals, high humidity, or dissimilar metal contact. Align the passivation process with application risks and industry standards to maximize corrosion resistance of self-clinching nuts.
Have more questions?
Contact us for technical support, advice and quotes.
FAQs
Q1: What materials are stainless steel self-clinching nuts available in?
They are standardly made of Grade 304 (1.4301) or 316 (1.4401) stainless steel. Medical-grade 316L (low carbon) is customizable for enhanced corrosion resistance in sterile environments.
Q2: Do these nuts require welding for installation?
No. They are installed via pressing tools (e.g., hydraulic press), forming a permanent mechanical interlock with the sheet metal. Welding-free assembly minimizes thermal distortion and pollution.
Q3: What environments are they unsuitable for?
Avoid prolonged exposure to:
- Sulfuric/phosphoric acid concentrations >10% (causes pitting).
- Temperatures exceeding 400°C (compromises tensile strength).
- Carbon steel sheets without isolation (risk of galvanic corrosion).
Q4: How do I choose between passivated vs. electropolished surfaces?
- Passivated: Ideal for industrial/marine applications to boost corrosion resistance.
- Electropolished: Mandatory for FDA/EU-compliant food/medical equipment, offering smooth, bacteria-resistant surfaces.
Q5: Are they compatible with aluminum sheets?
Yes, but isolate the contact area to prevent galvanic corrosion. Use insulating washers or coatings if exposed to moisture/electrolytes (e.g., automotive or marine applications).
Buy Self-Clinching Nuts in Bulk from Rivetfix
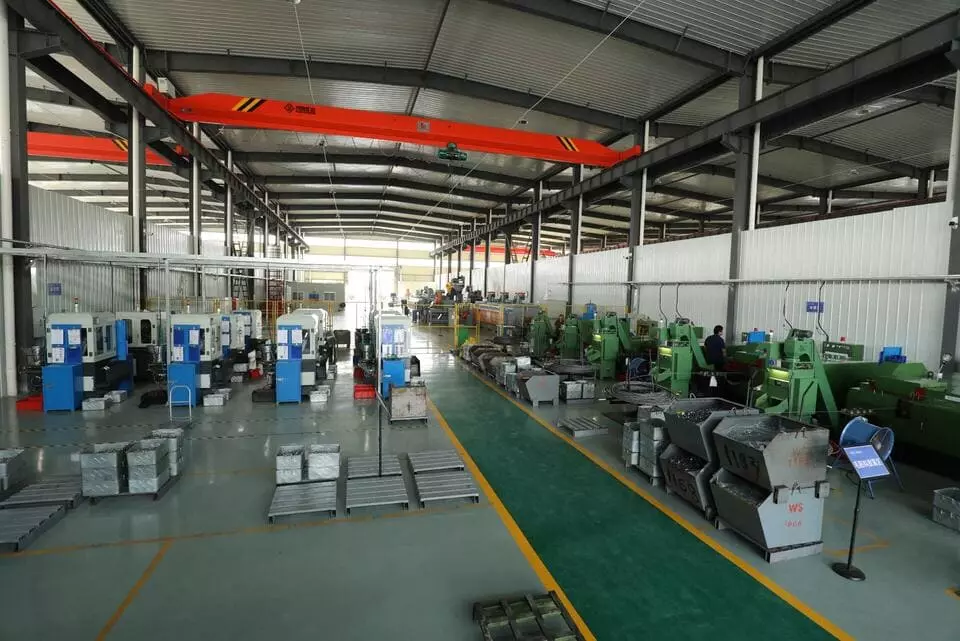
At Rivetfix, we offer competitive pricing for bulk orders, making it easier for businesses to stock up on the fasteners they need without compromising on quality. With fast delivery times and exceptional customer support, we ensure that you receive the right product for your requirements, every time. Trust Rivetfix to provide you with the best self-clinching nuts in bulk, backed by industry expertise and a commitment to customer satisfaction.
Packaging & Delivery
At Rivetfix, we offer a variety of packaging options to meet different customer needs:
- Bulk Packaging: Suitable for large orders, products are packed in bulk for efficient storage and transportation.
- Custom Packaging: We provide customized packaging services according to customer requirements, including personalized packaging design, labeling, and box dimensions, ensuring product safety and brand consistency.
Delivery Time: Depending on order quantity and production schedule, the standard delivery time is within one month. We also offer expedited delivery services for urgent customer needs.
MOQ: 50000
Rivetfix, as part of Rivmate, can also supply high quality rivets and riveted parts. If you have a requirement, please contact us!